Exterior rigid foam and re-siding project

I’m seeking input and opinion. I’m looking to re-side with the dread vinyl (need the low maintenance for my two story house). My 40 year old post and bean house has interior sheetrock, 3.5″ of fiberglass batt insulation with kraft paper, rough cut full 2×4 studs on 24″ centers, plywood sheathing (I think 5/8″), paper (a mix of Tyvek and felt), and cedar shingles. Shingles and paper will of course be removed, sheathing inspected in the process. I’m in zone 6.
My plan as of now is to put up 1″ uncoated EPS, 4×8 sheets held up temporarily with a minimum of cap nails. Seams will be taped. I will then use vertical furrings strips over the studs. These will be 1×3 or 1×4, full dimension so they are an actual 1″ thick. Will use the Headlock screws of suitable length (4.5″) to fasten the furring strips thru to the studs. Another layer of 1″ EPS will then be fitted in between the furring strips. This satisfies the vinyl folks” requirement for having a flat, supportive surface under the siding.
This compromises the R value a bit (having the thermal bridging of the furring strips replacing foam in some places), but I’m thinking will work. The EPS is rated at R 4.6 per inch at 0 degrees (4.2 at 75). I realize I could go with a full 2″ first then furring strips, then the fill in foam in between, but I’m thinking the added cost and nuisance of additional thickness is not needed. My house actually heats quite will now so I’m not desperate in that respect.
Any red flags with this plan? Any advice? Should I tape the joint on each side of the furring strips onto the foam? Seems like I should. I know there will be some fussing to make the walls flat and planer.
GBA Detail Library
A collection of one thousand construction details organized by climate and house part
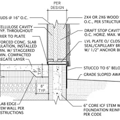
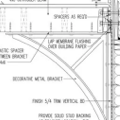
Replies
Howard,
I think that you can save a lot of labor and expense by eliminating the furring strips and Headlock screws. The following system will give you a more effective thermal barrier too. Here's what I did, also in zone 6:
-House wrap over sheathing for air sealing (mine was ship-lap boards).
-1" rigid foam (taped) over entire structure.
-Cut out window and door openings (assuming that new windows are to be installed).
-Picture-frame window and door openings with 1" boards (rough sawn full 1" boards or strips of 1" ply) over the first layer of foam. This will provide window attachment and trim base.
-Install second layer of 1" rigid foam over structure and cut around framed openings. Use a minimum of 3" cap nails to hold foam until siding.
-Install conventional flanged windows and flashing.
-Tape foam and/or apply WRB of house wrap, felt, your choice.
-Install vinyl siding with 3 1/8" GRK #8 cabinet screws. These screws are perfect for this application as their small diameter fits the siding slots and they will give you a full 1" penetration through your sheathing. They also have a pancake head, are strong, and won't rust.
Howard,
You need your rigid foam layer to have a minimum R-value of R-7.5. If you are willing to use a 1.5-inch-thick layer of foil-faced polyiso (which has a nominal R-value of R-9, and which will perform close to R-7.5 even at cold temperatures), you could get away without the furring strips.
Plenty of people install vinyl siding over 1.5-inch-thick rigid foam without furring strips.
Edward,
Thanks for responding with all that detail. Some food for thought. My contractor/neighbor, who I will be helping on this, mentioned a similar scenario as an option he has seen used. He was a bit uncomfortable, as it appears Martin is, It means the screws are all sort of cantilevered in holding up the vinyl siding. The siding people want at least a 2" penetration of screws/nails for warranty coverage, and your scenario has 1", although that could be fixed with longer screws I guess. There is also some concern about the soft support surface this provides for the siding brackets compared to the wood. Is this a valid concern?
Martin: I'm wanting to avoid the polyiso here, due both to its total lack of permeance and its reduced cold weather performance. Otherwise it would be the perfect solution. Does the rest of my scenario sound okay?
Can someone recommend a good tape for my needs here, -one other than Siga tapes which, while they seem excellent are also exceptionally expensive and I would need quite a bit.
