Double stud wall review

Hello,
I’ve tried to summarize a lot of good ideas of double stud wall. Could you please check for mistake?
I understand that details are important as a concept, and a “small” mistake could ruin everything, like no weep hole in brick for instance. But with a mistake in concept there are no success even with good details. 😊
Place.
Climate zone 6A: (Köppen: Dfb)
Location: Blue Mountain, Ontario
Not much rain, about 38” annually
Windy, up to 40 mph / 65 kmh.
Wall structure (exterior to interior):
1. Brick or stucco (don’t know that’s better)
2. Air gap (1×3@24” or 16”) (or rainscreen mat or additional 3d house wrap over liquid WRB?)
3. Liquid-Applied WRB (R-Guard Cat 5, STO Gold or something like this)
4. Plywood (1/2”) CDX
5. External framing (2×4@24” OC), filled by rockwool batts
6. Space (~11”), filled by blow in cellulose or fiber/cellulose batts
7. Plywood (1/2”) CDX or OSB (5/8” or ¾”), seams taped from outside. Worked as structural an as vapor barrier instead of poly. /Once again, I’m in Canada, hope it could replace 6 mil of poly./
8. Internal framing (2×4@16” OC as load bearing and service cavity)
9. Drywall
The main idea is to replace internal poly to plywood as smart and untouchable barrier from the basement to the roof and doesn’t matter how many holes in drywall would it has. Also, it should be easy to build, check and save while building in process.
The R-value should be about 40+, but it could be easily adjusted.
Thanks,
GBA Detail Library
A collection of one thousand construction details organized by climate and house part
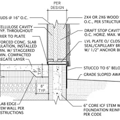
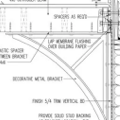
Replies
When the load bearing studs is on the interior and the exterior studs cantilevered off the foundation it's usually done as a "Larsen Truss", with the same stud spacing on both for better mechanical support and integrity of the exterior studs/chords. (See: https://www.greenbuildingadvisor.com/article/all-about-larsen-trusses )There are variations where both sets of studs are supported by the foundation (sometimes with a step-down to provide a better thermal break on the bottom plate), which in your case would make for a VERY fat foundation wall, but if you're installing a brick veneer that may already be a requirement(?).
This is a detail of a step-down fully supported truss wall that would make more sense than your proposed spacing & stackup:
https://www.buildingscience.com/sites/default/files/migrate/jpg/2014_HighR_wall_07_web.jpg
Keep in mind that the carbon footprint of an 18--24" thick wall is HUGE compared to the arleady substantial footprint of an 8" foundation wall. In your case the exterior step would have to extend far enough to support the brick. Stucco siding (or commercial thin-brick cladding solutions) would save a couple of inches, maybe three, but it's still not great.
With lighter siding and a thinner foundation wall it's common to frame the exterior chord of the truss to lap down the exterior side of the foundation a foot or so to provide a bit of thermal break.
With standard double-studwalls the exterior side studs are structural, supported by the foundation, with the interior non-structural studs supported by the floor framing. In that type of assembly the stud spacing doesn't need to align, and the thickness of the foundation doesn't need to expand with wall thickness.
Dana,
Yap the idea starts from "Larsen Truss", then they “fall down” and two walls connected continually vertically every 8’ (as Malcolm noted, probably not enough).
For the lightweight siding, I’m sure, the Larsen works fine, but definitely not for heavy (stone, brick, stucco) cladding. And agree, ~2’ thick wall has big carbon and budget footprint. And, I hope, nobody is going to use atomic, especially “in the middle of nowhere”. So, I’m trying to optimize wall thickness to normal ~10” with my pen and calculator. I think it shouldn’t be “mission impossible” – on one side about 1000 lb/ft external cladding and insulation, on the other floor and roof. Some tricks with magic rebars from structural engineer and “L” shape wall should work fine - Low carbon, wide wall support.
It’s easier to build classic double wall, but I think it’s harder to seal it completely. In this version, there are some questions about foundation top and straight way to make all barriers.
Thanks!
>"It’s easier to build classic double wall, but I think it’s harder to seal it completely."
