Double wall with cellulose and zip sheathing in the NW?

I’m slowly getting rid to build a house in Seattle (zone 4c) and have a wall system I think would work well, but wanted feedback:
Cladding (hardi-panel) on furring (rainscreen) on building-wrap (tyvek or similar) on zip sheathing (taped) over a 12″ thick 2×4 double wall (staggered?) filled with dense-pack cellulose with drywall finish.
I know the zip system is a WRB but I would be using it mostly as an air-barrier and preferring the mechanical joint of lapped building wrap to a chemical joint of the zip tape (although that would be a backup). I think for the cost of the house it would be a small up-charge.
I was wondering about the zip system, though: why is it based on OSB rather than ply? I know (especially in the NW) OSB is riskier than plywood but does the zip system eliminate that worry?
Also, I was thinking about adding 2 wythes (correct use?) of counter-batten 2x2s between the double-wall and drywall (similar to a mooney wall). It could act as a chase for wiring/piping outside of the insulation without having to drill through studs and also let you install mesh netting over the studs to visually see the cellulose installation without having to worry about the insulation bulging out. It increases the total wall thickness (excluding rainscreen) to 15″ but I can deal with that in the plan layout.
Is there a concern about the sheathing getting too cold and being — basically — OSB?
Is the building-wrap over zip redundant or useful?
Does the idea of battens on the interior seem good or are there problems with it?
Thanks in advance.
GBA Detail Library
A collection of one thousand construction details organized by climate and house part
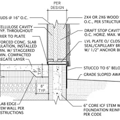
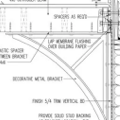
Replies
Daniel,
Q. "I know (especially in the NW) OSB is riskier than plywood but does the zip system eliminate that worry?"
A. If you are building a house, worries are endless. There's always yoga and meditation. Seriously -- no one knows how the Zip System OSB will hold up in the long run.
Q. "Does the idea of battens on the interior seem good or are there problems with it?"
A. I don't think you need double battens to create a service cavity; a single layer of horizontal 2-bys should be enough. For more information on service cavities, see Service Cavities for Wiring and Plumbing.
Would plywood with taped seams offer a reasonable air barrier while not having to worry about OSB siding or would it still not be enough and have to be combined with an air-tight drywall approach, or something?
If you were only going to use 1 layer of 2x's for the service cavity, would they even need to be horizontal or would it be easier to just use them to extend the studs vertically?
Daniel,
Yes, you can tape plywood seams. For more information, see Air-Sealing Tapes and Gaskets.
If you read the article I linked to in my last answer -- the one on service cavities -- you'll learn why many builders prefer horizontal strapping to vertical strapping:
"When it comes to framing a service cavity, many European builders prefer horizontal strapping to vertical studs. Floris Buisman of New York City, a distributor of European building materials, notes that service cavity framing can be either vertical or horizontal. “This wall-inside-a-wall can be a structural 2×4 wall in lightweight construction,” Buisman wrote. “Or you can run the 2×2s (or 2×3s on edge) horizontally when the structure is on the exterior. This makes the electrician’s life pretty easy as he no longer has to drill through a large number of studs to get the outlets where they are needed.” "
15" + rainscreen for a wall in seattle seems like overkill, even for a Passivhaus. big fan of the horizontal strapping, though i have seen a few installs w/ vertical that worked - but required more work on site.
i like chris corson's wall (GWB, 2x wall, OSB air barrier, TJIs & cellulose 'outsulation, rainscreen) - however the TJIs are overkill for our climate.
Daniel,
We have plenty of local (NW) air sealing experience that is based on plywood with taped seams. It works great.
As with most projects, the faces of the wall are really not the issue. Tape takes care of that easily. The issues for good air-sealing is in the connections: Wall to floor, exterior sheathing to bottom of truss, sill plates... Those are the are the area's that will challenge you and may require more than ZIP tape.
