Durability issues with dense-pack cellulose wrapped around a timberframe?

Hello All.
I’m currently designing a home for a client. That the home will be Timber-Framed is a given, and I will cut the frame myself. An exterior stucco finish is required to match existing buildings.The climate zone is 6b (I’m in British Columbia, Canada, but not coastal).
Project goals include energy efficiency and durability of construction, of course. Finding (or developing) an elegant solution to the problem of enclosing the Timber-Frame structure is my main focus at the moment. I’ve read many relevant posts here on GBA, but so far haven’t found quite what I’m looking for.
DETAILS: This is the concept, from inside out, so far:
-8×8 Timber posts, with latex-painted, (vapor-retarder) drywalled 2×4 infill walls set flush to Post exterior. (I’m hoping to replace most or all exterior-wall knee braces with these sheathed infill walls)
The 2×4 wall provides a chase for wiring.
-1/2″ plywood sheathing wrapping entire frame, and tying 2×4 walls to structural posts. Taped seams to create an air barrier. ( seems much simpler than trying to detail an infill airtight drywall approach)
-Larson/Riversong truss type exterior wall, using 2×3’s or 2×4’s (sitting on extended mud sill, cantilevered floor deck or braced down to foundation wall…not sure yet). I’m thinking to hang this exterior wall from cantilevered TJI rafter tails, so I think I’ll need minimal support at the base. Instead of the plywood gussets typically used, I may use a spacer between outer wall and plywood sheathing. I’m thinking about pieces of ABS plastic pipe, 1″ in diameter, with a long GRK screw through the middle and into the timbers or studs. I would consider filling the plastic pipe with foam as well. This would hold the two walls together, without having to butcher my air-barrier sheathing and wouldn’t create to much thermal bridging.
-Cavity would be filled with dense-pack cellulose. Cavity width will be between 10″-12″
-exterior sheathing (either plywood or re-used 1×8’s from the foundation form work. Could be nailed diagonally, though I’m not sure that more bracing is needed.)
-Housewrap
-back-vented & drained 3-coat stucco finish.
So far, this is where I’m at. I want to create a durable wall assembly that is relatively easy to detail. I want to achieve some level of material efficiency as well, but not at the cost of durability. This seems to me to be a vapor-open assembly, allowing drying to both the interior and the exterior. There are 2 relatively easy-to-detail air barriers as well, cutting down on both wind-washing and interior air-leakage vapor transport. Ventilation will play a role in moisture management as well.
I’m hoping for some feedback on this. If anyone sees holes/flaws in my thinking, or a simpler way to do things, please fire away. I would rather my wall-assembly theory fail than the house I’m preparing to build!
Nick Furfaro
GBA Detail Library
A collection of one thousand construction details organized by climate and house part
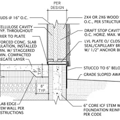
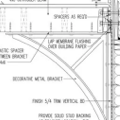
Replies
Nick,
It all sounds workable, though I would probably substitute #15 felt for the weather barrier over the outer sheathing, and prefer boards to plywood for breatheability. Since the housewrap will be in the cold zone, it can trap liquid condensate behind it - felt will allow outward diffusion of liquid.
And the key to durability of this system will be in how you define and detail "back-vented & drained 3-coat stucco finish". Cement stucco is not very vapor open (it's known to rot straw-bale walls, for example), so a well-vented cavity open to the outside will be necessary for good drying potential.
I would also have some concerns about the shear resistance of 12" or 14" screws, and would not rely only on the connection at the rafter tails. I would make sure there is good bottom support as well.
Here is a blog on proper stucco detailing
https://www.greenbuildingadvisor.com/blogs/dept/musings/install-stucco-right-include-air-gap
I'd be curious to hear feedback from you if you pursue the GRK screw route. Advisable to run that past a structural engineer.
See this blog on that topic - https://www.greenbuildingadvisor.com/blogs/dept/musings/fastening-furring-strips-foam-sheathed-wall
I think in addition if you haven't executed a thick wall of dense pac before you should get more info on procedures to ensure proper and consistent density. RRiversong is a good resource concerning this.
Thanks Robert and J. I appreciate the feedback. My hunch was to support the outer wall at its base as well, and you helped me to confirm that. Also, I remember from my home building experience on Vancouver Island that diagonal board sheathing and double-layer felt was the preferred method in the high-end custom market...and in a very wet climate. It's drier here, but I think I'll go that route anyway for some extra insurance.
As for the "vented and drained" stucco, I was thinking about using a plastic drainage mat to create a gap. After reading numerous articles and blog entries, including the link you posted,J, and this one,
(Building Science Insights-BSI-038: Mind the Gap, Eh! By Joseph Lstiburek )
I'm aware of the potential for disaster with improperly detailed stucco, and will be diligent in my specifications with regards to this area!