Howard,
Consider that the furring strips you describe will be displacing insulation on more than 22% (16" OC) or 15% (24" OC) of your wall surface thereby creating a likely scenario for dew point to be reached within your walls. Consequently you need a minimum of 1 1/2" of continuous foam. As Martin stated, it is very common to nail vinyl over 1 1/2" foam. If you go with EPS you will need 2". In my case, I chose 2" of polyiso and took the added precaution of using screws instead of nails. I'm very comfortable with the choice.
I don't think that you should be concerned with holding up the siding over 1 1/2" or 2" foam sheathing. Vinyl siding is a very light skin. Wind damage, uncoupling, and nails loosening over time are common problems, not sagging from gravity. Closer fastener spacing is the best insurance against these risks. You can use nails (up to 4" long roofing nails can be sourced) but because of concerns with pull-out they need deeper penetration (2"). To get that penetration you will need to nail into the studs and in your case that's 24". Given your situation, I would be more comfortable with screws at 12", at least half of which will only be in the 5/8" plywood sheathing. That's OK as screw pull-out will not be an issue and the vertical load on each screw is very minimal, not requiring 2" penetration. Though they are not covered with foam, SIP homes with only 7/16" of fastener thickness, are a testament to the success of screws and ring-shank nails at closer spacing as opposed to penetration depth.
Finding appropriate screws is challenging. The shank diameter can't be so large as to prevent some horizontal movement in the siding slots, thus #8 is about the limit. Also, the heads need to be large and flat (washer or pancake), thus construction screws don't cut it. Lastly the screws need to be corrosion resistant. The 3 1/8" GRK screws I described where the longest screws I have found that meet these requirements.
Edward:
Thanks again. It sounds like you think the R loss is considerable and something I should avoid. I don't see how I can go with only 1.5" of foam with wanting to avoid polyiso. I'd be more inclined to go with 2" of EPS and go without the furring strips. But this presents the issue of no suitable screws. I'd be more comfortable using longer screws where they can enter the studs at least. It sounds like the vinyl people might not honor warranty in the case you are describing. I will check again on screws, but it sounds like you did the research.
In your case the R loss puts you in danger of condensation in your walls. Durability should be our first priority with thermal performance next, followed closely by cost considerations. I was limited in the thickness of sheathing due to the skimpy overhangs on my house. That prevented me from using the 3" or 4" I would have preferred. With that limitation in mind, the next best plan was to apply as much rigid foam as practical without the the large jump in cost for strapping. 2" of foam was the sweet-spot for our situation, providing a margin of error for condensation protection, reasonable R, a tolerable thickness for our eaves, a practical build-up for the screws available, and a very good cost/benefit.
Yes, I too had hoped to find longer screws that would suffice but could not find them. I had originally planned to use a first layer of 1 1/2" foam followed by a second layer of 3/4" foam to match standard 3/4" boards around the windows and doors. I dropped the original foam thickness of 2 1/4" to 2" (two layers of 1") because of the screw limitation. In the final analysis the 3 1/8" screws with a full 1" penetration worked out for the best as we would have had a hard time in knowing when and if the screws found the studs anyway. With closer screw spacing and 1" penetration into the board sheathing we are very confident.
To be honest, I didn't consider the warranty implications. If I have a problem, and if the vinyl company (big if) is willing to take any responsibility, I doubt if the installation will be the issue or found to be deficient.
Best of luck in finding the right answers for your project.
I should mention another scheme I considered: If you are concerned about your fasteners penetrating the studs consider a hybrid scheme. Over the 1 1/2" polyiso or 2" EPS foam board, apply the vinyl with 4" roofing nails (just shy of 2" penetration) into the studs at 24" OC. Follow with 3 1/8" screws into the 5/8" ply sheathing, between studs. Again, nails alone at 24" OC, particularly over foam would make me nervous.