Depending on what level of air sealing you'd like, get familiar with things like tremco acoustical sealant, airfoil electrical boxes and perhaps EDPM gaskets from Conservation Resources http://www.conservationresourcesinc.org/.
Taping the sheathing is the easy part. Planning how that red air barrier line travels unbroken around the entire envelope is the challenging part. Getting to know a few extra tools is handy.
With a good air barrier plan upfront, execution will be as easy as it gets. Without a good plan...
Mike, 15" (which includes a service cavity) is a lot but the cost of the cellulose shouldn't change too much for a thicker wall, unless there's a reason you wouldn't want too much insulation. Cold exterior sheathing is a concern, which is why I'm skeptical of the OSB-based ZIP system. Taped plywood seams less problematic. As for the space used by the wall, unless the site was super narrow the wall thickness can be planned for.
Albert, I was considering building the envelope with no overhangs to simplify the envelope as much as possible and tacking that (and similar) elements on after it was taped -- as in this post:
https://www.greenbuildingadvisor.com/blogs/dept/musings/airtight-wall-and-roof-sheathing
Thanks for the responses.
Daniel,
Personally while I respect Marc Rosenbaum, I disagree with him that an exterior air barrier is easier and faster.
To quote from the post: "Rosenbaum pointed out that, compared to an interior air barrier, an exterior air barrier:
has fewer intersections to seal;
has fewer penetrations, and the location of the penetrations is clearer;
can better accommodate design complexity;
because it uses OSB or plywood, is durable;
is visible and verifiable;
is testable early in the construction process.
Summing up, Rosenbaum said, “Why do I like an exterior air barrier? Because of partition walls, floors, wiring, and things that go in and out of the walls.”
All of that is from the point of view of airtight drywall. Placing the airbarrier at the finish drywall layer leaves the barrier in a layer that has lots of penetrations, and that is ultimately going to be degraded by occupants over time. It works, there are lots of products to do it with, (tremco, airfoil, etc..) and it's based on existing construction methods and adding an "upgrade" at the drywall.
Personally, I think placing the air barrier behind the drywall & service cavity is the fastest/best approach.
-Fewer penetrations than drywall.
-You can still have all the rafter tails, brackets, and other do-dahs that you want.
-You don't have to use ZIP sheathing if you'd rather use another material
-The pressure boundary is better/safer on the interior layer at windows.
-If you use a structural exterior sheathing (ply/OSB/ZIP) the interior barrier can be a membrane (fast/easy to bring around and connect to floor ceiling)
-If you use a non structural highly vapor permeable sheathing (Agepan exterior fibre board, Diagonal shiplap... ) then the air barrier is can be OSB/Ply and pick up the shear at the inner chord.
I think the interior air barrier w/service cavity approach is ultimately the best approach because it matches ease of construction, no interference with exterior details, and offers the best long term durability.
Placing an air barrier at a finish layer, either interior or exterior, is by nature, the second best place to put it. The best place is inside and out of reach.
Daniel,
A friend (Anderas) just sent this pic down from Toronto CA. The builder is Andreas Herman, Hermans Timber Frames. Im posting this one to just show where the interior OSB is used to pick up racking. The stud bays get blown and the exterior sheathing will be Pavatex which is a Swiss high perm wood fibre board just like the Agepan that we use.
If you expand the picture, you can see Green Siga tape on the interior side of the OSB to create the air barrier. From there he puts a service cavity. The typical Swiss method is horizontal 2x3's rather than verticle.
Pretty simple method and no problem with rafters on a warm or cold roof system.
That building is so beautiful as it is being framed.
Albert, I know this isn't the discussion here, but I don't understand pressure boundaries. I have seen drawings with the red line (Lucas' drawings), but I don't really get it. I get air barriers - that's relatively easy, but not pressure boundaries. Do you think you could do a guest blog on pressure boundaries sometime? Photos always appreciated.
Lucy,
I expect that Albert will answer your question.
But as far as I know, a "pressure boundary" is just another term for an air barrier. I'm sure that someone will post a comment explaining why the term "pressure boundary" is preferable to "air barrier," but I'm perfectly happy with the term "air barrier."
