Controlling Vapor Drive Inside Soon-to-be-Renovated Walls

We made a mistake years ago when repairing rot and structural damage to our house and I need some help in finding the best solution and understanding some of the behavior of the building materials in question. I’ll do my best to get to the point without rambling as I have much respect for the experts who put their time in to help people here.
House: Built 1988, bought 2006, located near Albany airport (good weather data from station). Huge rot and structural damage found due to improper flashing and nothing installed between cedar siding and OSB. Repaired about 2010.
Repair: Removed all siding and replaced almost every door and window. Installed exterior rigid foam, fiber cement siding, pvc trim, windows pushed out, flex wrap door and window pans, typar flashing, custom metal flashing, calked flanges and trim, etc.
Repaired wall assembly (outside -to- inside)
Fiber cement lap siding
1″ Foil faced polyiso, taped seams
Tyvek house wrap
7/16 plywood where replaced (OSB where not)
5.5″ Mineral wool bats where opened (fiberglass where not)
6 mil poly sheet
1/2″ drywall
latex paint
Now that we are finally renovating the interior and I am educating myself about building science, I understand that what we did was wrong for our climate. The outside walls are sealed up tight as a drum, but can’t breath out. 6 mil poly keeps them from drying in. Only 1″ of exterior foam means we are below the dew point at the sheathing during the winter.
I would prefer not to remove the siding, trim, etc etc and break all the sealing we did just to add another layer of foam. I would also prefer not to spend a huge amount of money on a renovation only to find my walls rotted 10-20 years later. If I’m spending money, it needs to be on fixing any performance issues first.
During renovation many exterior walls will already be opened and so I am OK with opening ALL the exterior walls, from the inside. I have come up with some ideas, but I have yet to speak with anyone who can give me any kind of confident answer that we will be successfully addressing the problem.
To start, I will probably be using SIGA’s Majrex vapor control layer (which is directional) behind the drywall. It ranges from .16-1 perm inward, but up to >4 perms outward. In other words, it lets vapor in 10x faster then 6mil poly, but it lets it out 250x faster than 6mil poly. Vapor still goes where it wants.
I discussed flash and bat with someone (1″ open cell for breathability, but keeps air from the sheathing) but I was advised that it is a huge PITA in an occupied home because of the application mess.
The better option seems to be something like 1″ of EPS in each stud bay against the sheathing, cut about 1/4-1/2″ short all around. Then the gap filled with great stuff. This should keep the inside face of the foam above the dew point (almost all the time) but allow the OSB to dry inward if it needs to.
While I understand most aspect of vapor drive, I don’t understand the mechanics of moisture saturating something like EPS. If the temp at the interior of the sheathing drops below dew point, then vapor pressure = saturation pressure and moisture will flow from the wall cavity through the EPS.
If it encounters the condensation point inside the EPS does it condense and block the pores? If so, when its hot and AC is running and direction is reversed, if dew point is again in the EPS, does it stop the OSB from drying inward?
Does it keep pushing through and saturate the OSB?
Does it wick into the OSB?
How much water can EPS absorb?
If the Perms of the OSB are higher than the VC layer (inward) does it really do anything to help?
Is it more of a belt and suspenders in case of air infiltration in the cavity?
I should also say we have a ground source heat pump and humidity in the winter is 15-25%. Summer is low too (50% maybe) because of the level of dehumidification with this type of HP. Spring and Fall make me nervous. We will be installing an HRV as we tighten up the house.
Another idea is to install an active dehumidifier to force our indoor RH to track with outside temps to make sure sheathing inside is never below dew point (or in mold conditions).
Anyone ever apply mold killing paint in stud bays as a preventative measure?
Thanks in advance for your help. Sorry for the long post.
Also: Am I just crazy?
