Female “project manager” for her small retirement home with a tall ceiling needs help please,

First, I want to thank everyone who contributes to this forum as I am learning a great deal. I have read everything I can about Cathedral ceilings and find myself needing to understand more.
I live in zone 6 in CNY.
The structure I am building is a 26×30 “Mountain/Lake/Chalet style” home with 8-foot walls and an 8/12-pitch roof. The south wall contains 4 casement windows and matching geometric windows above. Anderson 400 series. It will sit on a full basement ICF foundation.
The interior is open concept. The only room having 4 walls and an 8 foot ceiling is the Bathroom which is 8 x 10 which creates a small “loft” above. There is one other wall that is only 8 feet tall and separates the kitchen from the bedroom area. My builder tells me the ceilings will be about 15.5 feet and they will be 8 Inch tongue and groove pine. Sigh. I used to be so excited.
I will be installing a wood furnace in the basement. The chimney is in the center of the house and will exit alongside the ridge beam at the peak. We will heat primarily with wood and have a backup propane furnace.
I have engineered plans, for 2 x 12 rafters 16″ OC. These plans call for 5/8 CDX plywood, a “proper styrofoam baffle” and r49 insulation. the remainder of the house is 2×6 construction also 16″oc. My engineered plans are bare bones without much detail. Enough to serve as “plans” and the engineer is not very interested in assisting me with questions.
My code officer let me know that the u factor of the windows I have ordered and the small sq footage allows my roof insulation to lower to r38 and wall to r21.
My builder would like to do the following and I am unsure what to think of his suggestion.
I would like to list the layers for you from the outside of the roof down to the inside of the house where the T&G is attached to see if anyone here would be willing to comment on this idea and offer input.
The roof will have Vented soffits and a 1 ” gap on either side of the peak with a vented ridge cap. The layers from the outside in are as follows:
*26 gauge metal roof (not standing seam)
*1×4 firring 2′ oc horizontally
*Rfoil as a synthetic underlayment (sigh)
*2 rows of ice and water shield at the eaves (to create 6′ wide)
on top of 5/8 CDX plywood (call to engineer, he insists it should be plywood, no reason given)
*Accuvent baffle system for cathedral ceilings from the top rail (it bends down into that area and attaches eliminating blocking so I am told) to the peak of the roof.
*Owens corning R38C faced fiberglass insulation high density 9.5″ thick batt
*Tyvek house wrap to fully cover ceiling (taped I assume) as an air barrier *Tounge and groove pine attached to rafter bottoms
The code officer will allow it and says that it will satisfy a class 2 vapor barrier (kraft facing) and also an air barrier (Tyvek house wrap) and would pass the door blower test)
There will be NO canned lights in the ceiling. ( well…there were but after reading here I decided against it.)
Today I talked with a rep from Huber products about zip board for roofing material. His opinion of the above was that if we used zip board instead of CDX and as long as there was air movement under the roof above the decking and below the roof from the eave soffit to the ridge vent, provided by the accuvent baffles, we would have adequate ventilation to deal with any moisture that would escape into the cavity. He said the faced insulation does indeed satisfy the requirement for the class 2 vapor barrier, and he thought that using the Tyvek house wrap instead of drywall was unconventional but would work as an air barrier and save quite a bit of money and time.
Foundation work starts in November and the builder starts Mid Feb.
I am very grateful to the builder as it has been incredibly difficult in my area to find someone who isn’t booked out for the next 18 months. I want to trust him, and I want to get along with the building code officer, but I also don’t want a bad ceiling in my small little dream house.
Help.
Best regards,
Lissa
GBA Detail Library
A collection of one thousand construction details organized by climate and house part
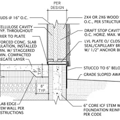
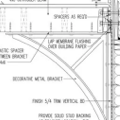
Replies
Your proposed roof will probably work and seems to be acceptable to the local codes guy. But this is really a minimum build. I don't know why he is allowing R38 roof, but this may be a local variation from the international codes that have been adopted in most jurisdications. The IRC 2021 requires R60 in your climate zone, and you would be well served to get as close to that as possible. First costs may be higher, but energy savings and savings on smaller HVAC equipment can more than make up the difference over time.
