Existing cedar sided walls nailed to studs without building paper

We’re remodeling a garage into a studio and want to “seal” (while allowing breathing) the exterior walls and then insulate. The siding is in pretty good shape (a few cracks) and is nailed directly to the studs. What is best for sealing the cracks? And can we insulate without building paper? Is there a way to install a wrap of some sort without removing the siding?
Thanks.
GBA Detail Library
A collection of one thousand construction details organized by climate and house part
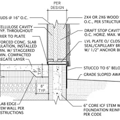
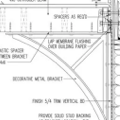
Replies
If there is no sheathing, what is creating shear (racking) resistance?
Some might suggest open-cell spray foam to air seal and insulate, but that would not allow the siding the breathe as it should.
I would recommend removing and salvaging the existing siding, installing plywood (not OSB) sheathing, 15# felt and re-installing the siding. Then you can insulate with dense-pack borate-treated cellulose (breathable, fire-retardant, insect and rodent resistant), though depending on your climate zone you may have to thicken the walls with cross-hatching in order to meet minimum R-value standards. Finish with air-tight drywall and latex vapor retarder primer.
Based on your goals I would consider- strips of cedar breather (or sim) on the back of the siding (between studs), then a thin layer of rigid insulation to start the thermal and keep the 'breather' open, then fill the rest with closed cell foam (higher r-value per inch since you have limited depth, plus added rigidity). Of course as Robert mentioned, it will all depend on your climate zone R-value standards and vapor barrier req's. You should also check with the foam mfg'r to make sure it's expansion won't crush the 'breather' material. I'm just assuming the racking resistance is handled by let-in bracing since it's standing....if not and you've just been lucky all this time....you could sheath the inside with plywood- assuming your local code official is OK with it. It's hard to say if all of this would be cheaper or easier than Robert's method.
Thank you both for your helpful responses.
The garage was built maybe in the 30's or even earlier without a foundation. In 1992 a big windstorm (60 mph gusts) blew the heavy old barn doors that were facing the wind all over the yard and also moved the bottom of one of the bearing walls (end to the wind) about 2 feet outside the garage perimeter so that the wall appeared to be held up by the top plate connection with the roof. (The roof structure is trusses). We had the wall put back in place and the building jacked up so a foundation could be put under it. Most of the cedar siding survived this, not to mention the structure itself...we have definitely been lucky all this time.
However, no one has spent much time out there for the most part and since we are changing that, I'm sure it would be a good idea to install sheathing for the shear factor, and thank you both for pointing this out. I'm afraid the siding won't make it through a removal process though, so I'm thinking of trying Hunter's solution to save the siding. I checked the building code (Seattle) and plywood is allowed for interior walls.
Julie,
You said that you poured a foundation under the building. What were the original bearing walls resting on? What was used to fasten the walls to the new concrete foundation? OSB/plywood sheathing will help for racking, but do little for uplift, sliding, and overturning forces.
Sounds like you may also invest in some Simpson anchors to fasten the bottom plate to the foundation.
Hi Brett,
I think the bearing walls were originally just set down onto gravel, though there may have been a few concrete blocks under them too. After the wind storm, the walls were bolted to the new foundation after the building was lowered back down. Thanks.