Chris
P.S. I opened a bathroom wall this mid-winter to put thermocouples inside to track the sheathing and insulation temp. The wall has been untaped, unfinished drywall since the repairs in 2010. It did have the PE sheet all that time. No mold, no water, no wetness yet. I didn’t measure the wood with a moisture meter but I will soon.
GBA Detail Library
A collection of one thousand construction details organized by climate and house part
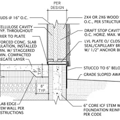
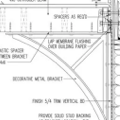
Replies
From the specs I've seen, Majrex 200 is so marginally unidirectional that I'd ignore this feature and consider Intello (with excellent wet vs dry perms).
Edit: link using EN1931.
Direction 1 - US perm 0.68
Direction 2 - US perm 0.23
Read Lstiburek's comments about why "too thin" XPS can work even with poly on the interior side - with your low humidity and adding excellent interior side air sealing, you may be able to make your wall similar enough to work OK. Your bathroom results support this.
Yes, adding cut-n-cobble foam will reduce condensation/sorption within the wall. Which allows you to let a little more moisture in with variable perm on the interior side. Which provides much better drying when drive direction reverses.
Cellulose (vs batts) also adds resiliency (because it can safely hold considerable moisture).
> never below dew point
Despite common belief, this isn't necessary and is rarely what exterior foam does. You only need "doesn't spend too much time below the dew point". Plus limit moisture entry so that moisture accumulation isn't excessive.
The house i am gutting, built in 1993 has foil faced polyiso as sheathing covering ~80% of the walls. 6 mill poly on the inside. The only place that had mold was where we had significant roof leaks and the moisture could not get out and the stud bays that had the dryer vent pumping into them. No sign of condensation problems that weren't the result of excessive moisture/bulk water infiltration.
That said, I am going back with rockwool, intello and a service cavity on exterior walls as I rebuild. Very easy to drive vapor back into the house that way.
Zone 7 N Wisconsin
Christopher,
I suggest you read these two articles:
"The Exterior Rigid Foam is Too Thin!"
"Rethinking the Rules on Minimum Foam Thickness"
Thanks for the quick feedback guys and the links to the articles.
Jon, where did you get those numbers? For a new product I am always skeptical of what the data sheet claims vs the actual performance so if there is someone has collected some real world data I would love to see it before putting this stuff in my walls.
Otherwise, their spec sheet:
https://media.siga.swiss/CIP/asset/download/medien/19603
and the chart at the end of this doc:
https://media.siga.swiss/CIP/asset/download/medien/22692
show that, if a room stays 50% RH or lower, you should see up to 3 perms inward. I've asked them for clarification on the outward perm rating. The data sheet shows it varies from .16 to 1.3, but they don't state what drives the spread. I assume, like most smart membranes, it varies with RH. But in this case, RH where? Interior, cavity or highest/lowest RH.
In a way, the amount of bias or directionality is irrelevant. If the VP wants to drive outward, the moisture is going outward. In that case, the only thing that matters is the outward perms. If it wants to go in, it goes in. It's more like evaluating two different membranes depending on which direction the vapor is moving.
Which brings me to my next question:
Martin, thank for the articles, they do give me some level of comfort regarding the areas that didn't need to be opened. I feel better about being able to address them in the future if needed. However, as I mentioned, there are several areas we will be opening anyway, or some that are already open. In these cases, what do you recommend doing in the wall cavity to minimize future risk?
Does using the Majrex make things more risky? I like the idea that drying in happens faster than wetting out. I am building a spreadsheet to see if I can estimate what % of time my house will spend driving out vs in to give me an idea of what kind of benefit this would bring. On the other hand, I am concerned with the fact that it is at least 10x more permeable outward than PE sheet.
On the other, other hand, if there ever is air leakage into the wall from some air sealing that failed (or less likely, bulk water intrusion) the wall would dry inward at least 100x faster than PE sheet.
Does the suggestion of 1" rigid xps or eps on the inside of the sheathing pass the smell test? Would I need something with a lower perm rating than the VC layer to make any difference?
