EPS as continuous insulation in above-grade, rainscreen cavity walls

We are building a house in Toronto, Canada. By code we need interior poly, so our walls need to dry to the exterior. The assembly is:
5/8″ GWB
6 mil poly (vapour retarder)
2×6 wood studs @ 24″ o/c w. R22 Roxul in the stud bays
1/2″ plywood sheathing
Tyvek (drainage plane / air barrier)
1″ continuous rigid insulation
1×4 PT wood strapping (fastened through rigid)
marine grade plywood or painted hardie board panels as cladding
My question is- because the exterior rigid will be continuous, I am concerned about limiting the exterior drying potential by using XPS. Conversely, I am also concerned that the EPS will be crushed when we fasten the battens through it, and would prefer XPS for that reason. I have located a high density EPS (Atlas XGrade), but even that product has a pretty tight vapour transmission rate, and its much more expensive. Because our air barrier is at the Tyvek, I don’t plan to have them tape the rigid.
– Has anyone had success fastening battens through EPS?
– I have a consultant up here that tells me that local builders have used 1″ continuous XPS with success for years, and that only if the exterior rigid was thicker would we start trapping moisture in the walls. What do you think about that?
Thank you.
GBA Detail Library
A collection of one thousand construction details organized by climate and house part
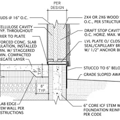
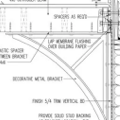
Replies
Wendy,
The principles behind this type of wall are well understood. You can read about the principles here: Calculating the Minimum Thickness of Rigid Foam Sheathing.
Your proposed wall assembly won't work. In your climate zone (Zone 6), the minimum R-value for the foam layer (when installed on the exterior side of a 2x6 wall) is R-11.25.
If you want to use EPS, you will need at least 3 inches of EPS. If you decide to use XPS, you will need at least 2.5 inches of XPS.
In all cases, you must make sure that the wall assembly doesn't include any interior polyethylene. If you have a building inspector who doesn't understand building science -- an unfortunately common occurrence -- you may have to install interior MemBrain (a so-called "smart" vapor retarder) so that you have a membrane to point to when the inspector asks about vapor barriers.
By the way, Tyvek is a good water-resistive barrier. It isn't particularly good as an air barrier; I recommend that you use either the drywall or the plywood sheathing as your air barrier (paying attention to leaks at seams and penetrations, of course).
Finally, if you expect the Tyvek to act as a drainage plane, you must include an air gap between the Tyvek and the layer that is exterior to the Tyvek. It makes more sense to put your drainage plane at a different location: mainly, on the exterior side of your rigid foam. This can be accomplished by using furring strips between the rigid foam and the siding.
It's a common misconception that Canadian code mandates interior poly- you can also use exterior insulation and no interior vapor retarders/barriers, provided there is sufficient exterior R for dew point control at the sheathing layer.
I'm not sure if the code has been revised/clarified but previously that had been interpreted by some to mean that the sheathing needed to stay at 4C or higher even at the 99% outside design temperature, with a 20C interior temp. This is a much more severe constraint than the IRC prescriptive values.
At 1" it's nowhere near enough for dew point control on R22 cavity fill, and thus you would need at least some interior-side vapor control.
At 1" most XPS is running about 1 perm, which is plenty of drying capacity into a rainscreen, and poly as the interior vapor control layer would actually work in that assembly provided it's VERY air-tight. MemBrain or Intello Plus would offer a lot more forgiveness on minor air leaks though. At 2" + XPS becomes too vapor tight to get away with poly on the interior.
FWIW: The concern about Type-II EPS (~2.5-3 perms @ 1") being crushed by the 1x4 strapping isn't well founded. The loading pressures are quite low, and the difference between 15psi EPS and 25 psi XPS simply doesn't matter here. There are many thousands of existence proofs of building this type of stackup with 15psi rated low to mid-density EPS & polyiso that work just fine. It takes quite a bit to crush the stuff with 1x4 strapping- you'd split the strapping if you torqued the screws that hard!
