Economic viability of exterior rigid foam retrofit

Hey folks,
Over the years I’ve been improving our house in northern Colorado (Zone 5). We’ve insulated everything we can get to, air-sealed, and leakage should be down under 1.5ACH50 by now (1.6ACH50 at last test).
At this point the biggest remaining addressable weaknesses are the 2×4 walls, lack of housewrap, sliding glass door, and windows. I’ve done some modeling in BEOpt which pretty much confirms those are the main cause of heat loss at this point.
The clapboard siding is 15 years old & in pretty good shape, a little hail damage & a little swelling but otherwise healthy. So, I’m figuring my best plan is, in another 15 years or so, to do the windows, sliding door, housewrap, and everything all together when the siding needs replacement. (Would also be my opportunity to expose some inaccessible leak sites)
The big question I want to ask is how exterior rigid foam retrofits go in practice. It sounds simple enough, but I’m concerned about all the “gotchas”. In addition to retrimming doors & windows, we’d also have to adjust utility boxes, conduit, vent hoods, the fence line, a wall-mount gas fireplace exhaust, roof flashing, gutters, the list just goes on and on. There’s even a few places concrete was poured right up against the lowest board, effectively entombing it. (sticking to 1-2″ of foam might avoid a need to mess with the eaves & soffits) With enough time & money anything can be accomplished- but, to those of you who have done exterior rigid foam retrofits, how did it go? Did the “gotchas” snowball, or was it all easy enough? Did the project stay within a reasonable budget that will recoup its costs, or did you overrun your budget so much it will never break even?
I don’t have to make any decisions for a while, but I do wish to start budgeting.
GBA Detail Library
A collection of one thousand construction details organized by climate and house part
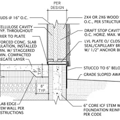
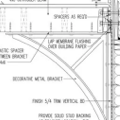
Replies
Hi Pshyvers,
I did all the work you have described and then some on the last house I owned. I didn't do any energy modeling nor track expenses or before and after utility bills too closely, nor did I calculate payback. The house needed new windows, doors, siding, trim, etc. anyway. So I just took the opportunity to improve performance because it seemed like the right thing to do.
You are right, it is a lot of work and fussy details. I also air sealed and insulated the attic floor, which is equally a lot of work and fussy details.
My utility bills came down quite a bit, though again, I can't say how much. More significantly, the house got a lot more comfortable.
Before the retrofit, the floors near exterior walls were cold and so were the corners of rooms with exterior walls. After the retrofit, the temp inside was much more even, floors were warmer, and the house heated very quickly, which allowed us to program the thermostat to much lower temps when we were away from home during the day and while we slept because it took only a few minutes to warm up in the morning or when we came home.
Looking back, I wish I had paid attention to before and after energy use, time and material costs, etc., but only because I'm curious. I would do it again even if the payback wasn't there.
Brian, thank you for the information. Did you do the work yourself? Another one of my concerns is that I don't have the broad background to do a good job on all of the details myself, while contractors tend to take shortcuts when there is a laundry list of fussy details. (Perhaps the answer there is just find a better contractor)
I did most of the work myself, except for some wiring and plumbing that was involved and called in some help when I needed extra hands. If you can't find a contractor who has either done this work before or is willing to do the research and learn new things, then you are better off doing it yourself, even if you are inexperienced and slow. It's important to get the details right or this work can just be a lot of time and money down the drain.
On an existing house a foam-over ONLY makes sense if the siding is failing (and that could take longer than you might be thinking) since re-siding is an expensive proposition. As a retrofit there is the additional expense of adjusting the window flashing details, which isn't always easy.
Using reclaimed foam is far greener and far cheaper than using new foam, given the high environmental footprints of both the polymer and in some cases the blowing agents. Using 30 year old pre- Montreal Protocol foam pulled off the roof of a commercial building can even exceed the performance of new foam, but the environmental hits have already been taken- re-use just piles on to the benefit side of the cost^benefit fulcrum.
