Existing brick over 1″ foil-faced EPS in zone 5A: Plans for air-sealing & re-insulating from the interior

Thank you for the opportunity to benefit from the GBA community’s experience. My project is a 1950s ranch with 2×4 walls sheathed with horizontal 1×6 and 15# felt. An addition was added in 1985 with 2×4 walls sheathed with 1″ EPS foam with steel let-in bracing. No wood sheathing. The foam has a mechanically-perforated aluminum foil on a thin cardboard facer. The same EPS foam was applied to the entire original structure over the felt and 1×6 at the time of the addition, then T-111 wood siding over all. EPS seams have overlapping facer-flanges but were not taped. The T-111 was stripped in 2007, the entire structure wrapped in thoroughly-taped Tyvek and bricked.
Submitted for your criticism and comments is the proposed air-sealing and insulating plan intended to be implemented entirely from the interior:
Original 1950 Structure Walls: Roll on a silica-based fluid-applied membrane air barrier (Sto Gold Coat, >10 perms for two 10-mil coats) onto the 1×6 to air seal the many tiny cracks and splits, then embed vapor-open fabric (Sto Fabric) over the larger gaps between the 1x6s. Ring each stud bay with a 3/8″ fillet of low voc silyl-terminated polyether (BASF NP150) to air-seal the 1×6 to the studs. Install foaming shells around electrical boxes (BoxShells). Insulate with unfaced (to enable full 6-sided cavity contact and allow use of drywall adhesive) R-15 fiberglass batts. Glue and screw drywall (Denarco gaskets or Dow drywall gasket in a can). Prime with vapor retarder primer (0.6 perm, Sherwin Williams). Inject latex foam into BoxShells.
1985 Addition Walls: No Sto Gold Coat. Air seal by ringing each stud bay with ProClima Contega HF sealant (adheres well to EPS and has low modulus to tolerate the expansion coefficient difference between wood and EPS). Seal electrical, insulate and drywall per above.
1985 Addition Wall with Shower: Two stud bays on a NW wall will receive a solid surface (Swanstone) shower cladding over paperless gypsum tile backer board (Denshield) and will not be able to dry inward. These bays will sealed with Contega HF, and then receive 3-1/2″ of tightly-fitted cut-and-cobble XPS foam to mitigate inward vapor drive and to increase the shower wall temperature for comfort. The XPS will be air-sealed by taping to the face of the studs using ProClima Vana tape to which drywall adhesive will adhere.
1.) I did not see any difference in the total perms calculation for all the materials in the 1×6 walls with and without Sto Gold coat. It appears to be dominated by the lower perm materials. Am I overlooking a downside to the Sto Gold Coat?
2.) Is this air sealing and insulating plan acceptable in my climate zone for these three example walls? I prefer to stay with a DIY approach using R-15 fiberglass batts for their workability and ability to easily cut down larger sizes to fit old, irregular stud bays that are sometimes up to 17″ wide.
3.) Does anyone have any experience with the Dow drywall gasket in a can versus the Denarco gaskets for air-tight drywall?
Thank you.
GBA Detail Library
A collection of one thousand construction details organized by climate and house part
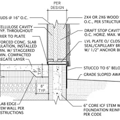
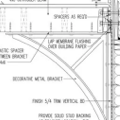
Replies
"air seal" should always be accompanied by "test with blower door". Good cold side air sealing and poor warm side air sealing can cause a problem.
I'd build to the "Side bar 2" recommendations for vapor retarders found below. Within the recommendations, I'd go as permeable as is reasonably possible.
https://www.buildingscience.com/documents/digests/bsd-106-understanding-vapor-barriers
Thank you Jon for your reply. I reviewed the reference you linked. I believe the vapor retarder paint at 0.6 perms meets the class II vapor retarder requirement. Seems to come down to the accuracy of the perm calculations which I am attaching to this reply for review. I would appreciate it if you could sanity check the perm values used in the calculations.
A blower door test is planned after exterior air sealing and a second test after the airtight drywall is installed. I hope to achieve good warm side sealing with the drywall gaskets. I am not aware of a better method to achieve air-tight drywall than drywall gaskets. Not interested in the Tremco acoustical sealant due to its high VOC property. Thanks again for your thoughtful response.
Use wet perms when calculating external perms.
While paint is also "smart", a smart membrane would probably improve overall moisture performance.
Perforated foil is a good counter example to "holes in a vapor barrier have little effect".
The perm rating of the sheathing assembly increased to 0.7 using wet perms, but still falls in the 0.1 to 1.0 perm range designated acceptable (in the BSC reference that you linked ) for a class 2 vapor retarder, such as the Sherwin Williams primer at 0.6 perms.