Thanks again
I would stay away from putting rigid foam inside each stud bay and trying to seal it in. There have been numerous threads here about the long-term reliability of canned foam to maintain a good air seal. I've never seen a failure myself, but I wouldn't want to risk it here. I would avoid rigid foam cut into a wall in your case because of exactly the same reasons it's not recommended in unvented cathedral ceilings: it can't be trusted to be sealed in the long term, and might leak moisture and cause problems. I would do any moisture control on the interior side, or use your last resort option of opening up the exterior to add another layer of rigid foam.
Mineral wool is good in that it won't hold moisture, so that's a plus in the areas you've used mineral wool. I have a very similar wall assembly to you in one corner room in my home where I have 1/2" polyiso on the exterior (which isn't enough), and R15 mineral wool in the walls. I used CertainTeed's MemBrain on the interior to manage moisture in the wall. I haven't had any problems, but the assembly is only about one year old so it hasn't been up long. There is a thread on GBA where I discussed this, and you'll want to read Dana's reply -- he discusses that need for SEASONAL drying cycles, but not constant drying. Basically you can be OK with an assembly that ocassionally dips below the dew point as long as it doesn't stay there for extended periods of time. A little wetting in the winter that can dry out in the summer isn't usually a big problem, but keep that "little wetting" part in mind -- it can't be too much.
Thicker EPS is a vapor retarder. It's OK in with vapor, but not usually a good idea to have submerged in liquid water. In some ways it's vapor permeance is a plus -- I've used it on my rim joist in 2" panels to provide some insulation and air sealing but also some limited drying potention. I did this because the exterior foil faced polyiso allows NO exterior drying for the rim joit area.
The info you've heard about spray foam being messy is true. There is a fine mist of spray foam "overspray" that floats around and sticks to things. It is surprisingly difficult to remove. I have an extension cord and a tool carrier for a wire fishing tool that have a mist of spray foam on them that I've given up trying to remove. In new construction this isn't a big deal, you just hang poly temporarily on fancy stuff, and cover less fancy stuff like studs with drywall so any spray foam mist doesn't metter there. If you have finished floor coverings and furniture, you'll have to do a LOT of covering and sealing to keep that stuff safe, and I wouldn't recommend spray foam here -- you'd really need to remove everything from the room to be safe. You could potentially cover the floors with something like taped ramboard, but you would absolutely want EVERYTHING you weren't replacing to be well covered and sealed.
Bill
Hey Zephyr. Why the Membrain? Wall board and latex paint permeable enough without it?
Belt and suspenders, and hard to add later. I also detailed it as an air barrier.
Bill
Bill, thank you for confirming the spray foam mess. The advice I was given was that you basically need to move out of your house. I tried finding the thread you mentioned but couldn’t. Any chance you can link to it.
In terms of the EPS or XPS idea, I think the purpose in this case is as a supplement to the VC layer. I would still use a vapor retarder, but the rigid foam against the interior of the sheathing would act as a backstop in case of air infiltration. That way moisture laden air will never hit a condensing surface if the VC layer is breached or a mistake was made during air sealing.
I think it might also help in keeping a section of the wall cavity from being in the mold zone. In running some numbers, for example in the summer, if the room and wall start in equilibrium on a hot day, and the temp drops real low at night, you can easily hit the dewpoint at the sheathing. Then you are at >50F and >50% RH somewhere in the wall. With an inch of foam board, you get just a little more margin.
Despite that, I looked at worst case scenario for the summer (70F 60%RH inside followed by a night around 40F 100%RH, smart membrane with perms about midrange) and while you get condensation, if the air barrier is reliable, you would transport about 0.3g of water through the membrane over 8 hours. This is for a single 2x6 stud bay. The next day if it only warmed to about 80, all the moisture would move back through to the room in less than an hour. That assumes all the water that condensed and soaked into the wood could evaporate that fast.