A relatively easy upgrade from your builder's proposal would include stuffing as much FG in the rafter bays as possible. Standard (not compressed) unfaced FG is rated at R49 at 14", but can be compressed into a 12" rafter cavity even with baffles. The R-value decreases to around R40-45. You could then add a 2" layer of foil-faced polyiso insulation on the underside of the rafters with seams taped with foil tape. The foil gives you an ironclad air and vapor barrier and the 2" of continuous insulation gives you a big bump of R14 whole-ceiling R-value. The T&G is then fastened through the foam into the rafters. I've done several roofs this way with much success. Even 1" of polyiso under the rafters makes a big difference in whole-assembly R Value.
The 2" of foil faced polyiso is a good idea, as it accomplishes three things:
1. It increase the R value of the assembly which you really should do even if you are not legally required to do so
2. It blocks the thermal bridging that occurs through the framing
3. It is MUCH more likely you will get an airtight install than with tyvek at the interior
- because while the tyvek theory is nice, it is difficult if not impossible to obtain an airtight install because it is just much more difficult
- because there is less chance of ripping the tyvek while the T&G goes up.
You might even decide to have them screw a few furring strips to the underside of the polyiso and then attach the T&G to that so there are not 100's of penetrations in the polyiso
I am very appreciative of your input on my future home. I have read that compressing the fiberglass does indeed diminish its R-value. I understand what you are communicating, but have to find a middle ground between the ideal and the code. We are heating with wood/coal (with a propane furnace as backup (a little upside down from the norm and code, but it is a resource we have and are used to here on the farm) and it will be our primary heat source despite what the code requires. We are blessed with a large forest on our property from which we remove trees that need to be culled from to keep us warm and our wood lots safe.
In the main farmhouse that our daughter will be taking over, we heat it with wood and it's about 100 years old. We have good insulation that was supplemented with cellulose, but the house breathes well. It has a unique balance of heat between our old Thatcher gravity cold air return furnace and insulation. We are trying to duplicate that in our little "dobby" house (Amish for grandfather's house).
I think at the crux of it, is to be sure that I am protecting this very small insulated space that I have no access to, from moisture and rot long term. It is not lost on me that I currently live in a home built with older materials, but well built and maintained and I haven't harmed its structure or longevity or ability to protect me despite its age. I am trying to be sure I can somewhat duplicate that in our wee little house with the tall ceiling. Thank you sincerely for the advice and please know it is valuable to me in bits and pieces to my whole.
Best regards, Lissa
The roof assembly you described generally makes sense to me. I don't see any advantage to using zip instead of CDX plywood, but I don't see any particular disadvantage either, as long as your engineer approves it.
The critical piece is that the taped Tyvek be successfully detailed as an air barrier.
You said you have no can lights, that's good.
Some things to discuss with your contractor:
- What is the wall air barrier?
- How does the wall air barrier connect to the Tyvek ceiling air barrier?
- How are the penetrations (such as the chimney) going to be detailed to be airtight?
- When is the blower door test being performed, and will they have access to the ceiling air barrier to fix any leaks that are identified?
- If you are running any wiring through the ceiling, it might be worth having furring strips below the Tyvek to create a little cavity between the Tyvek and the T&G to run wiring through so that it doesn't have to penetrate the air barrier.
Lissa,
Your roof will perform fine. It's at the low end of what you would ideally have as R values, but without adding another layer, it's about as good as you can get, and doesn't pose any problems as long as it is well-air-sealed.
I don't see what Zip roof sheathing will give you that plywood doesn't, and I'm not sure what the strapping under your metal adds, but those are preferences, which don't appreciably affect the performance of the assembly.
"Sigh. I used to be so excited." Come on now - you are building your own house. No reason to lose that feeling.
> ""Sigh. I used to be so excited." Come on now - you are building your own house. No reason to lose that feeling."