There are hundreds of existence proofs in Passive House/Passivhaus homes built as classic double studwalls that meet extremely low air leakage specs.
Oleg,
A few random comments:
- If you insulate the service cavity (there won't be much in it to reduce the R-value), you could reduce the wall thickness by that thickness. With a minor reduction of the space between the two walls, and cantilevering the exterior one out 1 1/2" you might be able to bear the whole thing on a standard shaped 10" concrete foundation (The present insulated portion of the walls is 14 1/2". What I'm proposing would be 11 1/2").
- Why not blow the whole cavity, rather than using batts on the exterior wall and then blowing?
- Those two hinges in the exterior stud-wall, supported by braces are problematic. Instead I'd suggest extending the second floor subfloor out and breaking the wall up into two parts at that level.
Malcolm,
Correct, the wall thickness mostly is 11 1/2” (some parts will be 10” probably).
It’s possible to insulate internal cavity too and reduce wall thickness by 3.5”. It saves about 1’ of external wall length. But it saves 3.5”, not 12”.
Rockwool in exterior cavity – I think it’s my prejudice against cold exterior sheeting and “sweating”. It can give some extra minutes of calm dreams. :)
Pardon, “two hinges” you mean stuff binding external and internal walls? Three will be better? I’m planning to bolt 2x4 along the wall into internal studs. And put 1/2 (or 3/4) plywood continually as structural wall binder, fire divider and to help insulation to settle more slowly. Make this every 4’ of external wall? For now, it gives 0.5-0.8% additional termobridge surface.
Thanks.
Oleg,
By hinges I meant the points where the exterior walls are divided up into three parts. These end up relying on the braces for their lateral stability. The typical detail is to frame the exterior wall up to the subfloor (which extends out) and start a new one above it. The exterior walls should be framed a bit shorter as they will not experience the same shrinking as the interior ones at the floor assemblies, and can inadvertently take on structural loading.
With the right materials and dimensions, I'd guess that all of these are possible support for double walls:
Making the outer wall structural (and not the inner)
Hanging the outer wall off the inner (Larsen)
A fat stem wall, perhaps wider at the top than elsewhere
A FPSF slab
A large steel L bracket (oversized brick ledge)
Floor joists (set on outer foundation) supporting an inner structural wall
Floor joists cantilevered out past an inner wall foundation
Is the cantilevered concrete foundation a common detail? I'm having a hard time understanding why it's worth making the interior wall the load-bearing if a foundation is necessary to support the cladding. As Jon says, possible, but does it make sense? Is it just so you can break the thermal bridging of the rim joists?
Maybe I'm just scared of concrete work (cantilevered) but another thought would be to cantilever the bottom floor to provide necessary support for ext. structure, but keep the second floor tucked back to the first wall if wanting that benefit. Blocking at joists above foundation for inner load-bearing wall would be needed of course. Mind you I'm not too familiar with brick siding and its needs for support (how it could be supported by a wood structure).
Also, I don't see this as a simple or elegant solution, just spit-balling.
Tyler,
No it isn't common to build out the exterior of a concrete foundation. It's hard to form, and can be awkward looking when finished.
The big advantage of having the inner wall load-bearing is that it allows you to keep the rim joist back and you can also air-seal the outer face of the inner-wall. The problem, as Oleg has found is there are practical l9imitations on how deep the wall can be and still fit on a foundation.
Yeah I seem to recall Joe Lstiburek advocating for interior load-bearing walls but never did see a detail or explanation about how the exterior wall is supported. Dana mentioned that a larsen truss is how this is typically done, but it seems like Joe was referring to true double-stud walls, so not sure how he envisions that detail... I suppose with a 10" foundation and only a 12" wall its less of an issue.
Tyler,
I think the idea came form Thorsten Chlupp. There is a good discussion around the subject back in 2011. https://www.greenbuildingadvisor.com/question/the-sunrise-home
Lucas Durand used it on his build. I think it works well with a slab with integral footings. http://ourhouseuponmoosehill.blogspot.com/p/details.html
Or as you say, narrower double-walls.
