Exterior foam application and window details

Im in Phoenix about 6 months away from starting my build. I was thinking about upgrading my exterior foam from 1.5″ to 3″ EPS. The window detailing is where my question lies. I’ve read the articles here, but we will be using mostly EFIS for our exterior cladding (with some stone veneer). My thought was to nail the window to the exterior after the OSB and Tyvek stucco wrap just like you would without using foam. Then add the 3″ of EPS right up to the edge of the window and just add the EFIS to the 3″ return created. For the stone veneer we will just frame out the window the 3 inches. It adds a little thermal bridging but that should be OK for my Pretty Good Home. Do you see any issues with doing this installation?
I will be using Intus double casement windows which open to the interior so Im not concerned about clearance issues to the exterior.
Thank you for your opinions!
GBA Detail Library
A collection of one thousand construction details organized by climate and house part
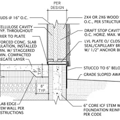
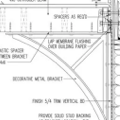
Replies
Here is a picture with a similar finished product
I'm glad someone in Arizona is aiming for a PGH.
From my limited time in AZ, it seems like the onslaught of bugs and critters is non-stop, and chemicals only slow them down. I wonder about foam being a home for ants and termites. Perhaps EFIS is a better cladding than some for this, but is it possible to put EFIS over mineral wool?
I don't understand why better insulated homes aren't more sought after here. We can have close to a 50 delta of internal to exterior temps in the summer. Even more for unconditioned attic spaces. Its not uncommon to have $600 dollar per month electric bills in the summer.
As for the critters, the use of bug screens is must at all slab penetrations and exterior cladding. Even then most people have quarterly sprayings.
A Google search (that included some hits from this website) shows that EIFS has long been used with mineral wood in commercial applications, normally because of the need for increased fire resistance.
I had to go for a period of time without AC during a hot spell. By opening and closing windows and shades I could make it into the afternoon before the room got uncomfortably warm, but with really warm attic and not enough insulation, it felt like the ceiling drywall was getting hot and then continuing to act as a radiant panel until late evening. If I thought I was going to be in the same place for a while, more attic insulation would be high on the list.
Jeffrey,
First of all, EIFS is almost always installed by a contractor specializing in EIFS. It isn't a homeowner-installed product -- mostly for liability reasons. (The EIFS failures in North Carolina cause a crisis in the insurance industry and the real estate industry, with many repercussions.)
You need to have your EIFS installed by a contractor who provides a warranty. Because of that need, you won't be able to specify the water-management and flashing details at your windows. Your EIFS contractor will be determining those details.
All of the facts I have summarized above are a result of the industry's transition from face-sealed EIFS to water-managed EIFS in the wake of the North Carolina crisis.
One more point: Most green builders try to avoid using XPS, because XPS is manufactured with a blowing agent that has a high global warming potential. Talk to your EIFS contractor about using EPS instead of XPS. (For more information on this issue, see Choosing Rigid Foam.)
Its standard practice to add EIFS to the lathe that is directly attached to the 1/2-3/4" foam board here in Phoenix. After watching 200 homes go up in my neighborhood I believe my detail is far superior to the flashing system they are improperly installing around the windows. They literally attach windows to the studs without sheathing and place flashing tape at that connection where 75% of the tape is flapping in the wind. Then they add the foam, lathe, stucco. The foam is their WRB, but its haphazardly installed. I guess the risk is worth it in our climate. Leaky windows are common complaints, but I haven't heard of any wall failures.
I hope I wouldn't have issues getting a contractor to comply with my detailing unless I am missing something fatal in my design. My home will be 100% OSB sheathed, taped (Siga), Tyvek Stucco wrap, taped and flashed, then foam. Like you said, I guess Im going to have to talk with the contractors. I'm weary of leaving that up to them as I do not have every sub completely vetted so my trust in some is less than ideal. I don't want to compromise something that takes very little extra effort just to make their process more cookie cutter.
Thanks sharing all these suggestions.