Drywallers damaging air/vapor membrane while hanging sheets

I’d love some help resolving an issue for our new build in Coastal Maine, Climate zone 6a. It’s a 2 story 20×40 2bed home 1600sqft total. The floor system between first and second floor is a timber frame, visible from below. The wall assembly from inside to out is cedar, cedar breather, zip R6, 2×8 framing with dense pack timber hp, rothoblaas clima 145, 1/2″ drywall. The second floor has a 5′ kneewall, a 4′ sloped section that is dense packed to R55, and a flat ceiling that is loose filled to R60. There are accuvent baffles from the kneewall to above the R60 loose fill, and the rest of the attic is unconditioned and well vented.
There is rothoblaas on the interior of all exterior walls, and sloped ceiling and flat ceiling. There is no strapping between framing/membrane and drywall.
We had local insulators install dense pack and loose fill TimberHp, and use Rothoblaas Clima 145 as interior vapor retarder and air barrier*.
*There’s a nuance here – as the builder and I never really set a clear distinction to the primary air barrier. (I know…I know..) The exterior is taped Zip, but doesn’t tie continuously to ceiling rothoblaas over the second floor top plate with tape/membrane. There are sealed accuvent baffles between the top plate and the flat portion of the attic on the sloped section of the ceiling. Additionally, the rothoblaas membrane doesn’t extend between interior wall partitions, nor does it extend between the first and second floor due to timber frame aspect. It either wraps around the corner transitions for the interior wall partitions, or terminates with tape at timbers, etc. The drywall also does not extend behind interior wall partitions, or between first and second floor. It can, however, be fairly easy to detail airtight with mud and tape – especially on the ceiling – as there are minimal wire penetrations for surface mount lights and otherwise just adjustable outlet boxes on the walls that could be sealed*
According to the drywallers, the insulators put the rothoblaas on too tight, and in order to install the wallboard, at some transitions, they had to rotozip through the membrane to get the wallboard to sit properly and hit a stud. The damage is mostly on the second floor ceiling, where the kneewall transitions to the slope, and at a few corners of wall partitions.
The drywallers are, of course, very reluctant to pull the sheets so I can retape. They are blaming the insulators for sloppy work. They want to start mudding and taping next week – so I have to decide quickly.
Assuming the gaps between the drywall are big enough to get a caulk gun or foam nozzle in, could this be a good alternative to pulling the sheets? I have an email pending with Rothoblaas technical advisor asking this question.
Should I just rely on drywall to be the primary air barrier anyways?
Should I ask the drywallers pull the sheets to retape? Do I run the chance of doing more damage? This would set the timeline back even further, and seeing as the membrane isn’t completely continuous anyways, is this unnecessary?
Are multiple non-continuous air barriers better then one non-continuous air barrier?
Thanks so much, look forward to the candor.
GBA Detail Library
A collection of one thousand construction details organized by climate and house part
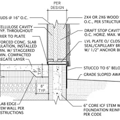
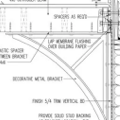
Replies
> Should I just rely on drywall to be the primary air barrier anyways?
Drywall isn't an air barrier for the simple reason that it has many penetrations cut out for every lightswitch and outlet. It can also shrink and crack over time.
> Are multiple non-continuous air barriers better then one non-continuous air barrier?
In recently took the CPHT course and the instructor used the metaphor of "a leaky bucket inside of a leaky bucket" which still has the effect of leaking water.
I've never been in this situation myself, but I think the only course of action is for your to get involved and do the repair work on that section of the membrane, and to the finish drywall on top. The drywall team, it seems, does not care about your high-performance ambitions — they just want to tick boxes and be done. So you can wait until they finish all tape and mud, or you can sneak in and do it now. But this is the kind of thing that a GC often has to fix themselves because it falls in between the state duties of each speciality trade.
Thanks Scott, appreciate the reply. That's a great metaphor and super helpful to visualize. Without doing tests myself, "a leaky bucket inside of a leaky bucket" is probably going to leak slower then just one leaky bucket...
At the risk of sounding harsh, you've done just about everything wrong, and now want us to choose the least worst option for you? That's not easy to do. It's also going to be hard for you to do anything meaningful with the drywallers breathing down your neck. It might be a good time to step and take a breath before continuing hell-bent to get 'er done.
Your best bet right now might be to find a local company that does energy upgrades and retrofits. They have the tools and skillset to improve the performance of existing construction and with drywall already installed, that's what you have. The goal would be to measure and improve your air barrier before it is really too late. A blower door test would be a mandatory starting point. You will have to pick an air tightness goal. You will probably not be able to get down to the 1 ACH range that most high-performance houses aim for, but 2-3 ACH might be doable and still a bit better than current code. If you run the test and you're already in that range, that's great. Some strategic sealing will only help. If you're way out of that range, you will have some thinking to do. Are there simple improvements you can make? Will detailing the drywall to be airtight help? Is it worth taking some things apart to make improvements? These questions cannot be answered without a blower door test, probably followed closely by blower door directed air sealing.
It will take some time finding an energy performance contractor and getting them in to do their work, but without that, you're just guessing.
Peter - yes, "you've done just about everything wrong" does indeed come off harsh. I think there are probably better ways of saying what you are trying to say. I think it's clear from my post that I know that we have made many mistakes, and that I'm not asking for you all to solve any of my problems - just looking for suggestions from the hive mind. I wonder why people on this site choose to be unkind, rather than just saying nothing at all...
