Flash and batt thickness

I have an old 2-story home that’s been rebuilt on the second story with 2×6 construction. The first floor is still existing 2×4 but it has been re-sheathed with 1/2 OSB (which is on the whole house). I’ve settled on flash and batt (for various reasons including costs, and I’ve read many posts/articles on this forum). I’m located in central Iowa in Zone 5 (right on the border of Zone 6). My question is, I’m debating on whether I should go with 1″ or 2″ of closed cell. It’s about 1690 sq ft. of wall area and there’s about an $1100 up-charge for the 2″. I understand the risk of going much under 1″ for condensation, but is the 2″ worth the money and alleviating that risk?
Cost is one aspect, but the other is the batts which I’ll have to install. Since R-11 is about the thinnest I can get, I’ll be compressing the batts down to 1.5″ in the 2×4 cavities, which will really be difficult (I think it’s going to bulge pretty substantially). My other concern is sound, I want the benefits of the fiberglass for sound isolation, which obviously reduces with less space.
One additional question. It’s my understanding that either with 1″ or 2″, I’ll still need an internal permeable vapor barrier such as kraft-faced rolls, is that correct? Thanks for the help anyone can provide!
GBA Detail Library
A collection of one thousand construction details organized by climate and house part
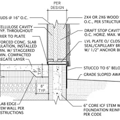
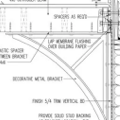
Replies
I wouldn't design to near code minimums. So consider 1.5" of 2lb closed cell spray foam.
> I’ll still need an internal permeable vapor barrier such as kraft-faced rolls
Meet certain specs and code doesn't require that. If it's a good idea anyway is widely debated.
Thanks! The 1.5" would be a perfect compromise (literally). When you say meet the specs and the code doesn't require it, do you mean for the closed cell? From what I've read (on this site) it says the R5 in Zone 5, R7.5 in Zone 6. The foam they would be spraying would be R7.2. I suppose 1.5" with unfaced batts would be a good way to go?
Also note the code's (IRC) 1.5 max permeance foam language. My opinion is that you are slightly better off with the kraft facing (or even better, a smart nylon membrane). Or the low side of Class III dry perms - say 1-3, not near 10.
Code for Zone 6 to enable Class III with foam is R7.5 for 2x4 and R11.25 for 2x6.
See R702.7.1 footnote a here:
https://codes.iccsafe.org/content/IRC2015/chapter-7-wall-covering
1" of closed cell spray foam should be safe for the 2x4 walls in climate zone 5. You only need about ~25% of your wall's R value to be in foam to stave off condensation, whereas 1" will give you ~40% (The R5 exterior foam minimum is because you would have ~R13 of fluffy behind it, with flash and batt you only have ~R8). Just be sure to specify in the foam contract that the foam be sprayed to a minimum depth of 1", not an average depth. It makes a big difference in performance, and is the only way to make sure there are no major condensation points.
There is not much reason to go up to 2", since the foam isn't really adding much whole assembly R value either way (1" of spray foam adds R1.5 to the assembly, 2" ups that to R3). The only real value of the foam is that it acts as an air barrier.
I don't think a vapor barrier is necessary, since there is no condensation risk.
I strongly encourage you to look into ways to get more insulation into the walls though. Have you considered extending the stud bays by using horizontal strapping? It is a fairly inexpensive way to add R4 or so to the assembly, and would not have to increase the foam thickness or compress the batts. Alternately, you can use Bonfiglioli straps and add about R9, but then you'd need to go with 1.5" or 2" of spray foam.
https://www.finehomebuilding.com/2014/11/26/breaking-the-thermal-bridge
I am not an acoustics expert, but I believe that the spray foam will have a much bigger effect in soundproofing of the assembly than the fiberglass batts would, so I wouldn't worry about compression. Hopefully someone more knowledgeable can verify this.
Edit: Kevin has pointed out that closed cell spray foam is not good for soundproofing. Only open-cell is good in this application.
I really appreciate the input. Couple of questions. They claim the closed cell they're using is R7.2, so by my calculations in the 2x4 assembly 1" would increase the the R-value by 3.5 and 2" by 7, am I wrong on that? As far as soundproofing, that's one area I'm very well informed as I work with that in a professional capacity, and that's one of the definite downsides to closed cell (and even open cell).
With respect to your 25% to prevent condensation, how would that come in to play on my 2x6 assemblies (which is about 65% of the walls). Would that be okay at 1" or would it need to exceed that threshold? In other words, 1" of closed cell and 4.5" of fiberglass would obviously not meet that 25% minimum. Thanks for the help!