+1 for that :-)
I tell my customers that for the first 2/3 of a project, it looks like you're just moving piles of stuff back and forth. The last 1/3 it looks like a lot goes fast. You WILL get there, but construction is a scary process if you haven't gone through it before.
Plywood is generally considered to be superior to OSB in terms of longevity, especially in the presence of moisture. I would consider plywood to be an upgrade from OSB, especially on a roof. For a while, plywood was cheaper than OSB too due to something in the supply chain wierdness, but I don't think that's still the case. OSB was originally developed to be a cheaper alternative to plywood. I don't think Zip gains you anything though, since Zip's real advantage over regular OSB is that it has a factory applied WRB in the form of the characteristic green coating. Zip is usually considered to be a better grade of OSB compared to plain OSB panels though.
I don't see much in your plans that jumps out at me as potential problems. I would recommend trying some reflective lighting in large catherdral ceiling areas (cove lighting), since I like that even, diffuse look that gives, and it doesn't require you to cut any holes in the ceiling. I also agree with Peter that continuous insulation (rigid foam) is a big upgrade in terms of R value, and also air sealing in most cases, that can really help with both comfort and energy savings. I usually try to put exterior rigid foam on all the walls, but it can help with roof assemblies too. I would also recommend insulating the exterior of the foundation walls, which is something you need to put in prior to the concrete being poured. That might already be required by your local code, but I didn't see you list it, so I wanted to mention it. insulating the foundation walls and under the slab really help, and have to be done from the beginning.
Bill
I would consider the ceiling penetrations- you will need some, but dont put more than you need, and detail them correctly. You will want a ceiling fan to push the warm air down, and the fan will need to be able to be installed on a sloped ceiling. This is a very important detail with wood heat and high ceilings.
With the open concept, where will your plumbing and radon vents be installed so they can go out the roof? These will typically be run up through through a wall tot he roof, make sure nobody tries to install them in exterior walls, as this will reduce insulation levels unacceptably. Maybe a chase can be built on an exterior wall for these pipes.
Good luck!
"Sigh. I used to be so excited".... this might be more challenging because you don't do this everyday. If you think of yourself as a PM, then it is just part of the PM's job. Like another day at the office. Looks to me like you are doing a darn good job at that asking questions and getting help. That is part of the PMs job.
-> 26 gauge metal roof (not standing seam)
26 gauge is standard, so no worries.
I would mention that we chose 24 gauge because we wanted it to be more sturdy, wear better and hopefully deal with our hail storms a bit better.
By the way, you can reduce your cooling costs in the summer by choosing a light color for the metal or galvanized or galvalumne. You can read about that in this article.
https://www.energyvanguard.com/blog/the-best-way-to-cool-your-attic/
This link explains difference between galvanized and galvalumne
https://sheffieldmetals.com/learning-center/galvalume-vs-galvanized-metal/
-> *Rfoil as a synthetic underlayment (sigh)
Yes, sigh. This is not a problem in it self, but the benefits of "foil reflective insulation" are somewhat overblown. There are articles on GBA, including one written by Martin Holladay but I will avoid quoting them. Again, not a problem but there are better products out there.
>> I'm not sure what the strapping under your metal adds so I then looked at Rfoil and voila!
Apparently the strapping is recommended or required by the manufacturers of the RFoil product. See image attached. Image is from page 2 of the brochure on this website.
https://rfoil.com/media/rFOIL-2200-2500-Thermal-Roof-Underlayment-Brochure-Y17-2b-Web.pdf
>> Potential value added of strapping
If youy keep the strapping, it can help reduce the risk of ice daming if there is not enough insulation (other have mentioned this). Strapping can reduce thermal bridging. Loof for the section titled roofs in this GBA article.
https://www.greenbuildingadvisor.com/article/thermal-bridging-how-it-works
>> Strapping, not a problem but there is a cost
So the strapping is not a real problem. It is just that when you combine the extra cost for RFoil (that apparently offers limited benefits) with the cost of strapping you could find better ways of spending your money - like Polyiso on the inside with taped seams. There are many synthetic roofing underlayments that would offer better value (but not necessarily cheaper).
