Foam adding load to roofs?

In a previous post, I referred to the request, from my township, that if I thicken my unvented roof by adding rigid foam insulation, I enclose load calculations, certified by an engineer, for the added loads. The alternative, which does not require certified load calculations, is closed-cell spray foam between the rafters — 5.5” to be specific, to reach R38.
For what I am concerned, that ship has sailed; I’ll go for the spray foam. However, I thought of running some calculations and making comparisons, to see what folks on this forum think. Please note that, in my calculations for the thick roof, I do not consider any added weight from lumber because the way in which my roof is built would call for removing more lumber than what would have to be added when thickening the roof.
a) Thick roof (1.5” polyiso = .32 Lb/sq ft + 2.5” XPS = .49 Lb/sq ft = .81 Lb/sq ft). If adding 5.5” of fiberglass between the rafters, that would have been an additional .46 Lb/sq ft). Total load added: 1.27 Lb/sq ft. (By the way, total R value: 42.5)
b) Spray foam (5.5” = 2.25 Lb/sq ft.) (Total R value: nominally, 38)
(Some of these numbers are somewhat indicative, as different brands publish different weights, but, for the closed-cell spray foam, I chose the lightest number I found.)
a), but not b), raises questions regarding “added loads.” What am I missing?
GBA Detail Library
A collection of one thousand construction details organized by climate and house part
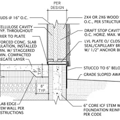
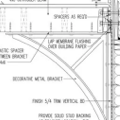
Replies
The "missing" thing is that the local officials aren't familiar with exterior insulation, and possibly that there's no prescriptive code addressing it, so they default to asking for an engineered design. The actual "added load" from rigid foam is going to be almost negligible for most structures and for sane amounts of rigid foam -- for example, in my area the ground snow load is 20psf, and a typical dead load for a shingled roof is 15psf, so the structure needs to be designed for roughly 35psf minimum (ROUGHLY -- not getting into a variety of other factors here for simplicity). My 6" of roofing polyiso, at ~2 pounds per cubic foot, adds a load of 1psf, roughly a 3% increase. As you pointed out, any type of insulation added to the interior also adds load.
Now, the thing that is actually more important in my view, and the thing that the building authorities in my area specifically asked for more information on, is how the roof itself is fastened to the structure through the insulation. Do the calculations, and there might actually be as much uplift that you need to resist as there is downward load, in the design (worst-case) wind scenario. The thing you really need to have engineering support for would be specifying the fasteners to attach the roof to the structure (some fastener manufacturers do have pre-engineered designs or engineering support for this though).
In my case, there were several other parts of the project that needed engineering, so it wasn't a problem to get the roof stuff specified & stamped to the AHJ's satisfaction.
Thank you, jonny_h. Indeed, I had not thought about the uplift issue. In any event, you’re spot on about the prescriptive code not including certain options, and the townships having to ask for an engineering report. The inspector has been collaborative and nice throughout. And to be fair I was not told I could not do it - only that I needed an engineer’s report. That would not be cost effective; moreover, it’s been hard to find a roofer who is acquainted we what I’d like to do. So, that project is abandoned for what I’m concerned. I was just curious on hearing people’s reflections on the matter.
matt2021,
Your 5.5" of spray foam at R-38 is R -6.9/inch. This is a figure considered to be fantasy by many on GBA. Also, your roof's functional R value of the roof will not be R-38 in any case, as thermal bridging of the rafters will require a calculation to get a corrected value. Solid 2x stock loses more than I-joists.
Additionally, for CZ6 or CZ7 a proper balance of your exterior insulation relative to the interior insulation would need more outside to be safest. You show approximately R20 above and R-19 below. Depending on CZ and interior details, this could be a little bit risky. You could substitute all polyiso instead of the blend with XPS. The fall in R value from cold is a bit over done, as the full thickness of polyiso doesn't fall to ambient in one mass.
I would also point out that getting a good closed cell job can be tricky and if it goes wrong it can go horribly, horribly wrong. Even if you get a good foam job there is the long term problem of repairs to the sheathing if something goes wrong top side. The sheathing will be quite firmly welded to the foam and re-foaming will be a nightmare.
You could try to point out that spray foam is actually heavier than the original plan, but I suppose they might default to "get an engineer to stamp it". Johnny H is right the fastener issue and uplift seems more urgent than the weight question.