I would say that Air Barrier and "Pressure Boundary" are the same thing
I think it is useful to think of the Air Barrier as a PRESSURE Boundary
I think people like Chris Corson, Albert Rooks and Lucas Durand have a very good understanding of Pressure Boundaries (Air Barrier Systems) and how to CONNECT the air barrier materials.
Daniel,
With the general wetness of the PNW, I loved living in Portland, sometimes wish I still did, but mold and moss grow on just about any exposed wood. I would NOT use OSB even ZIP on or near the exterior! Plywood maybe but the best alternative is fiberboard. Fiberboard can be the exterior air barrier if it's installed on a bead of acoustic caulk around the perimeter. Some fiberboard is legal without bracing but on a double wall why not install diagonal 2x4s on the inside of the outer wall. I'd dispense with house wrap altogether and use Greenguard DC14 as rain screen/drainage plane over the fiberboard. Hardiboard or most any other exterior ( I'm going to use thin brick on Ambrico's EZwall substrates) will work well and live comfortably on such a wall. Installing fiberboard on the outside of the inner wall gives a nice service cavity eliminating the need to seal every outlet etc. Detailing a fiberboard wall as an air barrier includes installing the panels with a bead of acoustic sealant under the perimeter, sealing the bottom plate to sub floor, more acoustic caulk, sealing the corners with guess what and sealing the top of the walls to the ceiling with more of the same, and any penetrations (dryer vent, range vent, sill cocks, outside electrical boxes, HRV or ERV ducts, conduit for HVAC wires & pipes etc.) need to be caulked as well. FWIW, I'm planning on making my exterior walls 4" taller than my ceiling height, installing a ring of ring of 12" wide zip sheathing as a airtight top to the double wall assembly, then installing the trusses, the attaching zip sheathing to the underside of the truss chords, colored side down, taping it, caulking the ceiling perimeter to wall toppers. Then, perpendicular to the trusses I'll hang 2x4s, 24" OC (long dimension vertical) by screwing Simpson A34's to the trusses at each intersection. This gives me a 3 1/2" deep ceiling service cavity and a easily detailed air barrier, makes the top of the ceiling safe to walk on, eliminates any worry about sagging drywall due to insulation above regardless of depth. Once the ceiling service cavity is in place interior walls etc follow. There are some penetrations of the ceiling for plumbing vents, solar collector plumbing, solar PV wiring that I;'ll use EDPM boots to seal.
Lucy,
I used the term Pressure Barrier in this circumstance because the same layer, or line, was controlling air + vapor. It was the outcome of a long rambling post between John Brooks, Lucas Durand and I. I've lost the thread (often in more ways than one...) on it but I think it was a Q&A that started over the funny condensation pattern on Dr Joe's barn.
Frankly, I'm not sure I'm qualified for a guest blog, but thanks :)
Jerry,
"I'd dispense with house wrap altogether and use Greenguard DC14 as rain screen/drainage plane over the fiberboard. Hardiboard or most any other exterior ( I'm going to use thin brick on Ambrico's EZwall substrates) will work well and live comfortably on such a wall."
Someday we'll have better fibre board made here in the PNW that is wax impregnated throughout (not a surface treatment). The material on this house in Olympia WA is such an animal. There was no additional WRB placed over it. Just a 3/4 gap rain-screen. It's around 18 perms and the water just beads up and rolls off...