-> 5/8 CDX plywood and zip board instead of CDX
I am a big fan of ZIP but I agree with others that I don't see any problem here with CDX.
Having 5/8" is really nice. Our code allows 1/2" but I would only ever want 5/8".
-> 2 rows of ice and water shield at the eaves (to create 6′ wide)
Protection against ice daming is good. 6' wide is good. As mentioned in my comments here, the strapping may also contribute to reducing the risk of ice daming. Of course with good insulation, an 8/12 pich and then metal roofing, I hope you will not have ice daming.
-> *Accuvent baffle system (it bends down into that area and attaches eliminating blocking so I am told) to the peak of the roof.)
Accuvent will likely not cause any serious problems. Using blocking is not much better if it is not installed well. Accuvent is an engineered product (I think so???) that is a quick,easy reliable way to create a gap between the insulation and the roof deck (CDX here).
My only concern is minor in that when the Accuvent is "bent down", it is not usually or unlikely to be sealed on the vertical sides and the bottom. This allows cold air to get into the insulation at the edge of the roof. When the cold air comes in, it will be very close to the Tyvek. The Tyvek has no insulation value so the cold air gets really close to the warm air just under the Tyvek.
One solution to this has already been mentioned. Bill and Peter recommended a layer of Polyiso under on the inside. This would solve some of the things that I personally see with Accuvent. This all said, consider that wood blocking that is installed without air sealing on the sides or bottom will have the same problems and wood blocking is not continuous at the edge like Accuvent is continuous.
-> Owens corning R38C faced fiberglass insulation high density 9.5″ thick batt
I echo what others have said about more insulation.
-> *Tyvek house wrap to fully cover ceiling (taped I assume) as an air barrier.
Tyvek appears to dominate the North American market. If it is well installed as a weather barrier on the outside of walls, then I have not issues with it. But when it goes on walls, there is a solid piece of wood sheeting underneath it. Also, the commercial version of Tyvek is apparently sturdier (better) than the residential version - something to consider.
>> Trouble spots for air leaks
Someone mentioned "detailing" the air barrier. It may be helpful to explain that detailing means sealing all the gaps: holes, inadvertant cuts, seams where they overlap, at the edges, around pipes, connection to the wall air barrier, etc. That "detailing" is much more challenging to get right when working with a flexible material like Tyvek or any other weather barrier that comes on a roll. The "detailing" is made much easier when the air barrier is a rigid board material, like polyiso. For example, if you have a gap around a pipe, you can fill it with spray foam and then tape on top of that. Sealing seams is much easier on a rigig board because you can press down on the tape to make sure the tape fully bonds to the surface.
There are many articles on GBA about air leakage problems. I found this one that specifically talks about ****Tongue-in-groove wood-paneled ceilings. **** The article suggest 2 solutions but the suggested by Bill and Peter are better in my opinion because it adds insulation and you can easily tape the seams of the Polyiso.
This article lists some trouble spots for air leaks (there are more) and one mentioned is where the walls meet the ceiling. One reply here mentions that it will be important to make sure that the air barrier on the wall is connected (likely with tape or sealant) directly the the air barrier on the ceiling.
https://www.greenbuildingadvisor.com/green-basics/air-barriers
If ever the engineer refuses to change the plans to include polyiso on the ceiling, you might ask your inspector whether you would actually need a new set of engineer approved drawings to add this additional layer. If adding to something to improve the assembly, some inspectors might be fine with it. Of course, any that the inspector says verbally could be changed later if another inspector comes along. If you choose this route, maybe write an email to the the inspector just indicating that you are recaping the conversation you had with him/her.
>> Air leak at the peak
The stack effect (lots about this on GBA) will be concentrating its force at the peak of the roof, in my opinion. You would want to make sure that
-> Strapping under the the tonge and groove pine
Adding a 2x4 "on the flat" to create a 1.5" cavity can be really helpful. That gap allows you to put standard size light boxes for ceiling light fixtures without creating holes in your air barrier (hopefully some polyiso.)
