Evaluating HVAC schemes for retrofit?

I’ve been planning a major retrofit to our 100 year old farmhouse and its coming down to crunch time. No surprise here, but the HVAC system has been the most challenging. I’m hoping that the astute staff and readers of GBA can offer fresh critiques and/or alternatives to the proposed scheme.
Here’s the background: Zone 6, Wisconsin; 1,950 sq. ft., two story, balloon frame; foundation is basement (not living space but within envelope) with jet-creted stone walls, concrete floor, no vapor barrier, no bulk leakage; ventilated attic, no flooring; mostly open floor plan on first floor, 3 bedrooms and bath on 2nd; original forced air ducting with supplies to all rooms but returns only on first floor; current furnace is 90K Carrier high efficiency, LP, single speed fan, 18 years old, also wood stove in living room; spot exhaust in two baths and range hood; summertime use of dehumidifier in basement; no AC now but wish to add for occasional hot spells.
Proposed structure improvements: Strip off exterior down to board sheathing, add new ARB, 2″ foam sheathing (limited by meager overhang), siding, windows, wall cavity insulation, attic sealing and insulation; some interior renovation but not gutting most rooms.
Performance expectations: R 26 walls; R 60 ceiling; R 15 foundation walls down to 3′ below grade; R 3.5 windows (best double pane, solar tuned); infiltration target of 3 ACH50; heating/cooling load calcs not yet computed.
Challenges: I just learned that basement radon level is 20 pCi/L and standard sub-floor mitigation will be very difficult, possibly ineffective. Prior to this discovery I was considering a pair of Lunos E2 ventilators on both the first and second floors. We are now considering an HRV or ERV to provide ventilation for the house along with diluting/purging radon and humidity from the basement. Note too that it will be extremely difficult to add/modify the current in-wall ducting, particularly for the second floor (i.e. a return run seems unlikely).
The proposed HVAC system includes: replacing furnace with a smaller, modulating unit (size based on load calcs) with ECM fan; Interconnect an HRV or ERV to air handler with supplemental ducting to ventilate basement (more basement exhaust than supply); AC to be provided by one mini-split in 2nd floor hallway over stair-well; retain spot ventilation; retain small wood stove in living room for ambiance and occasional supplemental heat. My HVAC contractor of choice handles Trane, Mitsubishi, Venmar and Ultimate-Air.
Thanks in advance for your comments;
Ed
GBA Detail Library
A collection of one thousand construction details organized by climate and house part
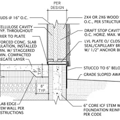
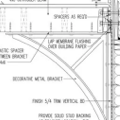
Replies
Edward,
You say that you plan to install a new ARB. I have no idea what an ARB is.
You plan to install 2 inches of exterior rigid foam. You didn't tell us what type of rigid foam you plan to install, but it will have an R-value of between R-8 and R-10. (If you install polyiso, it will have a higher nominal R-value -- but you have to de-rate the performance of the polyiso in cold weather, so 2 inches of polyiso will perform at R-9 or R-10.)
That amount of rigid foam will work if you have 2x4 walls, but not if you have 2x6 walls. For more information on this issue, see Calculating the Minimum Thickness of Rigid Foam Sheathing.
ARB = my abbreviation for air resistant barrier. Exterior foam sheathing = Polyiso over 2 X 4 walls with cellulose.
Edward,
As long as you remember to include a WRB (my abbreviation for a water-resistant barrier), as well as furring strips to create a ventilated rainscreen gap between your siding and your rigid foam, your wall plan will work.
Martin- I suspect "ARB" was a typo for "WRB", non?
A vapor barrier on the slab and sub-grade walls will very likely cut your radon levels by 3/4, after which a Lunos in the basement may very will bring it the rest of the way home. If it's a thin rat-slab and easy digging it may be worth demo-ing the slab, digging down 6-8" and installing a radon vent system surrounded by 3" of washed gravel with 2" of EPS on top of that with a poly or EPDM vapor barrier under a new slab.
If it's a thick slab or on bedrock, if there's enough head room 2" of EPS and a vapor barrier on top of the existing slab with another slab or 3/4" subfloor above that may work.
