Exterior wall design in climate zone 7

I have read many posts about building wall systems in cold climates and have seen many opinions. I had pretty much settled on a REMOTE systems wall with Four inches of EPS on the outside of a 2×6 wall filled with Roxul. The EPS would be held with furrowing strips and no interior vapor barrier (ie. Poly). My builder thinks this is labor intensive and very expensive. In the search for an alternative, I have come up with a couple options that may be more acceptable.
1. Build a staggered stud wall. Use 2×8 top and bottom plates with staggered 2×4 on 16 in centres. Fill the cavity with closed cell, blown in foam.
OR
2. Build a standard 2×6 wall. Between the exterior sheeting and the studs, apply 2 inches of EPS foam board as a thermal break. Once the electrical is roughed in, add 5 inches of closed cell foam between the studs.
I don’t believe the would be a moisture problem with either system.
Any thoughts on these?
Chris
GBA Detail Library
A collection of one thousand construction details organized by climate and house part
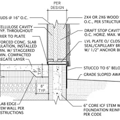
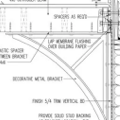
Replies
Chris,
What is it about walls? Why is everyone always trying to re-design the wall?
OK, I'm sounding a little tired -- and it's still only Monday morning...
Step one is to read this article: "How to Design a Wall."
Briefly, you can't install rigid foam between your studs and your wall sheathing unless you come up with an alternate bracing plan. I'm not saying you can't do it -- just that you need a plan. For more on wall bracing, see this article: "Four Options for Shear Bracing Foam-Sheathed Walls."
If cost is a concern, why are you thinking about expensive closed cell foam? Why not a simple double stud wall, filled with cellulose?
Martin,
Thanks for you reply. I should have been more specific. Both options would include 1/2 exterior sheeting. Option one would have it nailed directly to the studs and option two would be screwed using a structural fastener through the plywood, then the foam and finally into the studs.
Chris,
I stand by my response. If you install a layer of rigid foam between the sheathing and the studs, you can't expect the sheathing to provide bracing unless the entire system is designed by an engineer.
You're better off using Zip R sheathing panels, since they have had their system approved by labs who have performed testing for racking resistance and have come up with nailing schedules that work.
Ok, so it sounds like a 2x6 wall is out. What about the staggered stud wall. 4 inches or more of closed cell foam. Could use roxel on the inside 3 inches.
Chris,
You wrote that you plan to insulate your wall -- the one with 2x8 plates -- with closed-cell spray foam. That's usually a waste of money. Here is a link to an article that explains why: "Installing Closed-Cell Spray Foam Between Studs is a Waste."
Ok, so it sounds like a 2x6 wall with four inches of eps on the outside held on with structural screws like GRK is the way to go.
So I started reading about roofing systems. One of the "acceptable" options is:
Roof deck with venting underneath (seems a bit contentious as I have read this should not be necessary), then 6 inches of closed spray foam followed by fiberglass or rock wool batts.
Now I am confused. Why is this acceptable in a vaulted ceiling, but not a wall?
Sorry,
The GRK's will hold on the furrowing strips that would hold on the foam (in the wall assembly).
Chris,
Q. "Roof deck with venting underneath (seems a bit contentious as I have read this should not be necessary), then 6 inches of closed spray foam followed by fiberglass or rock wool batts. ... Why is this acceptable in a vaulted ceiling, but not a wall?"
A. If you want to install this on a wall, it is certainly acceptable. On a wall, the vent channel is called a rainscreen gap. The combination of closed-cell spray foam with fiberglass or rock wool on the interior side of the spray foam is called the "flash-and-batt" method. For more information on this approach, see this article: "Flash-and-Batt Insulation."
Although closed-cell spray foam between wall studs is acceptable, it isn't necessarily a good use of your money. To understand why, see this article: "Installing Closed-Cell Spray Foam Between Studs is a Waste."
Q. "The vent channel [for the roof] seems a bit contentious as I have read this should not be necessary."
A. If you install flash-and-batt insulation between roof rafters, the ventilation channel is optional.
Q. "I started reading about roofing systems."
A. Just as with walls, I would advise that it's better to install rigid foam on the exterior side of the roof sheathing than it is to install closed-cell spray foam under the roof sheathing. (There are three reasons for this advice: rigid foam addresses thermal bridging through the rafters; rigid foam is less expensive than spray foam, especially if you use reclaimed rigid foam that has been removed from another building; and most types of closed-cell spray foam are manufactured with blowing agents that have a very high global warming potential.)
For more information, see "How to Install Rigid Foam On Top of Roof Sheathing."
Seriously, closed cell foam is one of the least-green insulation materials commonly in use (even the stuff blown with low-impact blowing agents) due to the environmental impacts of the polymer production, and the high polymer weight per R. When it's high R/inch is being undercut by installing it be framing (whether rafters, joists or studs), it's important to know the rationale for using it.
For all practical purposes half pound density open cell foam is as air retardent as 2lb closed cell foam, at about half the polymer per R.
When using it for it's low water vapor permeance or for dew point control it's greener to use the minimum necessary for those purposes, which is usually substantially less than 5". But in a zone 7 climate for an unvented roof it takes R30, out of a code-minimum R40 total (or ~60% of the roof-R) to be closed cell foam applied directly to the underside for dew point control comes to ~5".
But R30 insulation (any type) above the structural roof deck achieves the same thing. And a vented R49 with all fiber insulation is usually cheaper, even when using I-joist rafters and dense-packed 1.8lb blown fiberglass or 3.5lb density cellulose to get there. When it can be designed out of the assembly (which is almost always possible), it's greener to avoid it altogether.
Rigid foam has similar polymer/R issues, but using RECLAIMED rigid foam from building materials salvage companies creates no new polymer, uses no new blowing agents, and can be had at a substantial discount (25-35% the cost of virgin-stock goods). That makes it greener than open cell spray foam or even blown cellulose (unless you subscribe to lifecycle accounting of cellulose as a means of sequestering carbon, which often takes huge leaps of faith on underlying assumptions.) In a zone 7 climate in a ROOF assembly the mean-temperature adjusted R of Type-II (1.5lbs nominal density) reclaimed roofing foam would be between R4.5-R4.7/inch, and Type-VIII (1.25lbs density- the lowest density typically used in commercial roofing) would be R4.4-R4.5/inch, so it would take 6.5-7" of above deck foam for dew point control with R20 fiber or open cell foam on the underside.
But when the insulation is continuous, not thermally bridged by framing the whole roof assembly only needs to hit U-0.026, or R38.5, and that includes the R-value contribution of the roof deck, roofing materials, plus the interior & exterior air films. That means you can reach code minimum performance with 8" of exterior, and nothing on the interior. From a total installed cost point of view, using only reclaimed roofing foam above the roof deck is usually going to be cheaper & easier than a foam/fiber combination in your climate (despite the cost of the nailer deck and longer screws) but not necessarily cheaper than an R49 vented all fiber approach.
Martin,
Thanks for your insightful responses. Looks like my builder is willing to work with me on putting foam on the outside of the framing. I continue to look for ways to simplify the build and came across the InSoFast panels. I realize the I would have to put more foam between these panel and the sheeting to meet the requirements for zone 7. Martin, your review on these is three years old. I was wondering what the current thought on these panels are. I plan to put canexcel (composite) siding on the building.
Chris,
My review of the InSoFast panels lists advantages as well as disadvantages. My opinion of the panels hasn't changed.
I'm not convinced that installing InSoFast panels will "simplify the build" (as you put it) compared to the use of furring strips, but if you've read the review, you're aware of the issues involved.