As far as the GRK screws go... I think that with both top (rafter-tail) support and bottom support which carries loads directly to the foundation, the GRK's will only be asked to serve the role of spacers, preventing the outer wall from moving in or out...though I doubt that it could move inwards with the cavity full of Dense-Pack... Also, plywood boxes at door and window openings will tie the walls together.
As far as dense-pack insulation goes, I intend to hire an experienced professional. There are no contractors locally, but I know of one company involved in the construction of numerous double-wall net-zero homes near Edmonton, Alberta (not so far away!). I won't be trying to do the installation myself, as I would with fiberglass, but I think the extra installation costs are worth it for the durability of the finished product.
Thanks to both of you for your input.
Nick,
Don't forget to seal all joints in the plywood window boxes - including to the plywood sheathing - since they are part of the air barrier.
And, if you want the look of timber knee braces, they can always be moved to the inside face of the exterior posts (they'd have to be 3" material to leave room for infill walls and drywall finishing).
Nick- What part of the BC interior? Do you have seismic issues? Will the structure be permitted?
As I understand your wall build, you'll have sheet rock attached to the outside of the timber frame, with what is essentially a shear wall outside of that, so that knee braces can be eliminated. The connection between the timber frame and the shear wall is key to rigidity here, and engineers often get twitchy about having anything (even 1/2" of sheet rock) between the sheer panel and the timber, as it creates a bending moment on the fastener. We have overcome this issue by furring out the shear wall on plywood strips the same thickness as the GWB (generally a 4" wide strip centred on the back of an 8" timber is sufficient; if it's done properly the GWB can be slipped in to the space from the inside after lock-up), so that there is no opportunity for bending in the fastener.
Good luck,
Chris Koehn
TimberGuides Design & Build
Robert,
Good advice on the window box air-sealing.
As for the braces, I had considered shifting them to the interior face, and will probably do so if : The client demands exterior wall-braces, or if there isn't enough plywood remaining after cutting window openings to provide sufficient bracing. I'd like to avoid having braces in front of windows if I can.
Thanks again
Chris,
Actually, my plan is to install shear-wall infill panels, between the posts, with 1/2" plywood sheathing covering both shear-walls and posts. Drywall will be installed on the inside of the shear walls, between the posts. I'll leave a gap between the drywall and the timbers, and a trim piece attached to the post but not the drywall will allow wood movement without drywall cracking (In theory)
Hope this clarifies my wall design somewhat.
Nick, surrounding wet timbers with infilled walls has caused moisture issues for some. A builder friend has built timber frames his whole life and believe me, there is much that you will learn as you put some time in your pursuit.
May your timbers dry, mold and moisture free.
AJ,
I appreciate the heads-up regarding wet timbers. I'll be using air dried, free-of-heart Douglas Fir to try to minimize risks associated with moisture content and movement. While the timbers will likely not be dried to their full potential, they definitely won't be green. Ideally I would raise the frame and roof it immediately to protect from rain, but I still need to work out the details of the wall/roof intersections and the dense-pack cellulose installation.
Nick,
I'd like to make two comments in regard the dense pack cellulose.
The density is crucial to avoid settling. It must be at least 3.5 pcf.
Use an all borate treated product. My manufacturer recommendations specify only all borate in enclosed cavities.
Bohdan Boyko
Bldg Sc Mgr Greenfiber
Bohdan,
Thanks for the input. My goal now is to find an experienced contractor to blow in the cellulose for me. So far I haven't had much luck in finding anyone in South-eastern B.C, but my search continues.
Nick,
Even if your timbers were green, there would be no moisture problems created by your wall plan. Large timbers require years to fully equilibrate to indoor humidity conditions and so release moisture very slowly and mostly at the endgrain.
And cellulose should not settle at anything more than 3 pcf installed density. Its gravity settled density in an attic loose-fill application is no more than 1.5 pcf, so doubling that density makes it virtually impossible to settle.
Robert,
Your thoughts on the drying of large timbers echos what I've learned over the years, particularly in regard to the endgrain being the location where most of the drying occurs.
I'm now thinking through the cellulose installation. I'm considering framing the walls and sheathing them with boards, and then getting the roof on next. If I leave some sheathing boards off, The cellulose could be blown from the outside, avoiding the need to punch through my plywood Air Barrier. I'm thinking that this is probably the only way to go for this wall build-up, but I'll have to discuss this with the contractor when I find one.
Nick,
I generally prefer board sheathing over plywood, but where would your air barrier be then? It seemed like the plywood approach made sense for air tightness. Easy enough to drill holes in the plywood and fill with plugs.
Robert,
If you review my initial post, you'll see my wall build-up involves 2 sheathing layers; The inner layer of plywood acts as both Air barrier and shear bracing, and the outer layer of board sheathing provides support for drained and back-vented stucco. If my structure weren't a timberframe, I could do away with the inner layer of plywood, but as it is, this seems to be the simplest place to locate an air barrier, and it also make knee-braces in the plane of the exterior wall redundant (well, at least some of them...)