Edward:
You mention using two layers of paper; directly over sheathing and then over foam again. Do you think this is necessary or was it the "extra mile". I was thinking of one layer over the rigid foam. Using furring strips there is the obvious attachment of paper to them. Without furring strips there is only the foam. How did you secure to the foam?
Also, did you have any difficulty making your walls flat, vertical and planer for the siding?
No, I'm not suggesting two layers of house wrap. Our project was a bit different in that the structural sheathing is ship-lap boards making the house challenging to air seal. A house wrap over the boards, sealed to the foundation and eaves (top plate) was chosen to initiate the air sealing process and provide weather protection until the siding could be completed. Since we needed to blow cellulose into the wall cavities after stripping away the old siding, the entire house had to be exposed at the onset. This made for a long period of weather exposure and the many open joints of the board sheathing would have been risky to expose to blowing rain. Our weather resistant barrier (WRB) was the outer surface of foil on the polyiso, taped and continuous with window flashing (flanged outies). Its a debatable issue if the taped skin of foam board is appropriate WRB (see other articles and blogs on gba). In your case It is likely that you can air seal the plywood sheathing with tape, foam, etc, and either apply your WRB over your foam or use the detailed foam surface if your EPS has a compatible facing, your choice. You are right that installing the WRB over foam, without strapping, can be tedious. You do have a wood surface to staple to around windows, doors and penetrations but nowhere else. Depending on how it ties in with your window flashing (new windows?) you could apply the WRB, one lap at a time, just ahead of the siding and use a combination of staples (at windows and doors), tape, and cap nails. This is how we used to apply felt, which is still an option for your WRB.
No problems getting a smooth surface with the foam board, provided the original substrate is. Even with the lower density EPS you should be able to keep it smooth. Remember you won't be drawing down the vinyl siding nails or screws tight. The siding has to be able to move on the nail-slots to accommodate thermal expansion/contraction. Regardless of the substrate, I recommend the thicker, premium vinyl with the fold at the nail flange. More rigid and less tendency to look wavy.
Thanks again Edward for the detail. I see why you did as you did. I agree that the taped EPS alone is not a good enough WRB, and is why I was asking about paper over the foam, and I can see the challenges of fastening. To complicate matters a bit more re windows, I have some newer ones that I would keep and reuse, and will replace some others. I'm still thinking about the innie/outie issues and pros and cons With outie some windows would have to be removed and reinstalled.
My walls are not that planer due to the rough cut lumber used and the inexperience of the builders (me and mine at the time), so I expect some fight with that.
Lastly, I wonder how you feel about the risk in my earlier idea, -the 1" of foam, taped, with 1" furring strips over the 24" oc studs, with 1" of foam filled in between. This solves a # of issues, but there is the loss of R. But I could use suitable screws thru the furring strips into the studs, and then the attachment of the vinyl would be to the well attached furring strips, and could be relatively short nails or screws.
In my view, the original scheme with 1" EPS covered by furring strips and inset foam should be off the table. Its not just an efficiency and comfort concern but one of durability. This scheme invites sub dew-point temperatures within your wall cavity. As I see it, the risk and added expense of this scheme is easily avoided. As Martin also attested, to adhere to this building science principle you really need a continuous layer of R7.5 foam, minimum. If you were looking at other siding types (wood, cement board), you would need to consider a rain-screen and strapping as well. Fortunately the vinyl siding you have chosen won't benefit from that so you can save the hassle and expense and apply the vinyl over a minimum of 1-1/2" of polyiso or 2" of EPS. Its doable and cost effective. In your case you have the sparse nailing interval provided by the 24" OC studs to deal with. Fortunately you have 5/8" plywood sheathing which is a good fastener substrate to apply additional screws to ensure a good siding job. Go for it.
Edward,
You mention 4" roofing nails in one of your posts above...do you have a good source for these? I have been looking at Menards and Home Depot (what we have for building centers around here) and they only show a maximum of 3".