Karagiozis and Lstiburek found a downside to the smart vapor retarder with brick cladding on page 8 in the report linked below, stating "For initial high construction moisture, better performance in the short term is achieved by using high permeance vapor retarders, i.e., 8 perm coating or smart vapor retarder but worst in the long term.
https://web.ornl.gov/sci/buildings/conf-archive/2007%20B10%20papers/143_Karagiozis.pdf
My take is that the data seem to indicate the subject walls will be ok with the 0.6 perm vapor retarder primer and that for an older, well-dried structure without an initial high construction moisture residual, perhaps more appropriate than a smart vapor retarder.
Additionally, there are two important advantages from my point of view: 1) insulation efficacy via improved precision cutting, splitting and fitting around obstructions for 6-sided cavity contact is possible with unfaced fiberglass batts and 2) long term drywall durability is achieved when the stud faces are available for drywall adhesive.
Your assistance is appreciated. Any and all comments and criticism are welcome.
1. difference in total wall vapor permeability with/without the Sto: Sure, the impact of one layer if you are evaluating TOTAL vapor movement from one side of the wall to the other is going to be small.
2. I agree with Jon R - best way to evaluate your air sealing plan is by performance testing: blowe door.
3. No experience comparing these.
Jon R - I am not sure what you mean when you say "paint is also smart?" Do you mean that paint has variable vapor permeability at different moisture contents? This is news to me.
Peter
Yes, paint is significantly smart (but a smart membrane is better). See figure 10 below. Not clear is if different paints show more/less of this beneficial effect.
https://www.buildingscience.com/documents/building-science-insights/bsi-099-its-all-relative
Hi Jon -
that is a great article that I had not read--thanks for that. But in Figure 10, that sorption isotherm is NOT for paint, but for the combined paint and GWB; not the same as assigning variable vapor permeability to just the paint.
Peter
Tech support at Sto was opposed to the use as I described stating I would significantly impede the ability of the wall to dry. My calculations didn't show that to be the case, but I needed to check my thinking.
Blower door testing will be performed.
My biggest concern is using the vapor retarder primer instead of kraft facing or a smart vapor retarder, but there are advantages, in my opinion, from an overall construction point of view. These are: 1) better insulation efficacy via improved precision cutting, splitting and fitting around obstructions for 6-sided cavity contact is possible with unfaced fiberglass batts and 2) better long term drywall durability may be possible when the stud faces are available for drywall attachment with adhesive and screws.
Do you see any downside to using the 0.6 perm vapor retarder primer?
As I mentioned to Jon R. in a earlier post, Karagiozis and Lstiburek found a downside to the smart vapor retarder with brick cladding in zone 5 on page 8 in the report linked below, stating:
"For initial high construction moisture, better performance in the short term is achieved by using high permeance vapor retarders, i.e., 8 perm coating or smart vapor retarder but worst in the long term.
This is an old house. All the studs, sheathing, and flooring test at less than 15% MC.
https://web.ornl.gov/sci/buildings/conf-archive/2007%20B10%20papers/143_Karagiozis.pdf
Thanks for your response Peter. Any additional comments and criticism are appreciated.
Hard to tell how .6 perm paint would compare since they didn't include it.
Note that they also write:
"Smart vapor retarders and kraft paper perform reasonably well when used in this type of wall system. "
" Brick veneer wall systems ... The smart vapor retarder was found to have a strong positive effect on the moisture performance of the walls in zone 5".
"The benefit of the smart vapor retarder (WVP permeance of less than 1 perm at low relative humidities [below 50%] and approximately 50 perm at high relative humidities), followed by the paint coating, then the kraft paper and finally the 6 mil poly case is obvious."
Figure 9 shows SVR being best.
My guess - the paragraph you quoted was poorly written and a nylon smart retarder is best.
Figure 6 seems to support the statement that the SVR (MemBrain) may be "worst in the long term". For wall initial conditions of low 16% MC and high interior initial conditions, a cautionary yellow square is indicated.
This is the case of a strong wetting condition for an unvented brick wall. It has been my experience that the venting gap in most "vented" brick walls is significantly obscured with mortar, making them effectively "unvented".
The permeance curves in Figure 10 of the "Relative" reference are notional. Certainteed's specification for MemBrain shows a wet cup perm rating of 15. Karagiozis states he modeled MemBrain in his "Scientific Analysis" reference and that "the vapor retarder data were measured by ORNL".
His model for the zone 5, MemBrain, unvented brick case with initial conditions of high interior relative humidity (only sample data for Atlanta is shown, Fig. 4) and for low wall MC (16%) resulted in a moisture accumulation of 18-25%.
"In the simulated cases, interior moisture generation rates simulating a family of four were used to develop the indoor relative humidity profiles."
Are these data telling us that for old dry walls without residual construction moisture and with high interior humidity levels, e.g. SE Michigan in the summer without dehumidification, the permeance of MemBrain can be too great?
Thank you.
This one sounds closest to your situation. The low perms of EPS on the exterior is a big change - you should probably ignore all the non-EPS statements
"In general, the application of exterior foam sheathing (1 in.) reduced the amount of moisture accumulation for the walls investigated in the simulation parametric. Walls with higher water vapor permeance (less resistance to vapor flow), i.e. 8 perm and SVR performed the best."