Foil faced rigid insulation

I am in mixed-humid (Zone 3A).
I plan to use foil faced roof sheathing in my vented attic as a radiant barrier and was wondering about the efficacy of foil faced rigid insulation on my exterior walls facing the air gap to the siding (brick, stone and plank). Given my climate, any wall moisture will typically dry to the interior, so it would seem the reduced permeability of the foil facing would not be an issue.
From inside out:
• Latex paint
• Drywall
• Dense pack cellulose or fiberglass (R-13 min) inside of 2×4 studs 16” on center (we could use 24” on center if code allows and we followed advanced framing techniques).
• OSB
• Tyvek DrainWrap
• Foil Foam board (R-7 min) giving R-20 wall)
• 3/8 air gap
• Brick/stone/stucco/siding/shakes.
Wall variation, if it will be cheaper:
• Higher R-value in stud bays (R-15 or higher)
• Tyvek Thermawrap 5.0 in place of drain wrap and foam board.
• Total of R-20 or higher.
Your thoughts?
Norman
GBA Detail Library
A collection of one thousand construction details organized by climate and house part
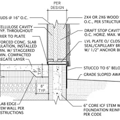
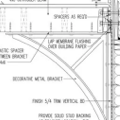
Replies
PNJFSX,
Please tell us your name. If this is new construction and you have a simple roof line, the best strategy is to install R-38 rigid foam on the exterior of the sheathing. In many areas you can buy reclaim foam for one-half or one-third the cost of new material.
Here is one of Martin's articles on this approach to insulation: https://www.greenbuildingadvisor.com/articles/dept/musings/how-install-rigid-foam-top-roof-sheathing
If it were me, I would look at exterior foam for the roof and 2 X 6 walls with dense-packed cellulose. (I might place rigid foam on the interior edge of the studs to combat thermal bridging). One factor to consider on new construction is the ever-lower cost of solar. It seems we are at (or near) a point where is makes more sense to invest in solar and settle for a somewhat lower performing house.
Roof will be vented, so exterior foam there is not being considered. The extra cost of 2x6 walls on the door and window jambs may be more than the cost of the exterior foam/house wrap. Lot is heavily shaded by mature hardwoods so solar is probably not viable.
My name is Norman (which was at the end of the post, but obviously not visible enough). I have changed the profile to note this.
NormanWB
Hi Norman,
Sorry that I missed your signature.
On using foil-face foam as a radiant barrier, are you considering this approach because your HVAC equipment and ducts will be in the unconditioned attic? While that approach is common in Zone 3A, it should be avoided. Ideally, you want your equipment and ducts within the conditioned space.
Martin has an article on radiant barriers at https://www.greenbuildingadvisor.com/blogs/dept/musings/radiant-barriers-solution-search-problem. These "radiant barriers" are not foil-faced foam, but you may find the information useful.
There are lots of trade offs when constructing a home. You can certainly use a 2 X 4 plus rigid foam approach on your project. The Thermawrap 5 sounds like a bit of a pain (https://www.greenbuildingadvisor.com/blogs/dept/musings/two-new-exterior-insulation-products-walls).
Ductwork and HVAC are planned for a conditioned basement/crawlspace. The foil faced sheathing for the attic is simply to reduce radiant heat in that space. Same for the exterior walls. Looks like Martin came to the same conclusion on attics from the article you noted:
"That said, radiant-barrier roof sheathing is effective at lowering attic temperatures. Since it doesn't cost much more than ordinary roof sheathing, it makes sense to install it on new hot-climate homes."
In the comments below the article, Brad asks about foil faced iso facing brick air space:
"If you are buying 2-in. polyiso, the radiant barrier comes free. If the foil faces an air space, you can pick up an additional R-3 on your wall assembly. That's good."
Thermawrap 5 will only be considered if the overall cost is significantly lower than Tyvek and foam board, which it sounds like it will not be. Plus I lose the R-3 Martin notes.
It's worth paying a small amount extra for the framing &/or energy heel trusses of sufficient depth and strength to manage 18" of blown cellulose, and meticulous air sealing of the attic floor prior to blowing in the cellulose.
Take a look at the zone 3 row of Table 2 in this document:
https://buildingscience.com/sites/default/files/migrate/pdf/BA-1005_High%20R-Value_Walls_Case_Study.pdf
https://www.greenbuildingadvisor.com/sites/default/files/images/BSC%20R-value%20recommendations.preview.jpg
See also:
https://www.greenbuildingadvisor.com/articles/dept/musings/r-value-advice-building-science-corporation
Those numbers are "whole assembly R", not center-cavity R. eg: The R20 recommended wall for zone 3 could be 2x6/R20 cellulose or open cell foam or fiberglass, with 1" of foil faced polyiso, or it could be a 2x4/R13 wall + 1.5" of foil faced polyiso.
At that level of whole-assembly performance a reasonably tight reasonably designed & oriented house can usually it Net Zero Energy with a PV solar array that fits on the house, assuming right-sized better class heat pumps for heat & AC.