Exterior walls

Zone 5a, Indianapolis
Single story ranch with slab on grade.
4 inch exterior walls
Current construction:
North facing exterior is stone (no weep holes) then 1/2 space then particle board then 2×4 framing with unfaced fiberglass batt then moisture shield ( guessing 3-4 mill regular clear plastic) then 1/2 in dry wall.
All other exterior walls are vinyl siding then particle board then 2×4 framing with unfaced fiberglass batting then moisture shield ( guessing 3-4 mill plastic) then 1/2 in dry wall.
Problems: all the walls are very cold in the winter. Also lots of moisture collects in the walls and does not dry easily to the outside because of the high humidity in the summer. Lastly, there were mold pockets but surprisingly only where there were previous roof leaks.
Solutions?
Because of other renovations, I will be able to strip the walls back to the studs. In the spring I will be redoing the exterior so will be able to remove all (siding and particle board if necessary. Also, renovations are happening in the attic so I will have unrestricted access to the wall and sofits.
First I would like suggestions on the best way to rebuild the exterior walls. I am open to anything.
I would an interested in a spray foam on the outside of the wall with possibly pearlite or no insulation or hydronic heating in the bottom half of the wall or a combination of the those in the wall cavity. Additionally, I would like to put rain screens on the walls and have the bathroom fans vented to the outside wall behind the rain screen.
Is any of that inadvisable? Is there an less expensive way to solve my the cold and condensate problems?
Thanks for considering
Edward
GBA Detail Library
A collection of one thousand construction details organized by climate and house part
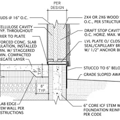
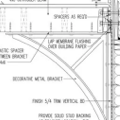
Replies
Edward,
Every exterior wall needs a good air barrier. Yours doesn't have one.
Every exterior wall needs a water-resistive barrier (WRB). Yours doesn't have one.
Every exterior wall needs an adequate insulation layer. Yours doesn't have one.
If you can afford the work, it would be a good idea to:
1. Remove the siding, particle board, and existing fiberglass batts.
2. Install a layer of exterior sheathing (OSB or plywood).
3. Drill holes in the new sheathing to permit the installation of dense-packed cellulose insulation between the studs.
4. Install one or more layers of continuous rigid foam on the exterior side of your wall sheathing. This rigid foam layer should have a minimum R-value of R-5, although a higher R-value is better. The rigid foam seams should be taped with a high-quality tape.
5. Install housewrap, vertical furring strips, and siding.
Of course, you would need to think through how you would detail your window flashing if you take this advice.
Is the particle board black (= asphalted fiberboard) on one or both sides?
Hello and thank you
to D. Dorsett - The particle board is black on the side facing the studs.
to Martin
1)are you suggesting housewrap on the outside of the foam board?
2) what is your opinion of spray foam on the outside vs foam board?
3) what is your opinion of pearlite inside the walls instead of cellulose?
4) if i put Pex in the bottom half of the exterior walls for hydronic heating, what if any insulation should be in the wall?
5) what are the concerns and problems with hydronic heating in the walls?
thank you
Martin, I assume you also meant to include in your advice to remove the poly vapor barrier.
Edward, here are my answers to your latest questions.
1) I assume he is suggesting that. I agree, although it can be under the foam. You can also use mineral wool boards instead of foam on the outside, in which case it is usual to put the housewrap under the insulation boards.
2) I know you asked Martin's opinion, not mine, but here's mine for what it's worth: Spray foam on the exterior is more expensive than foam boards, and likely to have a higher environmental impact, because it's harder to find spray foam with low global warming impact than it is to find foam boards with low impact. It also is harder to install siding on top of because it doesn't leave the surface as flat.
3) Pearlite is not as good insluation as cellulose--lower R value per inch. If you want an alternative to cellulose for some reason, and you are gutting the interior, you might want to use mineral wool insulation.
4,5. If you want hydronic heating in the walls, you can buy panels to put the tubing in, and still have the full wall available for insulation. But you will still lose some heat through the wall instead of it going to heat the space. For example, if your wall is insulated to R20, about 95% of the heat will go into the house and 5% will be lost to the outside. So you'd probably want thicker exterior insulation boards if you plan to do that.
But there are multiple problems and concerns, including:
Furniture placement blocking the heat from getting out of the wall, especially for the lower half.
Difficulty finding someone who knows how to design and install it well.
Likely high cost.
Leaks caused by puncturing tubing when you hang something on the wall.
I would sooner put hydronic heating panels in the ceiling than in the wall--less trouble with furniture blocking it.
Asphalted fiberboard is fairly immune to moisture, and isn't damaged even if left in the rain. It does NOT need a weather resistant barrier (it becomes it's own WRB, if the seams are sealed), but it does need to be made air tight.
But asphalted fiberboard is also fairly vapor permeable (more than 15 perms), which means during hot-humid summer days there is likely to be condensation forming inside the cavity if you are air conditioning, due to the presence of the 4 mil polyethylene. On steamy days with the outdoor dew points in the mid to high 70s the temperature at the poly sheeting can be below the outdoor dew point, and some amount of moisture would get into the cavity via diffusion through the fiberboard.
If the interior finish were standard latex paint (about 3-5 perms) and there were NO sheet polyethylene, condensation events would be pretty unlikely, and brief in duration if they occurred, since the paint would allow that moisture to dry toward the interior, to be dealt with by the air conditioning.
That high vapor diffusion helps the assembly dry toward the exterior fairly rapidly though (5-10x faster than OSB or plywood), which probably helped avoid mold issues.