Onslow, thanks! Indeed, I’m aware of what you mention: R38 not truly being such (having read Martin Holladay’s article about that); thermal bridging; and future issues if I ever need to replace any parts of the sheathing. Indeed, I’m planning to add a layer of polyiso under the rafters to mitigate thermal bridging. The proportion of insulation above and below the roof sheathing would have been fine for my climate zone by the way (I need a minimum of 41% above). And XPS was mentioned only because I have that already (purchased from someone who had leftovers), and because the only roofer who had followed me more on my idea liked XPS (go figure!). As I said, sadly, the thick-roof ship has sailed for me, and I will have to spend good money on a worse roof assembly. Yet, I was curious on people’s thoughts, here, about the loads.
This is perhaps slightly off topic but how are we supposed to make progress if building departments are so uneducated about this sort of thing that they don't realize the weight of a few inches of foam insulation is negligible?
Do plan checkers in these offices have to do any kind of continuing education the way architects and engineers are required to do? I'm guessing not.
Jollygreenshortguy, I believe there might be the issue mentioned by Jonny_h above, about the uplift. In general, there is the issue of the prescriptive code: I suspect that in all such cases, the building departments cannot but ask for an engineer’s report. Your point still applies in a way: the code should be updated - at least at the state level - and be opened to the new, more environmentally friendly approaches.
Yes, I have no issues about the question of fastening the roof for uplift. That's totally legitimate and should be covered up front in the drawings. Fastener schedules are a standard part of good construction docs. If they're missing the plan checker should certainly be concerned.
It's the misplaced concern about the weight of foam insulation that I was remarking on, that's all.
matt2021,
Don't complicate matters more than you need to. If you are going foam between 2x10 stock the excess heat loss is under 100 btu/hr for the roof. I think I used 0F as your 99% point. Mineral wool is on slightly better than fiberglass batts and for the wall area you have left the differences would be negligible. Not worth the cost. Same for all foam above the windows. You would gain resistance to condensation on the back of the sheathing with the flash and batt method. For the very small area of wall left and having the foam sprayer on site anyway, it might pay out over time for peace of mind. Don't forget the numbers I gave you are for coldest conditions and most of the year all values are lower.
Onslow,
Thank you very much for the additional advice! Unfortunately, I have to confess that I am not 100% sure I understand what you are suggesting. Let me try to reconstruct it:
"Don't complicate matters more than you need to. If you are going foam between 2x10 stock the excess heat loss is under 100 btu/hr for the roof."
Do you mean to suggest that I should NOT bother with adding a layer of polyiso foam board under the rafters? (The rafters, by the way, are 4x6s, 24" OC.) Is that what you mean by not complicating things more than it's needed?
"Mineral wool is on slightly better than fiberglass batts and for the wall area you have left the differences would be negligible. Not worth the cost."
Are you suggesting that, in the walls under the windows (or any walls for that matter), I should not spend more for mineral wool, as the performance of fiberglass is almost the same for those walls? If so, I will definitely keep that in mind. It turns out that I already have some mineral wool (leftovers purchased at a good price); so, I might as well use it; yet, I am not sure I have enough, so your reflections are helpful anyway.
"Same for all foam above the windows. You would gain resistance to condensation on the back of the sheathing with the flash and batt method. For the very small area of wall left and having the foam sprayer on site anyway, it might pay out over time for peace of mind."
Are you suggesting that spray foaming the walls above the windows is also a waste of $$, unless I want to do it to gain resistance to condensation, and hence gain more peace of mind that way? To be honest, I was having second thoughts on using the spray foam for any portions of the wall because the thought of having the nice ZIP R sheathing I will be using, and all the studs... all "glued" together scares me in case I ever have a problem of, say, water infiltration, and need to investigate things behind the sheathing, or within the wall cavities. The reason why I thought of doing it was to have a very good air and vapor barrier, since the installer is coming to spray the ceiling any way. Likewise, I am thinking of having the floor's rim joists just to have the air sealing benefit of doing so. In any event, I am definitely going to leave the walls under the windows alone, and fill them with fluffy insulation, so as to be able to access wires, or, again, do any repairs that might be needed down the line. Are you suggesting that, after all, that's not the most rational plan, and I should only have the ceiling spray foamed (plus the floor's rim joists, I guess), unless I desire that "peace of mind" you are mentioning?
Please forgive me if I misunderstood your suggestions, whether in part or whole, and thanks again!