I'm actually starting to get a bit philosophical and ask myself what the goal is.
If bulk water comes in, it needs to be fixed (pipe or rain leak) and I don't think I want it hidden by a self drying wall. I think our exterior detailing deals with that very well.
If we are talking about vapor drive, the only question is whether it is accumulating or drying over time. I think that comes down to how much time you spend in the condensation zone. Condensation is a special case, it is kind of like an on/off switch. When drying in, you can only move moisture until the VP in the wall matches the VP in the room, then the flow stops. When you have condensation in the wall, the saturation pressure in the wall is lower than the VP in the room and can never rise unless the temperature comes up. Once the switch is turned on, moisture will flow from the room into the wall forever. There is no equilibrium ever reached as long as the temperature stays low. The only thing you can do is slow the flow with lower perms.
So that leaves air infiltration. Bad for heat loss, but that's not damaging to the house. With a vapor retarder, the equalizing of the absolute humidity seems to happen (if I am doing the calculations right) on the order of hours, not seasons or even days. So the amount of moisture that moves from the room to the wall isn’t much different with a VC layer or not (specifically in my case where there is little to no breathing out. Maybe a bathroom is different too). Again, this seems to come down to the issue of condensation. If you have an air leak and condensation, now the moisture will flow in like a freight train and not stop until the temp comes up.
Of course all of this is why the exterior foam thickness recommendations are so important. If I could turn back the clock I would.
Maybe the idea of an interior layer of rigid foam effectively turns the inner part of the wall into a service cavity. If you can size it to never hit the dewpoint on its face, then air leaks in the membrane are inconsequential. Just thinking out loud as I try to settle on a strategy before starting the renovations.
Please set me straight if I'm off base.
"With a vapor retarder, the equalizing of the absolute humidity seems to happen (if I am doing the calculations right) on the order of hours, not seasons or even days."
I've often wondered what the 'lag time' would be under typical steady state conditions—collecting all the needed bits to do the math has felt too daunting —but I have to think your calculation is a bit off. If it were true, what would be the point of a vapor retarder/barrier?
Looking at some numbers (such as how much moisture a 1 perm membrane passes at 1" Hg pressure differential) I can't fathom that equilibrium would occur on the order of hours. (I suppose it depends on your starting conditions and outward drying paths though eh? If it starts at equilibrium, it takes 0 hours to reach equilibrium).
Your notion that condensation is a switch is interesting. Some of the accompanying phrases feel a bit...extreme, as if it’s a black hole sucking water endlessly into the wall. “Once the switch is turned on, moisture will flow from the room into the wall forever. There is no equilibrium ever reached as long as the temperature stays low.”
Your not really wrong per se. Condensation could continue ‘indefinitely.' It’s also possible that the system could stabilize by seeing a reduction in vapor content. The act of dehumidification via the condensation itself will lower the absolute humidity of the interior and raise the temp of the sheathing slightly (latent heat deposition).
Of course it’s possible that a house could work to impose a steady interior RH and therefore maintain the vapor drive and the wall wetting indefinitely. That is theoretically true at virtually any temperature condition if you maintain high enough RH. In fact, considering that 100%RH is liquid-vapor equilibrium, that is where a sealed container would trend if there was adequate water source. As such, if we could build a ridiculously tight house and run a wimpy humidifier we could create condensation endlessly on even an interior surface (steam rooms). At least until (and if) the latent heat of the steam warmed the interior enough to void condensation.
One can also reduce the issue by ventilating. Since even ‘tight’ houses have some ventilation, and cold air is dry air, we have yet another 'natural' feedback that helps reduce interior vapor pressures when it’s most helpful (when it’s really cold out and condensation is of concern). Unless we strong arm it and impose strict RH’s via active humidification.