-> Tounge and groove pine attached to rafter bottoms
Wow! This is going to be really nice.
-> Back up to air sealing.
If ever you get an undesirable result with you blower door test - before you move in - you can always look into Aerobarrier. I used this on my house.
https://www.greenbuildingadvisor.com/article/aeroseal-rolls-out-air-sealing-technology-for-houses
-> Wood furnace
I was just this past week listing to a recent episode of Building Science (BS) and Beer - associated with GBA. They were talking about "Masonry Heaters". They are apparently increadibly efficient and produce a very nice "feeling" of heat. They are used widely in Scadinavia and Europe. They apparently make tiny ones that produce 3500 BTU/hr (about 7% of a normal house's requirements) and very large ones for very large homes. This might be less expensive than a wood furnace (not ducting) and produce better results. I will add the link here later.
https://youtu.be/y-EMYz-4iq4
Chin up! I think you have a people rooting for you :)
My parents have a Tulikivi masonry heater. It was very expensive. And it is very pleasant to sit near. The flue passes through an integrated bench, so you can sit on and lean against the warm soapstone. The upgrade from a conventional wood stove to a soapstone masonry heater is more of a luxury upgrade than a green building upgrade in my book--but boy is it luxurious!
I don't know anything about ducted wood furnaces, so I've got nothing to add to that comparison ;)
The green angle is very appropriate for our discussions.
They use 35-50lbs (16-22kgs) of wood per firing, usually twice a day in heating season, providing enough stored heat to last the whole 24-hour period.
They are very efficient and produce very little pollution.
They burn so clean that they are exempted from wood-burning bans (even in Washington).
They fall into the super-low-emissions category.
Pros and Cons listed here. (Yes there are cons like anything else.)
Source: http://www.solar365.com/green-homes/heating-ac/pros-cons-masonry-heaters
In terms of masonry heater vs wood stove, are those masonry heater stats you listed notably different from a high-efficiency wood stove that meets the current EPA emissions standards? (Honest question, I'm not a wood-heat expert).
To be fair to me, you first mentioned conventional wood stoves. EPA says "With an EPA-certified wood stove, you can expect to use up to one-third less firewood than you would using an older, less efficient stove."
https://www.epa.gov/burnwise/frequent-questions-about-wood-burning-appliances#about
>> 1. This is the EPA list of certified wood stoves. You can sort by any column. You can see some are over 80% efficient.
https://cfpub.epa.gov/oarweb/woodstove/index.cfm?fuseaction=app.searchresults&manufacturersid=0&bturange=0%20BTUs%20%2D%20100000%20BTUs&efficiencytested=0%20%2D%20100&emissionrate=0%20grams%2Fhr%20%20%2D%2010%20grams%2Fhr%20&fireboxvolume=0%20Cubic%20Feet%20%2D%2010%20Cubic%20Feet&fireboxVolumeLower=0&fireboxVolumeUpper=10&heatoutputlower=0&heatoutputupper=100000&lu_appliancetypesid=5&lu_appliancesubtypesid=0&lu_fueltypesid=6&lu_testmethodsid=0&nspscompliance2020Only=no&recs2display=100&searchterms=&searchtype=advanced&z_outofproduction=0&sortby=EffSort
>> 2. Looking at central air wood furnaces, EPA lists 4 of them that burn cord wood.
Efficiency is between 75% and 83%
https://cfpub.epa.gov/oarweb/woodstove/index.cfm?fuseaction=app.searchResultsWH
Washington list of furnaces
https://fortress.wa.gov/ecy/ezshare/AQ/PDFs/wood-furnaces-approved.pdf
>> 3. Looking at Masonry, with my reading I see many claims of 90% efficiency but that does not align with what I see on the Tulikiv website. They have Masonry heaters between 81% and 83% efficiency. This website claims an efficiency rate of 77% up to 85%, which is more reasonable than the 90% claims.
http://www.homeenergy.org/show/article/id/2228/viewFull/yes
EPA does have a list of approved masonry heaters with emission ratings in gram of particulate matter per Kg of wood.
https://fortress.wa.gov/ecy/ezshare/AQ/PDFs/wood-masonry-approved.pdf
Greenstone Soapstone Masonry Heaters claims that masonry heaters will reduce the amount of wood you burn by 70-80% compared with a traditional wood stove or fireplace. So this is not comparing to 2022 EPA approved wood stoves.
http://www.greenstoneheat.com/80-percent-wood-reduction/
Comparing masonry heaters and wood furnace against wood stoves for emissions is a bit more challenging (for me).
