Envelope Renovation in 2A: Part 1- Attic

I’m going to break this down into 2 posts…attic and wall, with the attic/wall intersection here.
Brief background on existing conditions:
1970 2-story home (2500sf) here in Seabrook (SE Houston), a very hot very humid climate in a 110mph windzone
1st floor: 85% brick veneer on 2×4 stud backup and faced fiberglass batt insulation (sheathing/weather barrier unknown)
2nd:floor: is 12″ Masonite lap siding attached directly to studs (yes…no sheathing)…again with the fiberglass batts
Attic: As is the case with every home in this area, the fancoil, furnace and ductwork are all sitting in the oven otherwise referred to as the attic. As if this isn’t bad enough I can see the ceiling drywall from the attic access stair across the vast majority of the attic floor (iow…next to no insulation). It’s no wonder it is almost impossible to keep the 2nd floor cool during the summer (having only one thermostat on the 1st floor certainly doesn’t help either)
So addressing the attic…since the roof is relatively new my preference is to address the problem inside the attic. There is a continuous ridge vent but otherwise ventilation is handled by gable vents…no existing soffit vents.
Before pricing here is the plan based on reading several articles on the topic:
The attic is very shallow (6:12 pitched roof that is dropped 2′ in the front with dormers) and there is an amazing array of completely haphazard kickers and braces holding up 2×6 rafters.
What I want to do…ignoring the random kickers and bracing…from the furring down-
*add 2×2 spacers to each side of rafters
*install 2″ polyiso on the spacers leaving 1 1/2″ clear venting channel) (R13)
*Install 2″ closed cell icynene pro seal eco (closed cell spray foam) (R9.8) providing an excellent air barrier
*install 3″ polyiso to bottom side of rafters (R19.5)
*install 2×6 insulated kneewall to match roof
*if at all possible I’d like to spray in a 2″ layer of the closed cell foam to complete the air barrier the the exterior wall, then blow in the death triangle cellulose insulation leaving enough room for soffit ventilation to reach vent channel
Ideally I could get an engineer to evaluate the kickers and braces and clean up the remaining conditioned attic void. Since our HVAC system is way past it’s life expectancy replacing that is in the plan as well…hopefully smaller and more efficient for not running in a 130deg attic. Also…as part of the hardie siding job my preference is to eliminate the gable vents and install cont. soffit vents to replace them.
Current 2012 Energy code would require R38 here and this would comfortably exceed that with R42.3 and would bring the HVAC system inside the conditioned space.
Are there any obvious holes or dangers here? Aside from energy conservation the other main objective is to improve the air quality of the home…since moving here 9 years ago my wife has developed allergies and asthma that never existed before.
Since we are replacing the HVAC system…what recommendations would you have on system replacement under these conditions (climate and indoor unit)
I’ll get to the walls in Part 2
Thanks in advance for your time…
Jon
GBA Detail Library
A collection of one thousand construction details organized by climate and house part
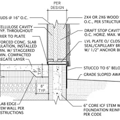
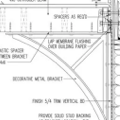
Replies
Jon,
Your approach has a few peculiarities, including your idea to insulate your rafter bays with rigid foam / spray foam / air space / rigid foam. That seems complicated. I'd be inclined to fill the air space between the rafters with insulation, if I were you.
Also -- what are the kneewalls for? If you are insulating along the roof slope, why install kneewalls? Or are the kneewalls already there?
Martin:
The air space is above the rigid and intended to provide a vent channel between roof sheathing and insulation. sheathing/airspace/rigid/spray foam/rigid (bottom of rafters)
On the knee walls...these were conceived based on one of the articles on this site. My concern is getting to the edges. The attic space is tight as is so I figure it will be easier to bring the air barrier down to the attic floor once the task of bringing the hvac equipment/ductwork inside the envelope is accomplished. It would no doubt be better to just continue straight down the roof to the exterior walls but how could an installer get there and what kind of workmanship could you expect. It's a means and methods question in the end with my main goal being a reliably tight continuous air barrier and all hvac equipment in conditioned space.
How best to accomplish this without the benefit of new construction is why I'm here:)
Out of curiosity...if total home electric use is ~20,000kwh/year, how much of that can be assumed to be cooling cost. This is just ballparking I know with no other information but I'm trying to quantify potential energy savings. At the moment I'm assuming half of that is cooling load.
Jon,
I misunderstood. I didn't realize that your proposed 2 inches of spray foam would fill the rafter cavities. (Now I realize that your rafters are only 2x6s).
If you create an air barrier at the kneewalls, that leaves the triangular attic behind the kneewall in a kind of no-man's land. Will there be an air barrier in there somewhere? What does it connect to?
2x6 rafters are hard to believe I know...explains the plethora of kickers and braces all over the place.
As for the devils triangle it is the biggest challenge regardless of whether a knee wall is installed or not...for that matter maintaining continuity of the air barrier from the wall (once rebuilt) and the roof/attic.
Here is my thought process: Fill the floor/ceiling cavity from the knee wall to the exterior wall with the closed cell spray foam...or at least a 2" layer of it. With the idea that the foam will be more forgiving by expanding into existing gaps. Once air barrier is accomplished blown cellulose could bump the overall r-value of the space up making sure that the venting is maintained.
I just thought it would be easier to do this on the attic floor than the angled roof but I could be convinced otherwise. I've personally never used spray foam insulation (or seen it used) so I'm not fully educated on it.
Tying into the wall I hope will be achievable when the wall/soffit gets stripped bare for the siding job.
Unless you have soffit to ridge venting you can't put foil face insulation on the interior side without creating a moisture trap.
