Flat roof insulation

I have built an extension to my house with flat roof, continuation of the existing house. The rafters are 16 in apart and there is 6 in left for the insulation under the sheeting. The plans are requiring R30 insulation and the building inspector requested hard foam Thermasheath- 3, 5 in thick, leaving 1 in for breathing. The drywall was not installed yet, when water from condensation came down all over the place. There are vents on both sides of the roof, in each bay under the insulation level, not allowing the hot air to escape.
What is the fix for this, please? This brain new addition is in Seattle, WA. I am so worried for all the money spent.
Thank you,
Angela
GBA Detail Library
A collection of one thousand construction details organized by climate and house part
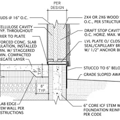
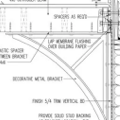
Replies
Angela,
The rigid foam insulation is supposed to go on top of the roof sheathing. You're not supposed to cut the insulation into strips and insert it between the rafters. I'm including an illustration from the Thermosheath web site (see below).
I'm also including a link to a useful article: Insulating Low-Slope Residential Roofs.
.
Angela,
The cause of your problem is air leakage. Air is leaking through cracks between the cut-and-cobble insulation you installed and the rafters. (For more information on the cut-and-cobble method, see Cut-and-Cobble Insulation.)
The best solution to your problem won't be cheap. You should remove all of the existing insulation and install closed-cell spray polyurethane foam against the underside of the roof sheathing.
Another possible solution is to install new rigid foam insulation on top of the roof deck, followed by new roofing. Needless to say, that solution is expensive too.
WOW, Thank you for the fast replies! Is what I feared the most: rework and additional payment. I just wish I had a better team in place. They just finished insulating and all is brain new material.
Some damage control:
1. Do I have to seal the vents on the sides of the roof?...or it does not matter too much.
2. Can I reuse the sheets of Thermasheats-3 and seal all around? With what?
3.What is better: to push them all the way to the roof-sheathing or to fill up that cavity with some other material and drop the hard foam? What would be the best/cheaper filler? In other words, can I use the cut-and-cobble method and with what filler? The method seems to be cheaper at this point in time.
Angela,
According to building scientist Joe Lstiburek, you shouldn't try to vent a low-slope roof like this unless you have room for at least 6 inches of ventilation space between the top of your insulation and the underside of your roof sheathing. So your type of roof is not a good candidate for a vented solution. You need to build a unvented roof assembly, and you need to make your ceiling airtight.
I don't really recommend the cut-and-cobble approach, especially since you have already tried it, and your ceiling is raining condensation. But if you want to give it a try, the only way it will work is if (a) you push the rigid insulation tight to the underside of the roof sheathing, and (b) the perimeter of every individual rectangle of rigid foam is meticulously air sealed as it is installed.
None of this should be attempted, of course, unless your building inspector agrees with your plan.
And if your contractor is responsible for your raining ceiling, then any changes should be performed at the contractor's expense, not yours.
In the case of using air sealing, which one do you recommend for best price in this application?
Thank you
Angela,
For the best air seal, you should probably remove all of the existing insulation and install closed-cell spray polyurethane foam.
In case of the cu-and-cobble, what sealing should I use?
Thank you
Angela,
The most important factor to get a good air seal with cut-and-cobble is paying close attention when performing the work.
Careful installation of silicone caulk or the use of one of the European air-sealing tapes will probably result in better air sealing job than canned spray foam.
If you insist on using the cut-and-cobble approach, you should finish the job off with a skim coat of two-component spray foam, following the "peanut brittle" method described in my recent article.
Peanut brittle...hope is the sweetest deal! Thanks a lot, I learned a lot too.
Martin,
As another Seatte-area resident, I have great interest in Angela's situation. But, I don't want to use spray foam because of the reported health risks from toxic offgassing, so "cut-and-cobble" still seems worth exploring. Thermasheath-3 has foil facing on both sides, which it seems would provide an impermeable condensation plane. Would Angela have been better off using unfaced polyiso, so the foam insulation board would have no surface on which condensation could form? Or, would she have been better advised to use unfaced polyiso for all layers of foam board inserted between the rafters, but with an additional full, carefully-taped layer of foil-faced polyiso attached to the underside of the rafters, intended to create an effective air barrier on the "warm" side of the installation?
