Exterior insulation in Zone 5B

Hi All –
I’ve posted a few times on this forum in the past while I was researching building envelope for our new home. The home is 8700 square feet with a ton of windows, many quite large – 2 16′ double sliders, 6 9-10′ OXO, and then 50 or so other more ‘normal’ sized windows. Windows are all low-e 366 double pane marvin ultimates. Most windows are western exposure (mountain views). House is at 6200 feet in a relatively windy area in zip code 80138 (Zone 5b).
Our house is sheathed in regular zip with 2×6 exterior wall assemblies framed at 16″ OC. Trusses have ~12.5″ heels in most of the roof. Due to the large windows and some high walls we ended up with pretty thick jack studs around windows (3-6 studs in many places). In hindsight I might have used LVLs at least for the really thick jacks, but that ship has sailed.
Planned insulation strategy is R21-23 in the exterior walls via blown in blanket insulation, R-60 blown fiberglass in the attic, 3″ closed cell in rim joists, and a high level of attention to air sealing the structure.
I am very aware our house is far from energy efficient, lot’s of corners, complicated roofs, many windows, etc. That said, I’m still trying to value engineer where I can to do as good as I can within my tight budget in terms of building an energy efficient structure.
We’ve got trusses up and most of the structure sheathed at this point. So we’re moving along. Very exciting.
My question to the experts is regarding insulation (or any other friendly advice you could provide me that would be low cost, high return or common missteps).
1) Would a untaped R-4 layer of continuous EPS insulation over the taped zip sheathing to reduce thermal bridging be worth the investment? I believe some of the EPS/GPS unfaced foam has a perm rating of up to around 5. It would only cost me materials.
I’ve read contradictory articles about the requirements in my zone for CI R-Value. The charts say R7.7 in my zone to keep the dew point on the outside of the structure, but then I’ve also read about the studies up in canada which seems to demonstrate long term success with something closer to what I can achieve with my budget which would be around R4.
Biggest challenge is that windows are ordered and jambs would be short so I’d probably have to detail and ‘innie’ window assembly if I went this route.
I’m an owner builder for this house. I’m having a blast doing it and wish I had more time to do independent research, but time isn’t always on my side with a day job and GC’ing such a large project.
Thanks in advance, it’s been a true pleasure reading and learning on GBA thorughout my process!
Nik
GBA Detail Library
A collection of one thousand construction details organized by climate and house part
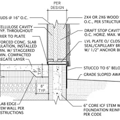
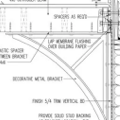
Replies
You didn't mention what your siding will be. Whatever it is, ANY continuous insulation underneath would be an improvement. An inch of EPS is pretty meagre, and isn't enough for dewpoint control, as you point out. To my mind any foam of any thickness up to 1.5" involves the same amount of work in terms of hanging it and trimming out, so why not go with the far superior 1.5" polyiso for a nominal R-10? The foam reclaimers on Craigslist will sell you a truckload of those panels at 30 cents on the dollar, putting you on equal footing with new 1" EPS. Or pick a zone of the house and go to 3", using that as your main living area during the cold months. Perhaps the entire fifth of an acre doesn't need to be fully conditioned year round.
Apologies - siding will be fiber cement.
My impression that foam up to 1" is labor cost neutral. I believe over 1" hardie/allura/nichiha would require furring strips and additional drainage plane.
I have considered reclaimed, but the diminished r value plus the reduced performance in cold climates like mine kept me moving toward EPS as a long term investment. I will explore again though...thank you for the reminder.
All that said, you echo the question I keep going back to. If ~1" of EPS is all I can do due to material/labor cost...is it worth it? "Worth it" to me isn't as much of a science as maybe it should be, but let's say it's perhaps a 20 year payback, but could also be weighted heavily if a comfort improvement was significant.
Back to the size of the house...it's actually two families living in the house w/ 1900 of those square feet being a second story apartment, and the rest split between the main floor and finished basement.
IMO, 1" of unfaced EPS will add moisture resilience (vs no foam) - it's much more vapor permeable than the Zip (almost no effect on outward drying) and does warm the sheathing some. This is hard to put a price on. Of course it also adds R value (this payback is easier to calculate). Don't expect to feel a difference in comfort.
I'd also air seal the interior side and use MemBrain. Test all air sealing with blower door tests.
The IRC will tell you exactly how much insulation you need on the exterior of your house. Here's one of our most commonly referenced articles, which should be helpful:
https://www.greenbuildingadvisor.com/article/calculating-the-minimum-thickness-of-rigid-foam-sheathing
And as far as the windows go, you're going to have to install extension jambs either way, either inside or outside. Here's an article on that topic:
https://www.greenbuildingadvisor.com/article/installing-windows-in-a-foam-sheathed-wall
The IRC will tell you that you can use no foam and, in many cases (eg >= 1 perm of foam (like EPS) or often vented cladding), little foam. You need to look elsewhere for what makes a moisture resilient wall.
About all one can accurately say here is that portions of an IRC table regarding vapor barriers are similar to some recommendations for a good performing wall design. It absolutely does not say "you need this much foam".
John,
You are right that the IRC doesn't require exterior foam, but it does gives minimum R-values for exterior foam if you plan to use it. That's where the table in Martin's article that I linked to above comes from. Check it out.
Brian
I have (very carefully) and the IRC doesn't say what you claim it does. For example, re-read it for the scenario of only 1" of unfaced EPS in zone 5. There are several ways this wall can be IRC and IBC compliant - without adding more foam. Eg, a) use a Class II interior vapor retarder or b) use vented cladding.