Faced OR Unfaced XPS Insulating Sheathing

I have a few questions regarding the following wall assembly in Climate Zone 4A and Hygrothermal Region Mixed-Humid. It is very similar to Building Science Corporation’s Enclosure Design for Charlotte found at this link https://buildingscience.com/documents/profiles/etw-charlotte-profile. The biggest difference between this wall assembly and the Charlotte wall assembly is that this wall is completely sheathed with OSB and then over-sheathed with rigid insulation whereas the Charlotte wall is not completely sheathed with OSB so must have an alternative method for dealing with shear.
Wall Assembly from Exterior to Interior:
-Painted Brick and Fiber Cement Siding
– Air Space (1” air space behind brick. 3/8” air space behind siding using vertical spacers)
– 1” thick DOW XPS insulating sheathing with joints taped as WRB per ICC-ES Report
– 7/16” OSB
– 2×4 wood stud wall
– Unfaced Fiberglass Cavity Insulation
– Gypsum Board
– Latex Paint
Questions
1. Should the 1” DOW XPS insulating sheathing be faced (0.3 perms) or unfaced (1.5 perms)? Would both work? In a mixed-humid climate with both heating and cooling seasons the unfaced, vapor semi-permeable XPS might initially be chosen to allow drying of the wall assembly to both the interior and somewhat to the exterior. Brick and fiber cement siding are both reservoir claddings, so there is an argument to use the faced, vapor semi-impermeable XPS to combat the inward solar vapor drive. Although in this case both the brick and siding will be back vented with an air space decoupling the cladding from the face of the rigid insulation and the brick will be painted reducing the amount of water absorbed by the brick from rain thus reducing the inward solar vapor drive. The wall will be able to dry to the interior by using unfaced fiberglass cavity insulation, gypsum board, and latex paint.
2. Any reservations/concerns about installing the rigid foam board directly on top of the OSB? From the many resources I have read and if I am interpreting Building Science Corp’s articles https://buildingscience.com/documents/insights/bsi-038-mind-the-gap-eh and https://buildingscience.com/documents/insights/bsi-071-joni-mitchell-water-and-walls correctly, using the rigid foam as the WRB placed directly on top of the OSB should be fine as long as the wall can dry to the interior. Although, these articles do not seem detail the rigid foam directly in contact with the OSB without some type of “draining” housewrap or small drainage plane created between the rigid foam board and the OSB.
GBA Detail Library
A collection of one thousand construction details organized by climate and house part
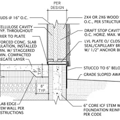
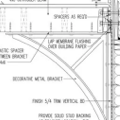
Replies
Either would work in your climate zone & stackup.
Swapping out the XPS for 1" polyisocyanurate would be greener than XPS due to the much lower impact blowing agent (pentane instead of high global warming potential HFCs), and it would have a slightly higher performance. As XPS loses it's HFCs over the lifecycle of a house it's performance drops to about R4.2/inch. Foil faced polyiso is very easy to air seal using temperature rated foil tapes.
Foam shrinks a little so I would add the housewrap (taped) or at least tape the OSB.
Any type of rigid foam will work from a building science perspective. From a green building perspective, as Dana Dorsett correctly notes, either EPS or polyiso is preferable to XPS. Foil-faced polyiso is easy to tape.
As John Clark correctly notes, your wall must have a water-resistive barrier (WRB); it's required by code. It's easier to detail housewrap as a WRB than taped rigid foam.
Don't forget: your WRB must be properly integrated with your window flashing.
-- Martin Holladay