Superinsulated Double-Stud Wall and Cold Sheathing

Just want to thank the community for being the continual wealth of knowledge that it is.
In examining super insulated walls without exterior insulation, cold sheathing keeps coming up as a concern. less energy makes it through the insulation to dry the sheathing made cold by the extra thick insulation, cold sheathing carries more moisture (correct?). A rainscreen is one of the recommendations to help dry the sheathing.
But what if there was an airgap between the insulated interior side of the sheathing and the exterior wall cladding side of the sheathing. From inside to outside a super insulated double stud wall assembly could go like this. 2×4 interior stud wall with a gap of chosen size to accommodate desired R value. 2×4 load bearing wall. A WRB applied directly to unsheathed 2×4 frame. A second layer of 2×4’s nailed like furring strips to the 2×4 frame creating a 3.5″ structural member to the nail the sheathing to. A rain screen can then be applied to the sheathing.
Would this be able to accommodate a super thick insulation cavity in the double stud wall without concern for moisture on the sheathing? Would this pass as still applying the sheathing directly to the bearing wall? Does this negate the need for an interior air barrier as there is no longer concern for outward vapor drive? All comments welcome I’ve just started to mess with sketchup so I apologize for the very rudimentary wall assembly model.
GBA Detail Library
A collection of one thousand construction details organized by climate and house part
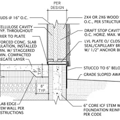
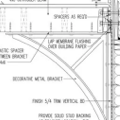
Replies
Hammel_Shaver,
The concern with moist air from the interior in walls occurs on what Building Science Corp calls "the first condensing surface" - which is often, but not always the sheathing. That is the first surface the the air comes in contract with which is cold enough for the moisture to condense on.
Because of that, vapour-barriers need to be located in the wall assembly close enough to the warm side that they don't become this surface (the rough rule of thumb is 1/3 of the depth of the wall from the interior).
So the problem with your proposed wall is that you have just moved any possible condensation problem from your permeable sheathing to an impermeable vapour-barrier, which is located too far to the exterior - and unfortunately, the second gap buys you nothing.
Luckily, experience has shown that double-stud walls that are build with 1) an effective air-barrier, 2) have an interior vapour-retarder appropriate for their climate zone, 3) are insulated with cellulose, and 4) have a rain-screen gap, don't have problems with their sheathing.
https://www.greenbuildingadvisor.com/article/the-mythical-threat-to-double-stud-walls
Thanks for the reply Malcom and the link to Ben Bogies article, which does act as a reassurance to thinking about the durability of a thick double stud wall.
Martin thankfully pointed out my large mistake in calling what I meant to say was a WRB a vapor retarder. I have edited this mistake!
What I am proposing is a vapor open wall assembly. It would be a WRB on the exterior wall. One such as Solitex Mento.
Any vapor or moisture movement moves through the WRB and into the airgap.
I would consider an additional WRB in the interior warm side of the wall, as a belt and suspenders approach to air tightness. But isn't that usually applied in a thick wall assembly primarily as an air barrier to protect the sheathing from warm moisture carried outward by air leakage? If there is effectively no first condensing surface of interest because it has been replaced by a highly vapor open Solitex mento outward air leakage stops at the air barrier and the moisture passes through the vapor open Solitex Mento. Am I thinking of this correctly?
My thought is that this would allow for an "over insulated" wall assembly with no fear of any structural part of the wall being at risk of moisture issues.
Sorry for the miscommunication I'm very interested to know if I'm on the right path here.
Solitex Mento is not a vapor retarder. It is a vapor-permeable water-resistive barrier (WRB).
Oh dear, please excuse the fuax pas Martin. I was recently listening to a builder podcast where they where referring to the WRB as a vapor retarder. I went back and corrected my use of vapor retarder.
Given this quite important change of materials do you have any thoughts on this assembly?
Hammel_Shaver,
Just to keep the terms clear: the interior side membrane you are suggesting would be a vapour-retarder, not a WRB. Would it be necessary in your proposed vapour-open assembly? Practical concerns aside, I'm pretty sure the codes I'm familiar with would require one.
I have a few concerns about the wall, but none about its ability to keep things dry.
- It doesn't have a defined primary air-barrier. Either the inner-membrane or the WRB needs to be detailed as such, as you now can't use the sheathing for that function.
- It contains a lot of layers, and uses a lot of materials. If you are married to the idea that the second air-gap is necessary I don't see why you couldn't use 1"x material, or the same furring strips you are using for the outer rain-screen. That also means your sheathing would still be directly fastened to the outer-wall studs. if you think you need the additional depth to keep the gap open with the cellulose bulging, 2"x 2"s would work fine too.
- How that inner-layer will be framed needs some thought at the top and bottom. You have competing demands there: The sheathing needs to be fastened back to the framing along the top and bottom of the walls, but a the same time, the whole point of that cavity is that these two areas be open to vent the moisture.