Sorry if I wasn't more clear. The calculations I was doing were with a vapor retarder not a barrier. Specifically I was using my best estimate for the Majrex since I still don't have a curve that shows how the outward perm react to RH.
In that case I used about 0.5 perms into the wall and up to 2 coming back to the room. Also, my spreadsheet is very simplistic. I'm assuming the temperature drops instantly and the wall temperature reacts instantly as well. Of course these things happen over hours. Additionally, the vapor drive is assumed to be constant through each period. When the wall is condensing, this is true, you can put all the moisture in you want and the VP in the wall doesn't rise.
But for the periods where the wall is below 100% RH at the coldest part, the vapor drive will slow down as the pressure differential gets smaller. So my formula doesn't account for that exponential decay in transmission speed. To get closer, I need to shorten my periods and make more of them.
Regardless, even with the simplified spreadsheet, I think its clear that vapor retarders will react on the order of hours to equalize. Again, this is just looking at my special case with no outward drying and my being able to control the inside RH and Temp at constant levels.
Just plugging in a vapor BARRIER, my spreadsheet shows that the reaction is more like days or weeks depending on the conditions. If I picture the different walls in my head as an annual graph, I can imagine the AH in the wall cycling up and down daily with the temp swings and the general level of the line going up and down with the seasons. For a vapor retarder, I imagine the daily peaks and valleys follow the pattern pretty close but with a dampening effect. For the vapor barrier, I would guess that the daily peaks and valleys are almost non existent.
After all, that's the point of the vapor barrier.
> I looked at worst case scenario for the summer
Look at Winter/Spring, where you have much longer periods of condensation/sorption followed by slow drying as it warms up.
> air infiltration
Yes, air movement is far more important than vapor diffusion. A wall that is well air sealed on the interior side and leaky on the exterior side will dry outwards, even with zero perm materials. An air leak from interior to exterior (or even near exterior) will deposit lots of moisture in a small area.
If you really want to model this stuff, use WUFI.
>Look at Winter/Spring, where you have much longer periods of condensation/sorption followed by slow drying as it warms up.
Working on it. Summer was much easier because there is no frost and, at least in my case, condensation conditions would be rare. Maybe an occasional night time low. Winter is different where the condensation could be over a stretch of cold weather that lasts days.
>If you really want to model this stuff, use WUFI.
Thanks for the tip. I downloaded the free version. I did a quick test, but for some reason the temperature profile in the wall stay at a constant 68 through the whole assembly and never varies with outside temps. So that means the moisture data isn't really valid. I'll come back to it when I get a chance.
Reply | Edit Reply | Delete Reply
Deleted
Perhaps my dissonance has to do with the fact you're getting essentially no drying to the exterior. The notion that ab. humidity equil. could be reached in hours seems to contradict the ubiquitous notion that vapor diffusion doesn't move a lot of moisture, but maybe it's because a little IN can be enough when it's near nil going OUT.
I would just add that a vapor barrier and vapor retarder aren't fundamentally two different things (unless we're talking a true and idealized theoretical barrier), nor do they necessarily serve distinct purposes: they both are implemented to reduce vapor diffusion. They are just defined at different ranges of specs and the specifics of application dictate which range is desired.
The relationship between the rates of diffusion IN and OUT are certainly of great import. As is whether or not you are getting condensation, as you point out. (Though hygroscopic materials will seek RH equilibrium so can do something vaguely similar in regards to maintaining vapor pressure differentials. An interesting thought, since usually cellulose is cited as being advantageous for buffering capabilities, but it would seem it could also increase drives slightly, ultimately allowing higher amounts of moisture to accumulate in a wall than one with less hygroscopic materials. Will have to think on this more).
In regards to your wall, whether you are better off with poly or a smart membrane, I am not sure. I lean towards smart to allow drying when drives reverse. Intello opens up quite a bit.
You are right that adding rigid foam in the wall will reduce overall condensation; concerns are that if/when the seal breaks, will those spots around the broken seal that get really wet be able to dry adequately?