-> Wood stoves (slower burning) measure emissions in grams/hour.
To get to a real comparison I suppose you would need to compare the actual EPA test results to understand which wood types are being used, the BTUs stored in that type of wood, the amount of wood burned per hour.
-> Central air wood furnaces evaluated on pounds (lb) of particulate per Million British thermal units (mmBTU).
-> Masonry heaters emissions are shown based on gram of particulate matter per Kg of wood burned in the link provided above. EPA 2014 proposal was 0.32 lbs per mmBTU.
This is because they burn wood very fast, within 60-90 minutes.
https://www.epa.gov/sites/default/files/2013-12/documents/proposed_requirements_for_masonry_heaters.pdf
Note about masonry heaters: "...since they are typically among the cleanest and most efficient wood heaters anywhere, Colorado and Washington states have compiled lists giving them better recognition and acceptance."
http://www.forgreenheat.org/technology/masonrystoves.html
https://cdphe.colorado.gov/indoor-air-quality/approved-indoor-burning-devices
https://ecology.wa.gov/Air-Climate/Air-quality/Smoke-fire/wood-stove-info
Hugh,
When I said that I didn't think strapping added much, that was looking at what it brought, versus what problems it might cause.
It yields an air-space necessary for the reflective barrier to work. That's all I can come up with as a positive.
Against that you have:
- It creates an air-space for condensation to accumulate in.
- It moves the onus for strength to resist point loads (debris or workers) from the sheathing to the roofing panels, making them more vulnerable to damage.
- As it is horizontal, there is no ventilation channel, meaning it doesn't help avoid ice-dams.
- It is above the sheathing meaning it doesn't appreciably reduce thermal bridging.
Again, it's not a big deal either way, but I don't think it yields the attributes you have listed.
Apologies Malcolm, I must have chosen my words wrong. I will remove the reference to your comment. Please accept my apologies.
Hugh,
There is no need to apologize. I just wanted to clear up what I see as misconceptions around the use of strapping.
You can reduce thermal bridging by strapping walls or roofs, but (simplifying wildly) that needs to occur in the insulation layer. So for instance an exterior rain-screen does nothing to help, where a Mooney Wall does.
And the idea behind strapping roofs to reduce ice-dams is to reduce the temperature of the roof surface by introducing cold air underneath. Horizontal strapping, especially when there is a ventilation channel under the sheathing, won't effectively do that.
Well the good thing is that the author of the question will now be armed with lots of information about the strapping on a roof. That can't be bad :)
I highly recommend this article from GBA if you have not found it yet. I talks about many of the same issues that are being raised and talks about solutions. You will notice some familar names in the article :) who have also contributed to your thread.
https://www.greenbuildingadvisor.com/article/designing-air-barrier-timbered-cathedral-ceiling
An exposed ridge beam looks nice inside, but there’s a risk that it can get cold enough in a New York winter to cause condensation. And then rot after some years. And then come the carpenter ants. A neighbor of mine has this problem.
norm_farwell,
I think there is a big difference in the risk depending on whether it is dropped or flush. If it is dropped, the control layers can be continuous over the whole ceiling.
I have been finishing a half built cabin with a similar roof/ceiling assembly (inherited design).
Installing the sheet air barrier on the ceiling, under the rafters proved to be time consuming and difficult. It would have been much easier to use a continuous layer of foam, with taped seams, as others have suggested here.
User ...048,
It is a bit difficult the first time, however it's maybe worth noting that 99% of houses built in Canada still successfully use poly on their ceilings as an air/vapour barrier.