Double stud wall and lumber prices in COVID times – alternatives?

Hello GBA community and experts – we live in rural Eastern Ontario, climate zone 6. We are planning a 750 sq ft addition that was originally going to have double-stud walls filled with 8″ of dense-blown cellulose with 1.5″ of Comfortboard 80 on the exterior. With lumber prices being what they are, we are wondering if there is a less lumber-intensive wall assembly that can achieve the same R-value for less cost? We’ve wondered about a 24″ OC 2×6 wall filled with 5.5″ of cellulose with up to 3″ of Comfortboard on the exterior. We will need to do the cost analysis on the lumber-savings versus additional cost of Comfortboard. But we’re wondering if there are any technical cautions about this type of wall assembly, or if there are other recommendations of how to build a well-insulated wall with less lumber and less cost. (to date, we’ve been wanting to avoid foam insulation). Thanks for any advice!
GBA Detail Library
A collection of one thousand construction details organized by climate and house part
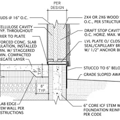
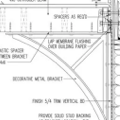
Replies
A 2x6, 24" OC wall with exterior mineral wool board is a quite viable plan. The costs will depend on your local material costs and on your builder's comfort level with putting siding over thick comfortboard.
As far as way to make the double stud wall cheaper, you could consider 2x3 studs for the interior wall, or even 2.5" steel studs, especially if you use that for an unisulated interior service cavity. Again, local prices would need to be checked.
Good point about installing siding over 3" of comfortboard. We just covered the original 1890s part of the house with 2.5" of comfortboard and finding ideal fasteners for the strapping was a stretch, no pun intended!
Your double stud assembly would likely perform somewhere around a true R-29. Your alternate assembly would be around R-28, and would have lower risk of moisture accumulation (not that double-stud walls with cellulose ever show problems). You could reduce your global warming impact by using rigid wood fiber insulation instead of Comfortboard. You could gain a bit more insulating value by using Canadian-produced Sonoclimate Eco4 sheathing instead of regular plywood or OSB. You could swap recycled EPS or polyiso for the Comfortboard, though vapor-open materials are marginally safer.
For more info, read this and the related links: https://www.greenbuildingadvisor.com/article/how-to-design-a-wall
Thanks for those suggestions of alternative and Canadian made products. Will do more research and number crunching!
Skip the 1.5" comfort board, bump up the distance between the double studs to compensate for R value loss and go for 24OC on your non bearing 2x4 wall. The money you save by loosing the 1.5" rigid mineral wool will more than make up the recent cost of increase in lumber.
You can also save a bit more by going with 1/2" gypsum sheathing instead of OSB/CDX.
Overall in your build cost, the lumber will be one of the smallest line items, I would not worry too much about it on a 750sqft addition.
Thank you, after crunching numbers and balancing both Rvalue and cost, we are planning to go with a widened double-stud wall, 2x3s on the non-load bearing wall and either the Eco4 or wood fibre board for sheathing and will leave out the Comfortboard. Thanks all!
Be careful with 2x3s where the finished wall surface tolerances are higher (walls with cabinets, walls with tile) as anecdotally they seem to be more likely to move and undermine the flatness of the wall.
2x3 and 2x4 are about the same price here. Dealing with warped 2x3 is not where you want to save money.
Depending on where you are in Eastern Ontario, you might be able to use lumber from a local mill for the non-structural wall. We are building a similar house near Ottawa right now and our CBO is happy for us to use the local lumber for anything that isn’t structural. It will be a big cost saving for us and I like that it comes from down the road.