Even post Montreal Protocol 2lb roofing polyiso can be presumed to be at least R4.5-R5/inch, and a couple inches on the exterior of a 2x4/R13 type wall would bring it up to current IRC code minimum performance. There are multiple vendors of reclaimed, factory seconds, and surplus foam board in Colorado. Repurposed Materials Inc has a facility the Denver area and often gets used roofing foam in, but there are others. Currently they aren't showing any in their Colorado outlet though they have some at other locations at about $17 for a 2" x 4' x 8' sheet sold in pallets of 24 sheets, which is their typical pricing: https://www.repurposedmaterialsinc.com/polyiso-insulation/
But there are others. Run this search on your local craigslist from time to time- it's' out there, and it improves the economic viability & verditude of the project by quite a bit:
https://denver.craigslist.org/search/sss?query=rigid+insulation
Thanks, I tend to forget about the option of reclaimed foam board (perhaps because I'm always slicing it up into pieces?). You're right that it is an excellent option.
As you say, it will probably be quite a while until the siding needs replacement, and I have no intention of pulling it off until then. The windows, too, are in good shape. So, it's quite possible I'm getting ahead of myself!
>"As you say, it will probably be quite a while until the siding needs replacement, and I have no intention of pulling it off until then. The windows, too, are in good shape. So, it's quite possible I'm getting ahead of myself!"
Aren't we all?
My house has 97 year old cedar clapboards in decent shape, and fairly tight (with a couple of exceptions) wood sashed 97 year old single pane windows behind ~35 year old reasonably tight triple track clear glass storm windows. Even reglazing the storms with low-E glass doesn't pencil out- there is still other lowering hanging fruit on the building-upgrade for comfort & efficiency & carbon reduction trees.
Capping off the connection to the gas grid, going with heat pumps and continuing to buy 100% renewable power (MA is a electricity decoupled state- I can buy from a wide number of generators) would be a cheaper and more effective/cost-effective carbon-reduction strategy for my house than a foam-over with new windows & new siding. YMMV.
The carbon footprint of any improvements matters, since near zero carb energy can be had simply with changes in the mechanical systems in my area, and that's likely to be the case in most of Colorado in the coming few decades, since PV + storage is already cheaper than keeping coal plants or fast ramping gas peakers running in your area, and utility scale wind is starting to encroach on combined cycle gas (having blown away the cost of coal power in the past decade).
At the current rate of climate change in 50 years my house will be in zone 4A rather than 5A, with lower total energy needs even if nothing more is done to improve the building's thermal performance. I'm still planning to put a few inches of used foam above the roof deck when it's time to reroof, given that I'm in a maritime snow cement mixer zone with significant ice damming potential. We get 10 feet of snow in some years, at an average snow density 2-3x what's typical in the Front Range. With full-dimension 2x6 rafters over much of the mostly cathedralized ceiling roof 4-5" of used polyiso will make a real difference in ice dams, but a much lesser dent on energy use, and zero effect on operational carbon footprint once the conversions away from gas toward heat pumps is complete.
Which comes first is still up in the air. The roof foam-over seems most likely to be the next major house upgrade right now, but if the boiler suddenly craps out heat pumps may immediately end up on the front-burner (as it were... :-) ) Even though plans are guaranteed to change with changing circumstance, it's always good to have a prioritized plan, updated it as-needed. (Of course mi esposa may have other, different priories...)
I had a very similar experience to Brian, above. The things that I would point out, based on my experience:
- Agree that paying for this work is expensive. It's most of the work of new construction with the troubleshooting of doing things a new way. I did everything myself.
- I have wood siding that I pulled off and reused. I'm having mold growth on the side that gets driven rain. To do it again, I would have done a rain screen (still might on that one wall). Such an easy bit of insurance.
- I am in the San Francisco bay area, so mild climate. Still, the house is much more comfortable. I wish, like Brian, I instrumented it more.
- I added shear walls, using a ton of caulk to seal every board to the studs and to each other. It was a big difference in sound reduction, so I must not have messed up air sealing too bad.
- I did 2" polyiso over the shear walls. All joints taped with foil tape.
- If I did it again, I would try zip and fluid applied for the joints.
- I needed to install an HRV after I did this. The humidity would drive up in the winter, worse than it did before. I guess pre-sealing, the house "breathed" well. The HRV is amazing. Just a simple Broan unit, but it works.