Exterior insulation on above-grade basement wall

Hi everyone, my first post here: I have questions about installing continuous external insulation when replacing a 5×13 section of wall (the above-ground portion of an exterior basement wall, unheated, unfinished, laundry/mechanical room only). Zone 5
We just purchased this house, and had to have Professional IICRC S520 Mold Remediation done, through which all the basement drywall, insulation, and tar paper was removed (1960 house), and the siding under the tar paper had the mold scraped off it by the remediation company. But we’re going to be replacing that section of siding because it’s in bad shape from the exterior (weather, insects, etc.), and also because replacing WRB would need to be done from the outside anyway.
We finally passed the mold clearance, the mold is gone, but we want to prevent it from coming back. The mold inspector/environmental hygienist who did the clearance said that when replacing the siding/WRB on the basement laundry room, we should not have any insulation (even rigid foam) between the studs, or inside of the sheathing, and that if we have any insulation at all it needs to be outside the sheathing i.e. keep the basement unfinished, and the order from the studs out would be: sheathing, tyvek, rigid foam (we’re considering foamular XPS but open to suggestions), rainscreen, siding. However, the contractor said in decades of installing siding here in the Northern CA mountains, he’s never seen insulation outside of sheathing, always between the studs (which the mold inspector said to avoid). The contractor spoke briefly to the mold inspector and is open to doing it that way (i.e. continuous insulation on the outside) but would like to see more literature on that. The contractor recommended fiber-cement siding but is open to others. This is just a 5 feet by 13 foot section. Has anyone here ever installed foam-insulation on the outside of a building envelope (outside the studs/sheathing, just inside of the rainscreen/siding), and does anyone have a link to a resource that I can share with the contractor?
We are in the Northern California mountains, climate zone 5 (but on the edge of zone 3), with intermittent snow in the winter (and the snow falls off the roof right at that section of wall, and it’s not safe to shovel it away until it has all finished sliding off the roof). The overhang is only a foot (which we can’t afford to change). The new section of wall, with the exterior insulation, would have more layers than what’s above it, sol is likely to jut out beyond the wall above it, so we’ll likely need some flashing to address it, and it also means the thicker of layer we add, the less overhang the outer (fibercement) layer will get from the roof.
That room is a walk-out basement (not connected to living area), and is unheated but has the washer, dryer, and water heater in it, and we’ll put in a dehumidifier, so that will create some heat. We intend to never use it as living area, only laundry/mechanical, so plan to leave it unfinished and will not fill the stud-cavities with anything, so when doing laundry one would just see the back of the CDX sheathing for the exterior wall. The heating/ac in the house is ductless.
For XPS Foamular, it’s R5 for 1 inch and R10 for 2. Is that a good product for this, and which option is best for minimizing risk of mold, condensation, etc. The contractor is open to 1 inch of XPS which is R5, and I’m wondering if that’s enough to prevent sweating and condensation if there’s no other insulation (besides individually on the water-heater and the plumbing pipes)?
In this scenario, if we’re not insulating the inside, and it’s only for laundry, for purposes of mold avoidance, is it better to have 2 inches (R10), or one inch (R5) or none. We’re not insulating for comfort here, as no one is going to hang out in the laundry room. Just for prevention of mold/condensation due to the natural heat of dryer/waterheater/dehumidifier, and to prevent pipe-freezing (though we’ll put pipe insulation on the pipes themselves). Do the codes on minimum insulation apply to unfinished, undrywalled, uninhabited walk-out basements?
Also, what type of flashing tape is best for penetrations (there’s a ductless heatpump attached to the siding there, which we’ll need to have removed and put back), and there’s a plumbing vent and a dryer vent? And any tips on how the addition of insulation changes the flashing process.
The wall we’re replacing that leaked is horizon shiplap, and the wall above it that the contractor would need to attach and flash to, is board and batton wood siding and tar paper (currently the vertical section above and the shiplap basement siding below, an unflashed gap between them which is probably one of the sources of the water damage). We don’t have the budget to replace all the siding, just the siding in the section that had mold that was remediated (i.e. the basement siding). Also, the siding above that section looks fine according to the contractor and mold remediators.
