Fluid-applied WRBs applied indoors on plank sheathing

I’ve got a old house (plank sheating with brick outside which cannot be removed because of historical protection laws) which we are gutting to the bones to reinsulate. We are especially concerned with air leakage.
I’ve found two products that seem to be easy to order in Canada:
– R-Guard Cat 5 Liquid Applied WRB 5-GAL
– Proclima VISCONN
We are expecting the planks to be dirty since they are 100 years old. We’ll do our best to vaccuum and clean it up but there is only so much that can be done. Applying tape between each plank and in between studs is too time consuming so we were looking at liquid applied instead.
Would those two products work just as good? Can they actually be applied on the inside of sheating even if not ideal?
GBA Detail Library
A collection of one thousand construction details organized by climate and house part
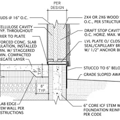
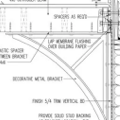
Replies
Before you start, be sure to read Martin's article on insulating old brick walls: https://www.greenbuildingadvisor.com/article/insulating-old-brick-buildings
Also...
You might want to check out Aeroseal as a possible option for air sealing: https://www.greenbuildingadvisor.com/article/aeroseal-rolls-out-air-sealing-technology-for-houses
PL C,
Do you have any idea what is on the outside of the sheathing? Also, what is your plan for insulation?
We had a structural engineer visit and inspect. He has experience with this type of old house. This is how we assume there is plank sheating on the outside. This is a early 1920 brick house so there was not much air sealing done at the time.
According to him we can expect the wall assembly to be: brick->air gap->plank sheating->studs ("real"/old 2x4)->lathe & plaster. Worst case scenario there is no sheating at all and we have to air seal the brick. It would be surprising to see a double wythe brick wall although the brick above the windows and no weep hole is interesting. Attached a picture of the exterior wall.
We are waiting for the permit to be approved & transaction to go through before we are allowed to open walls and confirm. This is a 1923ish brick house in Montreal, Quebec (zone 5).
At the moment the plan is to use cellulose but the engineer mentioned we have to be careful with the added weight. We might have to go to mineral wool bats instead if the structure is not strong enough. Using loose wool was also very interesting. Space is at a premium and air quality is very important so we can't make the wall thicker on the inside and are not comfortable using spray foam because of the VOCs/ecological concerns/no way to dry.
Target wall assembly at the moment is:
brick->air gap->plank sheating->studs ("real"/old 2x4) + cellulose or wood fibre->intello plus->drywall
We have been running into challenges getting good contractors since the ones who do leed/passiv/ecological don't want to touch a old house and the ones who do regular old houses don't care about air sealing and innovative products.
Pier-Luc
Looking at the brick, there doesn't seem to be any ties. With interior 2x4 studs, very little chance of it being a double brick.
Since the insulation will end up supported by the foundation, I really doubt there are any weight issues. Compared to house loads on the foundation, the weight of 4" of dense pack cellulose is noise (something like 20lb per liner foot of wall).
Air sealing planks is next to impossible unless you cover it with peel and stick or spray foam. The gaps will be too big for any liquid applied product. Even with peel and stick over the interior cavity, it will be a challenge to get it air tight enough. Your best bet is dense pack cellulose/fiberglass which will do a pretty good job of sealing up the leaks. Not air tight, but good enough. Anything non dense packed will leak too much. Insulation batts won't do much on this front and they are hard to put into non standard wall cavities such as your real 2x4.
The most important part to deal with is your flashing details. With the new insulation your bricks will be colder and will have less drying potential, any water leaks will cause a lot of trouble. Looking at the picture, it looks like you have wood window sills, those should be caped with metal and ensure the windows sills drain towards the outside.
You might also need to install some weep inserts at the bottom of the brick for extra air flow to aid in drying.
The engineer concerns regarding weight were mostly around the third floor (it is a four square house with a bedroom in the attic). The 3rd floor walls don't rest directly on the foundation. He basically said static load had a risk of making the floors sag and to be careful. He was unable to do any calculation since we don't know what is in the wall yet.
We had the same concerns regarding the bricks. From reading online and what the engineer told us air sealing (as long as it is vapor permeable) would not be an issue but we have to be careful with insulating "too much".
We do indeed have wood sills. If we can convince the town to allow us to replace the windows we will replace them with triple panes windows and do a good job of flashing and sealing water infiltration.
Peel and stick is a solution we looked at but very labor intensive and that is if we can find someone to do it right.
I spoke with a rep at Prosoco. They think it would be a good application.
We'll give it a try using a sample and see if it sticks.
I'm considering a similar application of fluid applied WRB on interior of plant sheathing. How did it go?
I've used the R guard Cat 5 WRB on exterior of plywood sheathing for the water barrier on plywood surface ( I used Prosoco joint and seam sealer and fast flash for air and water sealing of joints and cracks). I'm surprised that the Prosoco rep suggested the cat 5 for plank sheathing. The Cat 5 did not span cracks well, and required multiple applications to fill small cracks in the plywood. I would not be surprised if expansion and contraction of the planks would eventually reopen the joints between planks. Prosoco instructions say to fill joints, cracks and knots of 1/4" or less with Prosoco joint and seam sealer or R guard fast flash. Larger joints required backer rod. R guard fast flash can be purchased for application with paint roller or sprayed, and I would think would have the structural integrity to span plank joints over time, but haven't used the rollable version. Fast flash also comes in caulkable sausage tube version for larger cracks. Larger joints might require Prosoco joint and seam sealer. These are easy to use products, and are very durable, but costly. Really would be worth pricing out how much it would cost to air seal the field of each stud bay with non structural sheathing or rigid EPS insulation, and then just seal the edges vs. the liquid applied membrane for the entire stud bay, since the liquid applied barrier might require multiple applications to get good air seal.
https://prosoco.com/product/r-guard-fastflash/