Mineral wool is a little better in terms of R per inch than regular fiberglass batts, but you can get "high density" fiberglass batts that are the same R per inch. I would probably use regular density fiberglass batts here though, since they are more "squishable" and will probably be easier to install well against the less than flat surface under the spray foam. Fiberglass batts are also quite a bit cheaper. I like mineral wool batts in walls, where they have an advantage in terms of being easier to install well compared to fiberglass batts, but in roof assemblies I'll go with fiberglass if I need a batt, since the installation advantage isn't as important there usually, and fiberglass is cheaper.
I'd foam above the windows. Once you have the crew on site, the additional cost for a few more square feet of spray foam isn't that much. When I redid my "sunroom" several years ago, I spray foamed the roof, because it was a very low pitch unvented cathedral ceiling, so spray foam was the only practical option. I spray foamed two of the exterior walls too, which added maybe $100-150 to the job, and saved me some work. If I wasn't already spray foaming the ceiling, I would have used mineral wool batts in those walls.
I agree with the earlier posters that the building department is probably just not familiar with exterior insulation on roofs, and if they get a set of sealed drawings they are off the hook in terms of liability (the engineer takes responsibility for sealed designs). It surprises me the city wouldn't understand exterior rigid foam on a roof though, since nearly all commecial buildings are insulated that way. My guess is they just aren't used to it on a wood framed structure. The reality is that the drywall likely adds more dead load than the rigid foam does, but the code book talks about the usual ways to insulate, so the city is "playing it safe", from their perspective, and not wanting to go outside of what is in the code book.
This is a common issue with local building departments and high efficiency green building. The building departments are not familiar with the latest high performance building techniques, and no one wants to sign off on something new and different for fear of a failure down the road and a potential issue with liability. This means more engineering tends to be required, and a lot of convincing sometimes with the inspectors. Some people propose beefing up the code to require more stuff, but I don't like that option since it tends to go overboard, and also restricts flexibility with projects that aren't quite "regular" enough. My preference is to try to educate the building department people, which isn't all that easy to do, either. I run into these same issues commercially on ocassion, usually with energy codes, with the datacenter facilities I design. Building departments are never familiar with these facilities -- they just don't see them often enough -- so our solution is to just provide sealed drawings for everything and be done with it. We tend to have big budgets though, and we put a LOT of attention into operational efficiency of the facilities since electricity is our biggest operating expense, so it pays off bigtime to put in design effort to cut down on cooling load (we have no heating load).
Bill
Thanks Bill!
My ceiling does not have any room for additional, fluffy insulation: it will just be 5.5” of spray foam. I will have to decide whether to add a layer of rigid foam under the rafters, before installing the drywall, to mitigate thermal bridging at the rafters, or whether that is not worth it.
The circumstances of your sunroom project sound almost identical to mine. I, too, can have the top walls spray foamed for not much more. My only concern at this point is with having my nice insulated sheathing, and the studs, all “glued” together by the spray foam. Maybe I worry too much.
matt2021,
Yes, my first point was not to add a layer of polyiso to the underside of the roof. However, I was making the mistake of guessing you would be using common framing lumber like 2x10's on 16" centers for the roof. My bad. Your choice of 4x6 on 2' centers does alter my answer substantially and I would recommend that you put a layer of polyiso in the bottom before drywall or other finish.
My bad guess can now serve as an example of why one needs to do whole wall, whole roof thermal calculations before committing to a particular set of choices. While the final numbers that will fall out at the end here are trivial compared to your window losses, it may be instructive to see how seemingly small changes affect the functional R values of completed surfaces.
Basically, I de-rated a bit aggressively for your built up roof simply to speed up getting a rough answer. With 4x6 framing under the top side insulation build up, you actually show a whole roof R value of ~R-37.4, (ignoring dry wall, air films and so forth). If you had used 2x10's with topside insulation, your whole roof value would be ~R-39.3. The move to spray foam between the 4x6 rafters has a quite pronounced affect on your whole roof R value. By using 4x6 material your roof thickness is essentially like a 2x6 wall. Sorry to use with your project as an example, but perhaps it can serve as a lesson on why some choices have unexpected outcomes.
For your particular roof I am assuming you have 345 sf of thermal roof exposure to deal with. (NOT the eave to eave area) The 13 pieces of 4x6 joists of 14.5' lengths = total 55 sf of area needing separate heat loss calculation from the spray foamed area between joists. The suggested R value of pine is R1.5/inch, so your nominal 4x6 (actual 3.5 x 5.5 ) gives you R-8.25 as set. Final build up, ~ R-9. Spray foam at 5.5" of depth and a more realistic R-6 would give R-33. For calculations, I will concede the R-6.9 being sold to you. Drywall, sheathing, roofing materials and air films could get you there as a final build up.
