Exterior closed-cell spray foam to an existing house possibly a slightly different angle

First I apologize as this topic has literally been beat to death….. That said this is a slightly different twist that I cannot find any details on.
Existing house is a 1985 modified split entry. The wall assembly as it exists in the areas I have taken it apart are (from inside out): Paint of various kinds, drywall, foil faced kraft paper (independent of the fiberglass batts), fiberglass batts in a 2×6 wood wall (assuming R-19), fiber board sheathing, probably Tyvek and an old Masonite siding.
I’m looking to tear everything off down to the fiber board, add 1” x 2” strips of XPS over wall studs with a 1/2” plywood face to have a surface to attach siding, define cavity for spray foam, and achieve gap for rain screen. I would then add 2” closed cell spray foam around the entire building to air seal, insulate. The foam will also be the drainage plane.
Question:
1) Will the foil faced Kraft paper at the interior surface (assumed 0.5 perm rating or class 2 vapor retarder) be detrimental to the drying potential which is effectively cut in half or inside only rather than in or out?
2) What does the Minimum R-value of the CCSPF need to be (do you use R19 or the effective average R-value of the wall?
3) I’m looking for the windows to be “innie’s” or in the middle of the assembly and I’d really like a flashing detail. I cannot find a good one anywhere with this specific assembly. I will be replacing some or all of the windows, could use one with nail flange but am leaning toward a European window which do not use nail flanges.
4) anybody with any reason not to use Zola windows?
Thanks to anyone that gives any thought to this old topic.
GBA Detail Library
A collection of one thousand construction details organized by climate and house part
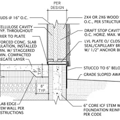
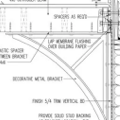
Replies
Lonney,
I'm a little lost. You are tearing everything off from the exterior (not the interior) -- right?
Leaving the existing fiberboard sheathing in place -- right?
Then what? It gets confusing.
Are these 1" x 2" strips of XPS rigid foam installed on the interior of the studs? Or on the exterior side of the fiberboard sheathing?
You plan to "define a cavity for spray foam," but you forgot to tell use the bounds of that cavity. Is that cavity between the studs? Or on the exterior side of your fiberboard sheathing?
You plan to "achieve a gap for a rainscreen." How will you do that? Are the 1" x 2" strips of XPS acting like vertical furring strips?
You write that "the foam will be the drainage plane." Huh? What foam?
Foil faced kraft is usually a class-I vapor retarder. Asphalted kraft (no foil) tests in the ~0.5 perm range, and foil is a LOT tighter than that, unless manufactured with perforations on a fine grid.
A 2 x 6 wall with R19s and fiberboard sheathing comes in at about R14-R15 whole wall, about R13 if the sheathing is 1/2" CDX or OSB. If you installed 5.5" of closed cell foam in the cavity instead of low density fiberglass it would still be less than R19.
If you left the R19s in place and added 1" of continuous ccSPF on the exterior of the fiberboard it would hit R19-R20 whole-wall. It's cheaper and greener to get there with continuous 1.5" of rigid EPS sheathing though.
Martin - Yes working from the exterior, removing all of the siding, wrap etc. down to the fiber board which will I'd like to leave in place. Yes the 1''x2''x8' strips of foam board will be vertical furring strips attached to the exterior face of the fiber board directly over the studs behind the fiber board to which the fiber board is attached. There will be a 1''x1/2'x8'' plywood face attached to the foam board as a nailing strips to attach siding to later. The idea is that the foam will make it easier to find the studs, allow for a continuous thermal break and stick away from the fiberboard 2.5'' which will allow 2'' for closed cell spray foam (what I meant by cavity) and 1/2'' spacing for the rain screen.
