Exterior roof insulation: top plywood?

Hello,
I’m in climate zone 5 insulating a low slope (1:12) unvented assembly.
The slope can’t be increased, unfortunately, due to site restrictions.
Insulation will be 9.25″ mineral wool batts in rafters, then 6″ of rockwool toprock DD above the roof sheathing (5/8″ plywood).
Roofing is standing seam metal with solar panels attached (S5 clamps).
I am having difficulty deciding on whether to include a second layer of plywood as a roof deck. Examples I could readily find details for were
1) The Fine Homebuilding California 2018 house where the stack was Plywood -> underlayment -> Rockwool -> underlayment 2 -> standing seam. They used long fasteners to attach the panels to the framing below, through the Toprock DD.
2) Matt Risinger’s house in production, with Zip -> Polyiso -> Zip -> Standing seam.
I am wondering if anyone has experience or comments with one or the other of these approaches.
Currently my stackup is
Intello Plus -> batt MW -> plywood -> Solitex Mento -> Toprock -> Panels, with no secondary underlayment (the roofing manufacturer has no stipulations about the stackup)
Approach #1 is attractive, but I have concerns about shear on the fasteners. Theoretically the fasteners should allow panels to slide and the Toprock will be separately nailed down so shear shouldn’t be communicated, but I am not sure about in practice. Also it makes details with an attached veranda somewhat tricky.
Approach #2 I worry about the ability of plywood or OSB as the top roof deck to dry in this unvented roof with solar panels shading it. Is this worry unfounded?
Thank you
GBA Detail Library
A collection of one thousand construction details organized by climate and house part
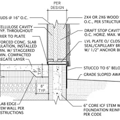
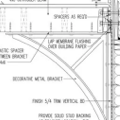
Replies
Bryan,
I will ask a question to give your post a bump. Have you check with the roofing manufacturer to see if it allows installations on a 1:12 roof?
Hi Steve,
Thank you for the bump. Yes, I went in the reverse direction -> searched out standing seam roofs that allow that pitch. I'd selected Fabral SSR 1 1/2"
Since the first question, I've realized it makes sense to put Ice & Water shield as the most outboard layer, since the standing seam panels would retard vapor flow anyways.
The question remains whether that should be applied to a second layer of plywood sheathing or directly to the toprock DD. If wetted, that second layer of plywood sheathing would have to dry through the entire stack to the inside.
I'd avoid cold wood in moisture traps whenever possible.
> since the standing seam panels would retard vapor flow anyways
Some claim that, but the little data I've seen suggests that the little bit of airflow you get does allow some vapor flow (when combined with permeable underlayment).
With a hybrid roof insulation as you are proposing, the vapor barrier should go above the permeable interior insulation and bellow the exterior rigid, this is where your peel and stick should go. The first layer of plywood can now dry towards the interior and the 2nd layer towards the exterior.
Most metal roof profiles have some air channels, some even qualify as a rain screen when used on a wall. Unless you go way out of your way to seal the metal up, there will be enough airflow to allow a bit of drying.
All metal roof manufactures call for the panels to be mounted onto a solid substrate, if you install over rigid directly, you would loose any warranty. There should also be an underlayment directly under the metal panel to protect the plywood bellow from any night time condensation on the underside and to allow for expansion of the panels.
For a proper standing seam over exterior rigid install, you either have to go with option 2 (I would skip the two layers of zip and go with good old plywood, much better) or strap out the rigid with battens as per the roofing manufacturer's specs.
Thank you very much for the replies and the discussion.
I've attached how I would detail it in light of your help.
Exploded view to show control layers and left some structural details out of the veranda roof for clarity.
As for changes:
#1, replace solitex mento with a vapor impermeable layer, such as perhaps peel and stick I&W. This now would prevent any diffusion of interior moisture from reaching the second wood layer, whether it be strapping or plywood.
#2 Add layer of purlins or plywood directly below the metal panels. As far as warranty - it's 2020. Not sure I've heard of any company honoring a warranty in decades. What's more important is the durability. It would be interesting to know how the FHB 2018 house is holding up without any such decking. I'd imagine that plywood is better in this regard and would certainly be more buildable when it comes to adding underlayment - just have to confirm uplift numbers with my SE as it may require 2x4 strapping as well and space is very limited.
#3 Replace final underlayment with generic underlayment. My understanding is that the specific choice here is no longer critical. Vapor open might be better if we believe there is some drying to the exterior. I do wonder if there would be appreciable drying (or what about inward solar drive wetting?) through the connected rainscreen gap in the wall.
As an aside, I'm wondering if the better option is to steepen the roof. It certainly would be better for solar panel efficiency and cleaning. The limitation is due to a second story window (this is an addition). That could, I suppose, be converted into to a deep-welled skylight in the addition roof, but I'm not certain which headache I'd rather have.
Bryan,
Before you get too far along deciding on the assembly, think though the overhangs in both directions. How the components interact, and how they support the overhang will determine a lot of the roof detailing.
The assembly you show should work.
Running the I&W down the wall is doable but taping the seams of the sheathing and standard housewrap is cheaper and works just as well.