In your climate you can safely dense-pack cellulose directly at the roof deck, (or 1" of closed cell foam against the roof deck with the rest as dense-packed JM Spide), no venting required. Without continuous soffit to ridge venting on each rafter bay maintaining the cavity is pointless, and in your climate venting the attic ADDS rather than reduces the moisture levels of the wood in the attic.
If it's possible to build out truss-type elements using 1/2" OSB or plywood sections for the truss webs and 2x2s as the interior chord you can hit R40ish performance pretty cheaply with a foot of damp-sprayed fiber, at lower expense and lower labor than your proposed solution. See Table 3 in this document (then read the whole thing to understand what it all means):
http://www.buildingscience.com/documents/bareports/ba-1001-moisture-safe-unvented-wood-roof-systems.
If the gable ends are the siding-on-studs-no sheathing type it's probably best to install a mesh-type rainscreen material (10mm Obdyke Rainslicker or something) against the siding and shoot 1" of closed cell spray foam onto the mesh as the air barrier, after which you can install as much cellulose as you like. The closed cell foam would qualify as a weather resistant barrier, and with the mesh to dry into the fiber cement siding won't load up with enough moisture to compromise the exterior stud edges.
How is the brick veneer being vented toward the exterior?
Searching the web for pictures to illustrate what I mean by the built-in-place truss approach, this wall-assembly Larsen truss is pretty close:
http://rootriverhouse.2030home.org/why-use-a-larsen-truss-wall/
It's pretty awkward to do in tight knee-wall attic spaces, but usually still possible.
Well the proposed solution does incorporate continuous venting from soffit to ridge but I'll definitely look into your proposal. My solution feels like an expensive solution and I don't want to spend unnecessarily. House has a lot of problems to fix.
Not sure what you're driving at on the brick veneer. It's cavity wall construction and weeps at the foundation. What I don't know is what the layer are from brick to stud without doing some demo. I won't be replacing the brick so the lack of an air barrier in these locations will remain a concern.
Part of the problem with adding a lot of depth is the very low clearance as it exists. Since they built it with soffit line roughly 3' below 2nd floor ceiling in front (dormers give the window height in the 3 front facing rooms), there is only about 6' of clearance from the attic floor to the bottom of sheathing at the ridge. So it gets cramped really fast. I at least need enough room up there to get the HVAC system in.
Also...I'm real leery of unventing a vented attic but I could possibly be convinced by science.
BTW...I will be adding sheathing to the exterior walls with the new fiber cement siding.
In addition to weeps at the bottom it's best-practice for the cavity to be vented at the top so that moisture will naturally convection-purge. With only weeps at the bottom when the sun hits dew/rain wetted brick there the moisture levels in the cavity become extreme, and can cause condenstation/mold/paint-failures in the interior side finish wall. But if vented at both bottom and top the same warming that drives the moisture out of the brick also creates a convection current, taking the extremely moist air to the exterior.
In your situation where the wall structure above the brick veneer is unsheathed studs with fiber cement siding and batt insulation in the cavities there can be issues in the upstairs walls if the brick-cavity air convected into the extremely air & vapor permeable fiberglass behind the fiber cement, but if there is flashing or something at the top of the brick cavity to block those flows, and exterior vents to allow free movement of that air to the exterior it'll be just fine.
Dana:
That's a very good point and I have no doubt that once I pull off the old masonite siding I will be horrified by what I find. There is a very good chance that I end up removing and replacing all the existing insulation once exposed if it's in the condition I fear.
The wall I was going to start another thread for but in essence once I solve the insulation question my intent is to sheath all the walls where new fiber cement siding will be installed, apply a vapor permeable air barrier which I will find some way to tie into attic/roof and at least seal up the top half of the house. Plan is to replace the windows too so will address flashing to seal them up throughout.
As for the brick wall it should be possible to vent it at the top without much trouble. There is actually a slight overhang of the second floor (N&S) which would provide an easy place to install a perimeter vent...or just vented soffit panels at the 2nd floor overhang. East and west ends could be trickier but maintaining that convective path does make sense. I'll just have to take a closer look at that transition detail to provide a vented path.
May be cheaper to just build a new house, lol.
BTW, I plan to install some cont. rigid over the WRB outboard in addition to the existing stud cavity insulation and incorporate a rainscreen application of the siding. Maybe I'll figure out how to use WUFI and do some energy modeling.
Jon,
Unvented roofs work fine, especially in hot, humid climates. To learn more about unvented roofs, I suggest that you read:
How to Build an Insulated Cathedral Ceiling
All About Attic Venting
Q. "What kind of HVAC system should I be looking at to properly control humidity levels inside the house?"
A. A simple, stand-alone dehumidifer (one that costs about $250). For more information on the use of stand-alone dehumidifiers in Houston, see All About Dehumidifiers.
Okay...so we spend a lot of time talking about venting the roof deck...fair enough, makes sense, time tested logic.
but
In a hot humid climate like SE Houston would it make sense to scrap the roof ventilation altogether and just use the closed cell spray foam to seal the attic up tight? Would you use a coverboard to separate the foam from the OSB decking to facilitate any future reroofing requirements since the foam would stick like glue to the decking otherwise.
I'm sure that felt is all that protects the OSB from getting wet but I wasn't here when the roof was installed.
Would this method make sense? And what special considerations would need to be addressed?
What kind of HVAC system should I be looking at to properly control humidity levels inside the house as well as temperature...and what about air changes? Since allergies are a big problem I'd like to make sure that positive pressure is always maintained but also that air changes are greater than normal and all outside air is properly filtered and cleaned. The air here is horrible! With the ship channel and countless refineries/plastics plants frequently upwind of our house (irony being the cooler northeast winds bring the worst polluted air). Any recommendations on managing this...or a good resource would be appreciated.
Thanks
Jon