Exterior wall assembly

Hi,
I am building up on Mount Washington, Vancouver Island BC, Canada. The build site is at 1200m, record snow fall has been up to 9m.
Due to snow loads the walls will be 2×8 construction.
I am planning the wall assembly as follows and would appreciate any help with it:
1/2″ drywall
Vapor barrier (TBD depending on inspector)
2×8 studs
R28 batt insulation
1/2″ Plywood
Blueskin VP100 SA house wrap
2″ exterior EPS (Silverboard Graphite)
Metal siding
Thanks in advance.
Paul
GBA Detail Library
A collection of one thousand construction details organized by climate and house part
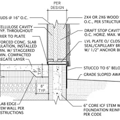
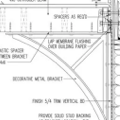
Replies
I don't have much experience building at elevation, but I worry that the foam is too thin relative to the wall .
By the books, northern Vancouver Island is climate zone 5, but it seems likely that at 1200m it is more like a zone 6 or 7. Per the manufacturer, 2" of that graphite EPS is about R9. Adding that to the R28 batts puts the center of cavity insulation value at R37. That means roughly 25% of your insulation is in foam, which is just shy of the cutoff for the IRC for climate zone 5. At elevation, I worry you might start running into condensation problems. The interior vapor barrier might cut down the risk if installed perfectly and detailed as an air barrier, but your assembly would be much safer with two layers of 2" EPS instead of just one. You can find fastener schedules in this nifty guide from BC:
https://www.victoria.ca/assets/Departments/Planning~Development/Permits~Inspections/Example~Plans/Illustrated-Guide-R22-Effective-Walls-In-Wood-Frame-Construction.pdf
You might also include a drainage gap between the EPS and the blueskin, though it probably doesn't matter. In all other regards the assembly looks good.
Note that while the IRC allows lots of different walls (including the one here just as it is), it says nothing about which ones are better than others. Nor does it use the % method for foam. And Canadians tend to ignore it. For what works best, consider the recommendations here (along with the excellent victoria.ca ones):
https://www.buildingscience.com/documents/digests/bsd-106-understanding-vapor-barriers
Be sure that some airflow is possible between the siding and the EPS.
It is true that the IRC allows for Paul's assembly, and passes no judgement on it. I use the recommendations from Table R702.7.1 as a good safety guideline. My preference for wall assemblies is personal, but it is based on good building science. I like those minimum foam thicknesses because I distrust interior air barriers, as they are tricky to install and easy to compromise. While the IRC only requires a vapor barrier, in general much more moisture can be carried by flowing air than allowed by diffusion, so recommending an interior air barrier is quite reasonable when dealing with thinner foam.
While the IRC does not explicitly use those percentages, they are implicit in the figures of Table R702.7.1. The percentages reflect how condensation actually works in walls that are not simple 2x4 or 2x6 assemblies with batts.
Thanks Aedi, I will look at the info you have included in more detail. Its difficult to determine the Zone for the mountain, looking at the temperature history it can drop to around 5 or 10 below.
I am having a hard time finding good data, but based on temperature data I could find it seems more zone six-y.
My recommendation for thicker foam is based on an abundance of caution. A well detailed interior air barrier installed following the instructions in the guide I posted should be safe, provided you don't go around punching holes in it later.
Paul,
I was involved in the repairs to a condo on Mt Washington a few years ago. It does get a staggering amount of snow. We had to dig the hydro lines out of a bank where they were usually 12 feet above the road.
The problems we had with the exterior stemmed from snow-melt accumulating against the walls. I'd pay articular attention to detailing the membrane at the bottom sill where it meets the foundation.
Your wall assembly looks good. Depending on the profile of your metal siding you may need strapping, rather than screwing through the foam.
Thanks Malcolm,
The bottom 8ft of the building is ICF but I will be paying attention to the transition between ICF and sill as the snow could easily pile up that high as you know.
9 meters of snow? You might consider going with a thicker plywood for your sheathing (maybe 3/4") to help brace the walls. Depending on how many window openings you have and how large they are you might consider adding plywood sheathing to the interior of the exterior walls as well (then covered in drywall or your finish material).
The last thing you want is an uneven amount of snow on one side of the roof causing the walls to twist or buckle.