>They claim the closed cell they're using is R7.2, so by my calculations in the 2x4 assembly 1" would increase the the R-value by 3.5 and 2" by 7, am I wrong on that?
As Akos noted, my lower assembly R values are a result of accounting for thermal bridging through the studs. This is a simple tool that will allow you to see how difference assemblies perform: https://ekotrope.com/r-value-calculator/
>As far as soundproofing, that's one area I'm very well informed as I work with that in a professional capacity, and that's one of the definite downsides to closed cell (and even open cell).
You are right in that regard. I was able to find one article that seems to have performed a few measurements for different foam/fiberglass assemblies, but I'm not sure how reliable the figures are (Johns Manville makes both sprayfoam and fiberglass insulation): https://www.buildingenclosureonline.com/articles/86914-fibers-vs-foams
If the figures are reliable, some takeaways from the article:
-For a 2x4 wall, fiberglass and open cell spray foam have equivalent STC ratings.
-In a 2x6 wall, flash and batt performs ever-so-slightly worse than straight fiberglass.
-Closed cell sucks at soundproofing
I do not know if the degree of compression you would get in a 2x4 flash and batt assembly would change its acoustic properties, but I bet there is research on how well different densities of fiber insulation absorb sound, which could be helpful.
>With respect to your 25% to prevent condensation, how would that come in to play on my 2x6 assemblies (which is about 65% of the walls). Would that be okay at 1" or would it need to exceed that threshold? In other words, 1" of closed cell and 4.5" of fiberglass would obviously not meet that 25% minimum. Thanks for the help!
Michael Maines in comment #16 does a great job explaining the math and reasoning. 1" of closed cell in the 2x6 walls would just barely be sufficient for a 2x6 wall.
Closed cell spray foam does nothing for soundproofing. It can actually reduce the STC rating of an empty 2x4 wall. Open cell is effective. Any foam does help in that it seals areas that sound can get through, but the foam is not an effective dampener of sound.
It appears you are correct! I would not have expected that. Updating my response accordingly
> there is no condensation risk
Some sorption/condensation will occur unless you use much more foam. Less s/c will occur with a Class II interior side vapor retarder. With a variable Class II, drying of this moisture will be more or less as fast as Class III.
That is of course true. My use of "condensation risk" in this situation is a little sloppy, as I am referring more to "the risk from condensation occurring", not "the risk of condensation occurring". As you note, the code does not require vapor barriers at that thickness, so any condensation that occurs should be easily handled by the assembly and does not pose much of a risk. Of course, as you also note, whether a vapor barrier is a good idea anyway is widely debated :)
I should also point out that a little extra research/care in air sealing (eg, plate to floor or OSB taping), blower door testing and pressure balance is more important to moisture risk than everything above.
What is the point of using any closed cell foam at all?
In a zone 5 location with any type of back vented siding (vinyl siding, or anything with a rainscreen gap) filling the cavity with open cell foam would do a better job of air sealing than 2" of closed cell, and uses less polymer than 1" of closed cell, without using expensive HFO or climate damaging HFC blowing agents.
Even 3.25" of closed cell (a nearly full-fill that doesn't need much trimming) buys you at-best R1 of whole-wall R performance over a full 3.5" of open cell foam. Do the math:
https://s3.amazonaws.com/finehomebuilding.s3.tauntoncloud.com/app/uploads/2017/07/05111418/cell-foam-chart.jpg
https://www.finehomebuilding.com/2017/07/10/closed-cell-foam-studs-waste
Even without back-ventilated siding the open cell full-fill assembly can be made relatively moisture safe with half-perm "vapor barrier latex" on the interior side wallboard, or a smart vapor retarder such as 2-mil nylon (Certainteed MemBrain) behind the wallboard. With the air-tightness of the open cell foam neither the wallboard or vapor retarder need to be detailed as an air barrier- there won't be any moisture moving via convection.
So, the main point of closed cell for me is air sealing. The first floor is an older home and I'd really like to take care of any air gaps through the closed cell, which I think is going to be my best option there. I had a bid on filling the 2x6 with open cell, but I really want the soundproofing characteristics of fiberglass. Also, it might seem stupid, but I don't love the idea of filling the wall cavity so to prevent ever fishing anything through the walls again in the future. I do a lot of smart home and tech projects, and I like the ability to make future modifications.
As far as the calculations on the R-value increase, as I mentioned above, I wonder if those values are accurate for my product. Both contractors I've spoken to claim their close cell has a R7.2 value, which is higher than that calculation indicates.
The foam is R7 or so, the problem is the wood beside it is R1. No matter what R value the foam is, the thermal short circuiting of the wood limits the overall wall R value you can achieve.