I'm building a new home and like your idea of using the zip on the ceiling with the studs attached for a service cavity, though perhaps i will use regular 7/16 OSB and tape the joints (very limited funds as i am rebuilding with insurance money from a tornado hit) Instead of using zip to join the two walls together at the top, I think i will use 2 x 4 blocks spaced so the trusses sit against each one for attachment purposes, which will leave the open wall below to dense pack the cellulose into and then right on up above the wall to guarantee for sure that it cannot settle (in case i don't get it densely packed enough near the top of the wall). My trusses overhang on the east and west side of the house by 12' for 10' porches (Georgia heat protection) which will give me about 4 feet above the walls giving me lots of space to blow in the cellulose on top (I'll have to put 2-3 x 8 foot strips of OSB on the vertical parts of the truss members between the porch ceiling and the walls to hold in the insulation. The webbing for the outside of the inner wall to hold the cellulose is so expensive, it will cost less than half that to put another layer of OSB there instead, be quicker to install, give a stronger wall. I priced the SIS type panels (which Dow recently stopped making anyway) at $47 each, so will use regular OSB for my exterior walls, adding two one inch layers of expanded foam (perhaps the outer 1" layer may be the polyiso with the radiant foil, just on the South gable end, since that will be the only wall that gets any direct sun due to the large porch overhangs). I will do the rain screen using 1 x 2 strips to hold the insulation on and to give the air gap to allow drying of the siding. I may use the new M-rock for the lower half of the walls, as it is ideally suited for the rain screen wall with 20" wide pieces with heavy PVC backing to screw to the strips. I will probably use either Hardiplank for the upper part of the wall or Smartside lap siding (hate how brittle, heavy the hardiplank is and smartside seems to be greener due to the use of chipboard, smaller trees, in its production).
Dale,
I too will have huge (9 foot) overhangs for covered porches. My only attic access will be through a panel in the ceiling of one of the porches making a decent air sealing job so much easier.
I built my "Double wall" house in 1981, in Winnipeg, Manitoba, Canada (no jokes). We are about 3 hours north of Grand Forks ND.
I used a 2x4 os bearing wall and a 2x3 is wall. We require vapor barrier and I put it on the back of the 2x3s. The VB is covered with 1/2" KB board, to keep the VB from flexing due to wind pressure. All electical is run in the 2x3 space, on the warm side of the VB.
The wall plates are 12" wide, 5/8" plywood, top and bottom and the walls each have single T & B plates. The outside finish is 3/4" stucco on wire lath ove building paper and 5/8" KB sheathing..
Ceiling was drywalled before the interior walls and only has the plumbing stack penetrating.
The walls are R-40 fibreglas, ceiling R-60 celluose, basement walls have 2" SM on outside, R-20 on inside. Basement floor poured over 2" styrofoam and 6 mil poly.
Have a 15 Kw electric furnace (only use 10), CA and an HRV.
I don't know what zone this falls into but after 30 years, no problems.
Keep up the good work.
Albert Rooks,
Regarding the Toronto house you posted a photo of earlier in this thread having an OSB air barrier on the inside of the framing, would you explain how the air barrier is maintained through the 2nd story floor joists, and how is it continued into the ceiling?
Daniel,
FWIW.
My double wall design has evolved considerably! First investigate Roxul comfort bats. I'll use them instead of cellulose, in the walls, mostly because of issues with fire blocking, and lack of experienced contractors to do dense pack cellulose. Believe it or not the material cost for equal r value is within very few percent of the material cost of cellulose. or quite possibly lower. I also went back to all 24" OC advanced framing (aligned as the gains of stagger are truly negligible) which the fiberboard sheathing did not permit I'll use 3/8 plywood with STO liquid applied WRB (Emerald Guard) to sheath the outer wall then Greenguard DC14 (XPS rain screen really neat stuff that has a perm of about 1, is r1, 1/4" thick and has drainage paths on both sides) then the exterior finish system. I'm using Ambrico EZ Wall but most anything would work. My inner exterior walls will have 7/16 OSB on their outer side. The OSB will have it's joints treated with the Emerald Guard. The OSB is my primary air barrier & the stud cavities of the inner wall are a service cavity. which I'll fill with r15 bats. My walls will be 12 1/8" thick including the brick and drywall, wiith 10 1/2" cavity insulation (r45) & clear wall r over 43 thanks to advanced framing and the DC14. An unusual requirement is that the outer wall be insulated before the inner wall is erected. The outer wall will be insulated with r30 bats even though it's 2x4. Then cut strips of r15 bat will be placed behind the studs and plates to face the sheathing of the inner wall. The inner wall WRB is installed (really painted on) before the wall is erected. I'm sticking with the OSB as a top tie plate but will seal it's seams as an air barrier.
