Does this wall assembly make sense?

I need some expert advice. Here is what I am considering for exterior walls:
siding (wood lap, LP, or fiber cement)
WRB (DeltaDry?)
Furring strips (oc to match studs)
4″-8″ XPS or Polyiso foam
2×4 or 2×6 studs (16″ or 24″ oc)
1″-2″ closed-cell spray foam in cavities
Drywall
Does this make sense for a cold/mixed climate (Omaha NE)? Is fiber cement to heavy for the furring strips? Is it worth fighting the battle with my local builder’s on going 24″ oc vs 16″ oc? With the exterior foam, do 2×6 studs make sense or are 2×4 studs a better choice because of less material? Is the spray foam necessary? Is this wall allowable by building codes?
I am posting this knowing that my assembly could very well be “full of holes”, but I will gladly swallow any pride in exchange for good advice. I really do appreciate people providing feedback. This site has been a tremendous resource for me.
Mike S
Omaha NE
GBA Detail Library
A collection of one thousand construction details organized by climate and house part
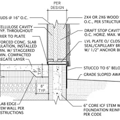
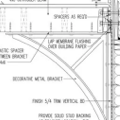
Replies
Make sure the OC spacing doesn't exceed the manufacturer's requirements for the siding you choose. Apply the WRB between the furring and the exterior foam board to protect it from wind deflection. Eliminate the interior spray foam and keep the sheathing in the conditioned space. Use the smallest structural framing members that code will allow for the sake of resource efficiency. Include some kind of shear bracing in the structural frame to meet code requirements.
Is there a reason you want to use such thick rigid insulation on the exterior and leave the stud bays largely empty? Why not use 2" of rigid insulation on the exterior and smart framing with 2x6 stud bays filled with blown-in insulation? That assembly should cost less, be stronger, and give similar thermal resistance and air-infiltration performance.
David,
By leaving the stud bays open, I believe that will help to reduce condensation issues at the interior side of the sheathing because they will be in conditioned space (This would answer my questions about spray foam in the stud cavities) . This will also make plumbing/wiring/etc easier to install between the studs. I'm not 100% sold that adding another contractor/product/process (blown-in insulation) will cost less and provide similar air infiltration performance. I'm interested to see the actual cost differences between the two approaches. Insuring that the exterior foam is installed correctly will have to be done with either my approach or your approach. Why not eliminate a second insulating method if the first one can meet my requirements (assuming that is true)? How would your approach be stronger?
This is one of the features of Lstiburek's "perfect wall"
http://www.buildingscience.com/documents/insights/bsi-001-the-perfect-wall?topic=doctypes/insights
Unusual to hear this strategy suggested by Robert?
The tricky parts are the long fasteners and details around the windows.
An advantage of not having insulation in the stud bays is that there is no longer an energy penalty for Not-So-OVE framing.
Extra framing in this case actually Increases R-value and "interior" thermal mass.
Just wanted to add that Lstiburek and Straube seem to spec OVE and cavity insulation except in the extremely cold climates.
John,
As you know, I would never advocate the outsulation strategy or the heavy use of petrochemical foams, but I was merely offering suggestions within the narrow options presented.
John,
As you know, I would never advocate the outsulation strategy or the heavy use of petrochemical foams, but I was merely offering suggestions within the narrow options presented.
Robert,
I'm interested in hearing alternative suggestions. In reading many of your other posts, you seem to favor more natural materials and some "breathability" to the walls. Do you have recommendations for our climate? I'm trying to budget whatever is necessary for the best walls I can build (hard to change 'em later). Thanks again for sharing your opinions.
Michael,
Breatheable thermal envelopes are inherently more durable and more healthy and, if made of natural materials, also far less impactful on the environment.
For instance, there is no need for a rainscreen with a breatheable wall system made from moisture tolerant materials (i.e. no OSB), except in high rain exposure zones (you're in a moderate rain zone). This makes flashing and WRB integration details simpler and less likely to result in leakage over time. A roof assembly should likewise be breatheable but also well vented in order to insure long term durability and drying potential (all roofs eventually leak).
So my recommendation is a double-wall or modified Larsen truss system with dense-pack cellulose, board or CDX sheathing, felt or polymeric WRB, back-primed and end-grain-sealed siding, air-tight drywall, flat ceilings with raised-heel roof for full insulation depth at eaves, uniformly vented roof with continuous soffit and ridge vents (with external wind baffles), felt roofing underlayment (no high-tech non-breatheable underlayments, and particularly no self-adhering membrane), and a high-albedo roofing.
Mike,
There is no need to use Delta-Dry if you have furring strips. Delta-Dry is a three-dimensional WRB that is used to provide a ventilation channel between the sheathing and the siding. If you have furring strips, you don't need Delta-Dry. Instead, use housewrap.
Robert,
Do you have any links or photos of your window flashing details?
I noticed that you build the "Outie"
which makes a lot of sense
John,
There is nothing unusual about my window flashing details. If I don't use sheathing, I have little alternative but to tape the WRB to the window nailing flanges, and then tape the aluminum drip cap to the WRB as well. I don't cut flaps in the WRB at the top of the window, since the WRB is the only uninterrupted barrier between the insulation and the weather.
With board or plywood sheathing, I prefer #15 felt WRB and use 6" wide felt gasket strips under the window flanges, as per AAMA method A, but I don't caulk the flanges (I don't want to reduce breatheability nor make renovation difficult). Then felt is shingled under the bottom gasket and over the top window flange.
For my new construction, I haven't used sill pans which I considered unnecessary with tightly sealed plywood window and door boxes (Tremco at all joints) and water-tolerant hygroscopic materials in the envelope. I believe that self-adhering membranes can cause more problems than they prevent be eliminating drying potential.
On renovation work, I use site-fabricated sill pans as well as window gaskets, but prefer non-adhesive materials.
Hi Mike. You asked how my assembly would be stronger. I think that hanging siding off of 4-8" of rigid insulation provides some challenges in making a tight, sturdy enclosure. Not that it couldn't be done, but I'm not sure how you would do it. I have installed cement-board siding over 2" of rigid insulation, and even that gives a small amount of play and slippage of the siding. You also inquired about bringing in a second contractor for the blown-in cellulose insulation. You were already planning on bringing in a second contractor for the spray foam, so it would not be any additional trades. I'm not sure of your jobsite location, but it could be that even 2" of rigid insulation would keep the dewpoint outside of your wall enclosure, and that would do away with the need for conditioned space immediately behind the sheathing. There are some other very smart answers in this discussion, so just my two cents...
Robert,
I have bookmarked your comments (as I have with many of your comments)
I think that current "best practice" of window and window opening flashing may be a case of what Lstiburek and Tooley call "doing the Wrong thing Right"