Flooring puzzle for uninsulated slab + humidity

I have a 1965 Sears cape in coastal Rhode Island (Zone 5, moist). It is built slab-on-grade, and I don’t think there is any insulation or vapor barrier under the slab, because 1965. Currently there is carpet laid on the slab with a pad underneath.
In the Summer, during times of high humidity, the relatively cooler top surface of the slab becomes a condensing surface. This creates moisture in the house and carpet. I would like isolate the top of the slab from the moist interior air, and lay an alternative flooring material that won’t hold moisture. The challenge is that the first floor ceilings are only 7’6″, so a thick insulated floor is not an option. I may be able to add a total of 1″ to the floor without making the ceiling seem too low.
My current thinking is that I need to (a) lay very thin layer insulation on the slab, (b), air seal over that insulation to prevent moist indoor air from reaching the top of the slab, and (c) add a thin moisture-tolerant flooring material that also provides some insulation.
For example, coat slab with liquid-applied moisture barrier. Then a layer of 1/2″ foil-faced polyiso, with taped seams. On this, lay 1/4″ plywood subfloor. Top with marmoleum or cork flooring.
Another option is the Forbo Quick Fit subfloor system, that appears to feature a taped insulating layer under a two-layer subfloor, which is topped with marmoleum: https://www.forbo.com/flooring/en-au/technical/subfloor-underlay/pmty4i#panel_6
I’m open to suggestions.
Thanks,
Chuck
GBA Detail Library
A collection of one thousand construction details organized by climate and house part
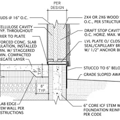
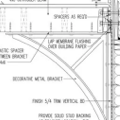
Replies
Also consider a test of this potentially less expensive option:
a) keep interior humidity <= 50% (use a dehumidifier) and,
b) a vapor/air barrier, closed cell soft foam pad under the carpet (in a small test area)
Whatever you do, make sure it can dry upwards.
I'm in the middle of installing 7mm vinyl plank over Dry Barrier on my basement slab. This might be an option for you due to being a completely waterproof combo with a small air gap. Although this combo does bot have much of an R-rating.
I did not level the first room I completed, which resulted in a hollow sounding floor. This week I'm attempting a bigger room and using self leveling compound for a (hopefully) better result.
I had also purchased a roll of DMX Airflow underlayment and the product seemed OK. However, the DMX LVP product I was considering was continuously out of stock and the customer service IMO was awful.
Chuck,
If you are sure that the slab has no vapor barrier beneath it, and that it is not getting wet from leaks, your first layer above the slab should be a vapor barrier. Poly sheeting will work. Then, as you noted, some rigid foam will help prevent condensation and separate your flooring from any condensation that does occur. You can then install a floating plywood subfloor and flooring. As Jon pointed out, some level of dehumidification may be necessary, but you can test for indoor humidity levels first, if you'd like. No one wants to give up head room in there basement, but you can't install a healthy basement floor without the right layers. I think you will learn a lot from this article: https://www.greenbuildingadvisor.com/article/installing-rigid-foam-concrete-slab
>"For example, coat slab with liquid-applied moisture barrier. Then a layer of 1/2″ foil-faced polyiso, with taped seams. On this, lay 1/4″ plywood subfloor."
If using foil faced foam the liquid applied moisture barrier is redundant. If there is any chance at all of flooding or high subslab moisture, 3/4" unfaced Type II (or denser ) EPS would be a better choice, since polyiso will wick and retain moisture, taking forever to dry through foil facers.
While the R3 is enough to prevent most summertime moisture issues, 1/4" plywood subflooring is nowhere near stiff enough to prevent permanent deformation of the polyiso in high load areas. Half-inch t & g plywood would be the absolute minimum, with the seams of the plywood staggered by at least a foot from the seams of the polyiso, and through-screwed to the slab with exterior grade coated masonry screws.
Thanks for the input
@Jon r - definitely want to ensure things can dry to the inside. Above all, I want to avoid creating a moisture trap that makes things worse.
@ Brian - thanks for the article reference. My challenge is that this is the first floor, not the basement, so losing ceiling height is very undesirable. Miss hearing you on the FHB podcast, btw.
@ Dana - thanks for the insight on barriers, foam type, and underpayment. At the minimum thicknesses if each, I will gain 1.5” of floor height, which may be too much.
What about LVT directly on the slab (with or without a moisture barrier underneath? Still a potential condensing surface, but more likely to dry, versus wall-to-wall carpet.
Controlling indoor moisture with a dehumidifier or A/C is also in the cards.
C
>"What about LVT directly on the slab (with or without a moisture barrier underneath? Still a potential condensing surface, but more likely to dry, versus wall-to-wall carpet"
Either LVT or ceramic tile on the floor should work fine for a slab-on grade. If ceramic, a vapor retardent concrete sealer should go on the slab first. (Vinyl tiles are true vapor barriers on their own.) Carpet could have mold issues, since it insulates the slab from taking up heat over the winter, resulting in a cooler slab temp (and higher mold potential) year-round.
In 1965 slab edge insulation was still pretty rare, but if you're up for it, digging down to 2' below grade along the perimeter and adding 2.5 - 3" of EPS (R10-R12-ish) all the way up to the sill plate and inserting flashing to kick the water out to the exterior side of the EPS makes a difference in limiting how cold the slab & soil gets over the winter, reducing the summertime moisture accumulation issues, and wintertime comfort issues near the exterior walls. The foam can be protected from sun & critter damage by finishing it with purpose-made cementicious EIFS coatings, a half inch of hard-stucco scratch coat, or an appropriate panelized material solution.
https://www.greenbuildingadvisor.com/article/how-to-finish-exterior-foundation-insulation