Exterior insulation retrofit when there’s no sheathing?

Our house was originally built by DIY solar enthusiasts, then later added on to by a clueless architect and builder who created all kinds of challenges. We’re looking at replacing a bunch of windows and siding, so we’d like to upgrade insulation at the same time. The construction is a little unconventional, so I’m interested in general ideas about how to proceed.
We’re in USDA Zone 4, or zone 6B via the map here, at about 5300 feet, in Montana where it’s overall very dry. Wildfire hazard is a significant consideration.
The old part of the house has 2×4 walls with R-11 cavity fiberglass and 1″ polyiso foam sheathing. There’s no plywood/osb sheathing; instead there’s diagonal bracing. There are polyethylene vapor barriers on the inside under the drywall, and on the outside on top of the polyiso. The siding is 6″ horizontal pine shiplap on ~1x stringers to space it off the foam. We’ve had issues with pest intrusion (mice) – they can burrow through the foam at the bottom edge. I think the outside polyethylene is somewhat degraded, and the polyiso isn’t glued to the framing, so there’s probably significant air intrusion at the bottom. With a thermal camera, I can see the studs from the inside, so there’s also some bridging.
I’m thinking that it would make sense to pull off the siding and stringers, add another inch or two of foam, add a textile rainscreen, and re-side with something fireproof. I’d rather not lose space on the adjacent deck, so metal seems like a good option. Presumably it would make sense to remove the poly sheet and tape the seams of the polyiso, or next new layer. But how can we deal with pest intrusion at the bottom edge, and improve air sealing between the framing and foam without a total redo?
I’m mindful of the tradeoffs between upgrading the envelope, and just adding efficient heat or solar. Given my so-so experience with efficient appliances, my bias is to put the money into the envelope. But what am I missing here? Any thoughts much appreciated. [Disclaimer: I asked this before in too many words to get an answer, so hoping this is a little more readable.]
GBA Detail Library
A collection of one thousand construction details organized by climate and house part
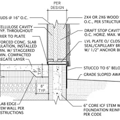
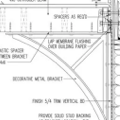
Replies
Tom,
That sounds like a good plan to me.
My preference is to use strapping for a rain-screen (both for the effectiveness, and because it make installing the siding and trim much easier), but tensile ones are certainly better than none.
I would suggest running a block of wood the same width as the foam around the house at the level of the sill plate. That excludes pests, and can be sealed to both the foundation and foam above. Metal siding has corrugations that are difficult to seal and still maintain a drainage plane at the bott0m. I like to use an L-shaped flashing made of perforated material there.
Tom,
You may consider using a self adhered WRB that would save the taping and also seal up any inconsistencies and not rely on the old polyiso for the primary AB. You could then tape the SA WRB to the foundation to complete the AB at that point. A great product is the Siga Fentrim. Malcom's idea of the block of wood is good and you could still use that with this option.
Definitely remove that poly on the outside...
From a dollars a cents point of view unless the current windows are literally falling apart replacing them will never save enough money in fuel costs to pay for the windows.
The same is true for the current R26 walls while not ideal they are also not terrible. The return on investment for walls over R26 is very long.
Does the current siding still keep the rain out of the walls or not? From a dollars a cents point of view it should remain until it fails.
From a green point of view using products for as long as possible is very green.
That is not to say there are not other reasons to upgrade like comfort or aesthetic.
When thinking about the fire risk you may want to consider skipping the foam for rockwool board.
Walta
The pine shiplap over furring strips is great for drying, but very high fire risk. If you are redoing the siding because it has failed and/or just because of the fire risk, go right ahead. Otherwise, as Walter said, your ROI will be very long on the additional insulation. If doing the change, metal siding over rigid rockwool insulation would be very good for both thermal performance and fire risk. Close the bottom with perforated metal to keep bugs and critters out.
Thanks for the helpful responses. I like the idea of blocking, taping and screening the bottom with metal. I'm not really familiar with WRBs but I'm guessing I could find a product with a combined barrier and rain screen? Or, if I go with rockwool, I guess I just need the barrier.
The siding is in OK condition - a coat of paint would suffice for maintenance. But, as you say, we're not enthusiastic about the fire risk. I'd sleep better with metal, stucco or fiber cement. Is there any evidence about ignition of materials under metal? Foam seems like a possible risk. Rockwool not (but more work). I was also wondering about something like Gutex fiberboard, which would be in between I assume.
The windows are, unfortunately, both aesthetically and mechanically poor. They're mostly original, from '79 to '86, and a lot are Norco casements, for which availability of seals and parts is problematic. I've tried refurbing a couple, but ran into subtle problems, like slight sagging of the inner frame that makes the far corner drag when opening/closing.
I think the builder was short, because a couple of big fixed glass modules are set too low - they block the view to the horizon for anyone over 5'10. It's kind of hilarious but infuriating after a while. That got me interested in the Litezones because they're basically frameless. If I can get a couple extra inches at the top, the problem will be solved without raising the headers, which would be an epic job.
Similar construction, 8,900' in Colorado. I removed the old 3/4" polyiso, the poly vapor barrier, much of the fiberglass cavity insulation (rodents & birds had trashed it). Replaced fiberglass batts, put on: 2" of Kingspan Kooltherm (R16), glued, foamed & taped; Obdyke HydroGap, nailers, and steel.
Regarding the LiteZones, the house came with IGUs framed directly in, and we didn't want to restrict views with fat frames--we went with the Marvin Essentials, which look great. They won't increase your viewable area as much as an IGU, but they will increase it some. And pay attention to visible light transmission--we were all excited about Alpen's R-10 windows until we saw them in person, 10% is just too dark.