Finishing out a cold attic space – 2×4 rafters – zone 6 – gambrel roof

We’re working on a remodel of our 1920s dutch collonial house. There’s a lot going on with some new construction building a stairway into our attic and turning it into new, livable space. It’s currently a cold roof and we’re going to insulate and finish it out. The roof rafters are dimensional 2×4. We’re in zone 6 and winter temps can hit -20. Also, we’ve had some big snow loads over the last few years. Ice damming is a problem on many houses in our city.
Here’s my insulation plan. Please weigh in and let me know if this sounds like a reasonable approach.
• The roof rafters on the new construction that will join the existing roof will be 2×8
• I plan to sister 2×8 onto the existing 2×4 rafters of the old construction
• Then between all the rafters (new and existing-sistered), 7″ closed cell spray foam (~ R40-R45)
• I am then debating adding some foamboard on top of the sheathing. I’d like to keep this minimal as the rooflines are somewhat complex
Attached is a front profile showing where the attic space is. I understand we’ll lose a bit of livable space with sistering the rafters but I’d prefer to build this as a hot roof system. Thanks for all your expertise!
GBA Detail Library
A collection of one thousand construction details organized by climate and house part
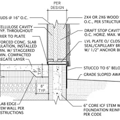
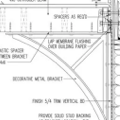
Replies
Generally it is very hard to insulate and air seal complicated roof shapes without SPF.
You can reduce the amount of SPF you need though. There is no need more than the minium needed for condensation control and the rest fluffy insulation or open cell SPF. Check here for the ratio:
https://www.buildingscience.com/documents/building-science-insights/bsi-100-hybrid-assemblies
Unless you need to add strength to the old roof, instead of sistering the old 2x4s, the higher performance option is to cross strap with 2x4 on edge. You can than spray foam area between the old rafters and install regular batts between the new 2x4s. Although the center of cavity R value of this assembly is less than the 7" SPF, because of the reduced thermal bridging, it provides a higher assembly R value.
>" I plan to sister 2×8 onto the existing 2×4 rafters of the old construction
Then between all the rafters (new and existing-sistered), 7″ closed cell spray foam (~ R40-R45)"
A couple of things rong with that picture
1:Akos has it right: SISTERING on to the pre-existing rafters increases the thermal bridging. Instead of a full dimension 2" of wood rafter thermally bridging the exterior 4", you now have 5.5", rendering most of that 4" of foam a real waste due to the excessive framing fraction. If they're 16" on center that's more than a 34% framing fraction even as a "clear assembly", probably closer to 40% for the actual framing. The framing will be conducting a major portion of the heat, delivering poor thermal performance. Do the math:
https://www.finehomebuilding.com/membership/pdf/184243/021269086NRGnerd.pdf
Unless the sistered 2x8s are needed for structural purposes roughly the same depth can be achieved with a set of milled 2x4s 24" on center mounted perpendicular to the old 2x4s. That way the thermal bridging will be dramatically reduces, since there will be at 3" inches of insulation between the original rafter edges and the indoors over the majority of the rafter length, and 4" of insulation between the exterior edges of the lateral 2x4s and the roof deck. This will outperform the new 2x8 raftered roof.
If more structure is required, converting the full dimension 2x4s into trusses using 2x3 as bottom chords, and 7.25" x 7.25" square guessets of half inch OSB as web, glued and nailed to both the 2x3s and existing rafters 24" o.c. will add a lot, and would offer at least an inch of thermally breaking insulation between the 2x4s and 2x3 chords, and less fully thermal bridged area overall (through the OSB gussets) than with sistered rafters.
2: Closed cell spray foam is one of the least green insulation materials in common use today due to the heavy CO2e footprint of both the high polymer per R, and in the case of HFC blown foam, the extremely high global warming potential of the HFC245fa blowing agent (about 1000x CO2 @ 100 years.) Even the (low global warming potential) HFO blown goods still suffer from the high polymer content per R though. To the extent possible it's better both financially and environmentally to minimize the use of closed cell foam. See:
https://materialspalette.org/wp-content/uploads/2018/08/CSMP-Insulation_090919-01.png
There are very few IECC climate zone 4B locations where it hits -20F with any regularity, few enough that hit -20C every year. A bit more specificity about your location might make a difference on how much foam it actually takes to get there.