55 sf of your roof area will be R-9, the balance of 290 sf will be R-38.
55sf x 65 delta T = 3575 divided by 9 = 397.2 btu/hr
290 sf x 65 delta T = 18,850 divided by 38 = 496 btu/hr
Total heat loss through roof, 893 btu/hr at the design temp of 0F ambient, 65F interior.
(Active roof area being calculated for) - 345 sf times delta T of 65 = 22,425 divided by 893 btu/hr = effective R value of combined elements. Effective ~R-25.1. This is R-10 less than I speculated and nearly R-14 lower than feasible with the original topside insulation and 2x10's.
Without the topside insulation the heavy joists are no longer protected by an R-20 "winter coat". With the R-20 layer, the 55 sf of timber value of R-8.25 now acts as 55 sf of R-28.25. If you run the calculation for the original build up with foam on top you will get ~ R-37.4.
Adding 1.5" poly iso on the bottom side of your current choice will now be a very good idea. The boost to the R value saves you from a hot ceiling all summer. If you take 1.5" polyiso as R-9, then the timber area R value becomes R-9 + R-8.25 = R-17.25. With final finishes we will give it R-18 for purposes of calculation.
55 sf x 65 delta T = 3575 divided by R-18 = ~199 btu/hr, not very magically half the prior value.
290 sf x 65 delta T = 18,850 divided by R-47 = 401 btu/hr, a gain as well.
345 sf x 65 delta T = 22,425 divided by 600 btu/hr = R 37.375 lower end of where one wants to be with a roof in summer.
Now, all this calculating is somewhat academic thanks to your window area. You will be in the range of 4200 btu/hr at 0F design point for your windows and doors. This is seven times the roof loss and likely twice the total of walls, roof and floor. Most of the year won't be 0F so the value of chasing small increments of R value in one area can become somewhat pointless. However, comfort should be addressed along with heating system requirements to arrive at a good balance. Pocketbook issues, code compliance, construction problems, durability, etc, etc, are the herbs and spices to the primary mix.
In general when analyzing whole wall R values, the "framing factor" of 25% is an oft quoted rule of thumb to keep actual losses somewhere near to reality. I have seen McMansions being built that had wall areas with framing factors in excess of 30% thanks to lots of jigs and jogs in exterior walls and/or myriad windows. The workers happily stuff insulation into the remaining space, but it doesn't really matter a great deal if it is fiberglass or rockwool by then.
This was the second point I was making about not being worth the cost difference for your very small wall areas. If you have free or bargain materials, go for it. If buying new, then the up charge will not be rewarded. I forgot you were going with ZipR on the walls, so my comments about condensation on the sheathing is moot. I would say the spray above the windows is questionable as well. Air sealing for your case should be automatic if the joists are going past the wall. The peace of mind I spoke of was not having hidden condensation issues. Just look for where cold surfaces and air exchange can occur.
For further reading and better diagrams than I can make, I recommend the link below.
https://www.jlconline.com/how-to/insulation/understanding-r-value_o
Onslow, thank you so much for this extremely rich and helpful explanation! I do hope that others can benefit from it.
One point of clarification: I haven’t chosen the rafters’ size; this is a retrofit of an existing structure, unfortunately.
The roof joists do go past the wall on the long side; I don’t have eaves though. And I don’t know how much I will be able to obtain a perfect job from whoever will do the ZIP sheathing installation for me. So, perhaps the spray foam above the windows will take care of the air sealing, and should be done for that. (I know that insulation should be used to insulate, and air sealing addressed as such.) I confess that I am still debating a bit.
I am confused about “air films”: for the ceiling, I though that the closed-cell spray foam would have taken care of everything, with no need for any additional barriers; and for the walls, I though that the fluffy insulation was supposed to be let dry towards the inside, and that it should be either mineral wool or unfaced fiberglass. I fear you touched, there, a topic on which I don’t know enough.