With 2" of EPS (R8.4) on the exterior there would be sufficient exterior R for dew point control on full-dimension lumber 2x4 balloon framing and cellulose in the cavities, but it would be pushing it with a full 4" of 1.8lb fiberglass. Go with cellulose- it's probably cheaper, and a bit safer in this stack-up. If you use dense-packed fiberglass you'd be well advised to use a smart vapor retarder detailed as an air barrier between the wallboard and the fiberglass.
http://publicecodes.cyberregs.com/icod/irc/2012/icod_irc_2012_7_sec002_par025.htm
Assuming a 20% framing fraction (about right for balloon framing ~16" o.c.) and 2"/ R8.4 EPS (highly recommended in your stackup) insulating sheathing the whole-wall R of the walls comes in at around R20.7, or a U-factor of U0.048, which is exactly IRC 2012 code-max U0.048 per TABLE N1102.1.3 (R402.1.3) in Chapter 11 of the IRC. If you went with 1.8lb Spider or L77 you'd be at a whole-wall R of about R21.6, or U0.046, only slightly better than code (and an expensive R0.9 improvement.) Adding a half-inch to the foam thickness would probably be both cheaper and higher performance than going with fiberglass vs. cellulose, and it would improve the dew point margin.
http://publicecodes.cyberregs.com/icod/irc/2012/icod_irc_2012_11_sec002.htm
A code-min house that size would likely come in around 28-30,000 BTU/hr @ -10F, and you're looking at performance that's ahead of that. I'd hazard that with U0.25-ish windows you'll be looking at a design heat load less than 25K. Good luck finding a modulating furnace that modulates down that far. You can get there with cold-climate mini-splits though. What's your 99% outside design temp?
https://articles.extension.org/sites/default/files/7.%20Outdoor_Design_Conditions_508.pdf
https://www.captiveaire.com/catalogcontent/fans/sup_mpu/doc/winter_summer_design_temps_us.pdf
If your design temp isn't much colder than -4F you can fully-specify a mini-ducted mini-split solution for the second floor, even if you went with a wall-coil or floor-coil type on the more open first floor. (You could also install a mini-ducted solution for the first floor in the basement, if you really wanted to.) You may have to move from Mitsubishi to Fujitsu for ducted solutions, but either would work for wall or floor units. A 3-ton Mitsubishi H2i multi-split can probably handle it just fine, but without the room-by-room load numbers and an outside design temp it's hard to spec a solution.
Thanks Dana. Good stuff. A few points of clarification needed.
Our design temp here is -8. My preliminary load calcs. suggest upwards of 30K, considering the above average window area, mostly uninsulated basement, tall walls, entry-way, etc. I was hoping or assuming that the smallest modulating Trane (60K I believe, minus LP reduction) might be acceptable.
I had hoped to avoid or postpone any modifications to the basement floor and foundation walls other than exterior insulation to 3' below grade. (big project to move mechanicals, storage, etc.)
An earlier HVAC scheme did rely on a first-floor mini-split for heating, second floor mini for cooling along with two pair Lunos ventilators (22 cfm/pair). I abandoned that plan to pursue more robust ventilation, now addressing radon and humidity in basement, with an HRV via furnace air handler's ECM blower. Are you suggesting that I go back to that plan? If so, is your main concern the over-sized furnace will be inefficient or lack comfort, or is your concern that the HRV/air handler coupled with the antique ducting won't provide effective ventilation?
Most century old houses have less window area to floor ratios than the late-20th century & newer houses, so yours may be the exception proving the rule.
The above-grade foundation is usually more than 10,000 BTU/hr if left unsealed and uninsulated. IRC code min would be R15 continuous insulation, which may be more than you were figuring on installing. What type and how much insulation are you planning for the exterior of the foundation, down to 3' below grade?
A pair of Lunos per floor (including a third for the basement) may be more expensive than a ducted ERV, but it may be easier to install. An HRV by itself isn't going to fix basement humidity, but it'll mitigate the radon, provided you've radon-sealed the slab or walls with either a purpose made sealer or a continuous vapor retarder. The radon sealing materials will also reduce groundwater entry, but infiltration and HRV will still introduce summertime moisture, since the slab temp will be below the outdoor dew point. If the slab were insulated the floor would be warm enough limit that problem, but uninsulated you'd have a mold problem at the floor unless you mechanically dehumidify the space &/or limit the ventilation rates. If you used a heat pump hot water heater it may be enough dehumidification all by itself, but maybe not.