>"I should also say we have a ground source heat pump and humidity in the winter is 15-25%. Summer is low too (50% maybe) because of the level of dehumidification with this type of HP."
A heat pump (of any type) does NOT dehumidify in winter. Low indoor humidity in winter in an IECC zone 5/6 boundary area is a symptom of excessive outdoor air infiltration or high ventilation rates. Your house may be too leaky to control until you make a serious round of blower door & IR camera directed air sealing. Nate Adams' rule of thumb is < 1 cfm per square foot of floor area at 50 pascals to make the moisture & heat movement in the house controllable, and half that can make it easy. But that's not always easy to achieve in a retrofit.
If the duct system is poorly designed and poorly balanced you could be experiencing excessive infiltration/ventilation due to air handler driven room to room pressure differences, differences that use leaks in the house to take advantage of "The Great Outdoors" as the return path for equalizing those pressures. The Energy Star standard for duct systems is room to room pressure differences no greater than 3 pascals (=0.012" water column) under all air handler speeds, whether room doors are open or closed. If a doored off room is becoming pressurized or depressurized in excess of 3 pascals when the door is closed, a transfer grille or some sort of jump duct of adequate size needs to be installed.
In summer a heat pump (any type) can and usually DOES dehumidify, which is what you want it to do during sticky muggy NY summers. Rather than being "...too low...", controlling the indoor humidity to <50% RH @ 75F is a good target, but hard to achieve without a dedicated whole house dehumidifier if the house is too leaky, or if the ventilation rates are set too high. Most of the health professional recommendations target a 30% minimum in winter, 50% maximum, some will target 40% minimum in winter (which is riskier to the house.)
>" Spring and Fall make me nervous. We will be installing an HRV as we tighten up the house."
In a sufficiently tight house the wintertime and shoulder season indoor humidity can be controlled by the ventilation rate of an HRV. Whenever the outdoor dew point temps are under ~50F, increasing the ventilation rate will keep the indoor RH from exceeding 50%, and whenever the dew points are under ~35F increasing the ventilation rates will reduce it to (or bel0w) 30%. Operating the HRV under dehumidistat control works great in your area for at least 2/3 of the time, but in winter high ventilation rates will over-dry the house, bringing it to less healthy less comfortable levels for the humans. In Albany even the outdoor air temp averages less than 37F for the coldest 3 months of winter. The dew point temp is always lower than the air temp, though sometimes equal to the outdoor temp in dense fog, so an approach other than dehumidistat needs to be taken in winter. See:
https://weatherspark.com/m/24051/1/Average-Weather-in-January-in-Amsterdam-New-York-United-States#Sections-Temperature
>"I should also say we have a ground source heat pump and humidity in the winter is 15-25%. Summer is low too (50% maybe) because of the level of dehumidification with this type of HP."
Sorry if this was said a bit inarticulately. Our GSHP definitely does not dehumidify the air in winter. Our interior RH is entirely because of air leakage. The walls and windows are very tight because of the repairs but we still have huge air movement through ceiling penetrations, a vented crawl space that is not isolated from the basement, chimney that doesn't seal and direct vent bath fans that the kids never remember to turn off. The intention is to remedy all this with the remodel.
However, in the summer, I'm fairly sure that our GSHP dehumidifies much better than a typical ASHP. The Delta-T in the heat exchanger is larger due to the ground loop temp and the heat capacity of the loop fluid is much higher than an ASHP using outside air in the summer. The LAT (leaving air temp) in our air handler is often in the 30's when air conditioning. I don't know what is typical for an ASHP, but I don't remember our duct work being so cold before we installed the GSHP.
Ultimately I would like to increase the RH for the winter as our current level is too low. We have a humidifier installed on the air handler but I don't use it due to me concern about our wall assemblies.