Reasoning behind Closed Cell Spray Foam - Of the few people I've spoken to I've heard some disappointment in the air flow reduction achieved in the process of adding rigid exterior insulation. Certainly, this can be solved with the right peel and stick or spray applied air barrier, and good attention to detail combined with testing. That said when your adding a peel and stick, spray applied air barrier, WRB and/or various layers of insulation board you have to be drastically limiting drying potential to the outside anyway unless your using an air permeable insulation board like rock-wool. I know it depends on the perm ratings, but I'd also say that perm ratings are not tested in an assembly where there are a number of different products sandwiched together and the exposure to air/airflow and temperatures are drastically altered. There would be an argument that the end perm rating of some of these assemblies could be much different than expected. That and there are how many trips around the house installing all of the different layers and what are the costs for the products and the labor. There is the shrinkage of foam board products. The actual R-values vary depending on actual conditions......... When the dust settles it seems like there could be some significant advantages to just spray foaming the entire exterior wall. Superior air barrier. One product that is the air barrier, thermal barrier, and drainage plain all in one. Yes there are the foam furring strips, but those can be broken up a bit to prevent air leakage along a sheathing seam or what ever. Plus I work for an insulation company that is willing to go and spray foam on an exterior wall but does not really want to install exterior foam board.
Dorsett / vapor retarders/barriers - Certainly a primary reason for the post was to determine the risks with the existing interior foil faced kraft paper. I had been under the impression that foil faced batts were class 2 vapor retarders and this was the risk I was primarily trying to assess. I knew the foil facing on foam boards had very low perm ratings. I revisited this again do to Dorsetts comment. When I looked up individual manufacturers foil faced batt products available today it looks like half of them are Class II and half Class I vapor retarders. I've had zero luck trying to identify the existing product and/or trying to find spec sheets for products that would have been common in the 80's. Honestly it was more work than it should have been finding the Perm ratings for todays products.
ICAA - http://www.insulate.org/tb6.pdf
- OC eco touch pure fiber (.5 perm rating) - http://www.homedepot.com/catalog/pdfImages/16/1625cbef-b3ad-46c4-8799-76d808649731.pdf
-Knauf Eco Batt (.4-.5 perm rating depending on facing type) - http://www.knaufinsulation.us/en/content/ecobatt-insulation
- Johns Manville - JM FSK-25 FACED BATTS - (.05 Perm rating) http://www.jm.com/content/dam/jm/global/en/building-insulation/Files/BI%20Data%20Sheets/Resi%20and%20Commercial/BID-0147_FSK25_BioBinder_DS.pdf
Certainteed certa pro fsk 25 (.02 Perm Rating) - http://www.certainteed.com/resources/3025033.pdf
Questions:
Assuming it is a class II vapor retarder does this limit drying potential enough to avoid a vapor closed exterior product? and/or If it's a class I vapor retarder is it ridiculous to think that if you put enough insulation on the exterior (more than 2'' CCSPF or other) so the interior sheathing will never gets cold enough to provide a condensing surface and therefor it doesn't matter?
Has there been any research on actual perm ratings for assemblies that have multiple layers of different products and drastically altered exposure to the energy (heat, airflow, etc) necessary for drying?
In the end I believe that continuous exterior insulation is absolutely necessary, and want to be one of the first to aggressively push such measures on the existing housing stock in the area but I'm not interested in being wrong on my own house or those of clients. That and I'm also a believer that if your interested in doing a little why not do more. Thus the reason for the questions.
Or maybe... probably it's best to just add a little insulation with fewer, very vapor open assemblies such as that recommended by Dorsett with a thin layer of EPS and some krinkle tyvek and some basic air sealing. Not saying that is a bad thing.
Lonney,
I'm still having trouble visualizing this. You are creating furring strips made out of 1" by 2" strips of rigid foam. These foam furring strips are capped by strips of 1/2" plywood (1 inch wide strips).
You claim that this arrangement will create cavities that are 2.5 inches deep. But that's only possible if you orient the rigid foam on edge, with the 1-inch dimension touching the existing fiberboard sheathing, so that these foam strips stick out 2 inches from the fiberboard. The foam furring strips attain the 2.5-inch depth once they are capped by the 1/2-inch plywood strips.
How are you going to assemble this? There narrow strips of foam sound quite precarious. Will you use cap nails? Foam-compatible adhesive?
Why are the foam strips so narrow?
"I know it depends on the perm ratings, but I'd also say that perm ratings are not tested in an assembly where there are a number of different products sandwiched together and the exposure to air/airflow and temperatures are drastically altered."
It sounds like you are conflating air permeance with vapor permeance, which are not the same thing. Vapor permeance is only about vapor diffusion through a material, not air leakage through the material (or air leakage into the assembly.) Orders of magnitude more moisture is transported by air leaks than by vapor diffusion, even through fairly high permeance materials. But you can't guarantee that the air leakage it also a drying path. Your goal here is (or should be) to make the exterior sheathing layer as air tight as possible, independent of the vapor permeance.