Thanks
Grip Rite nail company makes hot dipped galvanized nails up to 4" long. Possibly other companies make them too. You won't find them in stock at most stores but they can be ordered.
http://www.grip-rite.com/us/en/fasteners/nails/roofing-nail
I should have added the precaution that 4" electro-plated "box" nails are commonly stocked at home stores but 4" roofing nails are not. Make sure to use "roofing" nails with the larger 7/16" head for vinyl siding. Box nails have a smaller head which could disengage from the slot in vinyl siding. Also, hot-dipped nails are more corrosion resistant than electro-plated.
Thank you Edward. I was looking exclusively at roofing nails...not normal box nails. Thanks for the clarification on hot-dipped vs. electro-plated...I was wondering about that.
Howard, in answer to your question about tape- use the 3m all weather tape. You can get it min Amazon. It is incredible and reasonably priced. I have used a lot of it on my OSB seams, and my foam seams. However, the tyvek tape works on the foam that I used as well. That is EPS.
Thanks Joe. That gives me two specific options that an experienced user is comfortable with. Its what I was looking for. Any thoughts about your use of the EPS? Was this type 2, and did you find the compressive strength adequate and durability adequate on your installation?
It is regular OSB and I think Hubert makes it. I used 7/16. I taped seams with the 3M and caulked stud bays and such. It is covered in Tyvek Drain Wrap and 2.5 inches of eps foam. I don't know about the compressive strength as that is above my pay grade, but I think it will do the trick. I tried Vycor tape and it has no stick. Use 3M all weather.
Grace doesn't stick to anything. Don't waste your money.
.
Gentlemen:
I have a couple of follow up questions. One scenario Edward describes for my situation is the hybrid of 4" nails at the 24" oc studs, and screws (3 1/8th") into the plywood in between. That makes for a lot of cold air entry, especially with the screws that are not fully embedded in wood but protrude thru to the fiberglass. How much of a hit is this energy wise? Or is it negligible?
If I decided to drill larger holes in the vinyl piece that hangs the siding (#8 screw, a size Edward says works, is .161", and the 4.5" inch screws are .191", so I would have to drill slightly larger than that), what are your thoughts about whether this is enough fastening without the screws at 12" in between the studs?
Lastly, I'm thinking of sticking with innie windows so as to leave alone the windows I plan to retain. Best practice is to flash the rough opening, and this would not possible if I left them as is. Can a good job of flashing still be done? Is there a description of how best to do this?
Howard,
Q. "One scenario Edward describes for my situation is the hybrid of 4" nails at the 24" oc studs, and screws (3 1/8th") into the plywood in between. That makes for a lot of cold air entry, especially with the screws that are not fully embedded in wood but protrude thru to the fiberglass. How much of a hit is this energy wise? Or is it negligible?"
A. I would say that you don't have to worry so much about this issue. These fasteners won't affect your air leakage rate very much at all, especially if you have exterior rigid foam.
Q. "If I decided to drill larger holes in the vinyl piece that hangs the siding..."
A. If you are talking about ordinary vinyl siding, those are slots, not holes -- and they are slots for a reason. The vinyl siding needs to be able to slide right and left to accommodate thermal expansion and contraction. Don't use any type of fastener that restricts this movement.
Q. "I'm thinking of sticking with innie windows so as to leave alone the windows I plan to retain. Best practice is to flash the rough opening, and this would not be possible if I left them as is. Can a good job of flashing still be done?"
A. In my opinion, the answer to this question depends on the width of your roof overhang, the distance of the window from the roof overhang, the amount of annual rainfall, and the wind exposure of the building.
Stingy overhangs, lots of rain, and lots of wind = bad. Wide roof overhangs, not much rain, and not much wind = good. In other words, it's a judgment call.
Thanks Martin. Rainfall is 41"/yr, just above natl avg. and much of it in snow. My overhangs are 16", -probably good for upstairs window on my 2 story house, less so for windows on gable ends (further from overhang) and 1st floor. Not sure about wind compared to "typical", but I guess this remains a judgment call. The foam would be 2" thick.
