Fixing the devil’s roof: flat and cathedral

So as a challenge to GBA readers how do I SENSIBLY increase insulation in a vented, leaky cathedral roof?
Story so far: we recently bought a 1960’s fixer upper in British Columbia’s Rocky Mountains with 4″ framing, cathedral ceilings with 8″ roof joists and a miniscule R10-ish of roof insulation. We’ve already upgraded the electrical, plumbing, windows, doors and HVAC and are currently adding an extension/garage. However we found water damage when tying the two together so plans to replace the old tin roof have accelerated…..
There is poly under the ceiling tile, so vented seems to be my only an option (based on the GBA cathedral ceiling article and others, though I thought closed cell spray would be possible except for it being winter). The current plan is to:
1. Strip roof to joists and spray with mould control
2. Seal any penetrations (surprisingly few) and repair poly as required
2. Fill joists with 2 layers of Roxul (8″ R28 ish)
3. Scab 2x to create a new air gap
4. Replace decking, membrane and tin
5. Tie air gap into low-slope ventilation AND install ridge vent
Question: Is there any way (or need) to improve on this without physically overloading the roof or my bank account?
Budget is very finite (on disability) so extra spending here reduces what we can improve elsewhere; diminishing returns are simply unsustainable. Code isn’t required (only R29 anyway), this is entirely because it should be done….
Thoughts please!
PS If people are interested I can post more images/details etc.
GBA Detail Library
A collection of one thousand construction details organized by climate and house part
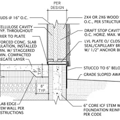
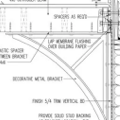
Replies
Since the roof is off the bests answer may be to cover the roof R30-R60 recycled rigid foam insulation in 2 or more layers staggering the joints.
Walta
Thanks Walta.
Rigid foam over the existing deck would be easiest, but leaves the air flow above the existing batts. Filling the void plus foam on top also seems to be a no-go given we have poly on the interior: am I correct in this?
Moisture control is the real devil with this project and having reno'd many buildings in Scotland I'm only too aware of the damage water can bring.
PS We are 5 hours from nearest city (Calgary) so finding recycled materials in bulk is next to impossible, I tried!
Plan B....
1. Strip roof to existing roof boards
2. Spray for mould control
3. Drill and fill void with densepack cellulose (compressing existing fluff)
4. Add vapor permeable membrane
5. Fasten 2x vertical sleepers to create ventilation
6. Strap and install tin
This is, in theory, far less work but it would be hard to repair the existing poly and penetrations. Also needs an extra trade (my contractor can perform first option himself).
Somewhere I would add "test that air sealing is effective".
Good advice and I may have to invest in a basic thermal camera Jon!
We tested a previous home with both blower door and thermal imaging and were shocked to find an internal wall was our greatest heat sink: it surrounded the chimney but had no insulation breaks at ceiling level.
Andrew,
Polyethylene on the interior is not ideal, but doesn't limit your options as much as you think, as long as (a) you make sure that the rafters, boards, and insulation are dry when they are encapsulated (this can be tough when working during the winter with no roofing), and (b) everything is fairly airtight.
You've been given a few options. Whatever you do, attention to airtightness is key. If you follow your original plan, make sure that you install airtight ventilation baffles above the mineral wool insulation. For more on this topic, see "Site-Built Ventilation Baffles for Roofs."
Thanks Martin
I am beginning to wonder if my 'understanding' is incorrect. (my mental health has failed badly in the last few years so please give me some leeway...)
These are my 'assumptions' based on the research:
1. With a poly vapor barrier inside, the roof HAS to dry to the outside (i.e. vents) as some moisture will get inevitably through from inside (unless I used closed cell spray foam)
2. Venting has to be outside of ALL the insulation (otherwise heat would just rise in the vent)
3. Given 2, I need to fill the existing vent if I am to add more insulation
4. XPS foam is a vapor barrier and won't allow the roof to dry so is a no go
5. EPS foam is better, but still a strong retarder in thicker layers (e.g. the recommended R25)
6. Spray foam isn't an option outside mid winter (hence our original plan to wait for summer)
7. Densepack (cellulose or mineral wool) is not to be used in unvented roofs
8. OSB and plywood should only be used above the vent (as they are retarders)
9. For unvented roofs a minimum of R25 foam is required above 'fluffy' insulation, but must dry to the inside
Given all this, my 'logic' was that rigid foam on top was a no go. Am I missing or misconstruing something? Alternatively, how would you do it?
The building inspectors advice was simply to add 2x4's over existing roof with insulation in-between and my contractor is very old school when it comes to insulation (but an excellent carpenter)......
This used to be my bread and butter (LEED for commercial buildings), but my health failed 6 years ago and now it is hard to put things together in my mind so a second opinion is greatly appreciated. Many thanks!