Enclosed room on slab

In the midst of an enclosed porch over slab job. Plans initially included flash on un-vented roof, rigid foam on exterior, house wrap and fiberglass in walls.
It was initially assumed that the floor was on slab, however upon demo I found out it is actually 3/4″ plywood on 1×3 sleepers. Seems to be 15lb roof paper under sleepers. I removed some of the subfloor and found evidence of moisture and mold on both the sleepers and plywood. There was a leak in an exterior wall as well as in the hydronic heating so I am not sure if the mold is from that or from moisture making its way past the roof paper from the slab. what would ideal remedy here be? The slab is sloped a bit so installing foam with plywood on top wouldnt work by itself.
The slab is above grade about 14″ and exposed. Climate is 4a
GBA Detail Library
A collection of one thousand construction details organized by climate and house part
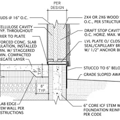
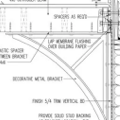
Replies
Jason,
I'm not sure that I understand your question. It seems to me that you have a sloping slab that may or may not be damp. This slab used to be an exterior patio or a porch slab that is now being enclosed and made into a room. Is that right?
What's your question? Do you want to know how to prep the slab for finish flooring? If so, it would be good to know what type of finish flooring you intend to install.
Jason your only way of telling if the moisture is from the slab or the wall is via thermal imaging (FLIR Camera) and testing the slab for moisture (Wagner Meter).
http://www.flir.com/flirone/explore.cfm
http://www.wagnermeters.com/flooring-moisture-meters/concrete-moisture/
Richard,
There are actually several ways. You can tunnel under the slab from the exterior to determine whether (a) there is any crushed stone under the slab, and (b) whether there is any polyethylene under the slab.
Sorry for being too vague... I was posting on my phone and couldn't add pictures.
I attached a picture of the enclosed porch as it currently exists (minus a few windows), as well as the current state of the floor. I am renovating the porch --- new windows, exterior foam, roof/ceiling insulation etc. When I started the job, I incorrectly assumed it was strictly a slab --- however there are sleepers, with 3/4" plywood that had carpet on top.
My questions involves the most effective way to treat this renovation --- from both an energy and moisture standpoint. At the moment I am not sure what floor covering the homeowner is planning as I am not installing it.
* i do not know why the pictures are upside down, but if you click on them they seem to be right...
Jason,
I'm still lost. You wrote, "My questions involves the most effective way to treat this renovation --- from both an energy and moisture standpoint."
Can you be more specific? In general, to be energy-efficient, you want a thermal envelope that is as airtight as possible and is well insulated. If you can afford them, you want to include high-performance windows.
Martin,
I am focusing on the floor and what to do with that --- keep the sleepers/asphalt paper? Add foam? Add 6mil plastic?
Jason,
How you prep the slab depends on your finish flooring choice.
If there is moisture and mold on the sleepers, you need to identify the source of the moisture and correct the problem.
From the pictures it looks like there may be cutback adhesive present. (black stuff on the concrete) Hard to know for sure. If this is an accurate statement there are ways to cover it over without disturbing what potentially could be asbestos in the product.
Need more information before I comment further.
As for the moisture... You can install Schluter Ditra over the concrete pad, tape the seams and flash up onto the walls with Schluter waterproofing tape for a water tight barrier. Of course you can next... install a floating floor over this surface or install stone or ceramic tile over this as well. Seems this would be the cheapest solution to me or you can tear it all up to investigate further like Martin would do and build the assembly to modern standards at a substantial cost.
http://www.schluter.com/6_1_ditra.aspx
Martin..... :)
Why would you want to tunnel under a slab when testing instruments are available to you to make life easier? Lol
The black on the concrete slab is just roofing paper.
Martin, the homeowner is looking to put carpet down. Assuming there is no poly under this slab based on the age of the house, I was thinking of treating this like a mini crawl space? Wouldn't 6-mil plastic under the sleepers be a good idea? How about rigid foam between the sleepers? The perimeter of the slab is exposed - as shown in the first picture - so I don't know if that would diminsh the effect of any foam on top to the point where it isn't worth it
Jason since carpet is the choice you need to manage the water or your going to have a mold claim.
This link should help you. If it's good for hardwood flooring it will work for carpet.
http://www.oakcrestlumber.com/nofma_installinghardwoodfloors.pdf
Jason,
You have at least three issues.
Your slab is uninsulated.
Your slab is not level.
Your slab may be damp.
If you want to correct the slab's slope, you need a solution that includes tapered sleepers. I would suggest that you begin by installing a vapor barrier (for example, 6-mil poly), and then install pressure-treated tapered sleepers, with the tops of the sleepers level. I would also install rigid foam between the sleepers.
Then install 3/4-inch T&G plywood, so that you have a level floor. Then install a continuous layer of rigid foam, followed by another layer of plywood, screwed through the foam to the lower level of plywood.
Of course, that takes up several inches of your ceiling height. But after all, you can't create finished space in an area with a damp, uninsulated, sloping concrete slab unless you correct these three problems. Right?
Thanks Martin --- I was thinking of steps 1 & 2 --- hadn't considered the extra continuous layer of foam. Any minimum recommendation for thickness of the 2nd layer of rigid foam? XPS?
Appreciate the help & expertise.
Martin,
Respectfully speaking, your solution is an indoor environmental nightmare and extremely labor intensive.
This project has 2 solutions as I see it. Your IAQ nightmare which is also what the previous link I posted earlier refers to, or the following....
