Double wythe CMU vs. Thermomass

After living in Europe for several years I have become a fan of concrete. I build in the Southeast and have mainly used concrete commercially and as stem/foundation/retaining walls and for slabs in residential.
I know that concrete is expensive compared to the “normal” enclosure for a home here (platform framed,2Xwall,sheathing, cementious siding). I have been following the debate on Thermal Benefits of Mass Walls and conclude that its effects are minimal if any in Zone 3, also the overuse of “effective R-value” in advertising as a reason for higher mass walls, is a non-starter with me, as it is not backed up by scientific facts.
Here is the thing about concrete, it is durable as hell. Joe L. uses CMU in his “perfect Wall” 500 year wall. I really doubt current, affordable framing stock would last so long, and this claim by Matt Risinger of 500 year wood framed structure is at odds with what BS Corp. was stating:
I think it is disingenuous to claim a persist/remote wood framed wall could last so long (BTW what is the guarantee on that house).
I was in Czechoslovakia in 1993 and met a great Czech Entrepreneur that was selling German manufactured panelized tilt-up homes (he had failed in the market with stick built homes as no one believed in their durability). One thing he said to me about 20 years ago still sticks in my mind. I asked about the porcelain roof tiles and he said they come with a 100 year guarantee (same as all the structural parts of the house) from a company in business for about 300 years. He then looked at me and asked what type of guarantees we in America give on our houses and I said frankly, i don’t know many builders that like to guarantee their structures at all. I told him once the house is sold, unless it is an ongoing large home builder concern that guarantees were not given usually. He was shocked.
This idea of durability has been in my mind ever since. I live in a part of the country with epidemic mold issues, a High decay (of wood) coefficient, now Formosan termites, carpenter bees, carpenter ants, etc.
I had decided to build my latest spec house out of the thermomass system: http://www.thermomass.com/
As the house is modern in design, I also had decided to use many of my commercial techniques on it, steel trusses, decked and poured floor.
I am sure that many of the builders on here have had to “educate” framing and finish crews about proper detailing on framing and enclosure for stick built. Most of the crews I have educated in the last 20 years have been from Mexico, Latin, and South America. One day I struck up a conversation with a framer who confided in me he had only been framing for @ 3 months and was still a rookie, but in mexico he was considered a very skilled builder. He said that if I was building the house with Concrete or CMU or stuccoing it he was not a “rookie” at those things as that is how houses in Mexico (and most of the word are constructed). I thought what a waste to educate this guy on how we stick build instead of exploiting his built-up knowledge in masonry/concrete. After that I started to ask all my trades people from other countries what building skills they were competent in, most frankly stated, “concrete, clay tile, CMU, stucco”.
I am not sure if it is true but I have been told that if you are a Cook/Chef in China and you move to the USA, you have to learn to “cook” all over as our Chinese food bears little to no resemblance to Chinese food as prepared in China. This seemed the exact parallel to the Mexican builder that must “start-over” here learning stick-built.
I am interested in a few things when building a house; cost-effective, high quality, durable, simplified structures. To that end, if i were to emulate the 500 year wall a la Joe L. I would use CMU or concrete then foam/insulation then an external elements/rain barrier (in his example brick).
I have several questions for you guys:
1. instead of the very expensive Thermomass system, could I not just build an engineered CMU interior wall, stucco/glue 3′ of XPS on the face of that wall, then, without a drain plane build another external engineered CMU wall and stucco/parge it smooth with acrylic and waterproofing additves?
2. If the external cladding in a 500 year wall is waterproofed by design, then is a drain gap necessary?
3. Do metal wall ties really cause a huge thermal energy penalty? Anyone aware of a cost effective composite wall tie?
4. this double wythe wall would have all utilities place in the internal wall during construction and be smooth stuccoed on the inside with no vapor barrier to allow drying inward, as such wouldn’t the external waterproof stucco and the xps both act as protection against external solar and or wind driven rain penetration to the structure?