What little I've read of the engineering here suggests that "not enough nails" is nearly always the limiting factor in the structural strength of typical wall sheathing, with an additional inspector complaint of "The nails missed the studs" being extremely common when the inspector bothers to complain, and very rarely tested by loads. In the Fortified Homes standards the dominant structural advice is specifying intense nailing schedules for things. In some seismic codes they actually recommend going up from 2x lumber to 3x (or more accessible, sistered 2x), not for strength, but just for better contact between nails and the edge of the sheathing (sheathing gets weak at the very edge, so there's a skinny tolerance between zero-strength connection to the sheet good, and zero-strength connection to the stud).
Holding back 9 meters of snow against a wall is... intimidating. I'm imagining the amount of bracing people add to tall, long sections of single-pour concrete formwork.
You might consider one of the more structural varieties of double stud wall, with blown-in cellulose. We have Larson trusses using plywood gussets, the Klingenberg Wall using I-joists, and I think in Alaska they sometimes use open-web 2x4 wall trusses, much like an increasing fraction of the country uses open-web floor trusses. Blown-in cellulose will cope with even a fairly irregular space, there may be a lot less issue with thermal bridging (particularly through eg all those nails) and it's cheap.
A good number of interior partitions engineered as shear walls would not be amiss here, or at least a few shear pilasters on the interior side of exterior walls (forming alcoves).
BSC offers https://www.buildingscience.com/documents/insights/bsi-031-building-in-extreme-cold for the slightly orthogonal case of extreme low temperatures.
Burninate,
I think you are right about the sheathing, but I wouldn't worry about making the wall more resistant to lateral loading. Snow exerts almost nothing but vertical loads. The walls will be wet, but that's about it.
I don't know that I believe that it can be this easy on an intuitive level. 9 meters is taller than many houses. Snow is heavy. There's got to be a structural reason we don't build our houses below ground level, aside from the obvious moisture reasons. Even a tiny fraction of horizontal bearing / creep would drastically overload a wall designed purely for wind forces.
But more importantly: I don't know that I believe that on a practical level. While most of us only have to deal with ice damming on the roof, wouldn't you be looking at it in the walls as well for this sort of condition? Anywhere you get snow acting as effective insulation, some of the snow should be melting against the heat source, and water (as well as ice-water slurry) exerts horizontal pressure.
it does seem counterintuitive, but I discussed this with a structural engineer years ago when designing a condo with a flat roof and doghouse-like penthouses. There is no horizontal component to the snow load.
Here is a link to a discussion on the topic:
https://www.eng-tips.com/viewthread.cfm?qid=302277
At least one older engineering guide mentions lateral snow pressures leading to some failures, but these failures seem to be related to snow creeping downhill or being pushed by a snowplow. For more information, see Snow and icing problems -- the quote in the image below comes from that source. ("Lateral snow pressures have also caused some structural failures. The plowing of streets may, for example, damage traffic sign poles. In Alaska, snow creep has caused failure of power transmission poles in steep slopes.")
Snow is very self-supporting, and so in general doesn't have horizontal loads. Think of how good snow is at staying on slopes, even steep ones -- it takes very special conditions to convince it to avalanche.
Any snow that melts near the house is quickly carried away from the assembly and re-freezes. The R-value of snow (and the high amount of energy needed for a phase change) means you don't get any slush mixture. In fact, I imagine the ice that forms strengthens the horizontal integrity of the snow.
Hi Paul -
RDH Engineering has done some great building industry information resources for Vancouver over the years, including this one: https://rdh.com/wp-content/uploads/2014/07/Guide-for-Designing-Energy-Efficient-Building-Enclosures.pdf.
Happy reading - Peter
Everyone seems to be considering the 9m of snow resting on he ground and whether downhill creep will cause it to push against the side of the house but what about the 9m of snow that lands on the roof?
Yes, wind will probably dissipate some of that snow from the roof but the shape of the roof may cause a large amount to remain in certain sections, such as valleys. Uneven loading of heavy snow on the roof could cause structural failure.
Scott,
Here is a study into exactly that: https://nrc-publications.canada.ca/eng/view/accepted/?id=e9de2c72-00c1-4160-b8f5-ba2baccb5d09
I'm pretty sure that the Comox District requires all projects to have a structural engineer.