Jerry:
to clarify, is your wall assembly, from outside to in:
siding, drainage plane (XPS? You don't mean rigid foam, do you?), 3/8 ply w/ liquid WRB, 2x4 w/ roxul filled cavity, a couple inches gap, 7/16" OSB w/ same liquid WRB as exterior, 2x4 w/ roxul filled cavity, and finally drywall?
Do you really need the exterior 3/8 ply if you have the interior OSB to act as both air-barrier and shear? One of the weakest points of a double-wall has always seemed, to me, to be the exterior sheathing, since it's necessarily cold with all the insulation behind it. I like the idea of moving that sheathing to the interior where it could also isolate a service cavity, as you're doing.
I had thought, though, that it would much more trouble to install sheathing on the exterior face of the inside wall -- is it actually fairly straight-forward, though?
Also, what advantages does roxul have over dense-pack cellulose? Two issues with DPC would be having someone who can install it and having the open stud bays.
I was starting to consider (exterior to interior):
siding, furring strips* , wrapshield (or similar), 2x4** w/DPC filled cavity, 4 1/2" space (+/-), 7/16" OSB with taped seams, 2x4 w/ no insulation (leave as open service cavity), 5/8" drywall.
* I like the physical separation rather than a drainage plane, but am willing to be convinced otherwise
** Wrap the exterior with insulation mesh.
I'm not sure about no exterior sheathing or using the interior 2x4 as service cavity (less R for thinner wall), just trying to think through difference options. This is Seattle, so it doesn't get too cold and the wall would still be R27+/-.
Jerry, thanks for the clarification. That is basically how I understood it to be.
I had heard that dense-pack cellulose was:
R3-4 -- where did you hear .7?
Is fire resistant
And I had thought it's ability to absorb water could be a benefit, since it could aid in dispersing moisture back through a vapor-permeable wall.
Thanks for your responses.
Daniel,
You pretty well have the picture. So I'll repeat it from the outside I'll have " siding" consisting of 1/2" "thin" brick glued to 4 ' x 4' steel panels that are screwed through the drainage material and the 3'8 plywood to the 2x4 studs. This comprises the outer wall which will be erected first. The 3/8 plywood is only there as an air barrier, the steel panels are structurally sufficient according to the manufacturer.. Since the plywood is the exterior air barrier and the required WRB I'll apply the liquid WRB called Emerald Guard by STO. I made this choice as, to me anyway, it allows the best method for dealing with my "recessed" windows. and making them truely water tight. The drainage plane material is a fan fold XPS that adds a very low permeability layer to prevent solar drying of moist brick from wetting the plywood. Yes it's an exterior foam but It also adds r1 and it is only 1/4" thick and it allows drainage on both sides. The important functions of allowing outward drying of the sheathing, preventing solar driven wetting of the plywood by the brick could as well be accomplished by replacing the DC14 with vertical furring strips then a layer of "tar paper. But the alternate would not provide a 'solid' surface under the brick holding panels, perhaps, leading to cracking or other problems, or any insulation & it's thicker, and subject to more variability ie requires greater craftsmanship to 'get it right. As to advantages of Roxul over DPC: 1, Absolute fire proofing! 2 Roxul is over r4/inch while cellulose is r.3.7/inch. 3, Does not store liquid water, it drains freely and completely. 4. from my shopping the material cost is lower & I did not even consider the cost of the mesh or netting that DPC needs. 