With lighter weight siding a Larsen Truss can be cantilevered off the foundation by quite a bit, but full sized brick needs more support from below to manage the weight.
As I recall the lore, the original Larsen Truss was a retrofit onto an existing 2x4 wall, installed on the exterior of the structural sheathing which is pretty much what Oleg's stackup looks like, except that Oleg's wall isn't using the structural studs to support the exterior studwall due to both the difference in stud/chord spacing and the mass of the masonry siding. The original Larsen Truss didn't need modification of the foundation, but the new siding & exterior sheathing was hanging 9" to the exterior of the structural studs, unsupported from below. (The truss itself was ~8", and added to the exterior of the original sheathing, designed to take ~R25 fiberglass batts.)
Thin-brick cladding systems more commonly used in commercial construction might work. Those systems typically use steel panels with low density thin bricks that fit into clips or rails formed in the panel stamping, with less less than 1/4 the heft of a full brick veneer.
eg:
https://brickit.com/systems/systems-dmg
http://blog.tlcsupply.com/loxon-brick-panel-system/
http://www.redlandbrick.com/downloads/tn28c.pdf
That's probably lighter than most stucco walls, and with some engineering of the trusses one could hang thin-brick siding a foot off the foundation, no brick ledge required.
I've done this for hanging LVL beams off concrete, but I think there is also a masonry hanger for I joists. Basically hang your floor joists inside your foundation instead of resting on top.
With a top flange hanger, you can hang your floor joists inside your foundation. This would would let you move the load bearing walls above in and give you more space for a thick wall but still allow for standard brick veneer support.
I would check with an engineer to see how far in you can move your load bearing walls with this type of detail.
Akos,
That's an interesting option. You would need to figure out how to deal with where the joists were parallel with the foundation, and point-loads though.
I wonder if making the framed walls in the basement or crawlspace load-bearing might also work?
There are some details that need to be worked out including basement window/door openings.
Interior load bearing walls are good especially if the basement will be finished. It would mean wider footings but that is easier than non standard width.
Another option is ICF style ledger. Either cast in place or on ledger connectors.
Some options, still a lot simpler than trying to figure out how to cantilever brick veneer.
The more one thinks about this, the better a standard double stud construction sounds.
I guess the first thing to do would be to see what the optimum width of wall is for the climate and design. Maybe the depth is a non-issue? in how many places does an 18" wall make sense?
Akos,
I think your idea could work. My current house has 2x6 walls about 2.5’ off the foundation for both sides. And it’s not mandatary - inside wall has to be bearing. In my draft inside wall sits on concrete. Your suggestion could bring interesting case – inside wall could bear the wall, outside – the roof. As I know there is no requirement to have one bearing wall.
For this project I would like to save current foundation, but it’s not big. And 1 foot out much better then 1 foot in. :)
Generally you design a house to have one load bearing wall. This holds up all the floors and the roofs. Having two bearing walls (one holding up the roof and one for the floors) only complicates details for no gain.
This load bearing wall typically sits on the foundation. My suggestion was that you can move this load bearing wall in towards the center of the house to allow for the brick veneer to sit either directly on a standard width foundation or on a shelf angle attached to the foundation.
Cantilevers are never simple especially if they are holding up a lot of weight. Assuming 2 story house, 20' of brick veneer is a LOT of weight. You want to keep this simple, stick to a standard detail.
May I summarize a little bit.
The walls stack itself are ok and it should work fine in cold climate. And no questions arise to use it on FPSF (or similar) slab.
The only issue is exterior wall and siding support (cantilever), pardon, only heavy siding support. For lightweight we can use/adopt "Larsen Truss".
I thought about Martin’s third question about this detail in the article https://www.greenbuildingadvisor.com/article/lstibureks-ideal-double-stud-wall-design. I found two ways – concrete and metal. First one should be more budget and design friendly.
I never saw such stuff in real life at our local residential projects. But I never saw a kangaroo in wild too. I don’t see any big issue to build a small additional form and pure concrete cantilever. Rebar should help to keep it whole and on place. Loaded bearing wall should help either.