Encapsulated crawl
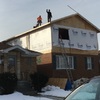
I’m looking for some suggestions and best practices. I just finished tearing off 3 layers of siding and 1X6 sheathing off of my hodge podge off an addition. I assume this portion of the house was originally an exterior porch that someone converted into living space. I poured a rat slab this afternoon and am getting ready to re-insulate and sheath and convert into an encapsulated crawl. I previously furred out the walls from the interior to accommodate thicker insulation. My plan is as follows. Insulate with R23 rockwool and use canned spray foam in the hard to reach spots, use foam board in any stud bays or rim joists that are not deep enough for rockwool. Replace sheathing with plywood and tape all seams, cover ply with a minimum of r8.5 foamboard also taped, housewrap over foamboard, then 1×3 furring strips, finally finished off with vinyl siding. I’ve decided that the new window will be an outie and door will be an innie. Did i miss a detail or is there perhaps a better approach to this? I am still debating on replacing the 3yr old steel door with fiberglass triple pane but have no idea what to do with access door to crawl. I have called a few local door manufacturers and no one is willing or capable of making a door that size(aprox 28wX36H) Thought of making my own out of PT 2X joined with some glue and pocket screws and backed with some foam board. and not sure of what foam board to use. I found some foil faced 1.5″ polyiso R9.3 but should the foil go towards the exterior? my local menards has eps in 2″ for much lower price buts it only an R8. All input is appreciated.
Raul
GBA Detail Library
A collection of one thousand construction details organized by climate and house part
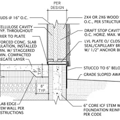
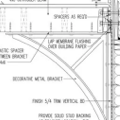
Replies
Hi Raul,
That's interesting construction. Seems like a hybrid with elements of a crawlspace, pier foundation, and balloon framing. Anyway, to give the most helpful information, we'll need to know where your home is located, and unless I missed it, you didn't mention that.
I am in chicago climate zone 5.
Interesting is an understatement. When I purchased the house the entire rear addition had pulled off the house due to inadequate footers(brick/cmu buried about 18") code calls for 42". I hence hand dug some 10" rounds and reinforced everything to the best of my abilities. With some 2x10s and 6x6s. Originally the rear addition had a shingled roof if was carrying but I since I cantilevered my second floor addition there is not much weight on it now basically a glorified deck without the snowload.
Raul
>"I found some foil faced 1.5″ polyiso R9.3 but should the foil go towards the exterior?"
Most foil faced polyiso is foil on both sides, but often only one side is shiny-bright. Where it's facing an air gap the low-E bright facer delivers an additional ~R1 to the assembly, but if laminated to slabs of plywood it doesn't.
There is no need to use pressure treated wood in the custom door assembly- it's not in ground contact, and given that it's under an overhang won't even get much direct wetting of the exterior.
The crawlspace needs to be ventilated with either indoor or outdoor air to meet code.
I can add supply or a return duct from my furnace would this suffice? The other option I contemplated was to create a pass through register on the floor. I really I would like to run a return through the crawl area to the dinette area above but with the ductwork only running through the space I dont believe it would meet the code. In theory heating the crawl would in turn heat the space above.
Raul