Asphalted fiberboard adds R1.2-R1.8 to the "whole wall-R" value, relative to what it would be if you swapped it out for OSB or plywood. If air tight that's about a 10% improvement in performance 16" on center 2x4 studwall full of fluff.
If you're gutting drywall you can leave the particle board in place, and spend the money on exterior insulating sheathing rather than new structural sheathing. Strip the 4 mil poly, and pull the batts- if they're in good shape and reasonable density you may be able to re-use them, but before re-installing (or installing new ones), caulk the framing to the fiberboard wherever they meet, in EVERY stud bay, and lay a bead of caulk between doubled up top plates, and where the bottom plate of the framing meets the subfloor, making the sheathing the primary air barrier. Use can-foam to seal any wiring penetrations in the framing or sheathing.
In zone 5A you only need R5 total exterior to the sheathing for dew point control if it's a wood sheathed (OSB or plywood or plank) assembly, but for asphalted fiberboard (which is impervious to high moisture content) you only need R5-R5.5 exterior to the cavity fill fluff. The fiberboard itself is good for ~R1.5, so even an inch of EPS (R4.2) or an inch of polyiso (R6, but derated to R5 for temperture) would have you covered. More would be better, but the bare-minimum would be R4. If you change out the fiberboard for plywood or OSB it goes back up to R5. With that much exterior insulation you can safely skip the plastic sheeting on the interior- just take care to make the wallboard air-tight.
BTW: If you're keeping the interior it's often possible to dense-pack over R11 batts from the exterior without removing them. If it's impossible to snake a dense packing tube in with the batts in place, drilling multiple holes per bay and just blowing from the exterior to compress the batts can can work fairly well too. While it's not as air-tight as caulking the framing to the sheathing, blown fiber under pressure will find and fill most of the leakage area.
With the 4 mil poly still in place you can still use exterior foam, but ideally you'd give it more than the bare minimum called out for dew point control, and use foam that is semi-permeable to still retain a drying path, while impeding summertime moisture drives. Ideally it would be 1.5-2" of 1.5 density "Type-II" EPS (R6.3-R8.4), which would still be more than 1-perm, but under 3 perms (compared to 15+ for the asphalted fiberboard.) Foam board with impermeable facers would create a moisture trap when used in conjunction with the poly vapor barrier, and should be avoided. XPS has a vapor permeance a bit less than half that of Type-II EPS, and has a much heavier environmental footprint to boot, and eventually it's performance drops to that of EPS anyway, as it loses it's blowing agents.
Edward,
I disagree with Dana Dorsett on the question of whether asphalt-impregnated fiberboard (if that is indeed the product on your wall, which you describe as "particleboard") qualifies as a water-resistive barrier (WRB). WRBs are required by code and defined by code -- and no type of fiberboard, to my knowledge, has ever been submitted for testing or approval as an acceptable substitute for a code-required WRB (which, incidentally, is defined as asphalt felt). Plastic housewrap is an acceptable substitute, but not fiberboard.
So in my opinion, you still need a WRB -- either asphalt felt (tar paper), plastic housewrap (for example, Tyvek), or another code-approved WRB.
While not a code-defined WRB, asphalted fiberboard is still WAY better than bare plywood or rosin paper over plank. The fact that it's gone probably 4-5 decades or more without developing widespread moisture issues is pretty good evidence that it works, absence of accredited lab testing or code-approval for the application notwithstanding.
But things will change when adding exterior foam. If you're installing exterior foam you'll still need an additional housewrap, lapped correctly to the window flashing. If the window flashing only extends to the fiberboard layer, it's preferable to put the housewrap between the fiberboard & foam, and use a crinkle type housewrap (eg Tyvek Drainwrap.)
Hi - Thanks for the info.
I am still a little confused on how to approach the walls with stone on the outside- no weep holes, 1in gap to fiberboard.
What is the best way fix the wall to eliminate condensation problems. winters here are mid 30s with low humidity. Summers here mid 80 avg humidity 75% outside.
will spray foam on the inside on the fiberboard help with the condensation issues?
Edward,
On the wall with exterior stone and mortar, you will need to make all improvements from the interior. Your suggestion -- to install closed-cell spray foam on the interior side of the existing fiberboard sheathing -- is a good one. The closed-cell spray foam will provide an air barrier, a water barrier, and will provide R-value.
If you want, you can either provide all of the wall's R-value with closed-cell spray foam (you'll be aiming for at least R-20), or you can go with a combination of spray foam and air-permeable insulation (an approach called "flash-and-batt" or "flash-and-fill").
For more information, see these two articles:
Flash-and-Batt Insulation
Combining Exterior Rigid Foam With Fluffy Insulation
Midsummer outdoor dewpoints in Indinapolis average about 65F, which isn't too severe (you'd never air condition the house that low), but for the moisture drive off the masonry exterior. Adding weep holes would definitely help, as would adding a vapor retarder on the interior face of the fiberboard.
A flash-inch of closed cell foam, or cut'n'cobbled 1.5 inches of unfaced Type-II EPS (1.5lbs per cubic foot nominal density) would bring the vapor retardency down to the 1-2 perms range, or about half the vapor diffusion of standard interior latex paint. The vapor retardency would be low enough to prevent summertime moisture problems inside the stud cavity from the brick, and the R-value would be high enough for dew point control at the foam/fiber to prevent moisture accumulation from wintertime moisture drives from the interior. The EPS solution needs that thickness & density for vapor retardency only.
Using 1" plastic or aluminum faced Type-I EPS (1lb nominal density) would also be adequate for both winter & summer moisture drives, and would be even cheaper, and would be fine, as long as the sheathing is asphalted fiberboard. The facers are extremely low permenace- true vapor barriers, and need to be considered carefully before inserting into the stackup.