flat roof: moisture concerns with polyiso above fiberglass batts

hi,
any help would be greatly appreciated.
the situation: i am remodeling the interior of a low-slope-roofed addition (15′ x 16′). the studs and rafters are exposed. i installed 2×6 ceiling joists (level) below the existing rafters (which are sloped), allowing room for ventilation. i installed a soffit vent on the low side and plan on installing a pop-up roof vent at the high side. this is my home. i am in climate zone 5.
the plan: with ventilation of the rafters and sheathing in mind, i was thinking of the following for the ceiling (bottom-to-top): drywall, fiberglass batts, and 1-inch polyisocyanurate boards (with the impermeable foil) laid across the top of the ceiling joists (keeping the fiberglass from interfering with the venting and stopping some of the thermal bridging through the ceiling joists). the foam board would be foil-taped and secured to the joists, and the perimeter would be caulked / foamed.
the question: concerning moisture, am i correct in thinking that warm air (with moisture) from the interior will be trapped in each of the bays because of the polyiso? will this warm air contact the cold foil on the polyoso and turn the bays into swamps? or… does the fiberglass insulation sitting between the warm interior and the cold exterior mitigate the contact between the warm and cold air, thus reducing sorption / condensation? additionally, would drying in the direction of the interior be enough to be prevent rot?
i have read many different articles and have only been left confused. clarification on this specific question would be awesome. i realize there are better ways to go – unvented, spray foam, etc. – but those bridges have been crossed and would require a lot of alteration.
thank you.
GBA Detail Library
A collection of one thousand construction details organized by climate and house part
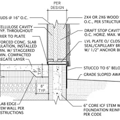
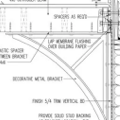
Replies
Allan, find a good builder or insulation company to advise you at your site and check your plans and workmanship.
To me it sounds like you should have some local assistance.
aj
Reshuffle the stack: Putting the 1" iso between the gypsum and the joist/fiberglass plane, and it works just fine in a zone 5 climate. The layer cake looks like this:
Roofing shingles & felt whatever
-----
rafters
----
ventilation space
-----
fiberglass & joists
------
foil faced polyiso, seams taped
-----
gypsum
-----
latex ceiling paint
For the fiberglass, use only "cathedral ceiling" high density batts (better yet, use rock wool)- the low-density goods will lose thermal performance to convection with the ventilation gap air at the cold temperature extremes.
If you feel you MUST put the foam above the 2x6 joists for any reason, use unfaced EPS, not polyiso, and put 2" if you can. At 2" of Type II EPS is sufficient R in your climate for tolerating R21 in the 2x6 joist bays without condensation issues without interior side vapor retarders, and the assembly can dry into the ventilation cavity through the ~1.5 perm foam at acceptable rates, with 3-5 perm latex paint on the ceiling (standard latex.)
With 1"/ R6 iso and a foil facer above R21 cavity fill you WILL get significant condensation at the foil facer, enough to create localize drippage issues during (or shortly after) cold snaps. The thermal performance of 1" polyiso will be a shade less than R5 when it's 10F outside (2" of EPS will be nearly R10 @+10F outside temps). Assuming a 70F ceiling and R21 batts, frost would form on the interior facer in the 1" polyiso case whenever the roof temp drops below +22F (which is about the January mean temperature in many zone 5 locations). With 2" EPS that only happens when the roof deck hits +14F. Assuming an interior air dew point of 40F, the interior facer of the 1" polyiso would hit that temp at a mere 31F roof deck temp, which means MOST of the winter you'd be collecting liquid water in there, with nowhere to dry but downward toward the ceiling even when it warms up. But with 2" of EPS the dew point is only reached at roof deck temps of +27F, which means there are still substantial drying hours even in January, with the preponderance of the winter hours being amenable to some amount drying through the semi-permeable foam into the vent cavity.
Thank you so much for your thoughtful response, Dana. Your information is extremely helpful. The EPS sounds like a good option. As for shuffling the stack with the iso on the bottom... I had been thinking about it, but I worry about lowering my finished ceiling height by another inch, aesthetically speaking; the joists are already fairly low.
Thanks for the advice, AJ. I figured I would ask here first.
BTW: Your total R-value is below current code-min for zone 5 locations in either stack-up (but you probably knew that, eh?) If you have room for more rigid foam than 2" above the 2x6 joists, it may be "worth it" in a long term financial analysis.
In my area (central Massachusetts) it's possible to buy reclaimed roofing foam insulation for 25-35% the cost of virgin stock foam from a number of vendors (making it cheaper R than batts), which can take the sting out of it.
One inch is not worth saving. The simple and safe build is Dana's reverse all build IMO. We have done a similar build here often.
Stop the air moving into the assembly and vent out any moist air that does enter.
Dana, I am in Connecticut. Do you know of any specific vendors for reclaimed board, or would a google search suffice? Yes, increasing the r-value would be great if I could afford to do so. I know it is worth it longterm. The room / addition was in such a terrible state that anything I do will be an improvement, but getting everything as close to ideal as finances (and space) will allow is my goal. So yeah, some reduced price foam would be great, particularly if it allows me to add more.