- Most of the attributes of exterior rain-screen cavities have to do with their ability to deal with water intrusions from the outside. That's why many don't have a vented top. The inner-one you are proposing is primarily to deal with venting moist interior air. It needs to be detailed with that in mind. Somehow that inner-gap needs to be open at both the bottom and the top - and protected.
Malcom thank you for your detailed perspective.
The primary air barrier would be Solitex Mento applied directly to the outside of the load bearing stud wall. 2x's (or whatever suits the job) nailed over that and then the sheathing.
I think the largest issue you brought to my attention is where the sheathing needs to be fastened back to the framing along the top and bottom of the walls. This is why I suggested 2x4's as the "strapping" that creates the space between the Mento on the exterior of the 2x4 wall and the warm side of the sheathing. The 2x4 strapping would span the top and bottom plates of the first and second floor and also be mechanically attached to the foundation would that be enough? Would hurricane ties be able to take it the rest of the way if it wasn't?
This wall assembly would connect to a vented roof deck creating what Matt Risinger would call monopoly style framing.
A big take away here is that I need to created a much more detailed set of models to show important details.
I appreciate the input.
Hammel_Shaver,
The layer of 2"x4" strapping can effectively transfer shear loads back to the framing from the sheathing. The problem is those top and bottom horizontal 2"x4"s also block airflow to and from the cavity. So that's where I'm having trouble seeing how the competing demands of providing backing at the top and bottom are reconciled with needing the gap to be ventilated.
You should also check your code and see whether you can connect the cavity with your roof space. For fire spread reasons our precludes having the two "concealed spaces" connected.
Hi Hammel,
I think if you want to avoid any chance of moisture in the sheathing, making your interior wall the load bearing wall might be the best option.
From a materials only perspective, Swinburne's modified Larsen truss is one of the cheapest ways to make a ~12" wall. And it keeps the sheathing warm. Here is a screenshot of a video of a man holding a photo to clarify. It's also in the Pretty Good House book. This photo is showing 5/4 lumber I think, since this house sourced onsite lumber. But same idea with 2x material.
Hi Tim, I like the Larson truss system but have always struggled with the idea of how to transition it to the foundation? Have you seen any good details on this? I'm also curious how that would scale to say a 24" thick wall?
In this case, I believe they had the mudsill overhang the foundation. Below it, they had 6" of EPS anyway, so it went right over that to make the transition seamless. Scaling it up to 24" adds more difficulties there, if you don't want your wall floating.
6" of EPS would certainly help. Though I question the long term durability of the EPS from two data points.
First point, the house I grew up in was a timber frame SIPS house. The sips had an EPS core. You could hear the mice tunneling through the EPS and see the ejected shreds of EPS beads from the carpenter ants.
Data point 2 Jake Bruton (The Unbuilt it podcast and Build Show Network) lived in a house where his dad lined the exterior of the foundation with EPS insulation above and below grade and flashed over it. When they went to sell the house years later the building inspector had them remove the flashing to inspect the foundation and they discovered that something line 60% of the insulation had been removed by rodents and insects.
Personally I wouldn't mind a floating wall but seeing as there is plenty of space to diagonally brace the interior of a thick double stud wall and rain screens and vented roof decks are already a practice it seems like have a vented sheathing option should be achievable with little additional engineering.
Hammel_Shaver,
Foam from a roof I replaced last fall:
I still hear people speak of this "cold sheathing" problem in connection with double-stud walls. In the absence of insulation outside of the sheathing, then on cold winter nights the sheathing will be cold regardless of whether the insulation inside of the sheathing is thick or thin. As an example, consider a "to code" wall with a total of R-19 worth of insulation inside the interior surface of the sheathing, compared to a double-stud wall with a total of R-39 inside the sheathing, and with a total of say R-1 for sheathing and siding. At steady state, center-of-cavity one-dimensional heat transfer says the temperature rise from outside air to inside the sheathing will be total delta T divided by 20 for the "code" wall or total divided by 40 for the double-stud wall. If inside is at 70 and outside is at zero F, the inside of the sheathing ("first condensing surface") will be at 3.5 F for the code wall or just 1.75 F for the other. Sure, the inside of the sheathing will be colder in the wall with more insulation, but the difference is less than two degrees. This is much less than the day-night or even hourly outside air temperature changes. The sheathing gets quite cold in either case, because it's barely insulated on its outside. So why do we speak of this "cold sheathing" problem with thick walls and not with "code" walls? Am I missing something? Of course, in either situation, care should be taken to keep interior air out of the wall cavity.
dickrussell,
https://www.greenbuildingadvisor.com/article/how-risky-is-cold-osb-wall-sheathing
I believe the cold sheathing discussion began when some decided to move the primary air barrier to the cold side of the wall. We do not do this in MN and even 2x6 walls with OSB exterior sheathing do OK.
Doug