Flash and Batt for an Unvented Flat Roof Ceiling

Greetings everyone. I am working on a modern house in Southern California near the ocean. It is a flat roof with an unvented rafter assembly and we cannot install rigid foam above the sheathing. We are hoping to use a ‘flash and batt’ approach with closed-cell spray foam directly in contact with the roof sheathing and Rockwool mineral wool Comfortbatt insulation below that and this would fill the bays between 11 7/8″ high LVL rafters.
Any thoughts on the proper thickness of each component? I am hearing one should have at least 2″ of closed-cell SPF but should I try to calibrate it so that the standard thickness mineral wool batts completely fill the rest of the rafter bays? (e.g. if we use 7.25″ thick batts I would need to use 4 3/4″ thick SPF? If there is no need to fill the rafter bays how can I hold the Comfortbatt in the proper vertical position, rather than having it drop to the GWB surface?
Thanks in advance!
GBA Detail Library
A collection of one thousand construction details organized by climate and house part
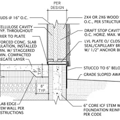
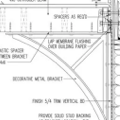
Replies
IMO, 8'' R28 Comfortbatt leaves a 2" cavity that could drop and create a void if not installed right. Can you use 9.5" LVL in your span? Is there an option to install 11 1/4 LVL or TJI and fill the cavity with 2" R14 ccSPF under the roof decking, and 9.5" R32 Comfortbatt? Or you could go 2.5" ccSPF if not. That would give you higher performance at a reasonable cost difference, less costs than 4" R28 ccSPF. It's a good option with NM's flat roofs.
Hi Armando-
Thank you for the feedback. We have a significant span so our structural engineer specified 11 7/8" LVLs and he is unlikely to let us reduce to shallower rafters. I do think the 2.5" CCSPF (+/-R-17) with the 9.5" R38 Comfortbatt could work. That would net an R-55, which is fantastic but I'm sure my client will want to know why we can't just meet the minimum R-30 requirement per the Title 24 report (performance-based). Is it safe to infer from your answer that in your opinion the joist bays must be completely filled as opposed to using some sort of netting product to hold the mineral wool higher in the joist bay with an air gap between the mineral wool and the GWB?
While I have you, two more questions if you're willing: (1) Almost all of the flash-and-batt articles I have read refer to fiberglass batt insulation. Are you aware of any reason flash-and-batt can't be done with mineral wool? Also (2) when people refer to Roxul are they referring to Rockwool Mineral Wool (like Comfortbatt) or some other product?
We did flash and batt with mineral wool, R-23 batts over 2 inches closed cell in 4a climate zone.
1) if I remember correctly this came up in another post (but I was unable to locate it) and while there isn’t a technical BS reason that you can’t use mineral wool, my understanding is that fiberglass is typically used because it’s easier to compress against the uneven surface of CCSF.
2) Roxul changed their name to Rockwool in North America, so my guess is that they’re referring to the product generically.
Exactly how much "air impermeable insulation" does applicable code require?
This may apply:
https://www.energycodes.gov/sites/default/files/documents/cn_unvented_attic_assemblies.pdf
If you were to use 2" R14 ccSPF and 10" R35 dense packed cellulose, you'll have an R49 assembly, and less expense. FWIW, the 2021 IECC is going to R49 in CZ3 and R60 for CZ4. I know you follow T24, but why not move up to a new code on a new build? I'm upgrading to that in my NoCal project.
1. The option of flash and batt is ccSPF and a permeable, less expensive insulation, usually batts and cellulose, but mineral wool and other BIBs can be used as well.
2. A couple of years back, Roxul rebranded as Rockwool.
I would like to add that R30 is the minimum LEGAL amount of insulation required by law... woohoo! What's the price of this project near the coast in SoCal?
Something else to think about, the thermal bridge of a TJI is much less than with LVLs. I would consider talking to the Engineer if he would be able to replace the rafter system. I'm sure if you do an energy analysis, it may support the change; maybe even less costs.
And with I-joists, you could insert 1/4" plywood strips above the lower flange to create a smaller space for insulation, while creating a handy service cavity above the GWB. Kind of the opposite of using the top flange to create air vent channels.
Thank you all. Very helpful! So does anyone know of a way of holding the Rockwool up higher than the bottom of the joists other than switching to TJIs and using 1/4" plywood strips? Maybe some sort of 'Insulweb' netting like one would use with blown-in cellulose or some sort of expandable brackets? Is there a problem with having an air gap between the bottom of the batts and the GWB?
Rockwool is pretty stiff and friction fits well. Add some spring insulation support wires and you'd probably be fine. Unfortunately, there's no way to really inspect this after the drywall goes on though.
An air gap below the insulation won't hurt anything with SPF flash on the sheathing. Especially with Rockwool - very little convection through the insulation.
Thank you all so much. So just to summarize:
I will push the client to go for the most roof insulation his budget can support (and remind him about life cycle cost) but if he only wants the minimum insulation required it sounds like it would not be too problematic to specify 2" of closed cell spray foam in direct contact with the underside of the plywood roof sheathing (R-14) plus Rockwool Comfort Batt 5.5" (R-23) held against the CCSPF with insulation support wires for a total of R-37, which exceeds the R-30 minimum per Title 24. Any one have any concerns about this approach?
Just to clarify - I have no doubt that we will ultimately be able to convince the client that the upgraded assembly is well worth the modest additional investment, we just need to first establish what the cost would be for the minimum assembly that code requires so he understands the ROI. Really appreciate everyone's insight here!
What is the ASTM C1289-20 rating for this supposedly R7 spray foam?
Oh I thought I'd heard CCSPF was R-7 per inch, but I just checked Holladay's Musings book and he says R-6.5/inch. so I guess the assembly above would be R-36. To be honest I'm not really sure where I can get technical data for CCSPF. I would love to learn more about the 'greener' alternates that are still air-impermeable if anyone knows of a resource?
Here is R5.6 and R5.2. And after only 5 years, the R value will be even lower.
Thanks, Jon. It looks like Johns Manville has some R-7 CCSPF options, unless I'm missing something? https://www.jm.com/en/building-insulation/residential/spray-foam/
Those numbers are bogus (because the wrong standard is used). Without the correct test it's marketing fluff - I'd use R5.5.
Thanks, Jon. I am still learning about all of this but when I search for ASTM C1289-20 it seems to deal with rigid insulation. Which testing standard should I be looking for on ccSPF?
The "lower" link in #14 is a good explanation of the standards (although most have newer "-" versions). Canadian spec sheets appear to be more honest - you can search for "CAN/ULC-S770" R values (preferably -15).
Unless there is a good reason for LVLs, I would switch to I-joists.
A 11 7/8 I-joist with 2.5" flange will be stiffer (less deflection), cost about 1/2 as much and would have significantly less thermal bridging.
An 11 7/8 LVL roof with R30 of insulation works out to and R28 assembly once you take into account the thermal bridging of the LVLs. The same roof with I-joists gets you an R30 assembly.
When it comes to building envelopes, not often you get a win/win on both cost and performance.