Most of the modulating furnaces out there don't have more than a 2:1 turn down ratio. If the min-fire output isn't much lower than your average daytime winter load it won't modulate much. Which model Trane, and what's it's min-fire input or output? Typical modulating 60K Tranes run between ~23K-out on the low end, ~57K-out at high fire, just slightly more than a 2:1 turn-down eg:
http://www.bayareaservice.com/wp-content/uploads/2011/12/XC95m-Performance-Data.pdf
So if your whole-house load is say 33K @ -8F and your mid-winter binned hourly mean temp is +16F, the load at +16F is about 23K, the min-fire output of the thing. That means it will be cycling rather than modulating, except during mid-winter nights. It'll keep the place warm, but it's not ideal, and it's not something that's easy to effectively zone. A 2 story home usually has sufficiently different heat loss & gain characteristics between the top floor and first floor that at least the floors need to be zoned separately for optimum comfort & efficiency, and you can do that fairly readily with mini-splits & multi-splits.
If you're heating hot water with a condensing propane tank, you can probably just micro-zone the top floor rooms with low-temp panel radiator type baseboards (Runtal UF-3 or UF-4 or similar) using an ECM-drive smart-pump and some zone valves, and use a cheaper cooling-only mini-split for the upstairs cooling. Routing pipes is usually easier than routing ducts (even mini-ducts), and a micro-zoned condensing hot water heater based system w/radiators will be far more efficient and comfortable heating than a modulating propane furnace that rarely modulates.
The odds that the antique duct system is adequately balanced for supplies/returns or room-by-room, floor-by-floor temperature balance is somewhere between slim & none. It's utility as a duct system for the ventilation is also probably not very good. You'll likely have to either re-work the ducts extensively, or rip it out and start over, or abandon them for a plan-B.
What is the preliminary estimated heat load of the first floor @ -8F?
And the heat load of the second floor?
Fujitsu mini-duct units are fully characterized at -5F, and would probably cover the load for the second floor at -8F. The largest is the -18RLFCD, nominally rated for heat at something like 20,000 BTU/hr, which usually means it has that much capacity at +17F. It's output at -5F would have to be looked up in the extended capacity tables, but it'll be more than 10K, maybe even 15K. It won't have a specified capacity @ -8F, but it'll still be running and putting out substantial heat at that temp.
The Mitsubishi -FH18NA wall-coil type mini-split is good for something like 15,000 BTU/hr @ -13F/25C (comparable to the Fujitsu 15RLS3H) and may be able to cover your first-floor load.
Alternatively, a Mitsubishi H2i multi-split with 2-3 9K-12K mini-duct cassettes mounted where the output can be split between 2-3 rooms may also work just fine, and would be micro-zoned per cassette. The 2.5-ton 3-zone system is good for over 25,000 BTU/hr @ +5F in an all-mini-duct configuration, and probably good for more than 15K @ -8F (would have to consult the engineering manuals.) But like the Trane it's minimum modulation during the shoulder seasons might be too high to run truly efficiently & comfortably during the shoulder seasons if the heating load for the entire floor @ +47F isn't at least 6-7000 BTU/hr, but it has a better shot at right-sizing than with the modulating Trane.
http://richairductless.com/wp-content/uploads/2015/09/MXZ-3C30NAHZ_Submittal.pdf
The 4-zone 3-ton version is good for 45,000 BTU/hr @ +5F, and may be able cover the whole house @ -8F, not just the upstairs:
https://www.acwholesalers.com/hvac/pdf/mitsubishi/mitsubishi-multizone/MXZ-4C36NAHZ-sb.pdf
You are right about the window area Dana. This old house currently has a typical window ratios but because the orientation is oblivious to the great views we have on our farm, we are adding four new windows and expanding a couple more. Domestic bliss may not be energy efficient but it is sustainable.
You asked about the basement foundation; it will have R15 to 3' below grade. I am also planning on sealing the concrete floor as a first step in combating radon and moisture. Not sure what product yet.
Your discussion has helped me refocus on the comfort and efficiency concerns that have motivated this project in the first place. I seem to have lost that focus while listening to the conventional opinions of HVAC folks that don't have a diverse tool kit and didn't want to make the effort to dig deeply into our needs. Zoning between the 1st and 2nd floor has been a perpetual problem with the current furnace/ductwork and will not be resolved with a new furnace, not to mention the sizing problem. Moving forward, I intend to finish up the load calcs (with new windows and final wall U factors), then proceed to design a mini-split based system that will accommodate zoning the two floors. I will likely plan for a few cove or baseboard heating units to tweek the system for the occasional "closed door" use of a small guest room and office. For the ventilation system, I will probably be looking at three pair of Lunos along with the spot exhaust.
Again I thank you very much for your thoughtful analysis and suggestions. You have probably saved me from a regrettable choice. As always, any other thoughts are appreciated.
Ed