That being said, the rest of your reply does have some substance, which I appreciate. The blowerdoor before drywall was 2.6ach50 and this was before tightening up some of the transitions between the rothoblaas and the timbers. Also, four lunos fans were not installed, and the open housing was not sealed well. Additionally, there was still a 3'x3' hole in the first floor slab where the plumber was finishing up plumbing for the tub/shower and I believe this was a big draw of air when we depressurized the house.
You might be a good candidate for aerobarrier if your blower door comes back no good.
Excellent idea. This is the local Aerobarrier contractor: https://lordbuildingsolutions.com/.
Michael and Freyr, Thanks so much!
I was actually already following this thought train, and Michael, funny enough, just got off the phone with Alex from Lord Building Solutions.
My hesitancy to invest in this service was because of the exposed timber frame details and finish concrete floor, as these would increase the sq ft cost.
It isn't cheap, but he basically guaranteed that he could take me from 2.6ach50 to passive levels, if that's where I wanted to go.
I was just discussing the pros and cons of the Aerobarrier approach yesterday at a green building conference in Boston, including concerns about the particulate matter. The gist, among builders already routinely getting well below 1.0 ACH50 blower door numbers, was that it fills an important gap in the industry (no pun intended) and that with enough planning and trained builders, it shouldn't be necessary, but that the planning and training are not as wide-spread as they should be.
Consider it an expensive lesson and next time be sure you can draw a single, continuous red line around your entire building section to represent your air control layer!
"Consider it an expensive lesson" HA! I could have probably funded a year of the finest engineering or architecture school with all the expensive dumb lessons from this project... and still had some left over for lunch. Absolutely could have paid for tickets to the NESEA conference and a fancy hotel room in boston...
I've read many of the threads on aerobarrier on GBA. Are there any new or profound concerns about the particulate matter?
Thanks Michael!
I did AeroBarrier on a house that was new construction but for regulatory reasons the foundation of the predecessor house has to be kept, which created a complicated footprint that was hard to seal. The salesman told me the same thing, we can go as low as you want to go.
When it was applied, they pumped in nine gallons of caulk, then the guy running the machine said he was no longer seeing improvement. Final reading was 1.4, down from 4+. Which is excellent, there's no reason not to be happy other than the expectation that had been raised.
Cost was about $3500 for a 4400 SF house.
Thanks DC,
The quote I got was for $2100, plus an extra $700 to plastic off the finished t+g decking on the first floor ceiling, and the finish concrete slab.
This is for going from 3 ACH50 to 1ACH50. I wonder what the ROI would be for this? With heating load loss over time? Or am I looking at that wrong?
Join the club! Unfortunately homes are complicated, there are many ways to build them and new products and techniques reaching the market all the time, so if you're trying to keep up on best practices, you'll make some mistakes. My job is partly to try to get ahead of those mistakes but there seems to be one surprise or another on every project.
I haven't read or heard anything specifically negative about the Aerobarrier spray. I don't think it's something you want to inhale, but otherwise, from what I understand it's an acrylic product and pretty benign once installed.
Thanks Michael,
Curious if there's anyway the aerobarrier could do unforeseen damage in the long run? eg, Fentrim tape on the windows? They're Salamander tilt/turn, barrier taped on bottom per PBSupplies details.
Ian,
I suspect the damage to the membrane will not cause any real problems that weren't already there in the way the membrane was installed initially. Drywall isn't a good air-barrier on its own, but where the damage has occurred is also where the drywall will be fastened to the framing, and will compress the area underneath, so I doubt there will be much if any additional air-leakage there.
Drywall is an excellent air barrier on its own; in fact it is used as the definition of an air barrier. The problem is the penetrations in the drywall, and sometimes the transitions. An interior membrane that is not detailed specifically as an air barrier will have the same penetrations as the drywall. So I agree that there won't be a big difference in air leakage.
Michael,
I should have said: Drywall isn't a good air-barrier unless it is detailed as such.
As neither the drywall, sheathing or membrane look like they can be relied on to function effectively as air-barriers, Aerobarrier is probably a good solution.
Thanks Malcom,
Yes. I understand the flaws with the initial membrane installation. I wish this article had been posted when we were framing!
https://www.greenbuildingadvisor.com/article/installing-an-interior-air-barrier
Thanks for your reply
For those on the edge of their seats... I heard back from Rothoblaas and they suggested using their canned Hermetic foam product to spot seal the sliced areas that were accessible.
They also suggested Aerobarrier for the same reasons detailed above.
@ $2700 for Aerobarrier, I wonder what the ROI for going from ACH3 to ACH1 would be?
I also wonder if there are examples with building assemblies where Aerobarrier would actually do potential future damage, then good, due to it's indiscriminately non-targeted approach?
On a recent energy model of a similarly-sized home in climate zone 6, I found that going from 3 ACH50 to 1 ACH50 would save about $175/yr in energy costs. That's roughly a 15-year payback or a 6.5% simple ROI, or a higher ROI if you include inflation, likely increases in energy costs and compounding returns. It's safer than the stock market for returns in the same ballpark, plus there are ancillary benefits.
I can't think of any downsides to making your house tight, as long as you have mechanical ventilation, no combustion appliances, etc.. I haven't used it yet but I've been paying close attention since it hit the market and I haven't heard a single horror story on projects where proper protection was done (taping off finished surfaces, etc.)
Thanks so much for your thoughtful responses Michael. I really appreciate it.
Ian_plum,
I can't think of a building assembly where inhibiting air-movement would be detrimental. We do introduce ventilated gaps in walls and roofs, but those are outside the air-barrier.
Thanks Malcolm!