If you're really in zone 4B, per the IRC prescriptives, it only takes R15 out of a presumptive R49 (a bit more than 30% of the total R) to achieve dew point control at the foam/fiber boundary, with the foam on the exterior side of the fiber (or even above the roof deck). Three inches of 2lb roofing polyiso (R17) above the roof deck would be sufficient to be able to use R30 rock wool (designed for 2x8 framing) in the new section. Polyiso is blown with low impact hydrocarbon blowing agents, and has about the same polymer per R as HFO blown polyurethane, using very similar chemistry. But by being installed in a continuous layer over the exterior rather than thermally bridged by framing, the full benefit of the high R/inch is achieved. From an environmental cost/benefit perspective it's a no- brainer. From a financial cost/benefit point of view it usually is too, even after factoring in the cost of an additional nailer deck and the fasteners.
On the older construction, if going with perpendicular milled 2x4s (3.5" nominal depth) over the full dimension 2x4 rafters, the full cavity depth is 7.5". Since batts are a lousy fit for full dimension lumber framing, it's better to use blown cellulose (R28 @ 7.5") or half pound open cell polyurethane (also R28), which is blown with a low-impact blowing agent (=water), and has about half the polymer per R of closed cell foam. The net CO2e footprint per R is about half that of HFO blown closed cell foam, putting it roughly on par with rock wool. A full 7.5" cavity fill uses less polymer than 2" of closed cell foam, and has about the same R value of about 4" of HFO blown foam. But the CO2e of cellulose would be NEGATIVE, the hygric buffering capacity of the cellulose would be protective of the roof deck, and during the cooling season the thermal mass effects of cellulose would give it a slight performance edge over R28 open cell foam.
Thank you both for all the information. A couple things.
Sorry, I am in plant hardiness zone 4b, IECC zone 6 (SW Montana). It's quite dry here but also can get very cold.
I am really interested in the cross bracing, perpendicular mounting of the new 2x4s. Also, great point about the thermal bridging as this would really reduce the possibility. Could you provide an example of what this sort of setup would look like? Any sorts of photos or diagrams where this has been used?
Mounting 2x4s on end could support drywall? Attach with structural screws or something?
Take a look here:
https://www.builditsolar.com/Projects/Conservation/MooneyWall/MooneyWall.htm
These are walls that are dense packed but the SPF/Batt roof would be similar.
I've done this with 2x3 on edge and used long screws. You can toe nail the 2x4, sometimes this tends to split them. If you use screws, pre-drilling makes it much quicker.
There is no issues with hanging drywall off it. I would add some vertical blocking to provide a bit of extra support.
>"IECC zone 6 (SW Montana). It's quite dry here but also can get very cold."
In zone 6 the IRC prescribes R25 out of the presumptive R49 ( a bit more than 50%) of the total R to be impermeable foam on the exterior of a foam/fiber stack up in unvented roof assemblies. See TABLE R806.5 (near the bottom of the page):
https://codes.iccsafe.org/content/IRC2018/chapter-8-roof-ceiling-construction
In that case going with 3" of closed cell foam (~R18 if HFC blown goods, R20- R21 for HFO blown foam) and 4.5" of cellulose (R17) would have an adequate foam-R / total-R ratio. The negative carbon footprint of the cellulose would also offset much of the CO2e footprint of the foam if using HFO blown foam.
An alternative to the perpendicular 2x4 approach would be to rip 2" thick polyiso foam board into 2" wide strips, and gluing & screwing them to the rafter edges with 1x2 furring through screwed to the rafters with 4.5" cap screws, mounting the ceiling gypsum to the furring. This is sometimes referred to as "Bonfiglioli strips", named for the builder who pioneered that approach, with lots of details here:
https://www.finehomebuilding.com/membership/pdf/9750/021250059.pdf
With 2" foam board it puts an R13-ish thermal break between the gypsum and the stud edge, and leaves a 6.75" deep cavity. That approach using 3" of closed cell foam there is plenty of dew point control on 3.75" (R14) cellulose.
If you're up for it, using 3" polyiso Bonfiglioli strips leaving a cavity depth of 7.75" would still work from a dew point control perspective with just 3" of closed cell foam, and 4.75" (R17.5) of cellulose. That takes 5.5" cap screws to get sufficient bite into the rafters, but that's not too awkward.
I ran into a similar insulating conundrum in zone 6. If I could do it all over, I would use (2) layers of 3" polyiso, top layer being vented nailbase, all above the structural deck air barrier and be done. You do want it vented if you never want the ice dams, at least according to Building Science Corp.
Instead I got clever (dumb) and suspended 2x2's with plywood gussets fastened to the existing 2x4 rafters. This made a nice, mostly continuous insulation gap of about 7". One lift of 3" ccspf for R19.5, followed by R19 batts (yes, I know better now) for code minimum U0.026. Inside corner/valleys were a pain. The whole thing was a pain. Gave me a new appreciation of simple roof lines. No ice dams yet, but no guarantees if too much snow accumulates.
Best of luck.