Exterior rigid foam details/concerns for roof

Finally am at the point of redoing my attached Ell roof on my 200+ year old colonial.
This is what I currently have.
Zone 5
Inside 3/4 inch pine (obviously very air leaky) cathedral ceiling, Behind that it appears to be a foil faced fiberglass. Prior owner did this some time in the 80’s. The sheathing is 1 x 10 running from peak to soffit ( again very leaky). There are 2 layers of asphalt shingles, then a 1 inch layer of Styrofoam insulation board with another layer of asphalt on top of that. Fun Fun!
At this point I am not opening up the ceiling inside. That will happen down the road.
From the exterior I had planned to strip everything down to the board sheathing. Was going to skin with 1/2 inch plywood, ice and water the whole thing to make an air barrier. Then put down 5 -6 inches of poly ISO on top of the ice and water. Then strap with 2 x4 from peak to soffit, throw sheathing on that, building paper, then install my enviro- shake shingles.
First question?
Dollar wise it would be much cheaper to skin the roof with Zip sheathing and tape seams. That would save me time and money. I just can’t get past the OSB thing. I am a plywood guy. Should I worry about that in a set up like this?
Second Question?
Can I get away without the venting above the rigid foam. I remember Dr. Joe stating it is a good idea. I am assuming if I stagger the rigid foam joints and tape each layer there should be no air pathways. Especially if I do the air barrier right under the insulation board.
Third Question?
This winter or next winter when I finally take down the interior ceiling to add insulation what would be the best option? I want the beams to remain exposed partly but now I would be concerned about the foam sandwich if I sprayed the underside of the sheathing?
Just looking for others opinions before I move forward. Feel free to poke holes in my plan if need be.
GBA Detail Library
A collection of one thousand construction details organized by climate and house part
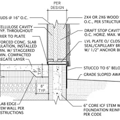
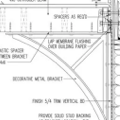
Replies
If you indeed have foil-faced fiberglass in the rafter bays you'll need to yard it out before putting an impermeable membrane such as Ice & Water Shield over it or you will have created a moisture trap. If you pop the ridge planks off you may be able to do that pretty easily, or it could be pretty tough, but go they must! (You may have to fabicate some sort of hook for reaching in and pulling out the batt fiberglass, and it's important to take most of the foil facer with it- just ripping the facers won't do.
It's then worth filling those cavities with cellulose before building up the rest, which is done more easily than demolishing and re-building the interior side. Howdedicated are you to the exposed beam-edge look?
Staggering the seams of the polyiso is important to manage the seasonal expansion/contraction of the foam to avoid thermal voids that extend from the exterior to the interior. Venting of the nailer deck is really optional, but know that in 20-30 years when it's time to re-roof it's likely that some of those exterior sheets will have to be replaced, since there is effectively zero drying capacity in either direction for the exterior OSB/ply nailer.
In a zone 5 climate with 5- 6" of polyiso and 3-6" of cellulose in the rafter bays the last 2-3" of polyiso will underperform during the winter when you need it the most, in fact making at least the uppermost 2" of foam EPS rather than polyiso would improve the average winter performance. When the average temperature through a polyiso layer drops below about 40F it begins to lose performance pretty quickly with falling temperture, whereas the performance of EPS increases. When it's 0F outside and the average temp through an outermost 2" of EPS is something like 20F, it will running about R9.5, whereas 2" of polyiso with an average temp of 25F would be barely R5. With the outer EPS keeping the polyiso a bit warmer, the polyiso will be running much closer to it's optimal performance temperature.
This is the approach Building Science Corporation endorses at the bottom of this analysis:
http://www.buildingscience.com/documents/information-sheets/info-502-temperature-dependent-r-value
Note where it states:
"Use a hybrid insulation approach – install cold temperature-tolerant insulation over top of the polyisocyanurate insulation to increase the mean temperature of the polyisocyanurate."
Thanks for the response Dana.
I had planned to install 2x4 nailers over the top of the rigid insulation. Then install the plywood decking for the shingles . So this would allow drying of the plywood with soffit and ridge vents installed. By removing the foil faced fiber glass the original decking could then dry to the interior. I like the idea of adding the top layers of EPS over the ISO. Had not thought of that. I was just planning to use more ISO to compensate for the losses when it gets really cold. Do you think skinning the original decking boards (once roof is stripped) with 1/2 plywood then covering in ice and water is better, worse, or equal to skinning with zip roof sheathing and taping the joints? As I mentioned I am a plywood guy. I guess if money was no object I would just go crazy with insulation on the exterior side and call it a day. I'm not looking to become a Passivehouse (personally I think it's greener to improve an existing structure rather than build a new one) I just want to make this 200+ year old house perform better than it has in the past but still need to keep the charm and character of the home.