1. Clean the slab
2. Prime the slab
3. Poor self leveling cement .... http://www.mapei.com/US-EN/Floor-Covering-Installation-Systems/Self-Leveling-Underlayments-and-Primers
4. Install 6 mil poly, over lap seams and seal with urethane caulk
5. Install 2" of rigid foam
6. Install 3/4" T&G plywood / fasten down with Tapcon Screws
7. Install Pad & Carpet
and also read the following GBA article.... ;)
https://www.greenbuildingadvisor.com/blogs/dept/green-communities/carpet-basements-issues-solutions-and-alternatives
Richard,
Your suggestion is a good one, and Jason should consider it.
My suggestion simply indicated one of many ways that Jason could proceed. There is always more than one way to skin a cat.
However, I disagree with you that my suggested approach was an "environmental nightmare."
Martin,
If I enjoyed eating out at the Wok down the street, I'm sure they would agree with you on the cat issue.
Do you have non-biased IAQ / IEQ data to support chemical emissions from PT lumber is safe for interior use? How many times has this product been reinvented to only prove modern playgrounds are toxic waste sites when they were the cat's meow previously? This is what I mean. I simply do not trust this industry is looking out for anyone but the $$$$$
Richard,
"Environmental disaster" is strong language. The Valdez oil spill was an environmental disaster.
Thousands of homes have pressure-treated sleepers on concrete floors, with the sleepers covered by T&G plywood subflooring. As I'm sure you know, subflooring is installed with subfloor adhesive, so the plywood subfloor is close to airtight.
If you can point to a researcher's report showing illness or problems in a home with pressure-treated sleepers between a slab and a layer of T&G plywood subflooring, please submit it. If you don't have a link to such a report, I'm going to conclude that your language is unjustifiably alarmist.
Martin your turning a mole hill into a mountain. I did not intentionally mean to step on your toe.
"unjustifiably alarmist" is a powerful insult Martin?
That's what everyone said when I came out 3 years ago writing about high pressure spray foam and it's toxic chemicals for which my family was subjected to. I like to think the attention I have brought to this product is bringing safety to the fore front today for everyone's protection. Do you disagree with this to?
EPA, CDC, CPSC, SPFA, ACC, CPI are certainly not calling me an alarmist today. Frankly they are all scrambling to come up with warnings and safety data, including ASTM's call for IAQ standards.
Facts are facts. It's just how it's written as to how people accept the language.
Chemicals harm people especially in today's air-tight building environment. Dose is the poison is taking on new meanings today as we are being overdosed in air-tight modern construction all while building science determines what is the proper air exchange rate for a healthy home. Those families are Building Science lab rats. Sad but true.
We should minimize chemical exposure as humanly possible to protect our children. Builders unlike you and I, do not have the time to research every single item they install inside a home so chemical exposure is not on most builders minds. Money is and safety is referred to code writers.
Chemicals compound in homes which is where the harm begins over time. We spend most of our lives in our homes and we breathe, ingest and absorb these chemicals into our bodies. Should I be hung for warning people that they need to pay attention to health and safety?
Pressure treated lumber has always been thought to be safe and as always it's found later in life to be poison by WHO, EPA and CDC which is why the chemicals change over time as human science is written.
What may be good for you may be poison for me. That's life.
Now lets look at the chemistry used in pressure treated wood and it's warnings about the chemical(s) used to treat the wood. Which pressure treated treatment are you specifying Martin? Is it just generic language. Here are your choices below. Pick your chemical of choice.
Alternatives to CCA published by the EPA
"Propiconazole"....
http://msdssearch.dow.com/PublishedLiteratureDAS/dh_005f/0901b8038005ff9b.pdf?filepath=/011-10099.pdf
"Cyproconazole"
http://www.syngentacropprotection.com/pdf/msds/03_267445302008.pdf
"Copper Azole"
http://www.americanpoleandtimber.com/pdf/MSDS-for-MCA-treated-wood.pdf
"Borates"
http://www.rosemill.com/v/html/msds/dot_MSDS.pdf
"ACQ"
http://isites.harvard.edu/fs/docs/icb.topic967858.files/ACQ%20Pressure%20Treated%20Wood%20and%20Lumber.pdf
Now here's the EPA warning to those men cutting and breathing the dust of all the chemicals listed above... Safety and Precautions When Working With CCA Alternatives
Handling and Disposal Recommendations
Wear a dust mask, gloves, and goggles when cutting or handling treated or untreated wood. Whenever possible perform these operations outdoors to avoid indoor accumulations or airborne sawdust.
After working with wood, wash exposed skin thoroughly.
Wash work clothes separately from other household clothing to avoid cross-contamination.
Do not use pressure-treated wood where it may come into direct or indirect contact with drinking water, except for uses involving incidental contact such as fresh water docks and bridges.
Do not use pressure-treated wood in circumstances where the preservative may become a component of food, animal feed, or beehives.
Do not use pressure-treated wood for mulch.
Do not burn pressure-treated wood in open fires or in stoves, fireplaces or residential boilers because toxic substances may be produced as part of the smoke and ashes.
Treated wood can be disposed of with regular municipal trash (i.e., municipal solid waste, not yard waste). Homeowners should contact the appropriate state and local agencies for further guidance on the disposal of treated wood.
Dispose of treated wood from commercial or industrial use (e.g., construction sites) by complying with local landfill rules. It can also be burned in commercial or industrial incinerators or boilers when done in accordance with state and federal regulations.
Richard,
I'm unconvinced. I think we'll just have to agree to disagree on this one.