Foil-faced rigid insulation under floor joists

Dear GBA
After reading Building Science Corporation document BSI-009: “New Light in Crawlspaces”, I have a couple of questions about using foil faced rigid insulation (isocyanurate) attached to the bottom of floor joists. My question assumes a vented crawlspace, 12in floor joists, R30 Rockwool batt floor cavity insulation with air space between the insulation and the subfloor (as shown in the article), and Climate Zone 4C (Oregon Coast).
Questions:
1. If the foil faced rigid insulation layer is sealed as an air barrier (as recommended) how would water get out if there is a plumbing leak? Recommendations?
2. Does it mater how thick the foil faced rigid insulation is? If so, how would the thickness be determined?
Thanks,
Tom K
GBA Detail Library
A collection of one thousand construction details organized by climate and house part
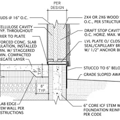
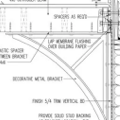
Replies
1) water will always find a way out, if there's enough of it. If there's not much, you won't know it because of the rock wool. The only leaks that will be worse with this system are the ones that just fit between small leaks that keep the wood wet but don't drip onto the floor, and big leaks that run through everything. And, you need to go into the crawl space regularly to catch any but the biggest leaks. The risk of medium sized leaks that you would have caught with only rockwool is pretty low, whereas the risk of rotting your floor with only rockwool can be pretty high.
2) in your climate, the thickness doesn't really make much difference. There is some very low risk of condensation on top of the foam if the crawl gets really cold, but most crawls just don't get that cold. 3/4" polyiso is easy to get and easy to work with. It should work just fine. Most important is to make it airtight at seams and edges.
In order:
>1. It doesn't. Bulk water won't drain through air tight foam- it would have to dry slowly through the subfloor & flooring.
2> In zone 4C it doesn't much matter a whole lot what the foam-R ratio is in minimally vented crawlspace, but on a cooler breezier pier foundation it's wise to use the prescriptive R ratio for walls, which is about 16% of the total. So with R30 rock wool that would be 1.16 x R30= R35 Total, R5 of which is foam. That would be conservative for the crawlspace though.
In zone 4C it's NOT worth leaving the air gap between the rock wool and subfloor from a temperature striping /comfort point of view. It's never going to be 0F in the crawlspace, it may never drop below 32F, and the channel is a potential thermal bypass unless you get serious religion about air sealing the band joists. The 7.25" of floor joist through the R30 is about R7.5 (assuming Doug-fir).
In zone 4C the outdoor summertime dew points average in the 40s F, below the deep subsoil temperatures, and well below the summertime temperature of the subfloor and joists, even in an air conditioned house. Unlike the eastern half of the US there is effectively zero summertime moisture accumulation in the structural wood even without a vapor barrier on the bottom of the joists. As long as there's a vapor barrier on the crawlspace floor a vented crawlspace works just fine.
With a full cavity fill of rock wool or fiberglass in a 9.25" 2x10 joist you'd be at about R10 of thermal bridging through the joist, which is roughly the average wall performance of a 2x4/R13 wall. Consider skipping the foam board, stackng a rock wool R15 + R23 in there (9.0" nominal thickness and R38) or compressing an HD fiberglass R38C batt (10.25 nominal thickness, R35-ish at 9.25") , suspending them in place with perforated radiant barrier (about 5 perms) stapled to the underside of the joists further supported by furring 24" o.c. perpendicular to the joists holding both the RB & batts up. The perforations should have enough capillary draw to allow bulk water to drip (but not exactly pour) out in the event of a leak, and the joist bays can dry toward the crawlspace at a reasonable rate even after a leak.
Hi Thomas -
I think every building can benefit from a leak detection system (see FloLogic: https://www.flologic.com) but this design makes it seem like more than just a good idea. These systems are not inexpensive, but then, neither are the results of a leak...
Peter
Thanks to Peter Engle, Dana Dorsett, and Peter Yost for their thoughtful replies.
Dana:
Are you saying that even with the perforations it would still (in my situation) reduce thermal coupling with the ground and would keep the joists and insulation significantly warmer and dryer than they would be without the perforated radiant barrier?
Since the perforated radiant barrier would not be an air barrier, how would you compare the benefits of that approach to the benefits of a foil faced rigid insulation (polyiso) with joints in contact but without sealing tape?
Thanks,
Tom K.
Tom,
I have a similar question and situation, but mine is in climate zone 4a (foothills of NC). I also read the Fine Homebuilding article and it led me to this discussion. If I have your typical R-19 batts in the crawl space between floor joists, could I add the 1" of polyiso and tape the seams if I secured the batts with strapping instead of the joist hangers that are there now? That would give me the 2" air gap at the subfloor. All flooring is carpet or solid oak tongue and groove.
Thanks for the expertise,
Matt G.
>"If I have your typical R-19 batts in the crawl space between floor joists, could I add the 1" of polyiso and tape the seams if I secured the batts with strapping instead of the joist hangers that are there now?"
