Foam adhesion and Air Sealing
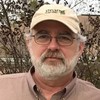
The most significant materials failure we have ever had has happened on my own house. I completely changed the roof assembly on my 1950 ranch-style house. We vacuumed all the old nasty insulation out. And spay foamed the underside of the roof decking and rafters with open cell. I was worried about being able to get close enough to the outside plate line to adequately seal. I chose a spray foam company that guaranteed that they could get a good seal. Getting in the attic and watching them work, I thought they had it. But a thermal camera showed otherwise. The roof is only 4/12.
To address the failed sealing at the plate line of the outside wall, I removed the roofing. We cut a 16″ swath of decking at the outside plate line and sealed it from the top. We went back with a popular ice and water product rated for going under a metal roof and put on a standing seam metal roof, followed by a solar array.
Two years later, the underlayment failed and started dripping out from under the metal. The company has been little help to this point. Their warranty department has drug their feet and provided no information on how to deal with this. Meanwhile, tar is dripping all over my house, landscaping, and deck. But this is not about poor me.
It appears, from the experience of others, that the proper remedy is to remove the decking. Here are a couple of pictures from another project where decking was removed in a restricted area of a roof. Notice that the foam stays in place, which finally gets to my questions.
1. How good is the air sealing of spray foam, if the decking can be peeled off of the foam leaving it in place?
2. When removing decking from a whole roof, I would be nuts to leave the existing foam in place, right?
GBA Detail Library
A collection of one thousand construction details organized by climate and house part
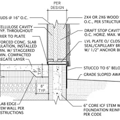
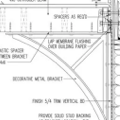
Replies
I think the main issue you have here is that water got to the roof sheathing, and caused the OSB to disintegrate. Once the OSB sheathing comes apart, spray foam has nothing to "adhere" too. I don't think the problem here is the spray foam. That first pic you posted makes me think you had a failure with the flashing along the side, allowing water to get into the sheathing on that first rafter bay since there appears to be a lot of rot there.
Water getting into a roof is not something to blame on spray foam under the sheathing. Spray foam is NOT there for water protection. It wouldn't be the responsibility of the spray foam contractor to deal with, either, it would be the contractor that warranted the roof itself, since the roof let water get to where it shouldn't be.
Since the rot seems to be downslope from the penetrations, or along roof edges, that is why I think this is a flashing failure, and bulk water intrusion. If the problem was with the spray foam air sealing, I would expect moisture-type failures and not bulk water type failures. Moisture related failures from moist interior air working up into the roof assembly tend to cause rot in the higher areas of the roof, not lower sections down slope of penentrations like you see in your pics.
I'd go after your roofer, not your insulator, from what you've shown in those pics.
Regarding leaving the old spray foam in place when removing the roof sheathing, you probably won't have a choice -- in areas where the sheathing is intact, you're probably going to cause significant damage to the spray foam insulation, requiring the spray foam to be reapplied. In areas where the sheathing has disintegrated, it will probably be able to be pulled off of the spray foam layer, but you'll never be able to get the "fully adhered" spray foam layer after replacing the sheathing, which is why you'd be at risk of moisture accumulation in the resulting non-adhered gap. That very small gap might not be a problem in practice, but since you're likely to need to replace a lot of the spray foam in other areas anyway, I'd use a sawzall to cut out the spray foam in the areas where the sheathing rotted, and then have the insulator reinsulate the entire roof in the area you're having work done.
Bill
What is your climate zone?
The photos of another project look like it might be closed-cell foam, not the open cell that you have.
Grace has two "levels" of high-temp underlayment, both supposedly safe for use under metal roofing. I learned the same lesson you did, using the regular stuff, but I have not had a problem with the high-temp version. Are you sure the installers used the right product?
I think a better option in your case would be to add some rigid above the existing sheathing. This saves you having to pull the deck plus add some extra R value which is not a bad idea with open cell spf in cold climate.
With the rigid over the peel and stick, it will be colder and stop oozing*.
If this is not an option, and you want to pull the whole deck, I think the simplest would be to strap out the rafters and build a went channel above the SPF. New deck over the strapping to finish. This way any moisture that can now get there will be vented away.
*Sometimes mod bit peel and stick will ooze from contact with pine tar. If your roof is newer board sheathing, this can be the problem at which point your only option is to replace the deck.
Michael, we used the right stuff. The warranty is slow-moving but approved. I didn't consider that the pictures might be closed cell.
Akos, I had considered adding an insulation layer. That would be the easiest solution. The problem is the risk of that not doing the trick.
I have built this stack up with regular I&W under rigid (2.5" plyiso above, r24 batts in rafters). No issues with regular I&W oozing.
If the problem is heat adding a thick layer of rigid above should solve it. Quick check is if the oozing is only there in the summer. You can also try it on one of the smaller sections of the roof first.