Can there be too much foam insulation?

Greetings,
I am the blessed recipient of a nearly unlimited continuing supply of polyiso foam panels, both 4’x8′ & 4’x4′, varying thickness but I can puzzle that together without any issues. They’re essentially construction site damage rejects so here and there I’ll have corners and edges to patch but I can work tirelessly with FREE material.
I also have a small amount of EPS foam board collection accruing.
The plan is energy efficient wall framing with 2×4’s & rafters 2×10’s filled with Roxul/Rockwool. Layer the north wall and roof with 10″ of polyiso topped with 2″ of EPS and S, W, E walls 6″ polyiso topped with 2″ of EPS.
Zone 6b. Prevailing Northern Winter winds are rough around here. Planning for triple glazing and since the most awesome view is north I will have a fair number of windows with rolling insulated barn door shutters on the north to lock down when winter storms approach. Due to design usage there will be little solar gain from the south.
So given I have a relatively endless free supply of foam is there any notable energy value in installing it any thicker? Certainly the thicker will have more cost in foundation, screws, etc but that is something relatively negligible long term.
Thank you for your consideration.
GBA Detail Library
A collection of one thousand construction details organized by climate and house part
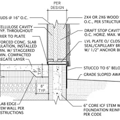
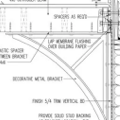
Replies
Once you insulate your walls to around R40, your windows become a much larger precentage of your heat loss. Basically, even if you double your walls to R80, your energy use will not change much.
There are practical limits to hanging thick insulation. Hitting studs through 3" of foam is pretty easy, 6" is pretty hard. Going with wider flange TJI for your rafter will definitely help. You might want to look at splitting the insulation between the inside and outside. You can hang drywall directly through foam on the interior.
Make sure you don't use a single thick layer, aim for 1.5" to 2.5" layers with the seams staggered/taped.
Thanks Akos,
The foam boards range from 1" to 4" and have a fiberglass coating on both sides. I agree with staggering and taping joints.
With such deep insulation I have considered nominal threaded rod protruding from the studs every 2' to hold the foam in place and capping with 1x4's to create a drainage plane with metal lathe being thru bolted making a good mounting surface for the real slate finish. Thru bolting would allow a really snug way to cinch those panels to the plywood sheathing.
Any issues with moisture putting the foam on both sides of the studs?
Should be an interesting project!
I live in the land of double vapour barriers and have seen no issues with them, I know it is a bit of a boogeyman in green building circles.
Provided you have sufficient ratio of exterior to interior insulation, the only thing you have to deal with is water ingress from rain. Something like crinkled housewarp does a good job with that for very little extra cost:
https://www.buildingscience.com/documents/building-science-insights-newsletters/bsi-026-they-all-laughed
Hanging drywall through a couple of inches of foam is pretty easy (part of my roof is built that way). Electrical is also not too bad, just go with surface mounted device boxes on the stud face and add extensions as need to get flush with the finished drywall.
I would rather deal with 2" interior foam plus 4" exterior than 6" of exterior.
I like the sound of the threaded rod, I imagine it being very robust. But after a second thought I wonder how annoying it would be in practicality with installing the foam boards. I don't think you'll be able to easily push the foam and have the rods poke through, Or not have the foam blow out when you start hitting the boards. Then you'd be getting into measuring and drilling holes in the boards, or cutting around the rods. Sounds extremely frustrating. Definitely set up a test rig and try it out before hand.
I personally like screws. They're easy, can sit flush and they've gotten pretty robust these days with lag screws. I've even seen some people set up a jig to screw in at 90deg. I've only done a few lag screws through 6" of foam, not a whole house, but I'm assuming a bit of setup for screws will be easier in the long run. Since you'll have so much exterior foam, 2x4 blocking on the flat against the backside of the sheathing won't significantly effect the thermal performance. lay these in between studs at 2ft height increments. Then you'll have a good 3.5" wide surface to hit. I'm assuming you'll be doing blocking anyway, so this eats into that as well.
Or go with the illicit T stud approach.
I’d say over 4” or so is getting pretty tough to work with. 3” is a good spot to be.
I see no problems with using threaded rod. You may be able to find those specialty fasteners that have a lag screw on one end and 1/4-20 machine threads on the other. Screw those into the studs and let them poke through the foam to the outside, then bolt your furring strips to them. If you can’t get those fancy fasteners, it might make sense to use the 90 degree strut brackets so that you can connect the threaded rod to the side of the stud.
I wouldn’t put rigid foam on the inside of the studs. Too much work that way with electrical and mechanical services, and a double vapor barrier too. I’d pile the extra foam on top of the roof sheathing. Do all your insulating on the outside with foam, basically building a big beer cooler. If the material is all free, the labor vs materials tradeoff is a lot different :-)
Bill
Thank you Bill,
Always appreciate ideas! I truly believe in building science, only thing is this line of building is still in the "now that we think we know what we're doing, let's see what actually works" ;-)
PM
PM,
I like the idea of the threaded rods too, but the complication may be the connection to the furring. Long structural screws have a pan head that doesn't appreciably stick out past the face of the 1"x material. Threaded rods would need washers and nuts that might have to be countersunk, and there isn't much wood there to start with.