4. DPC installation requires "not so common" equipment and skills where any laborer can install bats after 2 minutes or less of instruction. I'm not so sure you understood how I'm installing the insulation in the outer wall & cavity between walls so to be sure I'll re-explain with some added detail. Once the outer wall is standing up r30 bats which normally go in 2x8 framing are inserted in the stud cavities of the 2x4 wall. 3 1/4" or so of these bats will be hanging out the inside of the wall in what will become the cavity. Behind each stud or single plate or horizontal blocking is a gap that is less than 1 1/2" wide strips made from r15 bats are pushed into all these spaces. Doubled plates or studs if present get similar treatment with wider strips of r 15. Once all wood is 'covered' the inner wall can be erected with sheathing ( OSB) already applied just as sheathing was put on the outer wall while it was horizontal & lying on the sub floor the OSB is nailed to the 2x4 framework of the inner wall while it is horizontal BUT because the outer surface of the inner wall will soon become inaccessible the air barrier detailing is also done while the wall is horizontal. Finally if the inner cavity were left empty the clear wall r value (no allowance for window & door framing) would drop from 43 to about 29. Which is probably fine in Seattle, although I've been there when it was 3 degrees f. If you wanted a more "open" service cavity, consider framing the inner wall with 2x6 but still filling it with r15 (31/2") bats.. Also I've considered using "MemBrain" by Certanteed instead of the liquid for the inner air barrier. It may be slightly more economical but I'll have to train the "crew" to use the liquid for the outside anyway so why add another unfamiliar step. FWIW the combination of thin brick and resessed windows results in an r40+ wall that looks like any plain 2x6 wall with brick veener both from inside and out. No deep window cavity s.
I've edited out that typo it is 3.7 according to my sources. Sorry it slipped by me. Yes cellulose insulation products are treated with fire retardants but mineral wool is simply UN-combustable & melts at over 2000 degrees F. There is a down side to the mineral wool, it does little to "air seal" while DPC helps significantly.. I am unsure whether holding or draining any liquid water is better.
Reply to: JACK WOOLFE
Jack, I'm not sure how Andreas get's through the 2nd floor framing. I'll ask him If I can catch up with him. There are some pretty good tools to go around all those penatrations.
In that style of building the roof is a build-up or wood fibre boards & OSB on the timber rafters and also not too hard to seal between wood, tape and membrane. I've attached a picture of the typical "warm roof". Andreas imports Pavatex from Switzerland for his applications, along with the Swiss SIGA that I also have started in the US.
To me the roof is pretty easy as is the connection to the 2nd story wall. As I said, I'm not sure what he does between the two floors. It looks like a pain. I'll see if I can find out.
The SIGA Corvum 30/30 is whats typically used to go around timber penetrations. The picture attached is not the best... Just imagine a tape that's pre folded with a 90" bend to seal right angle penetrations.
Jerry and Daniel,
I realize that we all have differing tolerance levels, but to be fair to "air sealing", Cellulose, in whatever density applied, does not provide any air sealing. It may slow the air movement, as I may slow a busy friend with conversation, but it's not an air seal.
Air sealing stops air movement at a boundary. Fibre insulation like cellulose, fiberglass, MW or other "fluffy stuff" will slow air at low pressure differentials, but really does not do anything as the pressures increase.
Also, to be fair to MW, when it's used in it's higher densities of 6pcf and more as exterior insulation, it does eliminate wind washing due to it's density. Provided of course, that seams are not an infiltration source.
Hi, Just wanted to chime in on the air sealing detail I saw mentioned, using building paper vs liquid applied. I want to second the recommendation of Jerry with the liquid applied method. We used BASF's Senershield instead of Sto's product. I think its cheaper and requires less products (Sto has a number of liquids, tapes, caulks). Senershield also has it in two different vapor permeability profiles. As we all know its in the details to get all the construction correct and lots of tape seams on building paper takes a ton of work to get right. A liquid applied membrane, rolled or sprayed, takes care of a water barrier and air barrier in one, plus you can use osb and helps the confidence about it lasting. At our pre-insulation blower door on a 2,500SF we were at .1, which should put us on our way to our passive goal of .06 at final (one of our doors has significant leakage underneath it).
