Flash and batt

Hi,
I have been reading on the site about flash and batt but don’t think I am “getting it”. I live in south central Kentucky ( zone 4A) and have a woodworking shop built in the rear of a 1970 built garage. I have insulated the walls with fiberglass and have put tongue and groove pine over that.
I have put in a ridge beam so I could create an open space in there to work by removing the ceiling joists. Because the rafters are 2×6 I have also had to put in a couple intermediate beams to minimize any deflection in the roof.
I have had closed cell foam sprayed on the ceiling. It probably averages about 1 1/2″ with some areas being more. I plan on putting the same pine tongue and groove on the ceiling but am wondering if the foam is adequate so have been considering putting in some faced R19 fiberglass. With the rafters being 2×6 and 1 1/2″ taken up by the foam I thought that the R19 would be a good tight fit with no voids. Can you give me your opinion on if this is a good idea and if condensation would occur, or what would happen if I just put the pine over the foam alone with no fiberglass?
Also, My roof decking is 95% those old pine boards (I think pine) with a piece here and there of OSB from old roof repairs and a single layer of shingles.
Can anyone help?
Thanks,
Nickey
GBA Detail Library
A collection of one thousand construction details organized by climate and house part
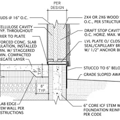
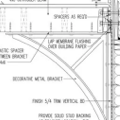
Replies
Nickey,
Your description is a little confusing, but it sounds as if you want to use the flash-and-batt method for an unvented sloped roof assembly (a cathedral ceiling). If you haven't read them yet, you should check out these two articles on the topic:
Flash-and-Batt Insulation
How to Build an Insulated Cathedral Ceiling
In your climate zone (Zone 4A), building codes require a minimum of R-49 insulation for roofs. According to the code, if you want to use the flash-and-batt method on this type of unvented roof, the spray foam layer needs to have a minimum R-value of R-15.
The closed-cell spray foam you installed (1.5 inch) has an R-value of about R-9.4. That's not enough to meet code. You need to add more spray foam to achieve R-15 (and to avoid moisture problems). Two and a half inches is about right.
What matters is the ratio between the spray foam and the fluffy insulation layer. If you can't afford to meet minimum code requirements, another possible solution is to skimp on the fluffy insulation layer. This article explains what you need to know about that approach: Combining Exterior Rigid Foam With Fluffy Insulation. (Even though the article talks about exterior rigid foam rather than spray foam, the same ratio rules apply in your case.)
In your case, 31% of the total R-value of the roof assembly needs to come from the spray foam layer. If your spray foam layer remains at R-9.4, that means that you can add a maximum of R-21 as fluffy insulation. Of course, you end up with a roof assembly that has a total R-value of only R-30.3, which is less than the code minimum. But at least it won't have moisture problems.
Nickey,
One more point: It's always a good idea to have an air barrier on the interior side of any fluffy insulation like fiberglass, to avoid the chance of convective looping or the chance that indoor air will enter the roof assembly and exit via cracks due to spray foam errors.
Tongue-and-groove pine boards are not an air barrier. The usual solution to this problem is to install taped drywall on your ceiling first, and then to install tongue-and-groove boards on the interior side of the taped drywall.
Martin,
Thanks for the answers, sorry about the confusing question but you do have it right about what I am wanting to do.
Since this is a workshop and not my living space could you tell me what would happen if I simply installed the pine ceiling, which would leave about a 3 1/2 -4" space between them and the foam insulation?
Also, if I went ahead and followed the recommendations above would heavy mil plastic with taped seams make a satisfactory air barrier?
Thanks again for your advice,
Nickey
Nickey,
Q. "Could you tell me what would happen if I simply installed the pine ceiling, which would leave about a 3 1/2 - 4 inch space between them and the foam insulation?"
A. You wouldn't have any moisture problems. You would just have a roof assembly rated at R-9.4 -- so the roof would leak heat at a rate that was about 5 times faster than a code minimum roof. Because of that, your heating bills would be higher than they would be if you followed the building code.
Q. "If I went ahead and followed the recommendations above, would heavy mil plastic with taped seams make a satisfactory air barrier?"
A. Not in my opinion. It's too easy to have holes or leaks in that type of barrier, which is why I recommended drywall. (Drywall does a better job of limiting air leaks at fastener penetrations, too.) Moreover, the poly would prevent your rafters from drying inward -- so if the roof ever got a minor leak, moisture might accumulate in your roof assembly.
Is your workshop conditioned, or do you just run a space heater if its cold when you're working? Do you work 9-5 M-F in the shop, or just on weekends? These questions might help you answer how much insulation is worth it in your shop.
Brendan,
I work in the shop in the evenings and on weekends. I have a natural gas heater that I use only when I am in there. I will have an air conditioner running in the summertime, if that helps any. We generally have about 2 - 3 months around here that it is necessary to heat, and not all days in that span.
Martin,
In rereading the last paragraph of your initial answer I think I found my answer. If I insulate with R21, which will make the foam account for 31% of the total R value. I will not be to code but I will not have moisture problems. If I went with R19 I suppose the same would apply with the foam accounting for 33%. I wish I could afford to have more foam put in but am hoping this will work. I only need to have temps around 60 in the wintertime. As for the air barrier drywall is not an option but I am thinking that the heavy mill plastic will be better than nothing. Do you agree?
Thanks
In zone 4 you only need 30% (minimum) of the total R to be the exterior foam to be able to use class-III vapor retarders on the interior.
A heavy plastic air barrier on the interior would be a problem- DON'T DO IT! That would create a moisture trap, since the assembly can't dry toward the exterior, and MUST dry toward the interior, but can't dry through heavy polyethylene.
If you want to use plastic sheeting as the air barrier, use 2-mil nylon (Certainteed MemBrain), which is fairly vapor tight when dry (less than 1 perm, a Class-II vapor retarder), but becomes vapor open when it's humid enough in the rafter bays to support mold.