Flat roof, no insulation and needs replacing

Just purchased a home, the living room addition in the 1980’s added a 20×30 flat roof that has ZERO insulation. The construction is large LVL type beams with 2.5″ tongue and groove decking spanning the beams. The roof is a old build up with tar and rock ,and it is in bad need of replacing. My father in law is a commercial roofing consulting and is offering to coat the roof with a commercial emulsion/silcone top coat. This is the option I am going to go for in making the repair on the roof (it will be free and we both want to explore with using this product in the residential market).
The plan for adding insulation is then to build down the roof from the interior 3.5-5.5″ with dimensional lumber and fill the cavity with spray foam. I am concerned since the new silicone coating will be vapor impermeable making sure I do not trap moist air on the 2.5″ decking causing rot.
If I use open cell spray foam, and tongue and groove wood on the interior, will this provide breathing into the house for any moisture that comes form the outside?
I am located in South Carolina, climate zone 3, so my understanding is I should design for air breathing to the inside of the home.
Should I use open cell spray foam in this case?
GBA Detail Library
A collection of one thousand construction details organized by climate and house part
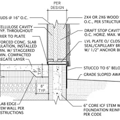
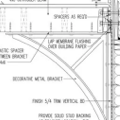
Replies
Hi Dilly.
There are some risks to using both open-cell and closed cell foam in your situation.
As you noted, the risk with closed cell foam is that you will create a double vapor barrier. Most builders shy away from an assembly that can't dry in at least one direction. But some builders feel that as long as the roof sheathing is dry when the work is done and the water management and air sealing details are impeccable, it is not a problem--if the sheathing can't get wet, then it doesn't need to dry.
There is also a well-documented damp sheathing risk with open-cell spray foam, common with unvented roof assemblies. Keep in mind that how you condition the space is also part of the equation. If you can keep indoor relative humidity down, you lessen the risks of using open-cell foam.
Before you make any decisions, I recomend you read these two articles: Insulating Low-Slope Residential Roofs, Open Cell Spray Foam and Damp Roof Sheathing.
Filling the cavities with closed cell foam would be a crime against the planet, and would underperform an open cell solution at any given R. See:
https://www.finehomebuilding.com/membership/pdf/184243/021269086NRGnerd.pdf
https://materialspalette.org/wp-content/uploads/2018/08/CSMP-Insulation_090919-01.png
In climate zone 3 as little as R5 continuous insulation above the roof deck would be sufficient dew point control for at least R33 of fluff or open cell foam under the roof deck, substantially mitigating the damp sheathing risk. Anybody in the commercial roofing biz probably knows where to get the relevant insulation products and how to apply them. A couple inches of Type VIII EPS on a flat roof is cheaper per R than cksed cell spray polyurethane, and would be good for more than R8, which is a good start toward the IRC code minimum R38.
R30 of open cell foam takes about 8", R30 rock wool about 7". How deep are the LVLs?
Since you need a new roof, now is the time to insulate from the outside. Besides the better performance, you can leave the existing celing as is and you don't need to do any framing or install and finish a new ceiling. It is a waste to cover up nice T&G. Doing anything on the inside will cost you more money to get the same R value as bumping the exterior insulation up a couple of inches.
Just make sure the roofers use the right size screws so it doesn't come through the T&G. If the decking is extended into the soffit area, it would also be good to seal the groove between boards over the top plates. Even a small gap between boards adds up to a big surface area on a whole roof and can leak a lot of air. You can drill through the grooves above the top plates and seal it with same canned foam.
The roof also need a decent warm side air barrier, with T&G go with either a peel and stick membrane over the whole thing on the outside or by sheathing with plywood and taping the seams.