fyi - as far as our wall assembly goes, we do stucco on the exterior over a 4" eps insulation board (dew point and thermal bridging becomes a non-issue), then Senershield over osb on a 2x6 wall. We flashed the inside of the osb wall with closed cell spray (advanced framing so helps rigid up the structure and a backup air barrier), then we wet spray cellulose the rest of the 2x6 cavity. My stucco contractor takes care of the liquid applied barrier, eps insulation and final coating. Since we were able to get this home so tight with the liquid applied barrier, I think we may do away with the closed cell foam next time to save money.
ps - for the roof, we did use zip panels and zip tape and sheeted with no outlooks, just to the edge of the walls. We wrapped Grace from the roof sheathing down to the osb (need to paint prime the osb to get a good stick), then we liquid applied from the Grace down to the stem wall of the foundation. Afterward we added 2x4 outlooks on end and used 3.5" polyiso rigid board as a layer on top of our roof sheathing, then sheeted again with osb. We took great care not to leave any gaps in the polyiso and stagger seams with the osb. Underneath the roof we again skim coated with closed cell then dense packed cellulose 14" in the between the wood I-joist. I'd like to value enginner the roof assembly a bit more but we we are confident in its assembly right now.
Good luck,
pss- sorry we are climate zone 5, dry, Boulder , CO
Brian, the major issue I have with a liquid applied WRB is that it doesn't allow for a mechanical flashing joint at openings (windows, doors, etc.)
I'd prefer to use the sheathing as the air barrier (taped ply, for example) and some form of building paper to be able to lap the flashing rather trust in tape or some other chemical bond.
Daniel, I don't understand your statement regarding liquid WRB, "it doesn't allow for a mechanical flashing joint at openings (windows, doors, etc." The STO instructions show metal flashing above windows & doors with mesh and Emerald Guard over the flashing connecting it with the panel that is above & behind the flashing. Basically the opening is sealed then the flashing added and sealed to the sheathing. I intend to use this detail above all such openings. I'm also going to 'slope' the flashing outward, to assure drainage away from the opening, by installing them to pieces of shim shingles. In my case the DC14 will be applied after the WRB & flashing. I will have no brick, within the recess, across the top of windows & doors while the brick will face the jams & sills of the recess. The sills will be sloped.. Wherever brick is installed it is over the DC14, so strips of DC14 must be cut and installed on the sills and jams before the brick substrate. I guess in my case I'm lapping the DC14 as you wish.
Jerry,
Yes, the instructions call for the installation of mesh over the metal flashing. But you are still relying on a chemical to seal the seam between the OSB and the mesh. It isn't a lap; it's just goo.
As far as I can tell, it's really good goo, but still -- it's just goo. And none of us know how long the goo will last.
Reply to Jack Wolf:
Jack, you asked:
"Albert Rooks,
Regarding the Toronto house you posted a photo of earlier in this thread having an OSB air barrier on the inside of the framing, would you explain how the air barrier is maintained through the 2nd story floor joists, and how is it continued into the ceiling?"
With the details so different to what we are used to, and probably interesting to many of us, I thought I'd post an answer since I just got new pictures from the builder Andreas Herman.
The Siga system that we stock at the Small Planet Workshop - http://www.smallplanetworkshop.com has a lot more to it than just a flat piece of tape. You can see in the picture that Andreas used the Green Rissan 60 tape to sealing the OSB panels at flat joints and then the pre-folded corvum 30/30 at the beam intersections. The Corvum 30/30 has 1-1/8" legs so that the infill OSB doesn't have to be cut too tight.
Using sheet stock material as the internal air barrier, and vapor control layer and to pick up racking is a very common way to build a wall with an increasing diffusion gradient to the exterior. The exterior layer is targeted to be 10x more permeable than interior layer. Hence the continual quest for highly permeable exterior sheathing.
Returning to your air sealing question, Since air sealing this way has to deal with varying materials and conditions, companies like SIGA have created a pretty wide range of products to take care of the applications in quick simple steps.
Btw... I think that we have to agree that Andreas does really nice work :)
albert.