Cavity fill insulation does very little for sound, it helps but not that much. The only cavity fill that really helps is dense pack cellulose because it seals up the wall.
If you want quiet go with RC + layer or two of 5/8" drywall. If you want super quiet I find a 1 5/8" metal stud wall with 5/8 drywall built 1/2" away from an existing wood stud wall works much better than RC.
Cutmoney, when closed cell foam is freshly installed it is usually R-7/in or higher. If your contractors are proposing HFO-blown, low global warming potential foam, it stays relatively high. But if they are using conventionally-blown foam, which they probably are, it degrades to around R-6/in or lower as air dilutes the blowing agents in the cells. The spray foam industry puts out more false and misleading information than most industries.
Totally understand. I feel like as with everything on the internet regarding construction opinions—especially in the insulation, HVAC, ventilation world—I'm almost more unsure than before I started. I was really set on the closed cell to seal up the old structure, but now I'm not sure. That's why I was really considering the 1", get some of the advantages of the sealing properties of the closed cell without the high cost. I'm just still not 100% clear on whether that's going to be a safe option (condensation, etc.) in either the 2x4 or 2x6 cavities.
For condensation resistance, most designers, including me, think it's reasonably safe to follow the guidelines in the IRC. The problem is that the guidelines are not clear. If you haven't already, read this: https://www.greenbuildingadvisor.com/article/flash-and-batt-insulation. Another article that explains the basics (using an image that I first drew, and FHB's art department dressed up): https://www.greenbuildingadvisor.com/article/flash-and-batt-insulation.
Table N1102.1.2 tells us minimum insulation requirements for energy efficiency: https://codes.iccsafe.org/content/IRC2015/chapter-11-re-energy-efficiency. In your case, R-13 cavity and R-5 exterior, or R-10 exterior if you want the higher efficiency required in zone 6. The problem is that those numbers have no relationship to condensation resistance.
For condensation resistance (there are more accurate terms, but that one's generally understood) look at table 702.7.1: https://codes.iccsafe.org/content/IRC2015/chapter-7-wall-covering. That table shows what you would need to reduce your interior vapor retarder from class 1 or 2 to class 3 (aka latex paint). Notice it does not say you can skip the vapor retarder altogether; they still expect some slowing of vapor diffusion. It's not clear but it's generally understood that the table assumes code-minimum insulation levels.
If you do some math, you'll find that in zone 5 you need about 27-28% of the total R-value in the impermeable layer to keep the interior surface above 45°F most of the time, which with normal levels of interior relative humidity means you should have very little moisture accumulation, if any. If you want to be more conservative, you could follow zone 6 requirements of 35-36% of the total R-value in the impermeable layer.
In your case, 1" of R-6 foam and 4.5" of R-3.5 fluffy insulation would provide a total of about R-22, with 27% in the foam layer, meeting the IRC prescriptive ratios. 1.5" of R-6 foam and 4" of R-3.5 would provide a total of R-23, with about 39% in the impermeable layer, meeting zone 6 ratios.
There are some fine points: R-3.5 is an estimate for fluffy insulation, foam can be higher or lower than R-6, it's impossible to get a perfect 1" everywhere, and closed cell foam is not completely impermeable; it allows a small amount of outward drying, especially in a layer that thin. In any case, if you decide to use spray foam, I would go with Dana's recommendation (usually a safe bet) and install 1.5" of foam.
The IRC ratios are generalizations. If you want more precision or assurance for your situation, you could find someone to do an accurate hygrothermal analysis. Many people think the IRC ratios are not safe. Others think they are too strict. I use them as a guideline.
Another fine (or not so fine) point is the environmental damage of conventional foam. It is extremely selfish to use a product with very high carbon emissions when there are low-GWP options available. The energy you save using conventional foam will most likely not be recovered before the climate starts to spin out of control. The foam does not add significant R-value to your assembly; it's just for air-sealing, and it's not even great at that, just ok. If you have any plans to replace your siding, I would strongly recommend air-sealing your sheathing from the exterior. Or if you don't plan to do that, good installers of dense-packed cellulose, with some additional air-sealing, should be able to get you below 3.0 ACH50 without using flash and batt foam.
Thanks for that clarification, that's very helpful. With all that information, maybe closed cell isn't the best option. I'm mostly concerned with the air sealing more than anything, honestly. I just felt like in my last older home, the actual R-value of the insulation was such a small part, it was the air leakage that was way more of an issue. I mean, feeling a draft of -5 degree air leak under the baseboard seemed like it had a MUCH larger impact than a slightly cool wall. Any opinions on a product like EcoSeal? After everyone's responses, I feel like the one thing that foam really misses is sealing between the plates, studs, etc. I've got a LOT of windows, so I have quite a few kings, trimmers, and headers to seal.