Why not support the batts with the 1" polyiso? R19 batts are very low density- they don't really weigh much, and 1" polyiso cap-nailed to the bottom edges of the joists isn't going to sag under the weight.
Be sure to carefully air seal and insulate the band joists as part of the project. R19s are more of an air filter than an air retarder, and a 2" air gap is a potential thermal bypass between the insulation and floor if it's leaking air on both ends.
Dana,
I appreciate the response. By strapping I meant some kind of cheap fabric to hold them in place while the polyiso is installed. I've got a few drooping now (moisture most likely), but I'd say less than 5 batts. I would plan to seal the rim joists as well and tape the seams of the rigid. The crawl space doesn't see much bulk water even in heavy rains.
My two options are seal the crawlspace (add french drain, sump pump, poly sheeting on floor, insulation on walls, etc. with exhausting conditioned air into crawl space and out of crawl space to the outside.) or add rigid and air seal to the floor joists. Keeping the fiberglass would just be a cost savings measure, but Rockwool batts would be the more expensive and preferred route. My primary concern is that with the encapsulation method I may introduce Radon issues and I feel I would have to sub that out, adding cost. I have only water supply and drain pipes in the crawl space. HVAC/ducts and water heater are all in attic and natural gas. I might add this is a 2-story, 2450 SF, built in 2001 with the attached garage 4' below the finished floor (really high ceilings) that shares a back wall with the crawl space. One bedroom above the garage.
Thanks,
Matt
>"By strapping I meant some kind of cheap fabric to hold them in place while the polyiso is installed."
Therein lies the confusion. In the trades "strapping" often refers to narrow 1x2 or 1x3 wood furring.
>"My primary concern is that with the encapsulation method I may introduce Radon issues..."
That isn't very likely, though it's complex. By encapsulating the crawlspace you are blocking the entry of soil gases into the crawlspace, which is currently uncontrolled other than dilution via random ventilation. With a sealed crawlspace and a code-minimum (1 cfm per 50 square feet of floor are) continuous exhaust-only ventilation the soil gases are largely blocked, and the crawlspace is depressurized relative to the first floor, so any radon finding it's way into the crawl space would not make it into the rest of the house.)
Even if left as a vented crawlspace it's well worth installing a heavy ground vapor barrier such as EPDM roofing or 10mil+ polyethylene sheeting sealed and strapped (with furring) to the foundation walls.
Note, in a Polar Vortex disturbance cold snap water pipes in vented crawlspaces on the far side of insulation from the conditioned spaces are at risk of freezing in a 4A climate. Conditioned UNvented crawlspaces insulated at the foundation walls are nearly impossible to freeze, taking heat from the subsoil during extreme conditions when the crawlspace temp drops below the subsoil temp.
I'm unable to interpret the abbreviations on the drawings. Could you spell it out in English or Hindi or some other Indo-European language?
It might be easier and cheaper to use the usual insulation support wires (basically short lengths of heavy gauge steel wire) between the joists. Just stick in enough of the wires to hold the batts in place while you install the polyiso, with the expectation that the polyiso will be doing the real work of holding the batts in over the long term.
Bill
Echoing previous comments about insulating the rim joist: if you end up with a gap at the top of the insulation, and the rim joists aren't insulated, the energy will just take a shortcut and bypass all of the insulation that you've put farther down toward the bottom of the joists. This can result in frozen pipes, etc; this happened to a relative of mine. We redid it, eliminating the gaps, and no more freezing pipes. This was in a "open crawlspace" with piers, but I think the same thing applies.
Zephyr - The method by which the fiberglass would remain between the floor joists is the least of my worries as the taped rigid was to address the air sealing and the support for the batts.
Andrew C - The rim joists are priority before either method takes place. I may be able to get some XPS for free from some of our vendors at work, so I'll use that if I can along with the cut and cobble method with the great stuff pro and gun. If not I'll shop other building supply houses around the area for pricing on the 2" or 1" polyiso. Lowe's always has the 2" XPS in stock though and it's around half the price when I've gotten it priced for work, we're a large commercial masonry outfit.
The purpose of my retrofit is better indoor air quality and lower heating/cooling bills.
Do these two methods I'm planning both address that? Any issues foreseen with either?
>"The purpose of my retrofit is better indoor air quality and lower heating/cooling bills.
Do these two methods I'm planning both address that? Any issues foreseen with either?"
It's more difficult to adequately air seal a the crawlspace ceiling than at the walls & crawlspace floor, especially when there are drain/plumbing/wiring /duct penetrations, but air sealing & insulating the crawlspace ceiling will almost always reduce heating energy use, but may slightly increase cooling energy use.
The indoor air quality issue may or may not be improved by those measures, depending on just how clean the infiltration air was coming up from the crawlspace. Air sealing the house reduces the overall amount of "natural" ventilation, but it also allows better control over the sources and paths of the incoming air using active ventilation.