Flatish roof and insulation options on the zone 7a/6a boarder Michigan’s UP

Compromise seems to be where I am at on this, I hope I picked the right category: I hope to have my thinking checked, and corrected and to hear if the builder science gurus here have some ideas that could help me leave this place better than I found it.
I have the options to 1) do nothing just re-roof it as is, or 2) try to insulate and struggle with the air gap, and air movement. (see proposed details below)
Spray foaming so far specs out as cost prohibitive a complete cabinet fill would be over 10,000 cubic inches of material,
Under Surface deck closed foam would require ripping out the entire ceiling in the home,
my third option is to provide the new roof deck an underventing, above the old deck, and to fill the 10 inch “vaulted ceiling” with dense pack cellulose.
A big of background: a 1954 flat Ranch (with just under .75/12 pitch) I am unsure of the current insulation, I belive there is no insulation currently.
There have been occasional issues with ice damming (depending on weather and how hot the house has been kept) but largely its been effective.
The roof is about to be replaced. Spray foam would drive cost nearly 2x as other options (either because I have to do a full cavity fill (10k cubic inches or rip the finished interior out to spray foam the underside
The thought for a replacement layer would be from the inside out and adding an air gap for the new roof decking over the top of the existing roof deck.
1) To keep inside moisture out of the system revisit the current Re-vapor seal(drywall and latex paints)
2) Filling the 10 inch current space between roof deck and ceiling with 10 inches dense pack and sealing the current vents
3) Plank roof deck stripped to planks and covered with air perm house wrap,
4) Layer of purlins to provide a new air gap over the top surface of planks and house wrap which should breath
5) 1.5” air gap to bottom of new roof decking
6) Create air gap: Add New roof decking on purlins to deck over with 1.5 inches air gap (with of a 2x purline) and full length venting low side larger than top side (direct east exposure) and venting the high side (28 feet of house width total deck with 35 feet east to west with west being the high side just under 2 foot higher and the prevailing wind side which may cause a vent issue I am unsure)
7) A layer of synthetic
8) a layer of poly iso ½” insulation (or other material as underlayment for the EPDM to help protect from impacts and to not soak up water should the epdm become compromised
9) 60mil EPDM black (black to generate solar heating to get snow removal as well as drying of the roof decking
Sorry about the original formatting issues, this should help clear it up a bit!
GBA Detail Library
A collection of one thousand construction details organized by climate and house part
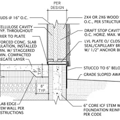
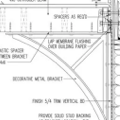
Replies
MichiganNick, a few comments:
Your wall-of-text is very hard to read. It would be much easier if you added more line breaks. I'm not being fussy, it's just difficult to follow what you are trying to relay.
Vapor barriers have nothing to do with ice dams. Air barriers do help but they are by far best used in conjunction with insulation, and ideally, roof venting.
It sounds like you’re proposing a vent space in between the existing roof sheathing and new polyiso insulation. If you do that, the polyiso won’t be doing any insulating, though it can still be an underlayment for EPDM. (Wood fiberboard also works and has less environmental impact.)
Martin’s article here covers the important aspects: https://www.greenbuildingadvisor.com/article/insulating-low-slope-residential-roofs
I will try and clear it up, the thing is, it had line breaks and bullet points all formatted prior to hitting submit.
In spite of the formatting, you seem to have nailed it. My goal is to avoid saturated roof decking to allow the roof to last its full-service length while adding insulation affordably without ripping the entire finished ceiling out to spray under the deck or having to resort to 10k in foam to cavity fill. As much as I'd like to encourage them to do so, it's simply not affordable for them, and they would not live long enough to recover their investment.
What I am mostly trying to figure out is
the Proper gap size to vent the underside of the epdm roof deck,
What issues with moisture I may create if I dense pack R30-R40 dense pack cellulose in the old 10 inch vented gap sealing it.
Will the 1.5 inch gap over old decking be large enough to properly wash the underdeck and draw moisture out of the system below?
I suppose is no different than a normal attic .
My worry is that i could suck conditioned air from the living space if the moisture is not controlled and that the house wrap may both control moisture venting out as well as resist any condensation or moisture in the air gap from easy entry.
Nick, I recommend reading Martin's article, which covers most or all of your questions in detail. If you don't have a subscription, it's worth the cost, or I believe you can sign up for a trial.
The short version is that to effectively vent such a low-slope roof you need a very large vent space, because the stack effect does not create as much draft as it does on a steeper roof. I avoid foam whenever possible but this is a case where either spray foam or rigid foam probably make sense. I know they are expensive but so is mold remediation, or paying to heat an uninsulated house.
I was just reading that article. I had read it some time ago and that's where some of the ideas came from but it was some time ago and I could not remember the specifics. It would seem I would need a minimum of 6 inches over the top to get enough air movement and given the width some dog houses built on top which given the snow depths would need to be fairly tall.. That was the residual memory in my head but I could not find that article when I looked. The memory being that my 1.5 inch would be maybe to small a gap to allow enough air to wash the deck, then I was thinking of the small gaps on normal slopes, but here gravity is not my friend. I had signed up prior to posting specifically to ask for more details. Thank you for the offer, I will dig in a bit more.
Thanks all, so the end decision was to go with closing that structure and doing a full cavity fill with closed cell foam. expensive but to keep the architectural look of the slant ranch without adding an additional 10-inch "Hat" to vent over whatever we put in the options were all expensive,