I'd value your opinion on the other question, if you have one, and that is about the adequacy of the fastening with the longer screws at the studs only and whether it is enough for the lightweight vinyl. Thanks for reminding me of the slot, and not a hole, so this would be contingent on a reasonable way to enlarge the slot to allow the panels to slide.
Howard,
I wouldn't hesitate to install half the screws to sheathing only, and half to the studs -- as long as there is a way to make sure that the vinyl siding can expand and contract (and slide right to left as needed).
On my build I have 2' overhangs at both eaves and rakes. I am finding that my windows hardly get wet at all, and even in a driving rain storm very little water is hitting them. I am so very glad I did the overhangs and can't recommend them enough. All the of entry ways on the house have covered porches as well. The doors are bone dry.
I'm looking for clarity on a couple of details in this post. I recently read elsewhere a comment from Martin that EPS cannot be taped and should instead be covered with housewrap such as Tyvek. I had asked about tape above and a type was suggested by Edward, although he may not have been focussed on EPS.
How would house wrap best be attached to the EPS? Cap nails?
I've also read conflicting information about EPS shrinkage, -from it not shrinking at all like other foams, to a 2% shrinkage. Is there an updated wisdom on these issues?
Howard,
I don't recall writing that EPS can't be taped. If I wrote that, I was mistaken. I'm sure that I have written that foil-faced polyiso is the easiest type of foam to tape. EPS can be taped; I would probably choose Siga Wigluv tape for that purpose.
Yes, housewrap is attached to the exterior of rigid foam with long cap nails.
Most of our information on foam shrinkage is anecdotal. Manufacturers have changed their manufacturing methods over the years, so the fact that older foams had shrinkage problems may not be useful information -- more modern types of rigid foam may have more or less shrinkage than older types of foam. If you are worried about foam shrinkage, install two layers of rigid foam with staggered seams.
Thanks again Martin. The post about the EPS was from 2012, but I don't have a ready way to identify it. Someone was pro/conning all 3 types of foam, with the EPS being much cheaper and you advised for that option. I'm not overly worried about shrinkage, and have not yet decided on one 2" layer or two 1" layer, knowing the two are better. But this will be a big boost in ease of heating my house, even with the penalty of some shrinkage.
BTW - is the tape redundant with Tyvek over the foam, or still worthwhile?
Howard, I am using recycled 2.5" EPS foam amd some of it is a tad grungy looking from leaves staining it and the elements. The 3M sticks like no tomorrow. Even Tyvek tape sticks to the cleaner stuff. Where there are any gaps we use can foam, like at corners or if there is a chunk missing that may have been damaged in transit. Then tape over that. At ten dollars per 4x8 sheet I feel happy. So go for it. And use the 3M. If you really want to overkill, add another layer of house wrap on the outside of it. Why not?
Joe:
I am planning on checking on recycled options, just haven't done so yet. I'm not fearful of using the stuff, and have a foam gun. At this point I do plan on Tyvek over the foam. Do you think I need to tape EPS seams if using the Tyvek? (I know it can't hurt but wonder if it is worth it). Or, is it better to tape the seams of the old plywood sheathing when I expose it?
It seems the level of instability of the EPS is uncertain, but I am thinking that expansion and buckling is just as worrisome as shrinking, but I guess it is what it is. All materials have some negatives it seems.
Howard,
You can tape every layer if you want; many people do. However, the tape cost can add up, so it's also OK to limit tape to the important layers.
In my opinion, plywood with taped seams makes a better (and more durable) air barrier than taped EPS, so I would certainly tape the plywood if I were you. You could save money by not taping the EPS.
Tyvek installation instructions require the use of Tyvek tape at the Tyvek seams. Not everyone does it, of course, but following the manufacturer's installation instructions is a code requirement.
Thanks Martin. This sounds like good, practical,Vermont type advice, and was my inclination so long as I wasn't doing anything sketchy (not that it would be the first time!)...