Energy load for wall assembly in Oakland, California

Hello all,
I am settling on a wall assembly for a 1000 sq ft, 2-bed, 1-bath. The assembly includes R-19 in 2×6 bays with Zip sheathing. Simple, but this is in climate zone 3.
The assembly does NOT have a continuous thermal break, and this is where I wanted to hear from the community. I priced Zip R-Sheathing R-3, and it comes out to $1633 more for the project.
I ran this calculator:
https://www.builditsolar.com/References/Calculators/InsulUpgrd/InsulUpgrade.htm
I compared R-17 (for loss through studs) and R-22, and it tells me I’d save $1259 over 10 years. And I’m assuming this calculator is costing electric resistance heating, where I’d be using a ducted heat pump.
*Money is tight on this project. Is it worth it to install the R-3 insulated sheathing?
*Is there some other way we’d be saving money that I am overlooking? (Like heat pump sizing?)
*Any other thoughts on this assembly?
Thank you!
GBA Detail Library
A collection of one thousand construction details organized by climate and house part
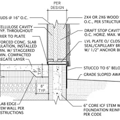
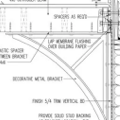
Replies
I would be sure to check your state and local building code. I am pretty sure that current or soon-to-be in effect California Title 24 will require R20 plus continuous exterior insulation for nearly all climates.
R17 whole-wall would be extremely optimistic. For 16" o.c. framing in your stackup figure R13-R14 after thermal bridging if using R19s. For 24" o.c. framing ~R15-ish.
Peter is right, R19 doesn't even meet code minimums anymore. R19 batts only perform at R18 when compressed to 5.5" in a 2x6 stud bay (rather than at their manufactured ~6" loft, the thickness at which they are tested for labeling.) R20 batts perform at R20, and would meet current IRC code minimum for zone 3, but will probably not meet the Zero Net Energy version of Title 24 that will be coming into effect soon.
Using rock wool instead of fiberglass would give you R23 at center cavity, boosting performance while making it more fire resistant. That's an upcharge, but it would bring the whole wall performance closer to R16-R17 in a 2x6 wall. If R21 fiberglass is cheaper, it would be almost as good from a thermal performance perspective, but much lower fire resistance.
To make it even more fire resistant while boosting performance, a continuous layer of rigid rock wool insulation on the exterior would be "worth it" in wildfire zones, despite being substantially more expensive than an inch foam board. If foam board, an inch of foil faced polyiso would have better heat rejection than EPS due to the low-E facer with even as little as a 1/4" air gap to fiber cement siding. Polyiso has a slightly higher kindling temperature, and unlike EPS chars in place rather than melting even when fully engulfed in flame.
To save money and for a more green assembly, lose the sub-slab and slab edge XPS sub-slab insulation- use EPS instead. XPS is more expensive per labeled-R, and is blown with extremely high global warming potential HFCs, and it loses performance over a few decades as the HFCs dissipate, eventually dropping to the same performance of EPS of similar density and thickness. EPS is blown with comparatively benign pentane, most of which escapes the foam and is recaptured at the factory.
Then there is the matter of how much sub-slab and slab edge insulation actually makes sense. Your 1.5" XPS under the slab is overkill. The IRC only prescribes R5 slab edge, and nothing under the slab, but that's not necessarily the optimal most cost-effective values. In Table 2 on p.10 of BA-1005 they recommend ~R7.5 for the slab edge, ~R5 for sub-slab insulation in zone 3:
https://buildingscience.com/sites/default/files/migrate/pdf/BA-1005_High%20R-Value_Walls_Case_Study.pdf
That could be met with 2" of EPS at the slab edge (R7.8-R8.4, depending on density) and 1.5" (R6.3, 1.5.ls per cubic foot Type-II or denser) for the sub-slab foam. In most cases you could get away with using 1.25lbs (Type-VIII) under the slab, which would still be about R6.2. Type-VIII EPS is commonly used as roofing insulation, and can often be had for VERY cheap (1/4-1/3 the cost of virgin stock) on the used/reclaimed market, in which case 2" would still be cost-rational under the slab.
Thank you both.
First of all, I wanted to make sure I'm reading my Title 24 requirements properly. I've attached a snip of my exterior wall calcs. And, here are the minimum requirements:
https://www.energy.ca.gov/title24/2016standards/documents/2016_Residential_Mandatory_Measures_Summary.pdf
This says: "Above Grade Wall Insulation. Minimum R-13 insulation in 2x4 inch wood framing wall or have a U-factor of 0.102 or less (R-19 in 2x6 or Ufactor of 0.074 or less)" I have 2x6 walls. Am I correct in reading that as R-19 insulation minimum?
Secondly, getting a well-performing wall. I'm on this website for a reason, of course, and I'd like to build the most energy efficient wall I can afford. Despite the Title 24 minimum, what REASONABLE R-value should I be shooting for?
It looks like I need to go back to the drawing board and start comparing prices. Here's what I'll be pricing:
- R21 fiberglass
- Rockwool batts (R23 you say??)
- Rockwool, rigid
- Polyiso, rigid
- Zip R-Sheating, of course
Since I'm planning to use Zip anyway, I assume the installation will be easier with integrated polyiso. I also have more trust in a "system" rather than a field assembly. Or maybe I'm just digesting the marketing.
Thoughts?? Thank you!