Feedback on partial unvented cathedral ceiling with cellulose

Hoping to get some perspectives on safety and avoiding mold. Have a 1900’s 2.5 story house in climate zone 6 I believe (Toronto Ontario area). The attic is just big enough finished to fit an office and a bed if everything is placed right. However, that sets up some challenging issues with insulation. Now I recognize I will never be able to get it up to modern code standards, but we recently had raccoons find their wait into the little attic space there is and we have now gutted the drywall from the ceilings.
The situation is that we have a mini-cape cod house isolated in the 3rd floor attic and was wondering how safe this plan is. The attic has knee walls, and behind the knee wall triangles there isn’t anything. At the top of the attic there is another triangle where there are mushroom vents. Between the knee walls and the top triangle I have 2×4 rafters.
Essentially I’d like to insulate the whole thing with cellulose. In the lower triangles behind the knee high walls, put some blocking down and fill the triangles all the way up. In the cathedral ceiling section between the knee walls and top triangle, put cellulose between the rafters. And in the top triangle, blow in cellulose but keep the very top of the attic open and vented in mushroom vents.
I’m thinking in this situation, with a ventilation channel, it’ll be alright because the moisture will move up to the ridge and then be vented out through the mushroom vents.
I’m considering making it safer by using a smart vapour membrane, but the previous owners had the same insulation plan with 6mil poly, and when we took everything out, the wood looked fine. So i’m thinking of using 6mil poly as the air barrier with interior polyiso to bring up the insulation a little bit.
I’m thinking based on BSC testing article, that this just might work because of the open vented mushroom vents and open top triangle?
Or am I just deluding myself. And of course, I can’t get it up to code without essentially losing the entire attic’s usable space, or rebuilding the roof from the outside, which we will consider in the future when the shingles go…
Thanks for your thoughts in advance
GBA Detail Library
A collection of one thousand construction details organized by climate and house part
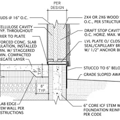
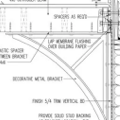
Replies
There is some good information here:
https://www.greenbuildingadvisor.com/article/a-low-carbon-approach-to-attic-retrofits
Thanks that's exactly what I was referring to, just hadn't found that particular follow up article!
If it helps, the prior owner did this exact setup with fiberglass Batts and 6mil poly everywhere. It was probably there for 15-20 years and when I took it all down this year, the roof sheathing and rafters are still in good condition (100 years on from being put in and 15-20years with the fluffy + poly).
What do you think about an inch of polyiso on the warm side of the sloped sections? It would prevent drying towards the inside in that section. but it would improve the u value of the assembly considering the limited space... I'm think that if the 6mil poly was ok, then doing the polyiso would be equivalent... My only concern is that cellulose is more dense than fiberglass and perhaps the upward vapour movement may be worse and thus better to add drying to the inside with a smart vapour barrier if taking away air movement...
Am I over thinking it?
Reading the article again it made me think of 2 more questions:
- if able, would connecting the soffit vents at the bottom to the filled in sloped rafter bays make sense? Would it allow for some venting down or through to the top mini-attic? Or would it more likely cause risk?
- if one had access behind the knee walls, would it be better to have the air barrier run along the ceiling of the 2nd floor and then up the knee wall? or put it straight in line with the rafter bay? If we ran the air barrier along the ceiling and then up the wall, it would give us the opportunity to fill the entire space behind the knee wall with insulation to increase the insulation a bit no?
Not sure it matters to vent bellow. The important detail there is to air seal the top plate area of the floor bellow as this tends to be a major leak point especially with paster and lath construction.
I think the air barrier along the rafter is the simpler one especially if you have ducting in there. Make sure to carry this air barrier down to the ceiling bellow, this will mean some notching and fiddling around the ceiling joists.
There is no issues with using rigid insulation for the air barrier. It is actually simpler as it is easy to detail around intersection and you can fill those gaps with canned foam. Unfaced rigid or one perforated facing (ie some GPS) has some permeability so these will still allow for some drying capacity.
Thanks Akos, super helpful! Do you think it is important to be vapour permeable for the air barrier? i.e. 6mil poly or foil faced poly-iso would be bad ideas?
I'm just thinking that total perms of a theoretical assembly of:
1) intello plus + 1" unfaced EPS + drywall + paint
is relatively low no? , perhaps low enough to justify the cheaper 6mil poly and increased R value of foil faced polyiso?
Assuming that the top attic triangle venting is doing the heavy lifting here for moisture removal?