Foam sheathing, WRB, remodel issues

Hello,
I originally posted this near the end of another thread. It was suggested I repost it as an original question.
I’m doing a remodel on a 1928 bungalow. At present, most walls remain the original 2 by 4 with 3/4 fir t&g or shiplap inside and out. I’m trying to retain this construction to avoid going down the major seismic retrofit route with the building department. It’s odd construction with non-uniform stud spacing.
The plan at present (from the inside) is 1/2 inch or 5/8 inch drywall detailed as ADA (with vapor barrier paint only if the bldg dept makes me), 3/4 fir shiplap interior cladding, densepack cellulose in the wall cavity, 3/4 fir t&g fir exterior cladding, 15 lb felt, 1 inch XPS, 1/2 PT ply furring/air space, fiber cement lap siding. ( Most manufacturers seem to suggest not back priming fiber cement) For what it’s worth, the fir cladding is nothing like air tight.
I’m trying to make the felt serve as an innermost WRB with flashing details to route water out to the exterior of the foam sheathing. I’ve constructed a model of the extant wall to work out the details of the design. The foam (1 inch Foamular t&g) will be taped (vertical seams) and Z-flashed (horizontal seams) and treated as a second WRB with window//door details flashed at the foam layer. I’m essentially trying to adapt the Lstiburek Wall Section 1 design from his Guide to Insulating Sheathing to the fact that I don’t have a continuous sheathing surface to flash to.
The house is located in Portland, OR. It is about 550 sq ft with a basement (it is relatively dry and I’m using large overhangs and somewhat improved drainage at the top of the vintage concrete) and will incorporate a Panasonic ERV, an LG Art Cool mini-split heat pump with direct vent, natural gas wall heat for backup. It will have soffit/ridge ventilated comp roof with about 18 inches of cellulose. I’m pretty sure I understand the issue with the ratio of inner-cavity insulation to exterior foam r-values regarding the effect on condensation and that it means paying careful attention to the interior air barrier and humidity levels. My thinking is that the storage capacity of the cellulose and felt (as opposed to housewraps) might also assist in preventing the exterior fir cladding or inner foam surface from becoming a first condensing surface.
I realize that retaining the present dual clad construction presents possible additional challenges in considering additional R and perm values but the alternative gets close to completely rebuilding the structure. (Even now, some of the wall sections will have to be rebuilt as shear panels with plywood sheathing on the exterior to meet seismic requirements.)
A related question has to do with the detail at the top of the rainscreen. I would have a trim detail at the top of the wall to conceal the upper rainscreen vent but I also have the soffit vents just above that. I note that some Canadian references state that venting the wall into the roof is a bad idea so I’m wondering how to isolate the upper rainscreen vent from the soffit vents – or if the mixing of outside air with the rainscreen ‘exhaust’ would mitigate any issue with that air finding its way into the soffit vent. (I recently noticed an APA publication illustrating a rainscreen not vented at the top – another possibility . . . a “drainscreen” I’m told)
GBA Detail Library
A collection of one thousand construction details organized by climate and house part
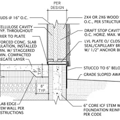
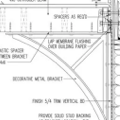
Replies
And, since I'm the one who suggested moving this to its own thread, I'll start the feedback with the response I had already posted:
You seem to understand the issues involved and have come up with a functional wall system that should work well in your climate while keeping the integrity of the bungalow. An inch of exterior foam should be sufficient for your "warm sheathing" approach, combined with the ADA, a vapor-open interior and hygroscopic cellulose insulation in the cavity.
It appears that the fiber-cement siding manufacturers' recommendations against back-priming are to allow the drying of process moisture from manufacture as much as to allow drying from environmental moisture. I would backprime any cellulosic siding that is not applied to a rainscreen, but leaving it unprimed with a drainage space is fine. I would recommend flashing with felt gaskets or aluminum step flashing at butt joints.
In your marine climate, it may be better to not top vent the rainscreen (which makes it a drainscreen), both to prevent extra moisture from entering your soffit vents and to prevent ground moisture from venting up behind the unsealed back of the siding.
Thanks Robert
I do like the idea of a closed-top drainscreen for the walls since it will easily integrate with the soffit vents at the eaves.
I'm being asked by the city to submit a building code appeal in order to avoid using a vapor barrier on the inside. There is a successful appeal on file already that addresses the issue with respect to cellulose insulation, but in my case the low permeability of the foam sheathing adds another reason to insure there is adequate drying potential to the inside.
Kurt,
You might get some help from cellulose manufacturers who typically advocate no interior vapor barrier. Here are a couple of such statements:
http://www.regalind.com/techPDF/General%20Information/Is%20%20A%20Vapor%20Barrier%20Needed%20for%20a%20Cellulose%20Insulatied%20Home.pdf
http://www.idealenergysolutions.com/linked/cellulose%20insulation%20-%20moisture%20and%20vapor%20barriers.pdf
Also Building Science dot com recognizes the importance of "Vapor Open Assemblies" on many of their tracts, such as: http://www.buildingscience.com/documents/information-sheets/3-water-management-and-vapor-control/vapor-open-assemblies/?topic=/resources/vapor_barrier_code_changes