Thanks Martin and Dana
Ontario Building Code dictates the thickness of exterior rigid when used in combination with stud bay insulation (Table 9.25.5.2) when the permeance of the exterior rigid is not greater than 60ng... For Toronto heating degree days, it specifies that the minimum ratio of the total thermal resistance of the outboard insulation relative to thermal resistance of the inboard is 20%. So for 1" of XPS with R5,and R22 Roxul: 5/22 = 22%, this complies. That said, 1" of XPS has greater than 60ng, so isn't regulated under this table anyway. Dana's comment about 1" being the max thickness you would want to go with interior poly jives with local practice. It has been recommended to us to not exceed 1 1/2" XPS when keeping the interior poly.
This is why I was asking about EPS, because it seems like it would allow for more drying potential to the exterior when keeping the poly. The use of interior poly as vapour barrier is extremely entrenched up here. Even on some projects where we were using 4" of closed cell SPF, we've had trouble with inspectors still wanting interior poly. It makes building permit process much easier if we use the poly, and so in the past we have stuck with minimal thickness exterior rigid and interior poly. We also do air sealing at the GWB layer, and have recently started to specify Blueskin VP100 instead of Tyvek to improve air sealing from the exterior.
The Ontario approach is contradictory to minimum thicknesses required in the US, but they don't seem to have widespread failures with 1" of exterior XPS and interior poly, which I know at least one giant homebuilder up here uses frequently. I want to improve our standard wall assembly, but there doesn't seem to much opportunity between a wall with poly and 1" rigid and the giant leap of moving all insulation to the exterior. Thanks for your time.
You should probably also consider rigid mineral wool board. Martin has an article about it from a few years ago. - https://www.greenbuildingadvisor.com/blogs/dept/musings/installing-mineral-wool-insulation-over-exterior-wall-sheathing
You can see some pictures from a recently completed project that I consulted on here - http://www.prometheanhomes.com/portfolio.html We used 2" Roxul "Rockboard 80" (8pcf) in this case. If I remember correctly, the material price was about 10% more than Type II EPS.
Martin, Have you changed you position on where the House wrap goes? Your comment above seems to be cut and dry, put it on the outside of the ridged foam. However I think in a previous article you indicated some pro/con to each and provided a way to simplifying the decision (innie/outie). https://www.greenbuildingadvisor.com/blogs/dept/musings/where-does-housewrap-go
In Joe Lstiburek perfect wall set up he does not really talk to the need for that capillary break at the house wrap plane (http://www.buildingscience.com/documents/insights/bsi-001-the-perfect-wall) but I do think you are right. This is why when I did my house last year I used Tyvek drainwrap between the plywood and the XPS. https://www.youtube.com/watch?v=7YO0t1FtyCg
Wendy, Agree with Martin that Tyvek is a poor air barrier. My two cents is if you going to all this trouble anyway get a good tape and tape the sheathing.
Mark,
Plastic housewrap usually functions as a WRB. It can be a drainage plane, but it usually isn't.
If you are using plastic housewrap as a WRB, it can be installed behind the rigid foam, or on the exterior side of the rigid foam. Either way can work. (Of course, some walls don't have rigid foam).
If you want a drainage plane, you need an air gap. That can be accomplished many ways: with furring strips, with three-dimensional plastic mesh, or with a wrinkled wrap that includes ridges.
However, if you use plain old-fashioned Tyvek or Typar, and you sandwich it between OSB and rigid foam, you can't call it a "drainage plane" (as Wendy did in her original question).
The crinkle type Tyvek maintains a drainage function and offers at least some capillary break when between foam & sheathing. It's enough to make a worthwhile difference, but it's nothing like the capillary break & drainage capacity of 3/4" of air.
Martin, I see were I went wrong. WRB doesn't necessarily mean drainage plane, which is obvious once you stop and think about it. As always thanks for the education.
Dana, I agree crinkle house wrap is no substitute for a 3/4" rainscreen.