One of my next strategic decisions (after I settle on a wall schedule) is to figure out HRV, dehumidifier, bath fan combo. But I think I ought to make that a separate topic.
Actually, after typing this reply, I just realized another issue. For better or worse, most of our second floor supply ducts run up inside exterior walls. Now instead of tracking with outside temps, these stud bays may spend much of the summer in the 40s.
To make matters worse(?) in the places we had to remove the sheathing, where ever we had a duct we packed mineral wool on either side and then installed 2" foil faced polyiso between the duct and the sheathing. We did not try to air seal the polyiso to the studs, just cut to fit and jammed it in. I have yet to re-open a wall with this configuration, but I can think of one or two that will be opened during the reno and we will see what has happened over the last 10 years.
Insulating the ducts with polyiso at least keeps the wood warm enough. If the seams in the insulation leak enough to cause moisture to drip it might make a few concentrated moisture points.
The air temp leaving the cooling coil in heat pumps is something that is controlled by both the heat pump and duct design. When better dehumidification is desired the cfm across is lower. The dumb rules of thumb for 1 or 2 speed AC is 400 cfm/ton of cooling, 350cfm for improved latent cooling, but with modulating systems those targets become irrelevant and it becomes a matter of how the system is controlled.
You're one step ahead of me. At the risk of diverging too much from the original topic I will also share that the GSHP setup is not great and will also need to be addressed. When it was first installed we added an Arzel zoning controller and now I understand the many reasons this is not a good fit. One of the issues that you hit on is the mismatch between the duct design and sizing of the system and the control mechanism.
I discovered that the heat pump and the zone controller have mismatched anti-short cycle delays. The result is that quite often the zone system calls for stage one and then waits for the LAT to come up (or down) before deciding to call for second stage. However, the HP delay is longer and then it takes time for the LAT to actually come up. So the zone controller steps up to stage 2 even if it is not needed.
When you combine that with the fact that you may only be trying to drive through 1/3 of the ductwork (because the other zones are not calling) you get over cooling of the air. The blower is an ECM unit and should be modulating the airflow, but because the heat exchanger is so large relative to the flow and open duct size, you end up with a slow velocity.
The Arzel system can't control the blower speed because it must be controlled by the HP control board. The Arzel does not have any feature that drops it to stage 1 (except for a fault trigger) once it has stepped to stage 2.
This just another example of the technology of the product offerings far outpacing the ability of the trades to become knowledgeable enough to adapt. I've been so put off by the number of times I get bad advice (or waste money on work that is wrong) that I feel I have no choice but to become an expert on these things myself. But that's a rant for another day.
P.S. I almost can't drive through part of our neighborhood because I have to look at a bunch of new houses going up and I can see the masonry veneer going onto the wall without any drainage plane behind it. Only one of many mistakes I can see just driving through.
Christopher, you may have moved past this bit about the eps in the wall, but after reading your original post again and some of the exchange here, I realize that the questions about the dynamic of the EPS wasn't addressed. I was with you in thinking that it will reduce condensation, but given the specifics of your assembly (namely the foil face of your ext. insul.) I'm not sure you would be seeing the benefit there. It's about the perm stack-up.
Thinking of it in the context of your earlier analysis with vapor retarders, EPS is a retarder, i.e. much higher perm than the foil faced polyiso. The moisture will drive through the eps, as you say, and will accumulate at the sheathing. Dew-point in the eps won't 'block' the flow.
Thanks for bringing this back around Tyler. That was my original thinking, and as this thread has progressed I am now revising my thoughts about this. Truthfully, this is as much about organizing my thoughts as it is about getting to the answer.
In terms of XPS or EPS as a layer against the sheathing I now understand that the effect would be to reduce air infiltration. If the perms of the rigid foam layer are higher than the VC layer, then the amount of moisture from diffusion is throttled by the VC layer and the rigid foam does nothing, I think. Maybe not, but maybe.