Hi Malcolm,
How about since I'm finishing with natural slate; threaded rod through the foam, thru the furring, thru metal lathe then washer and wing nut, leave excess rod exposed and cut to appropriate length as the mortar and stone work encounters the rod -- use like a brick tie???
Note: wing nut easy to snug up and will get locked into place with the mortar
PM
Tightening up a zillion wing nuts will have you hating life in no time. Use something you can put in a nutdriver on your drill.
You might look outside (actually “inside”, in this case) the box: use a T nut in the furring strip to keep things flush on the face. Tighten a nut on the other side — in the stud cavity — instead. This is easy if you used a 90 degree bracket like the strut corner brackets I mentioned. This does rule out the fancy lag/machine screw fasteners I mentioned before though.
I’d use a nylock nut here too, not a regular nut. You want something that won’t loosen over time. Thermal cycling in the walls will tend to gradually loosen fastener in an application like this, so you need something that will resist that.
Bill
Anyone feel like doing the math on heat loss through the threaded rod? (0.150 square inches for each 7/16" rod, r value for steel is 0.0031 per inch) I know this has come up on here before, but don't remember what the consensus was.
Would condensation on the rod, nut, washer, and bracket be an issue?
The fancy lag/machine thread thing is called a hanger bolt. these guys have them up to 12" long in stainless, or standard zinc plated
http://www.hangerbolt.com
I did the math once for the usual nailing schedule for exterior sheathing. The total losses through all the nails was something like 10 BTU/hr — a tiny amount, and that didn’t allow for the relatively difficult to calculate insulation provided by the framing to the nail points. Basically the actual thermal losses is something less than 10BTU/hr. Over an entire house, the additional thermal losses due to nails/bolts for hanging exterior insulation is going to be too small to reliably measure. I’d expect the threaded rods to be used less frequently than nails, so I’d expect something equal to, or less than, the heat lost through nails.
Thanks for posting the name for the “fancy fastener” I mentioned.
Bill
PM
If I successfully attach the photo, you will be able to see just how much heat goes through 8" steel timberlock type screws. I live in a zone 6a-b area with modest snowfall. It can get down to -15F, but winter lows run about zero at 5am and 25F by noon. The dots in the snow are easy to see when it is about 30 out. The deck insulation under this membrane roof is 4" of nailbase over 4" of Polyiso over 5/8 or 3/4 ply. All that sits on 2x8's because the span is relatively short. The under deck was foam flashed at the wall intersect to air seal better, and then batts between over the living area. The 2x8's are staying pretty warm, so the steel screws coming down have toasty toes in relative terms.
I can see the same effect on the roof areas that have a full 8" nailbase over sheathed 2x12 rafters. The 10" screws will make dots appear on the standing seam, even if just dew is forming. I have pictures of this as well....somewhere.
I have approximately 6" of EPS on the walls under synthetic stucco for weight reasons. I would worry about using something as heavy as slate mounted to the furring/mesh unless you have had an engineer okay it. I am in the early stages of another house and I am thinking about how to avoid the heat losses from poking big screws all the way in to the studs. One idea I have had is to use 2-3" foam over sheathed framing as a base insulation. Temporarily held with cap nails. Then place 2x3 or 2x4 furring horizontally with either 24" or 16" clear spacing up the wall, using 5- 6" screws. 1 1/2" x 24 or 16" foam pieces would go between the furring and full sheets of 1 1/2 or 2" material over all that. The vertical furring would then be anchored to the 2x stock with siding attached to that. The 5-6" screws should suffer less heat loss due to being protected by the two inch material. The furring holding the siding will also be under less leverage stress since the screws are only penetrating 2" of foam not 6".
Long screws through the furring and deep foam can get a bit springy if loaded heavily. The trick of drilling them in slightly uphill helps according to some sources. There are charts which will guide you on just how much load can be placed on the screws by length. Maybe someone on this side can direct you to current ones. One potential advantage to my double furring idea is the screws get a lot cheaper if 6" or under. The 8-10" ones cost around a buck a pop if I recall correctly.
Shooting in long screws is possible and the crew on my job did amazingly well. I only found 3-4 misses out of hundreds of screws. The heat losses from long screws is of course a subject of great discussion. Some feel the losses are trivial in the grand scheme, others suggest using stainless steel to minimize. My work around idea uses shorter, cheaper screws and thermally guards the first level of conduction from the warm side.
Unfortunately, it means three trips around the house, lots of cutting foam and awkward detailing around the windows and doors. I remain uncommitted to this idea, but there it is for what it is worth. I envy your free foam. Do be sure to seal off the bottoms with metal flashing to keep the critters and bugs from gaining easy access. The metal tray I used for the EPS is definitely a direct link for cold temperatures to the sheathing layer, but a trick detail makes that connection point below my rim boards in most places. Best of luck with your inspector, many don't quite get foam on the outside.