Ralph,
First of all, I don't recommend that cut-and-cobble method for unvented roof assemblies. Even if you have a vented roof assembly (as in Angela's case on this page), disasters are possible.
For reports of cut-and-cobble problems in unvented roof assemblies, see Cut-and-Cobble Insulation.
The problems encountered by Angela have nothing to do with the type of facing on the rigid foam insulation. The cold surface on which the condensation occurred was the roof sheathing, not the rigid foam. The solution to this problem is clear: the rigid foam belongs on top of the roof sheathing, where it can keep the sheathing warm and dry, not underneath the roof sheathing.
Ralph, Martin is right that the foil didn't cause the problem. But I like your idea of foil faced insulation under the rafters, carefully taped. Another, similar approach to air sealing would be to put a membrane of some kind between the foam/rafters and the not-yet-installed drywall. Perhaps in addition to careful caulking around the cut insulation.
But even with good air sealing, the horizontal venting channel is unlikely to work, unless you are in a very windy spot. To provide some elevation difference to drive the stack effect, I suggest Angela could connect all the vents on one side to a drainage space behind the siding (if one exists, or if the siding isn't up yet). Then the elevation from the bottom of the wall to the vents on the other side of the roof drives the stack effect.
In principle, the vents could also work with forced ventilation. Installing a fan in each channel would be unreasonably complicated, but could you connect all the vents on one side to a duct, and run a single fan on the end of that duct? Maybe control the fan based on a humidity senor in the vented space. Probably not practical but I'm throwing out the idea just in case it is useful.
Holding the contractor responsible for fixing the problem sounds like a good thing to do. Let us know if you'd like us to review his proposed solution.
After reading through the numerous articles relating to this topic, I wanted to chime in and clarify my thoughts. I hope that others will be able to further help. I have read many of the Building Sciences' articles, as well as the IRC & DOE information. My home is a mass masonry structure (Row Home) built in 1890 (PA), which currently has a finished 3rd story loft. I recently purchased the home and am still in the process of uncovering the decades of improper finishes installed in the home. In the loft currently are rough cut timber joists, and drywall with JM batt insulation. Underneath the insulation there are Styrofoam baffles that connect and vent to absolutely nothing; my home has no soffits. In the near future I will unfortunately need to remove all of the finishes to avoid the condensation issues that are sure to follow, if not already present. With my house or similar, it is highly unlikely that anyone is going to install exterior roofing insulation. Unless your roof is already rotten, this is not a procedure that makes any sense. Checking exterior insulation off the list, it is clear that spray foam or "cut and cobble" are the only approach. If you set aside all the concerns surrounding spray foam, permanently adhering anything to original wood members in a house such as mine is something I would never do. In addition what happens if sometime in the near future the roof decking turns out to require work? Not only would the labor costs for a professional installation be lost, but the material costs as well. Rigid insulation in my mind could help avoid this permanence concern. My questions to others are as follows. Wouldn't installing the rigid with a high quality Silicone such as DOW 790 makeup for expansion and contraction, as well as provide an airtight seal around the perimeter of our "cut & cobble"? From there it seems like taping all butt joints would be the next pair of belts and suspenders. If this was all done with care, is there still really a concern? If installed adequately it seems the installation becomes more about vapor permeability & drying potential than anything. What kind of permeability are we looking for in this situation? What about terminations at the eaves where the joists meet the wooden sill plate/top of masonry? What about connected neighbors in a row home situation, is it worth doing if we cannot tie the roofing insulation to the walls? I would love some opinions for older masonry homes where conditions are not ideal. Thanks!
David,
My advice is unchanged. If you want to insulate a low-slope roof, and you plan an unvented roof assembly, you should either install rigid foam insulation above the roof sheathing or closed-cell spray foam insulation underneath the roof sheathing.
Cut-and-cobble installations have been associated with failures. Of course, good workmanship reduces the risk compared to a sloppy job. Only you (the homeowner) can decide whether the cost savings of the cut-and-cobble approach are important enough to outweigh the risks.