>" I'm mostly concerned with the air sealing more than anything, honestly."
At 3.5" open cell foam is a BETTER air seal than a 1" flash of closed cell, and it's about the same cost as just the 1" closed cell (cheaper if it's HFO blown closed cell.) And it uses less polymer than 1" of close cell.
You're instincts on the framing seams are dead-on. Before closing up the wall install a bead of polyurethane caulk or purpose made sealants between any doubled-up framing seams (window headers, wall top plates, jack studs etc) and between the bottom plate and subfloor. Foam cavity fill only seals the framing to the sheathing, and misses all of those other leaks. It adds up.
Purpose made sealants like EcoSeal work fine for sealing the cavities if the sheathing is 4x8' sheet goods, but doesn't cut it for plank or ship-lap sheathing, and you'd still need to tape any exposed seams between OSB/CDX sheathing. If the surface isn't clean enough for tape to stick really well, trowel on 1/8" or so of fiber reinforced duct mastic to help keep the edges from peeling up.
Be sure to install backer rod and perhaps a shot of low-expansion can foam to seal up around the windows (latex can foam preferred- you don't necessarily want it firmly glued in place), and pack the remainder of those micro-cavities with fiber insulation. Don't be afraid of packing it too tight- as long as it still has some spring to it the fiber insulation isn't too tight, and is both more air retardent and higher R/inch at higher density.
> you could follow zone 6 requirements of 35-36% of the total R-value in the impermeable layer.
Read R702.7.1 footnote a) and you will find that those percentages are incorrect in the case of flash-n-batt. More like 45-46%.
> the IRC prescriptive ratios
The IRC has no prescriptive ratios relating to wall vapor retarders.
https://codes.iccsafe.org/content/IRC2015/chapter-7-wall-covering
>Read R702.7.1 footnote a) and you will find that those percentages are incorrect in the case of flash-n-batt. More like 45-46%.
That footnote applies to foam "with a maximum permeance of 1.5 perms at the installed thickness", and so does not apply to any closed cell spray foam, so long as it is applied thicker than ~2/3".
>The IRC has no prescriptive ratios relating to vapor retarders.
Again, it is implicit. The IRC doesn't use ratios for anything, they just throw in a "Linear interpolation shall be permitted" footnote on every table. That they left it off R702.7.1 is based on expediency, not building science.
> That footnote applies to foam "with a maximum permeance of 1.5 perms at the installed thickness", and so does not apply to any closed cell spray foam, so long as it is applied thicker than ~2/3".
You are misreading it. Less permeance means the low perms of CCSF are fine.
Flash-n-batt isn't continuous and isn't "over". Applying anything in (or derived from) the body of Table R702.7.1 to FnB that isn't covered by footnote a) is invalid. Based on what's written and building science. FnB results in cold sheathing and limited inward drying - the physics and risks are different than exterior foam. That's why code compliant R values result in a higher foam/other R ratio for FnB.
The exact phrase "linear interpolation" doesn't appear *anywhere* in the IRC.
Rereading the footnote, I think you are right in that I misinterpreted it -- so revising the interior closed cell spray foam to 1.5 inches in the 2x6 assembly would be wise, if using unfaced batts.
It's "invalid" in that it has nothing to do with code, but it is perfectly valid for designing assemblies. The IRC table is meant for condensation control, and what determines the temperature of a condensing surface in an insulated assembly is insulation ratios, not foam thicknesses. Continuity or which side of the sheathing it is on has little to do with it. So long as the assembly meets code, using a foam thickness extrapolated from Table R702.7.1 is a perfectly valid way to minimize the risks resulting from condensation in an assembly.
I could cite some complicated study measuring dewpoints and moisture levels in various assemblies in various conditions, and pick my own arbitrary cutoff for what is acceptable, but the ICC already did that for me, and citing that table is a simple way to say "the amount of condensation at the surface of the foam in these conditions is unlikely to cause any harm".
I know for a fact that linear interpolation appears throughout the table footnotes in chapter 6, particularly for wall bracing requirements. It is one of my favorite chapters :p
Jon, I disagree with your interpretation of footnote a. As we all know, code language is not always clear. The insulation ratios I mentioned are not explicit in the code, as code cannot cover every situation, but the science is not that complicated. The intent is stated as keeping the condensing surface above 45° as a generic dewpoint temperature, and for that, ratios are what is important, as anyone who can plot a dewpoint curve in a wall can tell you.
On the other hand, as I wrote, some people choose to be more conservative, so more foam certainly won't hurt anything (aside from contributing to climate change). I don't think flash and batt is the most resilient approach to insulating, but in some situations it can be a good option.