I will definitely go for the polyiso layer. I had never considered 1.5” though, but a max of 1”. Given the sloped ceiling and the need to raise the floor, the height at one wall is going to be around 7’; so, every inch counts unfortunately. For the same reason, I’m hoping to skip any furring, and screw 5/8” sheetrock to the rafters, using long screws, though the polyiso board. Is that a sound plan? And would it still be viable if using a 1.5” board?
matt2021,
If I understand correctly, you are stuck with existing 4x6 joists that don't extend very far past the header line. I guess as long as the inspector is down with it, go with the flow. I do think that sistering on some 2x6 tails to extend the roof line would be wise. It will drop the snow and rain further out from your posts and windows sills as well as provide some shading in the summer when you need it the most. I realize the view from inside will be impacted a bit, but check out what it looks like when sitting a a chair rather than standing. I suspect you will be relaxing on the new porch once done, not standing up.
Of course, best to check with the building inspector first in case they are real antsy-pantsy types that will ask for an engineer to review it. You can try to sell it on the basis of rain management. After all, I think eaves of 16-20" past siding should be pretty non-controversial. A framer can tell you how much 2x6 needs to be inside the header line to support the extended eave. Perhaps equal distance inside and past the header line would be adequate. I would block between the joists along the header line after placing the extensions to beef up the roof sheathing. The roof foam will also have a firm stopping point in case the Zip R is slightly short when set. I do tend to overbuild.
The 1.5" polyiso was suggested because you had specced it in the original profile. If 1" is more available the hit is pretty small on the scale of things. Roofing supply houses should have all sizes. You could then use 2 1/4" screws on the 1" and 5/8" , though I would try for 2 1/2" and avoid needing 3" if going with 1 1/2" polyiso. The 5/8" will span the distance fine. Don't forget your blocking if you are planning on any lights or ceiling fans.
The air films I was referring to are literally the film of air on inside and outside surfaces that do count when calculating total U value of a wall or roof assembly. The effects on heat transfer between air and solids is real if pretty small. Same for water and solids. If you were building a boiler or an air conditioning coil, then you need to detail it. For practical reasons, it is best to just model the primary elements and not get too crazy. Bottom line, don't worry about them, just worry about air leaks in the envelope to control for moisture risks. Windows are dominating the calculations.
Onslow,
Thanks! To clarify:
- I do have a one-foot overhang on the “front” side of the room, that is, where the 4x6 rafters end, away from the house. So, one of the three sides does have that protection, fortunately. Thanks for the advice, though, on how to present any plans to create eaves. Maybe I can pursue that in the future, if I ever redo the roof, for eaves on the two other sides.
- Sorry for indicating 1.5” of polyiso under the rafters; that was a mistake. Maybe I was adding a 3/4” iso board to 3/4” furring strips. Speaking of “overbuilding,” which to me sounds like a good idea, you do not think that furring strips are needed, if I read you right?
- A question that had occurred to me, and that maybe can be of interest to other members of the forum is this: in an assembly like the one I have (with 5.5” closed-cell between the rafters) which is better: 1) a continuous layer of polyiso board under the rafters, with drywall fastened to the rafters through the foam with longer screws; 2) a continuous layer of polyiso board under the rafters, furring strips, and drywall fastened to the furring strips; or 3) strips of polyiso board nailed or screwed to the rafters, and air between the rafters, and then the drywall fastened, with or without furring strips? Do you see what I mean? (My personal inclination is towards 1), maybe with glue applied to the back of the drywall, where the drywall will touch the board.)
- Finally, I wonder: are we talking about foilfaced polyiso under the rafters or other kinds? And should the foil face up or down?
In my mind the above questions are somewhat related. With the spray foam constituting a vapor barrier, I wonder whether it’s better to have no other barriers (hence using strips of polyiso only for the rafters and not the entire area, or, if using full boards, whether foil faced and in which direction).
I hope this makes sense. Thanks!
matt2021,
Skip the glue, you are not gluing to framing if the foam is first. You can do strips of polyiso if you like, run the numbers and see how the effect is. Kinda tedious and the full sheets aren't that much more cost. Foil is just for strength and will have no real function without an air gap of 1/2" or more. Moisture is taken care of by the depth of the foam. Furring strips to hang the drywall are nice if you need to run wiring cross-wise of the joists, but cost you head room. 5/8 dry wall is pretty tough stuff and will span the two foot joists well.
Onslow, Thank you very much for your response, and sorry for being so slow at seeing it and responding to it. That helps a lot indeed. I'll go without furring strips, I think, as I am planning to use wafer-style recessed lights, and the wiring will be done before we have the spray foam applies.
And, yes, I'll use full sheets of polyiso.
Thanks again!