Without data sheets for the foil facers, assume that it's a Class-I vapor retarder. Even half-mil (0.0005") aluminum foil is well into Class-I vapor retardency, not Class-II. Any foil facer that is over 0.1 perms (the high end of class-I) has to be intentionally manufactured with perforations to raise it that high. It would be silly to assume that a random unspecified foil facer is a Class-II vapor retarder. The only product on your short list that isn't a powerful Class-I vapor retarder is the EcoTouch at 0.5 perms maximum. (And I'm wondering if that isn't a typo, and that it's really 0.05 perms, which is Class-I.) Your description of the Knauf FSK and foil facers has the decimal point in the wrong place- it's .04 - .05, not 0.4-and 0.5.
If you don't have or aren't planning sufficient exterior R to keep the sheathing above the average wintertime dew point of the interior air (or as spelled out in chapter 8 of the IRC for Class-III interior vapor retarders) it's advisable to keep the vapor permeance of the exterior layers above 1 perm. Unfaced Type-II (1.5lbs nominal density) EPS is still above 1 perm @ 1.5" thickness, which meets your goals. Closed cell polyurethane may or may not be above 1 perm @ 1"- it depends on which product, the actual density, and the actual mix on the day it's installed. At 2" most closed cell foam is well below 1 perm.
A taping all the seams of the fiberboard and applying a vapor permeable spray-on WRB should work, over which you can put 1-2" of unfaced EPS. If using a lower permeance foam making sure there is sufficient R for dew point control for any incidental air leakage from the conditioned interior would be advisable.
At this point I've abandoned the idea of closed cell foam for this project. I've decided there is too much risk unless I wanted to do 3''+ and I don't want to do that. I'm still interested in details for this approach with a wall that does not have an interior vapor barrier. I would like window details but I'm getting closer on that front as well with the decision to go with a European style window with no nailing flange and some of the great details that Zola and Hammer and Hand have put up.
Martin - The foam strips capped with plywood only serve the purpose of providing a flat surface to fasten the siding and achieve the gap for the rain screen. They potentially add the benefit of showing where the studs of the original wall for whatever fastening needs. Essentially it is a furring strip that is a better thermal break. I was expecting to fasten them with a long GRK screw similar to what would be used for fastening thick layers of rigid foam but hadn't made any final decisions there and would be open to suggestions.
Dana - Thank you for the explanations, but I am aware that air flow is different than diffusion. I understand air flow well. I will admit that diffusion is a little tougher, but I have a decent handle on that as well. Perhaps I was conflating a bit, but I still have a really hard time accepting that the flow of vapor through multiple layers of different materials with different individual perm ratings is as simple as making sure that their individual perm ratings fall in Class 2(maybe 3) or vapor open. I feel they have to perform differently when piled on top of each other especially when air flow is greatly reduced. To be clear restricting air flow as much as possible is certainly the prime objective of this. Which is precisely my concern. Initially I thought I had a class 2 vapor retarder and was hearing that would be sufficient for drying to the interior if necessary. Double checking this was one of the primary reasons I came here; to find if class 2 was enough for proper drying with the assembly.
EPS foam was initially plan A. I thought of the spray foam idea due to all the steps necessary in getting a good air seal, however many layers of foam board, WRB etc. etc..... Thought well I know Closed cell foam reasonably well and it seems easier and potentially better if you have a competent foam technician, BUT it simply doesn't make sense with the foil facing. BACK TO PLAN A. I'm still a little concerned about the permeability and permeance of the assembly when there is 2-4'' of foam and peel and sticks and.........?
That said I haven't abandoned the idea for other customers that do not have the interior vapor barrier.
All of this said when adding exterior EPS and keeping the assembly vapor open to the outside does one still need to follow the rule for ratio of exterior insulation to cavity insulation? It seems that if drying is minimally changed any amount of exterior foam would improve the situation by warming to some degree the interior surface temperature of the exterior sheathing reducing the annual time it is risks being a condensing surface, and providing a better thermal break for the wall.?
Any recommendations on a good Vapor open peel and stick or spray applied air/weather barrier would be appreciated, but I'm sure there is a lot of information on this on other posts or sites. I haven't looked yet.