The next consideration would be whether or not the rigid foam would actually make things worse by trapping moisture against the sheathing and preventing it from drying. This would be in the case where you have water coming from the outside due to an unexpected failure in flashing or other water barrier.
> diffusion.. the rigid foam does nothing
Unless you have some infinite perm EPS, it technically isn't "nothing". But yes, in your case, it's mostly about preventing warm, moist air that made it through the interior side from reaching the cold sheathing. Everyone likes to analyze vapor diffusion, but air movement is much more important.
Is the say 5 perms of added EPS enough to allow effective inward drying? That very much depends on how much water is making it to the sheathing.
It's all interesting to discuss, but in the end, I'd trust that the 2021 code was done well and change to a variable retarder but not add more foam. This provides good inward drying and meets "TABLE R702.7(4)" and "Continuous insulation with R-value ≥ 5 over 2 x 6 wall".
My thinking now is more about how to configure the wall to handle "problems" and minimize risk. The articles above by Martin and Dr. Joe all (again, correct me if I'm wrong) discuss the real world performance of walls with too little exterior insulation, but generally only in wall assemblies without other problems. My take away is: "if there are no other problems (bulk water or air leaks) the wall will be fine." These articles are basically saying the same thing that Martin does in his book:
Q: How often does water vapor diffusion through walls and ceilings cause problems?
A: Very Rarely. In many cases, in fact, an interior vapor retarder does more harm than good. The most common way for moisture to enter a wall is from the exterior (usually due to flashing defects that admit wind-driven rain). The second most common way for moisture to enter a wall is by means of air leaks (exfiltration) carrying piggybacking interior moisture that condenses in a wall cavity. Vapor diffusion is a relatively insignificant cause of moisture problems in walls.
Or, to put the two together: With everything else in control, so little moisture moves into a wall from the interior as a result of vapor diffusion, that even when you have intermittent sub-dew point conditions, the real-world result is rarely ever a wall system failure.
So, barrier or retarder, my thinking is more about lowering the risk in the event that air or liquid water somehow make their way in. In that case, I am leaning toward a smart retarder to aid drying in either case.
In the even of air leakage, the problem still seems to hinge around condensation. The smart membrane can help dry it, but the next question would be how to prevent it (condensation, not air leakage).
The idea of a sealed layer of vapor permeable rigid foam would seem like a good solution to prevent AIR from reaching the sheathing, but as I asked in my reply to Tyler, what about the situation where you have liquid water from the outside wetting the sheathing. Would the rigid foam prevent the inward drying at a fast enough rate?
It seams to me that any foam that prevents air movement would work and the critical balance would be around the R-value to prevent condensation vs perms to allow drying.
I finally took the time to sit down with Wufi and I now have a wall assembly that works well and matches some of my observational data. It did confirm that in the case of a sheet of rigid foam against the interior sheathing, if the perms are higher than the membrane, the foam does not change the behavior of the wall (in terms of moisture loading from vapor diffusion).
Now I need to look at adding things like an air leak from the inside or water leak from the outside and reevaluate.
What was surprising was that Wufi was not predicting a condensation condition during the winters. This was surprising, but may be due to a slower thermal transience than I had figured. It also may be due to granularity.
On the other hand I was surprised at how much time Wufi predicts my walls will be in the mold zone during later summer and early fall. In these seasons the temp will generally always be above 50F in all parts of the wall so it really is just about the humidity level in the wall. I need to learn more about mold now, but high humidity against the sheetrock layer seems bad.
As of now, I am leaning towards adding a service cavity on the first floor to get plumbing, HVAC and electrical out of the exterior walls. Then anywhere on the second floor that gets opened (generally 2 bathrooms, 1 bedroom and a closet), a smart membrane and a 1" xps sheet air sealed, then compressed 2x6 mineral wool. The only reason I say XPS is because I have a bunch that I got used from a recycler. Most of it went on the basement walls, but there is enough left over.