Re: furring – between the insulation and the siding, the contractor would install vertical furring into which the cemenboard would be installed, and this will also create an airgap/rainscreen. We’re thinking of pre-painting the furring with Siloxane exterior wood water repellent sealer (we can’t use wood treated with strong chemicals due to chemical sensitivities), and the mold inspector said that would be good. https://www.homedepot.com/p/Eco-Advance-1-Gal-Clear-Penetrating-Siloxane-Exterior-Wood-Water-Repellent-Sealer-Concentrate-Ready-to-Use-EAWOD128PD/316770848
If we’re using furring, would it still be helpful to use a rainscreen product such as this: https://www.homedepot.com/p/MORTAIR-VENT-6mm-39-in-x-61-5-ft-Roll-Rain-Screen-MORTAIR-P-S/311223465 or is it just one or the other?
Also, the mold inspector said it’s fine to insulate the subfloor (there was some Rmax Thermasheath polyso there that was removed),. Since we’re not going to insulate the wall cavities of the basement, we want to restore the subfloor insulation since the area above that is living area. Is it better to use Rmax Thermasheath as before, or EPS, or something different, for the subfloor insulation?
Thanks!
GBA Detail Library
A collection of one thousand construction details organized by climate and house part
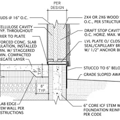
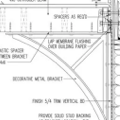
Replies
I included a picture of the outside of that wall. Here are pictures of the inside of the wall (post-remediation -- they finished remediating but haven't removed the containment yet). https://photos.app.goo.gl/SAJ1mmm1mDKRrwew5 (please let me know if the photos don't come through). Thanks!
It's a conservative industry and new techniques can be slow to reach less-populated areas, but exterior insulation has been an option in building codes and preferred among building scientists for at least 15 years, and a known option for at least 30 years. Your hygienist is correct that placing the insulation on the exterior of the framing is less likely to lead to microbial action than the traditional approach of relying solely on insulation between the studs. I disagree that 100% of the insulation needs to be on the exterior; depending on your climate, there are ratios of interior-t0-exterior insulation that are nearly as safe and that will keep your energy bills lower.
This article should answer many of your questions: https://www.greenbuildingadvisor.com/article/calculating-the-minimum-thickness-of-rigid-foam-sheathing.
Thanks! From that article, it sounds like for an unfinished above-ground basement wall with no insulation nor drywall on the inside, that R5 should be ok? Turns out we'll need to replace siding on the bottom of the other side of the house as well, but that side is on living areas with decades-old drywall and insulation (the traditional way) so perhaps on that side we won't do exterior insulation (because I don't know if that wall has 2x6, or other vapor barriers, etc.). Question: if, for the non-basement side, we're not doing external insulation (just plywood/tyvek, rainscreen, hardie), should we remove or not remove the tar paper? The contractor is just removing and replacing the siding up until the window there with hardie as there are some cracks in the lower part of the siding. https://photos.app.goo.gl/S6mJ7mjhTPwadim38
BTW, on that side, due to ground sloping from the road to the house, we're considering installing a ditch in between and in that french drain where the roof drops snow and water -- does that sound like a good location for that? Thanks!
An update: that contractor canceled doing the job (he asked me to send articles, and I did, but then he said it's too much "homework" and bailed). Probably for the best, because when I asked that the fiber-cement not be installed touching the ground, he said for fiber-cement ground contact is fine (which is not correct, as I confirmed with the manufacturer). Now that we're looking for another contractor, we don't have to do fiber-cement. What kind of siding is best for this scenario (exterior of basement wall, above-grade, with insulation on the outside). Thinking about metal now -- is there a way to install metal in this scenario that avoids condensation? Thanks!