Exterior foam over sheathing with closed-cell spray foam in wall cavity

I live in toronto canada. I have an old farm house that I’ve been retro fitting with closed cell foam when the opportunity comes up. I will be residing the house this summer and would like to add exterior foam. will this cause a problem with trapped moisture? the current wall system is drywall, closed cell, shiplap, wood siding.
GBA Detail Library
A collection of one thousand construction details organized by climate and house part
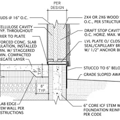
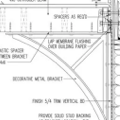
Replies
Hi Ontario boy.
It would probably be advantageous to keep the exterior somewhat vapor open to allow the sheathing to dry should it get wet. So, consider using a vapor-open water-resistive barrier, an exterior insulation with a higher perm rating like EPS or mineral wool, and a vented rainscreen assembly. You may find these articles helpful:
The Four Control Layers of a Wall
The Complicated Role of a Water-Resistive Barrier
All About Rainscreens
>"I’ve been retro fitting with closed cell foam when the opportunity comes up."
That's one of the LEAST green approaches possible, especially if it's a DIY foam kit, all of which use HFC245fa as the blowing agent. See:
https://materialspalette.org/wp-content/uploads/2018/08/CSMP-Insulation_090919-01.png
What's more, most if it's potential performance is squandered when installed between framing:
https://www.finehomebuilding.com/2017/07/10/closed-cell-foam-studs-waste
For any future retrofit opportunities, limit the closed cell foam to 1" (for air sealing & dew point control), and install compressed batts (or cellulose) for the remainder of the cavity. A 1"/R6 shot of closed cell foam is a bare minimum vapour barrier (per the NBC's definition), which still allows seasonal drying toward the interior.
Unfaced Type-II EPS is more than twice as vapor open as closed cell spray polyurethane at any given thickness. Installing an inch or less has very little potential for trapping moisture, but at 3" it's pretty much at the NBC's definition of a vapour barrier. Type-I EPS is even more permeable than Type-II but is also more fragile, and at 2" or thinner usually comes with impermeable facers.
The foam used was Waltite eco.
This is where my trouble lies. Changing the insulation cavity size is not doable. I also live in a climate that Will not allow for a 1-inch flash. So in retrofitting I chose to go with the highest R-value per inch option. I live in the country and my property is ran based on the burning of propane for heating and hot water. My attempt here is to burn less fossil fuel to heat. In the winter. The only room I have left to increase my insulation value is on the exterior of the home. Being separated by shiplap and wood siding from the spray foam on the interior. If you have a viable option for adding R-value to the exterior that is a green product. I would love to know about it.
The greenest R value on the exterior is recycled roofing insulation.
For new foam, your best bet is fiber faced roofing polyiso. It is still somewhat vapor permeable and generally the lowest cost / R value. If you limit thickness to between 2 - 3 inches, it is pretty easy to hit studs through the foam with the screws, fairly straight forward install.
If you are looking for foam free wall, you can always strap out the wall with 2x4/2x6 on edge install mineral wool bats, WRB, rain screen, siding.
For super high R value green retrofit, you can look at something like Larsen trusses with cellulose. Doesn't get much greener than that but it is a lot of work especially if you need to extend overhangs.
With expensive fuel, it would be worth while to put your house through BEopt and see where best to spend your efficiency improvement dollars. In most of Ontario, going much above an R25 wall assembly (not center of cavity but taking into account thermal bridging of the studs) is not worth it.