If you are tight on space, go with foam instead of mineral wool. Especially if you can find it reclaimed, this is way cheaper and you can get the same R value with one inch less thickness.
R60 only makes financial sense with blow in insulation. Exterior rigid is too expensive to have any reasonable return on a roof much above R35. In your case you can comply with code on U factor basis. This takes into account the whole assembly's performance including the thermal bridging of the rafters. Because of the thermal break from the exterior rigid, you can probably get away with R24 batts in the rafters with 3" of poyiso (or 3.5" of mineral wool) above.
There is a bit more loss through a roof in cold climates, but there is nothing special about it VS a wall. Your best $ for overall performance is making your roof and walls about the same R value.
Impermeable underlayment buys you nothing, whereas permeable allows for a bit of drying. Stock item at my local roof supplier so I use it by default.
Your rain screen should not connect up to the roof (this is a fire hazard is some areas). The rain screen should terminate at the top of the wall with either a vent or just capped. Capping it works almost as well as venting it, so don't go nuts on trying to detail this.
You can always angle the solar panels to increase the tilt a bit. There are racking designed specifically for this. There is very little efficiency gained in most cases by doing this, so run your array through PVWatts first to make sure it is worth the effort. Keeping them a bit above snow height does help in the winter but it doesn't sound like you have to space for it.
Thank you very much for the additional thoughts.
Malcolm, I've attached an image of my gable wall plan. The overhangs are pretty short here so I just have 2x4s on the flat, shimmed with a half inch plywood backer to match the insulation board thickness.
Akos, some really good points.
- Re running I&W down the wall - that was actually a mistake in the diagram. I was going to lap it over the wall WRB.
- No foam. We have two massive and aggressive colonies of ants in an adjacent abandoned lot.
- Reducing roof insulation is a thought. I wasn't sure about leaving space between the interior air barrier and the batts. I'm limited to minimum 9.25" based on structural considerations. One idea would be to replace the mineral wool with cellulose. That would reduce framed R to about 29, allowing me to cut exterior rigid to R20 (5"). Not sure if this would really change cost much. The Toprock DD is actually the least expensive part of this assembly. Batts and ice&water shield are where I'm getting hit. Cellulose dense pack means bringing in a contractor.
- Agreed on permeable underlayment.
- Rain screen: that was poorly worded. What I mean is that behind the rainscreen there is the mineral wool. Presumably the interstitium of the mineral wool would allow vapor transport. I'm just going to cap the rainscreen.
- Panel tilting: agreed it's not going to help much with efficiency. However, I am told that 1:12 pitch for a solar panel is too low for it to clean effectively when it rains. Increased racking angle might make good sense. The solar panels aren't really limited on height in the same way the roof is. Would have to price out the racking and it adds complexity to wind load calculations.
You can leave a space on the warm side of batts, you do not want a space on the cold side. With standard rafter spacing, you can use insulation wires to hold the fluffy batts up against the roof deck. Mineral wool is relatively self supporting and would stay in place, but I would still add some support.
Pick the minimum amount of fluffy and rigid to pass code, adding more is just not worth it.
Dense packing a small space is not worth it, the contractor will probably not even want to bid as it is not worth the setup/travel time.
Zero overhangs are the rage but they are rough on any painted siding. Overhangs are a buildings best friend, learn to love them.
Bryan,
Thanks for the sketch. You may have this covered, but what is always problematic with sleepers forming the overhang is the intersection between the gable walls and the eaves, which doesn't show up on sections of either.
If you have the sleepers extending out to form the overhang at the gable wall, what supports the overhang in the other direction? A plan view of the structure there is helpful.
How is the soffit supported at the exterior wall where it meets the insulation?
As I said, you may have thought all this through and I'm just belabouring p0ints you have already resolved, but from the drawings I don't see the two sections working together.
Akos,
Definitely love overhangs. The expanded view kind of makes it hard to see - there is actually a small 6" overhang here. I'm not sure how much more I could support with 2x4s on the flat and the architectural board may veto - everything new is supposed to be 'consistent' with what's in the neighborhood and virtually every house in the city (including the main house) has zero overhangs.
Malcolm,
Thanks for your attention to detail. I've attached what the roof framing looks like. Blocking plates are where the top plates of the walls are. The veranda is supported by columns to a big Glulam beam. The 2x4s will be hung from hangers, attached after the WRB and I&W shield go on. Will then do a little extra flashing around the hangers and then fit rigid insulation around them.
Eave is supported by the 2x4s on a flat with a long fascia board connected to the beam and to the framing of the main house by a separate blocking plate.
One thought is, I could support the rafters mid-span with a roof beam. The space is neatly split in half horizontally and vertically, so I could add a column there to support the beam. That would let me drop to 7 -1/4" rafters, reducing height and go with R30 MW, eliminating fiddling with insulation supports.
Bryan,
You've got it all sorted out. Looks good!
Malcolm,
Thank you very much! I really appreciate your help and that validation.
Akos,
Thank you again! I'm much more confident in this assembly now thanks to your assistance.