Thanks for all the insights here, I am glad I found a place to ask these questions and to try to come up with more meaningful techniques.
GBA Detail Library
A collection of one thousand construction details organized by climate and house part
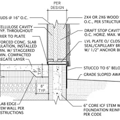
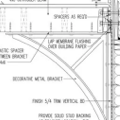
Replies
The vapor barrier is the water sealer depending on it's perm rating and moisture content. Which one are you considering?
Are you considering double CMU to use the outer wyth as structural and inner as insulating (more of an aerated CMU) ? What you are describing is a structural insulated panel(sip), or sandwich construction made of concrete which is MUCH stronger than the wood version.
If so, type SA mortar as the inner binder to the ACC and XPS will allow inner drying and breathing-mass effect of the inner wall, type S for the outers. The lime will absorb CO2, MG strengthen the bond...you might add some portland cement to the mortar structural wyth-xps, follow lable, not much 10%.
Sounds labor intensive have to done a cost study, put together a test sample. Test the foam brake with a heat source to get a thickness.
Leo,
The wall system you envision will work. The rigid foam layer in the center of the wall acts as a barrier to liquid water, a vapor retarder, and insulation. The main disadvantage is the high cost.
Plenty of manufacturers have developed concrete sandwich panels that are easier and less expensive to build than the wall you describe. Most of these systems have a layer of rigid foam with welded-wire mesh on both side of the foam. Once the foam panels are erected, they are finished with shotcrete on both sides.
Other manufacturers make concrete panel systems that resemble Thermomass.
The last time I wrote an article on these systems, I came up with lots of manufacturers, including 3D Panel Systems, Hadrian TriDi Systems, All Wall, Monotech, Solarcrete, Dukane Double Wall, and Thermomass (which you mention).
Do you by any chance have a link to that article, Martin? I'd like to read it.
Nathaniel,
The article, "Encasing Polystyrene Walls in Concrete," appeared in the April 2004 issue of Energy Design Update Unfortunately, it is not available online.
Here are some excerpts:
"Insulated concrete forms (ICFs) sandwich a layer of concrete between outer layers of polystyrene. To many building scientists, such walls are inside-out. For a variety of reasons, it makes more sense to sandwich a layer of polystyrene between outer layers of concrete: that way, half of the wall’s concrete mass is in thermal contact with the conditioned space; the vulnerable insulation is protected by a durable shell; and the need for finish materials is greatly reduced.
"Such wall systems exist. At least six US companies sell wall systems that sandwich a polystyrene core between outer layers of concrete or a cementitious coating: 3D Panel Systems, Hadrian TriDi Systems, All Wall, Monotech, Solarcrete, and T-Mass. Since all of these wall systems have rigid foam cores, they share some of the characteristics of structural insulated panels (SIPs), including above-average whole-wall R-values. But while SIPs have outer layers of OSB, which is vulnerable to rot, concrete-encased walls are inherently rot-proof. Moreover, while SIP walls have seams that require careful air sealing, most concrete-encased walls have no seams except at doors, windows, and penetrations.
"...Homes built with these wall systems, like other concrete buildings, are unusually resistant to fire, wind, and seismic activity. Most of the wall systems described in this article have a 1 1/2-hour or 2-hour fire rating.
"...Two manufacturers, 3-D Panel and Hadrian TriDi Systems, produce wall panels incorporating a polystyrene core sandwiched between two layers of welded-wire mesh. Once the panels are erected on site, they are coated inside and out with shotcrete.
"At the factory, the polystyrene core is sandwiched between two layers of 11-gauge 2” by 2” welded-wire steel mesh. The mesh layers are connected by a series of steel or plastic connectors that pierce the polystyrene, creating a three-dimensional cage with the foam at the center; the mesh stands about 3/4 inch proud of the foam. While Hadrian TriDi Systems uses steel connectors, 3-D Panel uses plastic connectors to reduce thermal bridging. The wall panels are erected on a concrete footing or slab. The manufacturer specifies that vertical #3 rebar stubs, 24 inches on center, should protrude about 16 inches out of the concrete along all of the exterior walls. The panels are relatively light, and are usually lifted by hand over the rebar stubs, which fit between the polystyrene core and one of the layers of mesh. Once plumb, the panels are secured with temporary diagonal braces. Seams between panels are then covered with strips of 2” by 2” splicing mesh; when installed at inside or outside corners, the strips of splicing mesh include a 90-degree bend.
"...Once the panels are plumb and braced and conduit has been installed, the mesh on both sides of the panels is coated with a 1 1/2-inch to 3-inch thick layer of shotcrete or gunite, with or without plastic fiber reinforcement..."
Most I have seen look at SCIP have a hard time finding a qualified dry-shotcrete sub...It's high skilled labor. I can't even find shotcrete equipment to rent here to try it out, the equipment is high maintenance, cleaning, etc...I may purchase my own, most pool companies own theirs. The pool guy's probably never of heard of building a home like this, or SCIP, so even they will need some training.
A builder I talk to in Denver said his home never got below 65 F no hvac during the winter build, unlike his stick homes. He said back then his wall-roof cost was around 10% higher, but his HVAC dropped: http://simsbuilt.com/SCIP_System.html Interesting since that is in-line with the ORNL c-mass calculator that clearly shows a higher benefit, or "DBMS", for SCIP compared to ICF/Stick.
He tried building his own panels, said it was too labor intensive for a one-off. Here is how,
https://www.youtube.com/watch?v=RR9nHNukj6o&playnext_from=TL&videos=3NiSyA7QYrs
He used GCT: http://67.205.102.169/~trabajos/gulf/, they've dominated the market a while now (surprised you missed them Martin), others have folded. Metrock was another big player now folded that sell you a portable job site jig and for site manufacturing for around $80K. You'll need a PE, code or no code. There is no doubt due to the monolithic skins over core this is much stronger than mortared CMU's, and if you can get past the shotcrete skill set required, less costly of a path shipping in a manufactured product. If I were doing production homes, I build the panels myself....which I am strongly considering for my roof, or steel.
Gigacrete is another......Las Vegas
@Martin, @Terry, I have stumbled (I am a little behind the curve) on CSIPs using MgO and either EPS or PolyIiso. They are even using them for floor panels. I have always been skid-dish about SIPS using OSB since I have had to replace a bunch of rotted/compromised OSB which was only a few years old.
Have you seen these panels? Any hesitations? I am rethinking SIPS now. i wonder if you can tape and parge directly over these externally, after water sealing them.
@Terry - I agree on the shotcrete thing, I have been looking at "3D panel systems" for about 10 years now but could never find a good shotcrete crew that would guarantee a high level / quality finish. I also have some issues with the massively thermally conductive galvanized wiring thru-struts.
New member here. I'm sure this will stir up a hornets nest...just my two cents...
Wanting to build a Thermomass house in New York. Been wanting to do it since 2006 when I was first introduced to the system. I like its strength, resiliency to disasters (i.e. fire, hurricanes, tornadoes), ease of maintenance, and thermal performance. Stucco or stone veneer the exterior, cement wash or plaster the interior. What am I missing here???
Everything that Leo says in his first post are my reasons for wanting to do it. Yes, manufacturing concrete and steel produces carbon, but a concrete structure is going to last - "once and done". I think its better to build a structure that will last centuries requiring minimal maintenance as compared to the typical wood frame structures we build here. There are masonry structures in Europe that are a thousand years old.
I'm also concerned that we'll be here 20 years from now talking about all of these fancy double wall stick frame structures - too many variables - need to be perfect to not have moisture issues. The woes of EIFS come to mind.
My buddy's brother-in-law was visiting from Germany while I was building my first house. I can still hear him in his thick German accent..."You build paper houses here in America". Ain't that the truth! I think we would all be better off if every architect and engineer had to spend a semester as an intern in the building trades in Europe as part of their training.